How to solve the problem of inaccurate positioning of linear robots?
2025/05/02 By Topstar
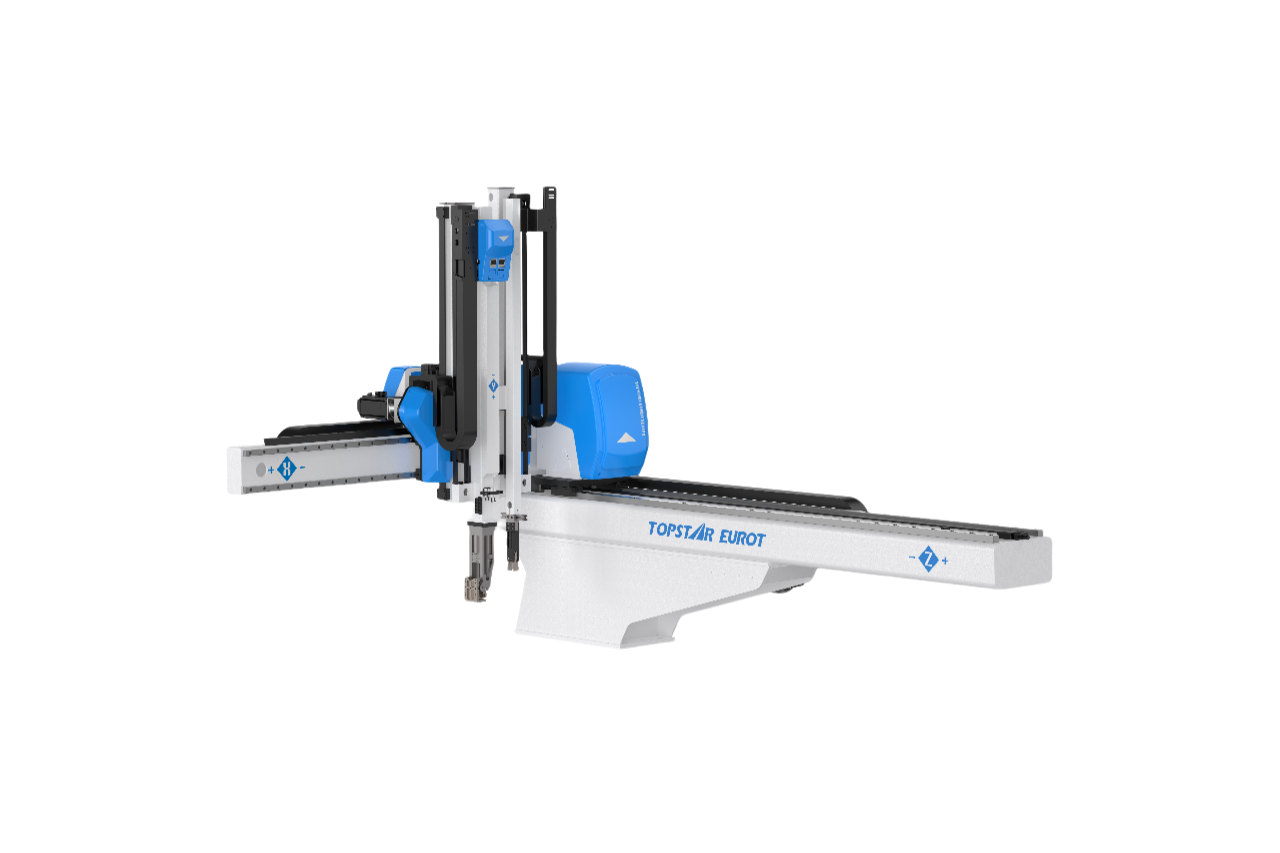
Linear robots, also known as injection molding robots, are used in injection molding to insert inserts into the mold and to pick up and place finished parts after molding. However, positioning inaccuracies can seriously disrupt production, leading to misaligned inserts, damaged parts, and increased scrap rates. To remain competitive, manufacturers need linear robots that can provide reliable repeatability and precise positioning accuracy, especially when handling delicate operations such as inserting plastic inserts into mold cavities and accurately placing molded parts on conveyors or packaging.
