Drying process of 3 in 1 Compact Dehumidifying Dryer in injection molding
2025/07/11 By Topstar
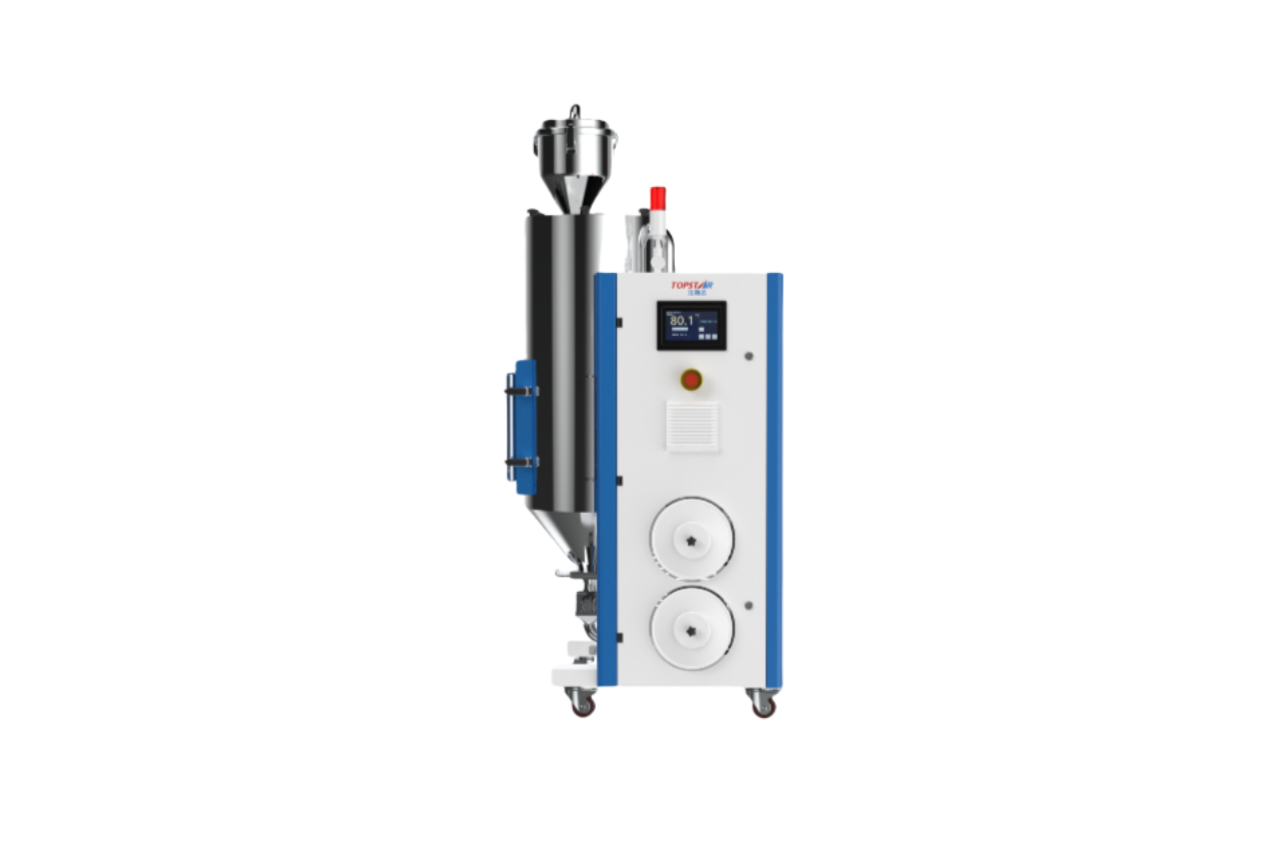
During the R&D and design process, we integrated the dehumidification and drying machines into a 3 in 1 Compact dehumidifying dryer, which can provide a perfect resin drying effect for the injection molding machine. We divide the drying process into four stages, covering compressed air treatment, rapid pressure change dehumidification, ultra-dry air delivery, and sealed barrel moisture absorption. The system first filters and cleans water and oil from the workshop’s compressed air using a dedicated removal screening program before routing it to the dehumidification tower.
