Relationship between mold material thickness and mold temperature controller settings
2025/05/07 By Topstar
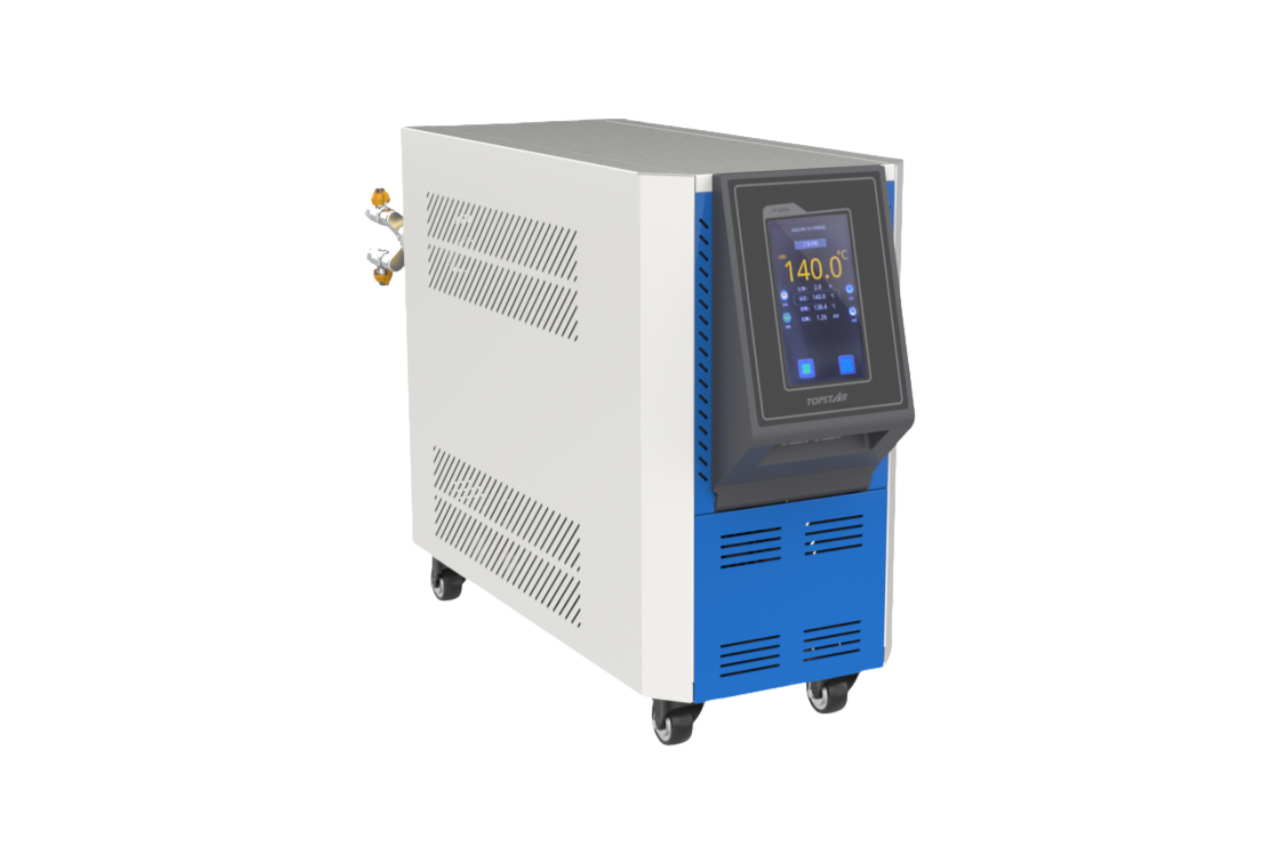
When injection molding, mold temperature controllers ensure consistent part quality and cycle times. A critical but often overlooked factor is the thickness of the mold material itself. Mold material thickness directly affects the heat transfer rate, with thicker mold sections storing more heat and dissipating it more slowly, while thinner mold sections heat and cool faster. Therefore, we must adjust the mold temperature controller settings based on mold material thickness to optimize temperature uniformity and prevent warping.
