Direct Clamp Injection Molding Machine – Your One-Stop Solution for All Your Plastic Machinery
2023/05/10 By Topstar
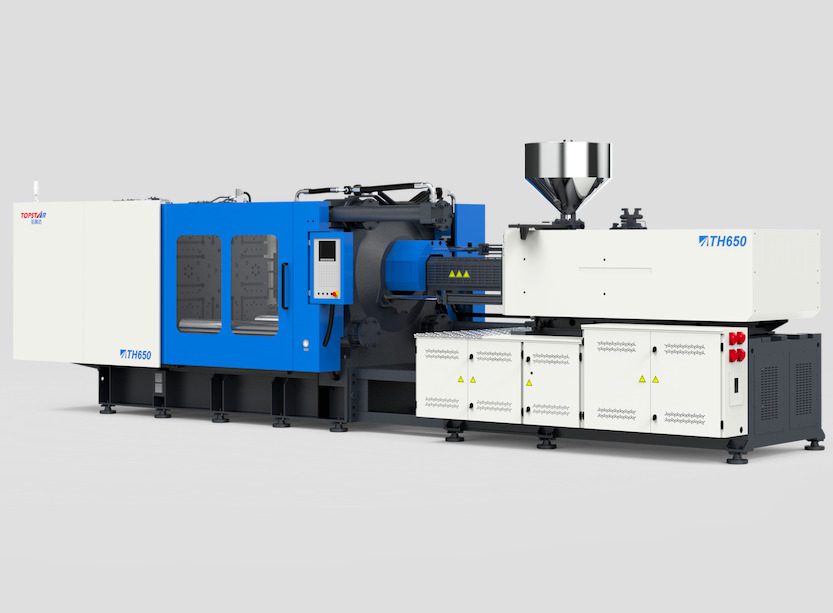
The direct clamp injection molding machine can solve all your plastic mechanical problems. It can produce high-quality products and meet the strictest production plans. Next, we will explore what direct clamping injection molding machines are and how they are manufactured. We hope to help you better understand why this is an excellent investment for your business.
What is a Direct Clamp Injection Molding Machine?
A direct clamp injection molding machine is an injection molding machine that uses direct clamps to hold the mold in place. The direct clamping machine is called the sliding door machine because the extruder slides back and forth on the guide rail to open and close the cavity. This allows for the rapid production of large parts, making it an ideal solution for mass production work.
Direct clamp machines can produce products ranging from small household items like toys or toothbrush handles to big industrial machinery like gears for machinery used in mines or factories (like large presses). Some examples include:
Why Choose a Direct Clamp Injection Molding Machine?
It is an excellent choice for your next purchase of plastic machinery. Here are some reasons:
It’s easy to use. The direct clamp injector is an automated machine requiring little training or expertise, making it ideal for first-time users.
It has a low cost of ownership. Direct clamp injectors have an efficient hydraulic system that reduces maintenance costs and increases uptime, saving you money by lowering repair-related issues.
It’s easy to maintain – there are few moving parts on this type of injection molder, so fewer things could go wrong during operation, which means less time spent fixing problems! This means less stress when running your business and more profits from selling products made from them too!
What Are the Benefits of a Direct Clamp Injection Molding Machine?
The direct clamp injection molding machine is an excellent choice for businesses looking to start producing plastic parts in-house. If you’re new to the world of injection molding, the direct clamp system might be a good fit for your needs.
Direct clamp systems have some significant benefits over other types of machines:
They’re cost-effective. It can start producing smaller batches with fewer resources. This makes them ideal if you’re starting or lack much capital. It also means they won’t require an extensive initial investment before starting!
They’re easy to use and quick to set up, and you’ll be able to start building parts right away without additional training or setup time. This makes them perfect if you need flexibility in producing products on-site and speed in your production cycle!
What are the parts that go into a direct clamp injection molding machine?
When you’re looking to purchase a direct clamp injection molding machine, you must know all the parts that go into it. Mold fixtures are part of the machine that holds onto a plastic part and shapes it. There are two main types of molds: cold runner and hot runner. No hard runners are involved when making the part, meaning no heated tools or pressurized lubricants are required during production. It also means less wear on your molds over time and less maintenance work overall (since there aren’t any moving parts).