While the pressure in the variable cylinder dehumidification tower is rapidly reduced, the dehumidified air with a dew point of -40 is obtained, and the -40 dew point dehumidified air (one-way delivery) is continuously sent to the sealed dehumidification barrel to absorb the moisture of all raw materials in the barrel. This system features a one-way air supply, eliminating the need for regenerated dehumidification.
Comprehensive filtration of water and oil
Our 3 in 1 Compact Dehumidifying Dryer’s multi-stage screening system strictly pre-treats the workshop’s compressed air before it enters the dehumidification tower. Next, the air passes through a coalescing filter rated to remove particles as small as 0.01 microns, thereby removing large amounts of water and oily aerosols. Additionally, an activated carbon filter element further removes hydrocarbon vapors, protecting downstream components and desiccant beds. You need to regularly check the filter pressure differential and replace the filter element according to a data-driven maintenance plan to ensure that each cleaning removes more than 99% of contaminants. This ensures that only ultra-pure, oil-free air can enter the dehumidifier, thereby maintaining the desiccant’s capacity and preventing the resin from discoloring or degrading during the drying process.
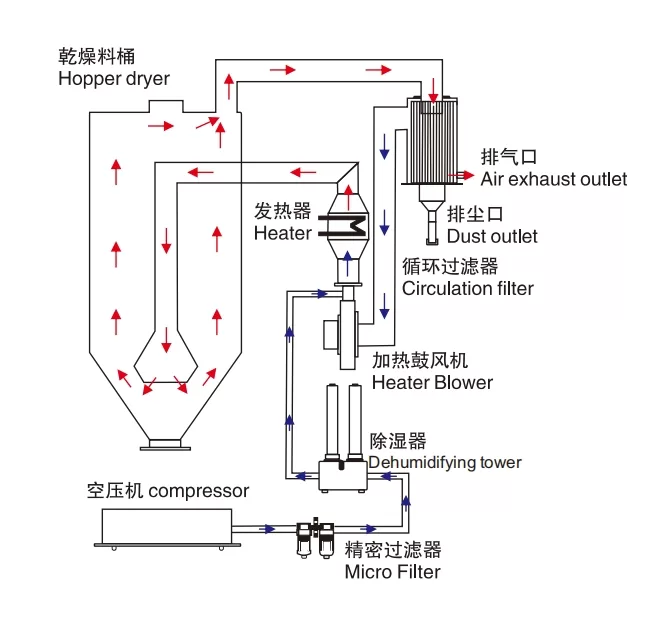
Rapidly reduce the pressure in the dehumidifier tower in the 3 in 1 Compact Dehumidifying Dryer
The filtration system sends the purified mixture to the dehumidifier tower once it completely removes water and oil. We regenerate the desiccant and produce ultra-dry air by quickly reducing the pressure. One of the core components of the 3 in 1 compact dehumidifying dryer is our patented variable cylinder dehumidifier tower. For example, we can reduce the tower pressure from 1 bar to 0.2 bar in five seconds, which will trigger adiabatic expansion, thereby driving moisture out of the silica gel. The system repeats this pressure oscillation cycle every two minutes, delivering a continuous supply of -40°C dew point air without requiring external heating. At the same time, you can fine-tune cylinder valve timing and monitor desiccant temperature to optimize regeneration efficiency, ensuring peak drying power even when plant load fluctuates. This regeneration-free approach reduces energy consumption and eliminates downtime associated with traditional heated dryers.
Sealed barrel moisture absorption
Inside the sealed barrel of the 3 in 1 compact dehumidifying dryer, the dry air absorbs residual moisture from the raw materials through patented baffles and distribution manifolds. At the same time, the internal baffle design promotes turbulent airflow, which maximizes contact between resin particles and dry air. The operator can set a dwell time of 2 to 6 hours in the microcomputer control, and adjust it based on the hygroscopicity of the resin to maintain moisture levels below 0.02%. Quick-release clamps and purge ports on all barrels simplify cleaning and material changes, reducing downtime and maintaining hygiene in strictly regulated production environments.