This how-to guide will share the specific adjustments required for different mold thicknesses – temperature setpoints, coolant flow, heating power, and PID adjustments. These settings are adjusted to achieve tight temperature control of the mold surface during injection molding.
Mold Temperature Controller: Adjusting Temperature Setpoints Based on Mold Thickness Variations
The first parameter to consider when setting up a mold temperature controller for different mold thicknesses is the temperature setpoint. Thicker mold parts have a larger thermal mass and therefore require higher set temperatures or longer preheat times to achieve thermal equilibrium. For a mold component that is 80 mm thick, the operator may need to increase the set point by 5-10°C above the recommended nominal temperature for thinner parts. Conversely, thinner molds, such as 20-30 mm, heat up quickly; setting the temperature too high may result in overheating, localized thermal gradients, and potential thermal damage to the mold steel.
We recommend performing multiple in-depth thermal analyses when setting up the mould temperature controller. Sensor data can indicate whether the operator needs to adjust the set point in stages—first by increasing the temperature to preheat the core, then by decreasing it to maintain a steady state. This enables differentiated control of different thicknesses throughout the mold.
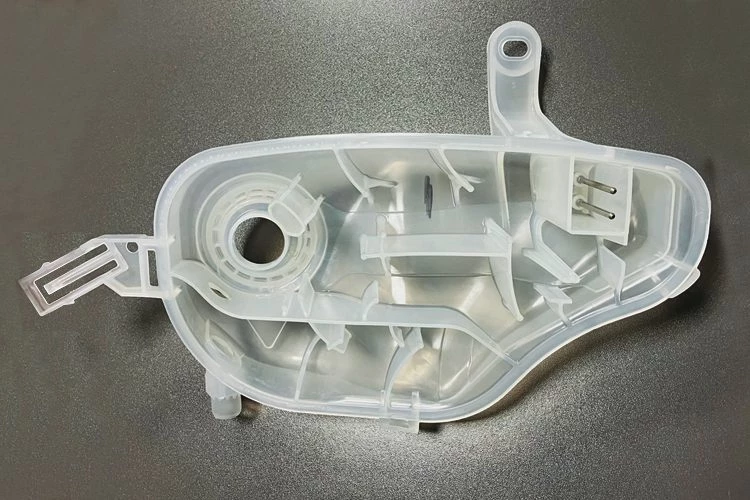
Optimizing Coolant Flow for Thick Molds
In addition to set point adjustments, thick mold sections require increased coolant flow from the mold temperature controller to remove excess heat during the cooling phase effectively. Coolant channels in thick mold plates must handle higher volumetric flow rates, typically 20-30% higher than those in thin molds. Inadequate flow rates result in extended cooling times and uneven temperature distribution, exacerbating cycle inefficiencies and part warpage.
Consider tubing size and pump capacity when setting up a mold temperature controller. For molds thicker than 60 mm, upgrade to larger diameter hoses (e.g., 3/4-inch to 1-inch) and high-flow pumps to deliver up to 10 L/min per cooling circuit. Some mold temperature controllers feature automatic flow control that adjusts pump speed based on temperature differential feedback, ensuring optimal coolant delivery without manual intervention.
Increase heating power for faster temperature ramps.
Thick molds require increased heating power from the mold temperature controller to reach the setpoint temperature within a practical preheat window. For example, a 15-kW heater may be sufficient for a thin mold, but a 30-kW system may be required for a 100-mm steel block. The mold may never reach optimal operating temperature without adequate power, resulting in poor melt flow and incomplete cavity filling.
Calculate the required power density to configure a mold temperature controller for thick molds. Ensure you appropriately size and evenly distribute cartridge or oil-jacketed heaters to avoid hot spots. Topstar’s mold temperature controllers offer programmable ramp rates for a fast full-power preheat phase and a reduced-power hold to maintain thermal equilibrium. This strategy minimizes preheat time while maintaining system life and energy efficiency.
