Advantages of using multi-cavity molds in the injection molding machine
2023/11/22 By Topstar
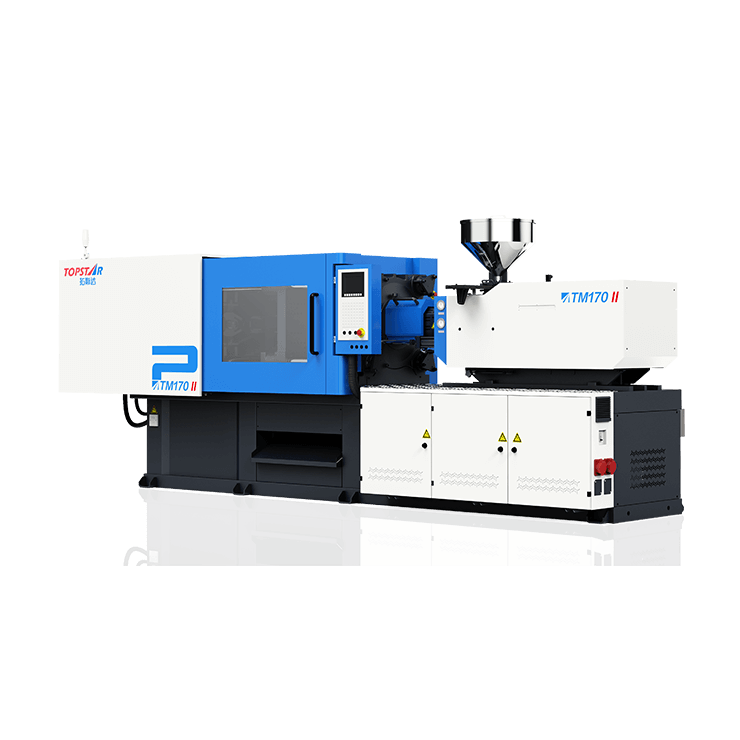
Almost every plastics manufacturer wants to improve the efficiency and productivity of their factories. These high-standard pursuits prompt plastics manufacturers to constantly explore innovative solutions. Multi-cavity molds stand out, providing advantages that make the injection molding machine more flexible. In this article, we at Topstar explore the many benefits of integrating multi-cavity molds, revealing how this approach is critical to achieving higher throughput and optimizing production processes.
1. Improve efficiency with multi-cavity molds
Maximize throughput with parallel production
One of the most essential advantages of using multi-cavity molds in injection molding machines is the substantial increase in throughput. These molds enable parallel production by allowing multiple identical parts to be produced simultaneously, significantly reducing cycle times. This increase in efficiency means more finished products can be made in the same amount of time, meeting market demand at an unparalleled rate. Manufacturers can achieve economies of scale without compromising accuracy or quality, positioning multi-cavity molds as a strategic choice for high-volume production.
In addition to significantly speeding up production, this simultaneous molding approach is critical in industries with strict schedules and market demands. For enterprises that need to respond quickly to market fluctuations or seasonal changes, the increased throughput brought about by multi-cavity molds becomes a critical factor in maintaining a competitive advantage.
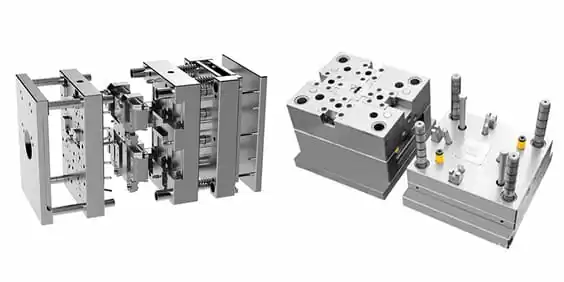
2. Scalable without scaling costs
achieve economies of scale
Multi-cavity molds help achieve significant cost savings in injection molding, which is critical for most plastic manufacturers. Despite the initial investment in tooling, the increased output per cycle offsets the upfront cost over time. This scalability ensures unit costs decrease as production volumes increase, making multi-cavity molds an economically prudent choice.
The impact of multi-cavity molds goes beyond lowering production costs. It encompasses a holistic approach that considers the entire manufacturing ecosystem. For example, reducing energy consumption from optimized cycle times lowers operating costs and aligns with the global trend of promoting sustainable and energy-saving manufacturing practices.
3. Reduce injection molding machine energy consumption
Green manufacturing of multi-cavity molds
Using multi-cavity molds complies with green manufacturing practices by minimizing energy consumption. Simplified, simultaneous production of multiple parts optimizes energy use and reduces the overall carbon footprint of the injection molding process. This is environmentally responsible and positions manufacturers well in a market where sustainable practices are increasingly valued.
This sustainability advantage is significant in industries with strict environmental regulations, and consumers value environmentally friendly products. By adopting multi-cavity molds, plastics manufacturers can increase efficiency and contribute to creating a sustainable and responsible production ecosystem.