By integrating servo motor drive technology on each axis of the linear robot, Topstar ensures high-speed motion and precision gearbox speed change. This approach can achieve positioning accuracy of up to ±0.1 mm. The following sections will explore specific technologies such as precision gearboxes, 5-in-1 servo drive architecture, and advanced motion control algorithms to overcome positioning inaccuracies.
Linear robots achieve sub-millimeter positioning with servo motor drives
An essential element in addressing positioning errors is using servo motor drive systems on each axis of the linear robot. Unlike pneumatic or general-purpose stepper motors, servo motors integrate high-resolution encoders to monitor their rotational position continuously. In Topstar’s linear robots, these encoders provide real-time feedback to the drive controller, enabling instant course corrections.
Fast response times (typically less than 1 millisecond) combined with closed-loop control enable linear robots to maintain accuracy of ±0.1 mm even under dynamic loads or high speeds. The servo-driven axes can precisely decelerate for insertion as the fixture approaches the mold cavity, allowing the insert to be placed gently and without jerk. Similarly, during the pick-and-place process, the linear robot decelerates smoothly with the help of precision guides to eliminate overshoot, ensuring the molded part is accurately clamped at the intended pickup point.
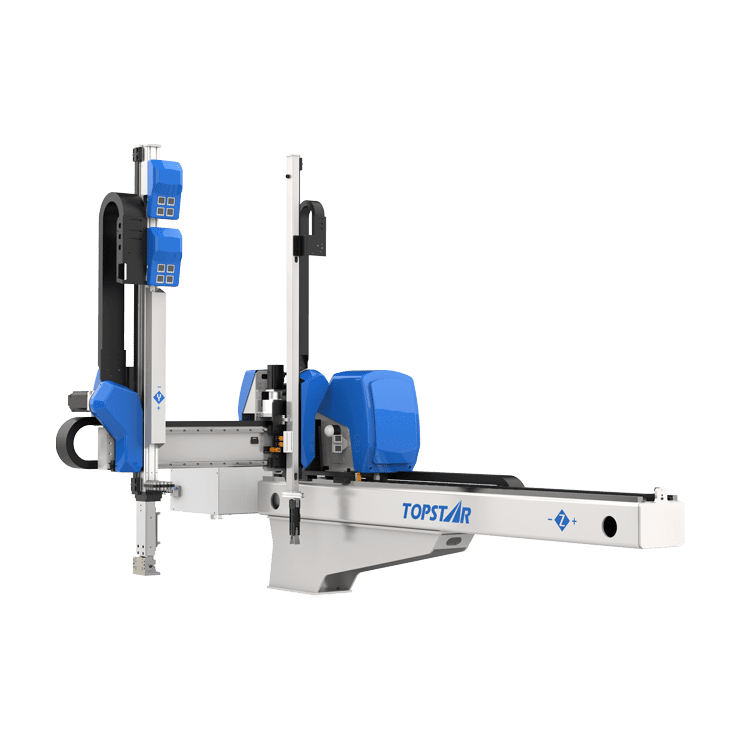
Precision-grade reducers for enhanced motion control
In addition to the servo motor drive, Topstar transmits power through precision reducers to accurately position the linear robot. Standard planetary or gear reducers typically introduce backlash and compliance, reducing repeatability. Topstar solves this problem by specifying precision harmonic or zero-backlash reducers for each axis. These reducers provide consistent gear meshing with minimal play, maintaining the servo motor’s rotational accuracy.
When used with servo motor drives, these precision-grade reducers ensure that the actuator’s linear motion directly converts motor commands into guide motion without lag or lost motion. During insertion, the reducers enable the robot to always reach the same depth and orientation in each mold cavity. The pick-and-place sequence ensures that the system executes the path from the ejector slot to the conveyor with precisely the same trajectory in every cycle. This allows the linear robot to combine fast dynamic response and mechanical precision.