PID Tuning of Mold Temperature Controllers for Thermal Response
The effectiveness of any mold temperature controller depends on accurate PID tuning. Thick molds respond more slowly to control inputs due to their greater thermal inertia. Standard PID settings optimized for thin molds often result in overshoots or longer-lasting temperature swings when applied to thick-walled sections. To accommodate slow thermal dynamics, operators should adjust PID gains: reduce proportional gain to avoid overcorrection; extend integral time to prevent saturation; and set derivative term to a moderate value to dampen oscillations.
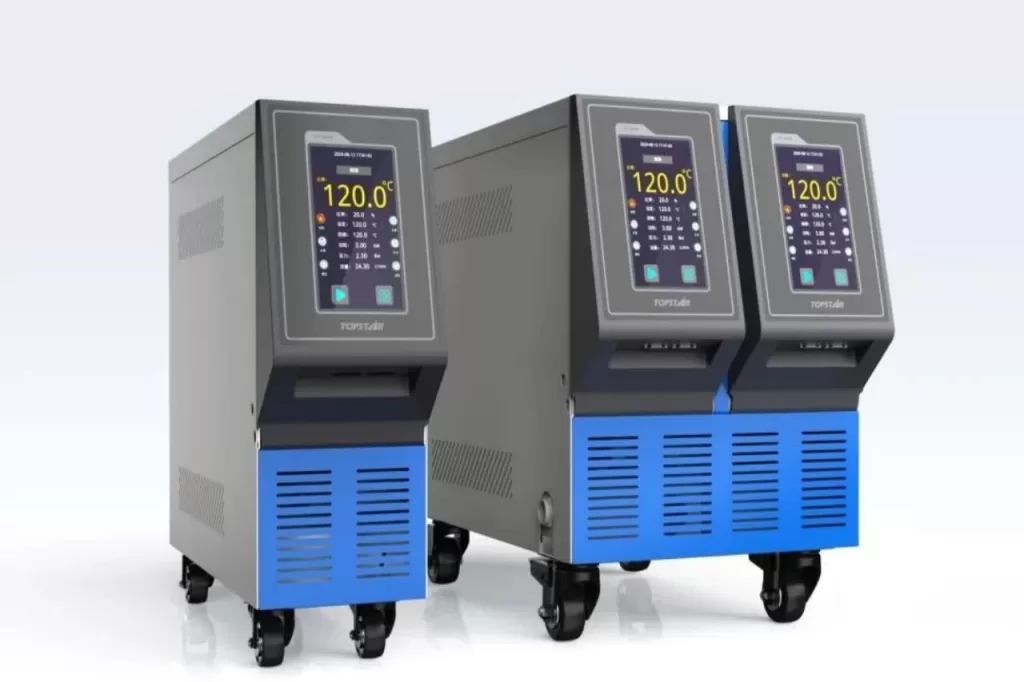
Topstar’s intelligent mold temperature controllers include an auto-tuning algorithm that identifies the best PID parameters based on the mold’s response curve. When dealing with thick molds, the controller’s auto-tuning feature can be enabled during a test cycle to measure thermal hysteresis and iteratively optimize the control loop. Proper PID tuning ensures that the mold temperature controller maintains the setpoint within ±0.5°C, providing consistent part quality and reducing scrap rates caused by temperature-induced process fluctuations.
Mastering Temperature Control
The relationship between mold material thickness and mold temperature controller settings is multifaceted: temperature setpoints must be aligned with thermal mass, coolant flow must be adjusted to dissipate heat effectively, heating power must be calibrated for fast warm-up, and PID loops must be tuned for slow response dynamics. By following these principles, manufacturers can ensure uniform mold temperatures, reduce cycle times, and deliver consistent part quality.