4. Enhance the consistency and quality of injection molding machine
Ensure uniformity with multi-cavity molds
Multi-cavity molds in injection molding machines ensure consistent part quality throughout production. Each cavity experiences the same molding conditions with simultaneous display, minimizing part-to-part variations. This enhanced consistency is critical in industries where precision and uniformity are crucial, such as medical or automotive manufacturing.
The advantages of maintaining uniformity across multiple cavities extend beyond visual aesthetics. It opens to both functional and structural aspects. In industries where components need to assemble seamlessly or meet stringent performance standards, the ability of multi-cavity molds to deliver high levels of precision and quality becomes a strategic differentiator.
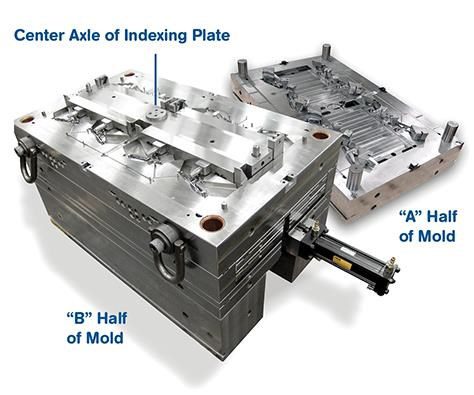
5. Optimize plastic material use!
Reduce environmental impact
Using multi-cavity molds in injection molding machines improves material efficiency by minimizing waste during production. By molding multiple parts simultaneously, you can optimize material use for each piece, reduce scrap, and minimize environmental impact. This aligns with sustainable manufacturing practices and solves issues related to material waste.
Many manufacturers produce many consumables using injection molding machines, so optimizing materials after using multi-cavity molds makes economic sense. In an industry where material costs represent a large portion of total production expenses, the ability to reduce waste can translate directly into cost savings. Manufacturers using multi-cavity molds can strike a delicate balance between cost-effectiveness and environmental responsibility.
The final point
The advantages of using multi-cavity molds in injection molding machines are manifold, providing a transformative approach to production. From increased throughput and cost efficiency to sustainability, design flexibility, and improved quality, integrating multi-cavity molds represents a strategic move to optimize the injection molding process. At the same time, you are also welcome to visit our official website to communicate with us for more relevant information.
TRENDING POSTS
- What factors can cause delays in the injection molding process of plastic molding machine? 2023/11/22
- Exhibition Review| Topstar participates in InterPlas Thailand 2024 2023/11/22
- Star Case | Topstar helps Santong upgrade its intelligent plant 2023/11/22
- Topstar Special | National Science and Technology Workers Day 2023/11/22
HOT TOPIC
- .ervo motor-driven linear robots
- 1.0 guangdong topstar technology co. ltd
- 1.0 topstar china
- 1.0 topstar robot
- 11
- 2
- 21
- 23
- 3 axis robot
- 3 axis robots
- 3 in 1 Compact Dehumidifying Dryer
- 3-axis robot
- 3-axis robots
- 39
- 41
- 5-axis CNC machine
- 62
- accuracy
- Air Chillers
- all electric injection molding machine
- all electric injection molding machines
- All-electric injection molding machines
- and overall production quality. Therefore
- AP-RubberPlas
- automated injection molding machine
- Automation changed engineering
- automation of injection molding robots
- auxiliary machine
- Bench Injection Molding Machine
- Cabinet dryer manufacturers
- Cabinet dryers
- chiller
- CNC Drilling Machine
- CNC Drilling Machines
- cnc engraving machine manufacturer
- cnc laser cutting machine manufacturer
- CNC machine
- CNC Machine Center
- CNC Machine for Sale
- CNC Machine Manufacturing
- CNC Machine Tool
- CNC machine tool product
- CNC Machining Center
- CNC wood carving machine
- Cooling system
- Cross-Walking Single Axis Servo Cylinder Robot
- Cross-Walking Single-Axis Servo Cylinder Robot
- Cross-Walking Three-Axis/Five-Axis Servo Driven Robot
- cross-walking three-axis/five-axis servo-driven robot
- Dehumidifier Dryer
- Dehumidifying Dryer
- delta parallel robot
- Desktop Injection Molding Machine
- Desktop injection molding machines
- Desktop Molding Machine
- desktop plastic injection machine
- Desktop Plastic Injection Molding Machine
- direct clamp injection molding machine
- Direct clamp injection molding machines
- Dosing & mixing system
- Drilling Centers
- Drying and dehumidification system
- drying and dehumidifying equipment
- Drying and Dehumidifying System
- drying system
- effective and efficient. Cabinet dryers are also used in other industries where large quantities of material need to be dried
- efficient injection molding machine
- elbow hydraulic injection molding machines
- electric injection molding machine
- electric injection molding machines
- energy-efficient injection molding robot
- energy-saving injection molding machine
- etc. Among injection molding robots
- exhibition
- features of CNC machine
- Feeding And Conveying System
- Five Axis Machine Center
- Fully automatic injection molding machine
- Gathering Topstar
- giant injection molding machine
- GMU-600 5-Axis Machining Center
- Granulating & Recycling System
- Heavy duty injection molding machine
- High-precision electric molding machines
- high-precision plastic molding machines
- high-speed all electric injection molding machine
- Honeycomb rotor dehumidifier
- horizontal injection molding machine
- Horizontal Injection Molding Machines
- Horizontal Injection Moulding Machine