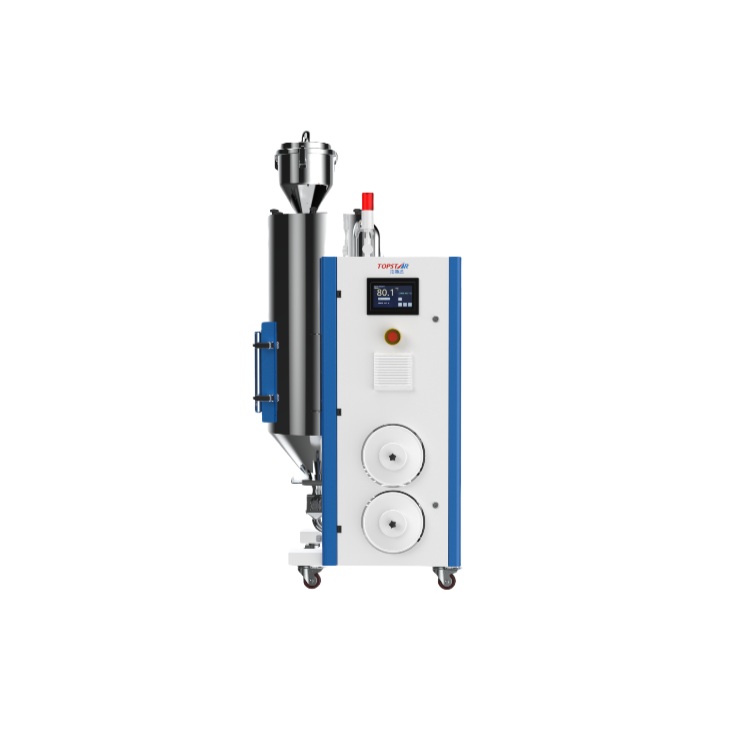
Continuous -40°C dew point air delivery to 3 in 1 compact dehumidifying dryer
After complete purification, the -40°C dew point air is passed through our sealed dehumidifying drum in a single continuous stream without recirculation. The unidirectional airflow prevents moisture re-entry and cross-contamination, ensuring that materials such as nylon, PET, or polycarbonate are continuously exposed to an ultra-dry environment. “Our microcomputer-controlled system maintains a precise airflow rate of 100-150 L/min, with adjustable settings for hopper size and resin throughput. This steady-state delivery ensures uniform drying dynamics, reduces the risk of moisture-induced defects, and supports high-throughput molding cycles without manual intervention.
Regeneration-free unidirectional air supply
Unlike traditional desiccant dryers, which require alternating regeneration cycles and heated purge air, our 3 in 1 compact dehumidifying dryers utilize a continuous, unidirectional air supply system. The system requires no purge air heating (typically 20-30% of energy loss in older systems), actively lowering operating costs and increasing time between maintenance. I integrate real-time dew point sensors upstream and downstream of the tower to dynamically adjust the timing of the regeneration cylinder, maintaining a temperature of -40°C even when ambient conditions change. This regeneration-free design ensures that the dryer supports 24/7 injection molding operations, minimizes operator supervision, and maximizes energy savings.
Bringing the most complete drying process
The drying process of the 3 in 1 compact dehumidifying dryer covers four stages, namely compressed air treatment, rapid pressure swing dehumidification, ultra-dry air delivery and sealed barrel moisture absorption. It integrates rapid pressure swing regeneration, multi-stage water and oil filtration, continuous -40°C dew point air delivery, and sealed barrel moisture absorption to provide a seamless, energy-saving drying process for injection molding machines. Ensure consistent pellet dryness and optimal molding quality by calibrating and monitoring each component, from pre-treatment filters to desiccant circulation algorithms.