TRENDING POSTS
- What factors can cause delays in the injection molding process of plastic molding machine? 2025/05/07
- Exhibition Review| Topstar participates in InterPlas Thailand 2024 2025/05/07
- Star Case | Topstar helps Santong upgrade its intelligent plant 2025/05/07
- Topstar Special | National Science and Technology Workers Day 2025/05/07
HOT TOPIC
- .ervo motor-driven linear robots
- 1.0 guangdong topstar technology co. ltd
- 1.0 topstar china
- 1.0 topstar robot
- 11
- 2
- 21
- 23
- 3 axis robot
- 3 axis robots
- 3 in 1 Compact Dehumidifying Dryer
- 3-axis robot
- 3-axis robots
- 39
- 41
- 5-axis CNC machine
- 62
- accuracy
- Air Chillers
- all electric injection molding machine
- all electric injection molding machines
- All-electric injection molding machines
- and overall production quality. Therefore
- AP-RubberPlas
- automated injection molding machine
- Automation changed engineering
- automation of injection molding robots
- auxiliary machine
- Bench Injection Molding Machine
- Cabinet dryer manufacturers
- Cabinet dryers
- chiller
- CNC Drilling Machine
- CNC Drilling Machines
- cnc engraving machine manufacturer
- cnc laser cutting machine manufacturer
- CNC machine
- CNC Machine Center
- CNC Machine for Sale
- CNC Machine Manufacturing
- CNC Machine Tool
- CNC machine tool product
- CNC Machining Center
- CNC wood carving machine
- Cooling system
- Cross-Walking Single Axis Servo Cylinder Robot
- Cross-Walking Single-Axis Servo Cylinder Robot
- Cross-Walking Three-Axis/Five-Axis Servo Driven Robot
- cross-walking three-axis/five-axis servo-driven robot
- Dehumidifier Dryer
- Dehumidifying Dryer
- delta parallel robot
- Desktop Injection Molding Machine
- Desktop injection molding machines
- Desktop Molding Machine
- desktop plastic injection machine
- Desktop Plastic Injection Molding Machine
- direct clamp injection molding machine
- Direct clamp injection molding machines
- Dosing & mixing system
- Drilling Centers
- Drying and dehumidification system
- drying and dehumidifying equipment
- Drying and Dehumidifying System
- drying system
- effective and efficient. Cabinet dryers are also used in other industries where large quantities of material need to be dried
- efficient injection molding machine
- elbow hydraulic injection molding machines
- electric injection molding machine
- electric injection molding machines
- energy-efficient injection molding robot
- energy-efficient water chiller
- energy-efficient water chillers
- energy-saving injection molding machine
- etc. Among injection molding robots
- exhibition
- features of CNC machine
- Feeding And Conveying System
- Five Axis Machine Center
- Fully automatic injection molding machine
- Gathering Topstar
- giant injection molding machine
- GMU-600 5-Axis Machining Center
- Granulating & Recycling System
- Heavy duty injection molding machine
- High-precision electric molding machines
- high-precision plastic molding machines
- high-speed all electric injection molding machine
- high-speed electric injection molding machine
- High-Speed Packaging Injection Molding
- Honeycomb rotor dehumidifier
- horizontal injection molding machine
- Horizontal Injection Molding Machines
- Horizontal Injection Moulding Machine
- Horizontal Mixer manufacturer
- How The CNC Machine Works
- hybrid injection molding machine
- hydraulic injection molding machine
- Hydraulic Injection Molding Machines
- in this article
- Industrial robot
- Industrial Robot Chinese brand
- industrial robot parts
- industrial robot supplier
- Industrial robots
- Industry Chain
- Injection Manipulator
- injection manipulator robot
- injection mold machines
- Injection molding
- Injection molding automation
- Injection Molding Automation Solution
- injection molding dryer
- Injection molding equipment
- injection molding hopper dryer
- Injection molding machine
- injection molding machine brand
- Injection Molding Machine Factory
- Injection Molding Machine Manufacture
- Injection molding machine manufacturer
- injection molding machine manufacturers
- Injection molding machine procurement
- injection molding machine robotic arm
- injection molding machine with a robot
- Injection molding machines
- injection molding material dehumidifying
- injection molding plant
- injection molding process
- Injection Molding Robot
- injection molding robot arm
- Injection molding robot automation
- Injection molding robotic arm
- injection molding robots
- Injection moulding machine
- injection moulding machines
- Injection Moulding Robots
- Injection Robot
- Injection robot arm
- Injection robot manufacturer
- Injection robot wholesale
- injection robots
- intelligent injection molding machines
- intelligent mold temperature
- intelligent mold temperature controller
- Intelligent mould temperature controller
- Introducing Injection Robot
- It is the best choice for drying large quantities of material at once. Cabinetmakers use these machines because they are fast
- Large flow water type mold temperature controller
- large injection molding machine
- large injection molding machines
- Learn what industrial automation and robotics is
- linear robot
- linear robots
- low speed sound-proof granulator
- machine plastic molding
- make sure to add some! Improvements (2) Keyphrase in introduction: Your keyphrase or its synonyms appear in the first paragraph of the copy
- manipulator machine
- manufacturing
- medical grade injection molding machines
- medical injection molding machine
- medical injection molding machines
- micro injection molding machine
- middle speed granulator
- Mini CNC machine manufacturers.