Cold runners use “clamping force” instead of hydraulic power packs like hot runners do–but don’t worry! That doesn’t mean there aren’t any cool features about cold runners, either! For example, they can hold tighter tolerances than hot runners because they don’t require additional pressure lubricants or heating tools within them.
It is one of the best ways to produce plastic products!
Direct clamp injection molding machines are one of the best ways to make a plastic product. They are more efficient than other methods and can have various simple and complex products.
Direct clamp injection molding machines work by injecting molten material into molds previously formed by another device or by hand. The process begins with an operator loading raw materials into a hopper, then moving to a heating chamber, which is heated into a liquid. Once this happens, an injection unit forces molten plastic into pre-molded cavities called dies (or molds). This process continues until all holes are filled and sealed shut and are ejected from the system onto a conveyor belt or cooling rack. They are further cured before being packaged for shipping or storage.
Final
The direct clamp injection molding machine is among the most essential devices in the plastics industry. A good injection molding machine can help you manufacture high-quality products while saving time and money. So if you want to start your own business or improve the current production process, in addition to understanding this basic knowledge, you can contact us to learn more about it!
TRENDING POSTS
- What factors can cause delays in the injection molding process of plastic molding machine? 2023/05/10
- Exhibition Review| Topstar participates in InterPlas Thailand 2024 2023/05/10
- Star Case | Topstar helps Santong upgrade its intelligent plant 2023/05/10
- Topstar Special | National Science and Technology Workers Day 2023/05/10
HOT TOPIC
- .ervo motor-driven linear robots
- 3 axis robot
- 3 axis robots
- 3 in 1 Compact Dehumidifying Dryer
- 3-axis robot
- 3-axis robots
- 5-axis CNC machine
- accuracy
- Air Chillers
- all electric injection molding machine
- all electric injection molding machines
- All-electric injection molding machines
- and overall production quality. Therefore
- AP-RubberPlas
- automated injection molding machine
- Automation changed engineering
- automation of injection molding robots
- auxiliary machine
- Bench Injection Molding Machine
- Cabinet dryer manufacturers
- Cabinet dryers
- chiller
- CNC Drilling Machine
- CNC Drilling Machines
- cnc engraving machine manufacturer
- cnc laser cutting machine manufacturer
- CNC machine
- CNC Machine Center
- CNC Machine for Sale
- CNC Machine Manufacturing
- CNC Machine Tool
- CNC machine tool product
- CNC Machining Center
- CNC wood carving machine
- Cooling system
- Cross-Walking Single Axis Servo Cylinder Robot
- Cross-Walking Single-Axis Servo Cylinder Robot
- Cross-Walking Three-Axis/Five-Axis Servo Driven Robot
- cross-walking three-axis/five-axis servo-driven robot
- Dehumidifier Dryer
- Dehumidifying Dryer
- delta parallel robot
- Desktop Injection Molding Machine
- Desktop injection molding machines
- Desktop Molding Machine
- desktop plastic injection machine
- Desktop Plastic Injection Molding Machine
- direct clamp injection molding machine
- Direct clamp injection molding machines
- Dosing & mixing system
- Drilling Centers
- Drying and dehumidification system
- drying and dehumidifying equipment
- Drying and Dehumidifying System
- drying system
- effective and efficient. Cabinet dryers are also used in other industries where large quantities of material need to be dried
- efficient injection molding machine
- elbow hydraulic injection molding machines
- electric injection molding machine
- electric injection molding machines
- energy-efficient injection molding robot
- energy-saving injection molding machine
- etc. Among injection molding robots
- exhibition
- features of CNC machine
- Feeding And Conveying System
- Five Axis Machine Center
- Fully automatic injection molding machine
- Gathering Topstar
- giant injection molding machine
- GMU-600 5-Axis Machining Center
- Granulating & Recycling System
- Heavy duty injection molding machine
- High-precision electric molding machines
- high-precision plastic molding machines
- high-speed all electric injection molding machine
- Honeycomb rotor dehumidifier
- horizontal injection molding machine
- Horizontal Injection Molding Machines
- Horizontal Injection Moulding Machine
- Horizontal Mixer manufacturer
- How The CNC Machine Works
- hybrid injection molding machine
- hydraulic injection molding machine
- Hydraulic Injection Molding Machines
- in this article
- Industrial robot
- Industrial Robot Chinese brand
- industrial robot parts
- industrial robot supplier
- Industrial robots
- Industry Chain