- Horizontal Mixer manufacturer
- How The CNC Machine Works
- hybrid injection molding machine
- hydraulic injection molding machine
- Hydraulic Injection Molding Machines
- in this article
- Industrial robot
- Industrial Robot Chinese brand
- industrial robot parts
- industrial robot supplier
- Industrial robots
- Industry Chain
- Injection Manipulator
- injection manipulator robot
- injection mold machines
- Injection molding
- Injection molding automation
- Injection Molding Automation Solution
- injection molding dryer
- Injection molding equipment
- injection molding hopper dryer
- Injection molding machine
- injection molding machine brand
- Injection Molding Machine Factory
- Injection Molding Machine Manufacture
- Injection molding machine manufacturer
- injection molding machine manufacturers
- Injection molding machine procurement
- injection molding machine robotic arm
- injection molding machine with a robot
- Injection molding machines
- injection molding material dehumidifying
- injection molding plant
- Injection Molding Robot
- injection molding robot arm
- Injection molding robot automation
- Injection molding robotic arm
- injection molding robots
- Injection moulding machine
- injection moulding machines
- Injection Moulding Robots
- Injection Robot
- Injection robot arm
- Injection robot manufacturer
- Injection robot wholesale
- injection robots
- intelligent injection molding machines
- Introducing Injection Robot
- It is the best choice for drying large quantities of material at once. Cabinetmakers use these machines because they are fast
- large injection molding machine
- large injection molding machines
- Learn what industrial automation and robotics is
- linear robot
- linear robots
- low speed sound-proof granulator
- machine plastic molding
- make sure to add some! Improvements (2) Keyphrase in introduction: Your keyphrase or its synonyms appear in the first paragraph of the copy
- manipulator machine
- manufacturing
- medical grade injection molding machines
- medical injection molding machine
- medical injection molding machines
- micro injection molding machine
- middle speed granulator
- Mini CNC machine manufacturers.
- Mold Temperature Control System
- mold temperature controller
- mold temperature controllers
- molding material Dehumidifying System
- mould temperature control system
- mould temperature controller
- mould temperature controllers
- New electric injection molding machine
- nitrogen dryer manufacturer
- nitrogen dryer system manufacturer
- Oil type mold temperature controller
- Oil type mold temperature controllers
- open day
- Outbound links: No outbound links appear in this page. Add some! Images: No images appear on this page. Add some! Internal links: No internal links appear in this page
- PET Preform injection molding
- phone case maker machine
- phone case making machine
- plastic bottle making machine
- plastic bottle manufacturing
- plastic bucket making machine
- plastic bucket manufacturing
- Plastic chair making machine
- plastic forming equipment
- plastic hopper dryer
- plastic injection machine
- plastic injection machines
- plastic injection molding
- Plastic injection molding equipment
- Plastic injection molding machine
- Plastic Injection Molding Machines
- plastic injection moulding machine
- plastic injection moulding machines
- plastic injection robot
- Plastic Molding machine
- Plastic Molding Machines
- plastic molding press
- plastic moulding machine
- plastic phone case making machine
- plastic-molding machine
- powerful granulator
- Powerful Type Sound-Proof Granulator
- precision injection molding
- precision injection molding machines
- production of plastic seats
- pure water mould temperature controller
- Robot injection molding
- robot injection molding machine
- robot manufacturing companies
- Robotic arm for injection molding machine
- robotic injection molding machines
- robotics in injection molding
- SCARA robot
- SCARA robots
- Service-oriented manufacturing
- Servo Cylinder Robot
- servo driven robot
- Servo Driven Robots
- servo injection robots
- servo motor-driven linear robots
- servo-driven 3-axis robot
- Servo-Driven Robot
- Setup of injection machine
- Silicone Injection Molding Machine
- six-axis industrial robot
- Stainless Hopper Dryer
- Stainless Hopper Dryers
- star club
- swing arm robot
- take-out robots
- the choice between servo-driven robots and hydraulic robots will have a certain impact on efficiency
- the most popular injection molding machine
- the type of injection molding robot
- toggle clamp injection molding machine
- Toggle Hydraulic Injection Molding Machines
- toggle injection molding machine
- Top 10 brands of injection robots
- Topstar
- Topstar Engineering
- Topstar Industrial Robots
- Topstar injection molding intelligent
- Topstar Scara Robots
- Useful Injection molding machine
- Vertical machining centers
- volumetric type blender
- water chiller
- water chillers
- water distributor
- water type mold temperature controller
- Water Type MoldTemperature Controller
- Water-Type Mould Temperature Controllers
- We often face choices when performing injection molding. We will choose the type of injection molding machine
- wholesale of injection molding machines
- x carve CNC
- 热门查询 点击次数 展示 排名 topstar