- Mold Temperature Control System
- mold temperature controller
- mold temperature controllers
- molding material Dehumidifying System
- mould temperature control system
- mould temperature controller
- mould temperature controllers
- New electric injection molding machine
- nitrogen dryer manufacturer
- nitrogen dryer system manufacturer
- Oil type mold temperature controller
- Oil type mold temperature controllers
- open day
- optical component injection molding
- Outbound links: No outbound links appear in this page. Add some! Images: No images appear on this page. Add some! Internal links: No internal links appear in this page
- PET Preform injection molding
- phone case maker machine
- phone case making machine
- phone cover making machine
- plastic bottle making machine
- plastic bottle manufacturing
- plastic bucket making machine
- plastic bucket manufacturing
- Plastic chair making machine
- plastic forming equipment
- plastic hopper dryer
- plastic injection machine
- plastic injection machines
- plastic injection molding
- Plastic injection molding equipment
- Plastic injection molding machine
- Plastic Injection Molding Machines
- plastic injection moulding machine
- plastic injection moulding machines
- plastic injection robot
- plastic molding
- Plastic Molding machine
- plastic molding machine 1
- Plastic Molding Machines
- plastic molding press
- plastic moulding machine
- plastic phone case making machine
- plastic-molding machine
- powerful granulator
- Powerful Type Sound-Proof Granulator
- precision injection molding
- precision injection molding machines
- production of plastic seats
- pure water mould temperature controller
- Robot injection molding
- robot injection molding machine
- robot manufacturing companies
- Robotic arm for injection molding machine
- robotic injection molding machines
- robotics in injection molding
- SCARA robot
- SCARA robots
- Service-oriented manufacturing
- Servo Cylinder Robot
- servo driven robot
- Servo Driven Robots
- servo injection molding machine
- servo injection robots
- servo motor-driven linear robots
- servo-driven 3-axis robot
- Servo-Driven Robot
- Setup of injection machine
- Silicone Injection Molding Machine
- six-axis industrial robot
- Stainless Hopper Dryer
- Stainless Hopper Dryers
- star club
- swing arm robot
- take-out robot
- take-out robots
- the choice between servo-driven robots and hydraulic robots will have a certain impact on efficiency
- the most popular injection molding machine
- the type of injection molding robot
- TMII injection molding machine
- toggle clamp injection molding machine
- Toggle Hydraulic Injection Molding Machines
- toggle injection molding machine
- Top 10 brands of injection robots
- Topstar
- Topstar Engineering
- Topstar Industrial Robots
- Topstar injection molding intelligent
- Topstar Scara Robots
- Useful Injection molding machine
- Vertical machining centers
- volumetric type blender
- water chiller
- water chillers
- water distributor
- water type mold temperature controller
- Water Type MoldTemperature Controller
- Water-Type Mould Temperature Controllers
- We often face choices when performing injection molding. We will choose the type of injection molding machine
- wholesale of injection molding machines
- x carve CNC
- 热门查询 点击次数 展示 排名 topstar