5-in-1 Servo Drive Architecture for Linear Robots
The 5-in-1 servo drive architecture combines the control of up to five servo motors into a single modular drive unit. This design reduces communication delays between axes, simplifies system integration, and ensures that coordinated motion remains perfectly phased. The 5-in-1 servo drive enables the linear robot to perform complex five-axis motion within a single motion command, such as descending to the mold, adjusting the gripper direction, and moving forward simultaneously. This unified drive approach eliminates the slight delays that occur when independent drives communicate over a Fieldbus network. For functions such as insertion, the drive automatically coordinates the vertical insertion speed with the lateral motion to prevent misalignment. In pick-and-place tasks, the end effector smoothly passes through multi-axis waypoints and precisely aligns with the bracket or pallet.
Automatic optimization of the removal process
Topstar linear robots can support host call signals to achieve integrated operation. The control system automatically optimizes the removal process, aiming to achieve optimal trajectory control, especially in complex injection molding environments. Through automatic optimization of the control system, overshooting at high speeds can be prevented, and vibration can be reduced, ensuring smooth movement and high precision. In dynamic molding environments, it also includes automatic compensation functions to account for mold wear and adjust robot motion in response to changes in mold geometry over time. This ensures consistent insert accuracy and extends the mold’s life. This real-time adjustment is critical when dealing with warped or asymmetric parts, as it can effectively reduce positioning errors caused by subtle inconsistencies in product geometry.
Vibration reduction technology
The high-speed operation of linear robots often presents vibration-related challenges, especially when handling heavy payloads accurately. To jointly improve the stability and accuracy of the robot. One of the core improvements is using a high-rigidity precision slide structure and a lightweight aluminum alloy injection molding robot arm. This reduces inertial loads and improves response time and motion smoothness. Complementing this is an active vibration reduction system that uses real-time servo torque control to counteract oscillations during high-speed transitions. This torque modulation method can fine-tune the motor’s output to suppress undesirable movements. These technologies enable Topstar robots to operate at speeds of up to 2 meters per second while always maintaining positioning accuracy within ±0.15 mm.
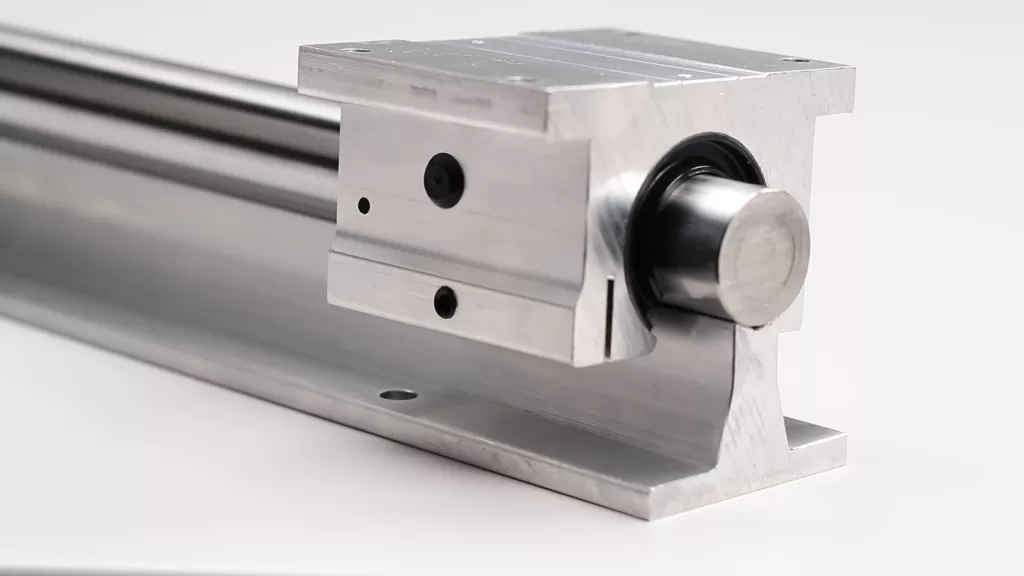
Achieving precision and reliability in molding automation
Topstar’s integrated solution – each axis has a servo motor drive system, precision-grade reducers, and advanced five-in-one servo drives to ensure high-speed operation and achieve sub-millimeter accuracy of up to ±0.1 mm. By adopting servo motor-driven linear robots, molders can eliminate familiar sources of position errors, reduce scrap rates, and achieve consistent product quality in high-volume production.