- Injection Manipulator
- injection manipulator robot
- injection mold machines
- Injection molding
- Injection molding automation
- Injection Molding Automation Solution
- injection molding dryer
- Injection molding equipment
- injection molding hopper dryer
- Injection molding machine
- injection molding machine brand
- Injection Molding Machine Factory
- Injection Molding Machine Manufacture
- Injection molding machine manufacturer
- injection molding machine manufacturers
- Injection molding machine procurement
- injection molding machine robotic arm
- injection molding machine with a robot
- Injection molding machines
- injection molding material dehumidifying
- injection molding plant
- Injection Molding Robot
- injection molding robot arm
- Injection molding robot automation
- Injection molding robotic arm
- injection molding robots
- Injection moulding machine
- Injection Moulding Robots
- Injection Robot
- Injection robot arm
- Injection robot manufacturer
- Injection robot wholesale
- injection robots
- intelligent injection molding machines
- Introducing Injection Robot
- It is the best choice for drying large quantities of material at once. Cabinetmakers use these machines because they are fast
- large injection molding machine
- Learn what industrial automation and robotics is
- linear robot
- linear robots
- low speed sound-proof granulator
- machine plastic molding
- make sure to add some! Improvements (2) Keyphrase in introduction: Your keyphrase or its synonyms appear in the first paragraph of the copy
- manipulator machine
- manufacturing
- medical grade injection molding machines
- medical injection molding machine
- medical injection molding machines
- micro injection molding machine
- middle speed granulator
- Mini CNC machine manufacturers.
- Mold Temperature Control System
- mold temperature controller
- mold temperature controllers
- molding material Dehumidifying System
- mould temperature control system
- mould temperature controller
- mould temperature controllers
- New electric injection molding machine
- nitrogen dryer manufacturer
- nitrogen dryer system manufacturer
- Oil type mold temperature controller
- Oil type mold temperature controllers
- open day
- Outbound links: No outbound links appear in this page. Add some! Images: No images appear on this page. Add some! Internal links: No internal links appear in this page
- PET Preform injection molding
- phone case maker machine
- phone case making machine
- plastic bottle making machine
- plastic bottle manufacturing
- plastic bucket making machine
- plastic bucket manufacturing
- Plastic chair making machine
- plastic forming equipment
- plastic hopper dryer
- plastic injection machine
- plastic injection machines
- plastic injection molding
- Plastic injection molding equipment
- Plastic injection molding machine
- Plastic Injection Molding Machines
- plastic injection moulding machine
- plastic injection robot
- Plastic Molding machine
- Plastic Molding Machines
- plastic molding press
- plastic moulding machine
- plastic phone case making machine
- plastic-molding machine
- powerful granulator
- Powerful Type Sound-Proof Granulator
- precision injection molding
- precision injection molding machines
- production of plastic seats
- pure water mould temperature controller
- Robot injection molding
- robot injection molding machine
- robot manufacturing companies
- Robotic arm for injection molding machine
- robotic injection molding machines
- robotics in injection molding
- SCARA robot
- SCARA robots
- Service-oriented manufacturing
- Servo Cylinder Robot
- servo driven robot
- Servo Driven Robots
- servo injection robots
- servo motor-driven linear robots
- servo-driven 3-axis robot
- Servo-Driven Robot
- Setup of injection machine
- Silicone Injection Molding Machine
- six-axis industrial robot
- Stainless Hopper Dryer
- Stainless Hopper Dryers
- star club
- swing arm robot
- take-out robots
- the choice between servo-driven robots and hydraulic robots will have a certain impact on efficiency
- the most popular injection molding machine
- the type of injection molding robot
- toggle clamp injection molding machine
- Toggle Hydraulic Injection Molding Machines
- toggle injection molding machine
- Top 10 brands of injection robots
- Topstar
- Topstar Engineering
- Topstar Industrial Robots
- Topstar injection molding intelligent
- Topstar Scara Robots
- Useful Injection molding machine
- Vertical machining centers
- volumetric type blender
- water chiller
- water chillers
- water distributor
- water type mold temperature controller
- Water Type MoldTemperature Controller
- Water-Type Mould Temperature Controllers
- We often face choices when performing injection molding. We will choose the type of injection molding machine
- wholesale of injection molding machines
- x carve CNC