TRENDING POSTS
- What factors can cause delays in the injection molding process of plastic molding machine? 2025/05/02
- Exhibition Review| Topstar participates in InterPlas Thailand 2024 2025/05/02
- Star Case | Topstar helps Santong upgrade its intelligent plant 2025/05/02
- Topstar Special | National Science and Technology Workers Day 2025/05/02
HOT TOPIC
- .ervo motor-driven linear robots
- 1.0 guangdong topstar technology co. ltd
- 1.0 topstar china
- 1.0 topstar robot
- 11
- 2
- 21
- 23
- 3 axis robot
- 3 axis robots
- 3 in 1 Compact Dehumidifying Dryer
- 3-axis robot
- 3-axis robots
- 39
- 41
- 5-axis CNC machine
- 62
- accuracy
- Air Chillers
- all electric injection molding machine
- all electric injection molding machines
- All-electric injection molding machines
- and overall production quality. Therefore
- AP-RubberPlas
- automated injection molding machine
- Automation changed engineering
- automation of injection molding robots
- auxiliary machine
- Bench Injection Molding Machine
- Cabinet dryer manufacturers
- Cabinet dryers
- chiller
- CNC Drilling Machine
- CNC Drilling Machines
- cnc engraving machine manufacturer
- cnc laser cutting machine manufacturer
- CNC machine
- CNC Machine Center
- CNC Machine for Sale
- CNC Machine Manufacturing
- CNC Machine Tool
- CNC machine tool product
- CNC Machining Center
- CNC wood carving machine
- Cooling system
- Cross-Walking Single Axis Servo Cylinder Robot
- Cross-Walking Single-Axis Servo Cylinder Robot
- Cross-Walking Three-Axis/Five-Axis Servo Driven Robot
- cross-walking three-axis/five-axis servo-driven robot
- Dehumidifier Dryer
- Dehumidifying Dryer
- delta parallel robot
- Desktop Injection Molding Machine
- Desktop injection molding machines
- Desktop Molding Machine
- desktop plastic injection machine
- Desktop Plastic Injection Molding Machine
- direct clamp injection molding machine
- Direct clamp injection molding machines
- Dosing & mixing system
- Drilling Centers
- Drying and dehumidification system
- drying and dehumidifying equipment
- Drying and Dehumidifying System
- drying system
- effective and efficient. Cabinet dryers are also used in other industries where large quantities of material need to be dried
- efficient injection molding machine
- elbow hydraulic injection molding machines
- electric injection molding machine
- electric injection molding machines
- energy-efficient injection molding robot
- energy-efficient water chiller
- energy-efficient water chillers
- energy-saving injection molding machine
- etc. Among injection molding robots
- exhibition
- features of CNC machine
- Feeding And Conveying System
- Five Axis Machine Center
- Fully automatic injection molding machine
- Gathering Topstar
- giant injection molding machine
- GMU-600 5-Axis Machining Center
- Granulating & Recycling System
- Heavy duty injection molding machine
- High-precision electric molding machines
- high-precision plastic molding machines
- high-speed all electric injection molding machine
- high-speed electric injection molding machine
- High-Speed Packaging Injection Molding
- Honeycomb rotor dehumidifier
- horizontal injection molding machine
- Horizontal Injection Molding Machines
- Horizontal Injection Moulding Machine
- Horizontal Mixer manufacturer
- How The CNC Machine Works
- hybrid injection molding machine
- hydraulic injection molding machine
- Hydraulic Injection Molding Machines
- in this article
- Industrial robot
- Industrial Robot Chinese brand
- industrial robot parts
- industrial robot supplier
- Industrial robots
- Industry Chain
- Injection Manipulator
- injection manipulator robot
- injection mold machines
- Injection molding
- Injection molding automation
- Injection Molding Automation Solution
- injection molding dryer
- Injection molding equipment
- injection molding hopper dryer
- Injection molding machine
- injection molding machine brand
- Injection Molding Machine Factory
- Injection Molding Machine Manufacture
- Injection molding machine manufacturer
- injection molding machine manufacturers
- Injection molding machine procurement
- injection molding machine robotic arm
- injection molding machine with a robot
- Injection molding machines
- injection molding material dehumidifying
- injection molding plant
- injection molding process
- Injection Molding Robot
- injection molding robot arm
- Injection molding robot automation
- Injection molding robotic arm
- injection molding robots
- Injection moulding machine
- injection moulding machines
- Injection Moulding Robots
- Injection Robot
- Injection robot arm
- Injection robot manufacturer
- Injection robot wholesale
- injection robots
- intelligent injection molding machines
- intelligent mold temperature
- intelligent mold temperature controller
- Intelligent mould temperature controller
- Introducing Injection Robot
- It is the best choice for drying large quantities of material at once. Cabinetmakers use these machines because they are fast
- Large flow water type mold temperature controller
- large injection molding machine
- large injection molding machines
- Learn what industrial automation and robotics is
- linear robot
- linear robots
- low speed sound-proof granulator
- machine plastic molding
- make sure to add some! Improvements (2) Keyphrase in introduction: Your keyphrase or its synonyms appear in the first paragraph of the copy
- manipulator machine
- manufacturing
- medical grade injection molding machines
- medical injection molding machine
- medical injection molding machines
- micro injection molding machine
- middle speed granulator
- Mini CNC machine manufacturers.
- Mold Temperature Control System
- mold temperature controller
- mold temperature controllers
- molding material Dehumidifying System
- mould temperature control system
- mould temperature controller
- mould temperature controllers
- New electric injection molding machine
- nitrogen dryer manufacturer
- nitrogen dryer system manufacturer
- Oil type mold temperature controller
- Oil type mold temperature controllers
- open day
- Outbound links: No outbound links appear in this page. Add some! Images: No images appear on this page. Add some! Internal links: No internal links appear in this page
- PET Preform injection molding
- phone case maker machine
- phone case making machine
- phone cover making machine
- plastic bottle making machine
- plastic bottle manufacturing
- plastic bucket making machine
- plastic bucket manufacturing
- Plastic chair making machine
- plastic forming equipment
- plastic hopper dryer
- plastic injection machine
- plastic injection machines
- plastic injection molding
- Plastic injection molding equipment
- Plastic injection molding machine
- Plastic Injection Molding Machines
- plastic injection moulding machine
- plastic injection moulding machines
- plastic injection robot
- plastic molding
- Plastic Molding machine
- plastic molding machine 1
- Plastic Molding Machines
- plastic molding press
- plastic moulding machine
- plastic phone case making machine
- plastic-molding machine
- powerful granulator
- Powerful Type Sound-Proof Granulator
- precision injection molding
- precision injection molding machines
- production of plastic seats
- pure water mould temperature controller
- Robot injection molding
- robot injection molding machine
- robot manufacturing companies
- Robotic arm for injection molding machine
- robotic injection molding machines
- robotics in injection molding
- SCARA robot
- SCARA robots
- Service-oriented manufacturing
- Servo Cylinder Robot
- servo driven robot
- Servo Driven Robots
- servo injection molding machine
- servo injection robots
- servo motor-driven linear robots
- servo-driven 3-axis robot
- Servo-Driven Robot
- Setup of injection machine
- Silicone Injection Molding Machine
- six-axis industrial robot
- Stainless Hopper Dryer
- Stainless Hopper Dryers
- star club
- swing arm robot
- take-out robot
- take-out robots
- the choice between servo-driven robots and hydraulic robots will have a certain impact on efficiency
- the most popular injection molding machine
- the type of injection molding robot
- TMII injection molding machine
- toggle clamp injection molding machine
- Toggle Hydraulic Injection Molding Machines
- toggle injection molding machine
- Top 10 brands of injection robots
- Topstar
- Topstar Engineering
- Topstar Industrial Robots
- Topstar injection molding intelligent
- Topstar Scara Robots
- Useful Injection molding machine
- Vertical machining centers
- volumetric type blender
- water chiller
- water chillers
- water distributor
- water type mold temperature controller
- Water Type MoldTemperature Controller
- Water-Type Mould Temperature Controllers
- We often face choices when performing injection molding. We will choose the type of injection molding machine
- wholesale of injection molding machines
- x carve CNC
- 热门查询 点击次数 展示 排名 topstar