TRENDING POSTS
- What factors can cause delays in the injection molding process of plastic molding machine? 2025/07/11
- Exhibition Review| Topstar participates in InterPlas Thailand 2024 2025/07/11
- Star Case | Topstar helps Santong upgrade its intelligent plant 2025/07/11
- Topstar Special | National Science and Technology Workers Day 2025/07/11
HOT TOPIC
- .ervo motor-driven linear robots
- 1.0 guangdong topstar technology co. ltd
- 1.0 topstar china
- 1.0 topstar robot
- 11
- 2
- 21
- 23
- 3 axis robot
- 3 axis robots
- 3 in 1 Compact Dehumidifying Dryer
- 3-axis robot
- 3-axis robots
- 39
- 41
- 5-axis CNC machine
- 62
- accuracy
- Air Chillers
- all electric injection molding machine
- all electric injection molding machines
- All-electric injection molding machines
- and overall production quality. Therefore
- AP-RubberPlas
- automated injection molding machine
- Automation changed engineering
- automation of injection molding robots
- auxiliary machine
- Bench Injection Molding Machine
- Cabinet dryer manufacturers
- Cabinet dryers
- chiller
- CNC Drilling Machine
- CNC Drilling Machines
- cnc engraving machine manufacturer
- cnc laser cutting machine manufacturer
- CNC machine
- CNC Machine Center
- CNC Machine for Sale
- CNC Machine Manufacturing
- CNC Machine Tool
- CNC machine tool product
- CNC Machining Center
- CNC wood carving machine
- Cooling system
- Cross-Walking Single Axis Servo Cylinder Robot
- Cross-Walking Single-Axis Servo Cylinder Robot
- Cross-Walking Three-Axis/Five-Axis Servo Driven Robot
- cross-walking three-axis/five-axis servo-driven robot
- Dehumidifier Dryer
- Dehumidifying Dryer
- delta parallel robot
- Desktop Injection Molding Machine
- Desktop injection molding machines
- Desktop Molding Machine
- desktop plastic injection machine
- Desktop Plastic Injection Molding Machine
- direct clamp injection molding machine
- Direct clamp injection molding machines
- Dosing & mixing system
- Drilling Centers
- Drying and dehumidification system
- drying and dehumidifying equipment
- Drying and Dehumidifying System
- drying system
- effective and efficient. Cabinet dryers are also used in other industries where large quantities of material need to be dried
- efficient injection molding machine
- elbow hydraulic injection molding machines
- electric injection molding machine
- electric injection molding machines
- energy-efficient injection molding robot
- energy-efficient water chiller
- energy-efficient water chillers
- energy-saving injection molding machine
- etc. Among injection molding robots
- exhibition
- features of CNC machine
- Feeding And Conveying System
- Five Axis Machine Center
- Fully automatic injection molding machine
- Gathering Topstar
- giant injection molding machine
- GMU-600 5-Axis Machining Center
- Granulating & Recycling System
- Heavy duty injection molding machine
- High-precision electric molding machines
- high-precision plastic molding machines
- high-speed all electric injection molding machine
- high-speed electric injection molding machine
- High-Speed Packaging Injection Molding
- Honeycomb rotor dehumidifier
- horizontal injection molding machine
- Horizontal Injection Molding Machines
- Horizontal Injection Moulding Machine
- Horizontal Mixer manufacturer
- How The CNC Machine Works
- hybrid injection molding machine
- hydraulic injection molding machine
- Hydraulic Injection Molding Machines
- in this article
- Industrial robot
- Industrial Robot Chinese brand
- industrial robot parts
- industrial robot supplier
- Industrial robots
- Industry Chain
- Injection Manipulator
- injection manipulator robot
- injection mold machines
- Injection molding
- Injection molding automation
- Injection Molding Automation Solution
- injection molding dryer
- Injection molding equipment
- injection molding hopper dryer
- Injection molding machine
- injection molding machine brand
- Injection Molding Machine Factory
- Injection Molding Machine Manufacture
- Injection molding machine manufacturer
- injection molding machine manufacturers
- Injection molding machine procurement
- injection molding machine robotic arm
- injection molding machine with a robot
- Injection molding machines
- injection molding material dehumidifying
- injection molding plant
- injection molding process
- Injection Molding Robot
- injection molding robot arm
- Injection molding robot automation
- Injection molding robotic arm
- injection molding robots
- Injection moulding machine
- injection moulding machines
- Injection Moulding Robots
- Injection Robot
- Injection robot arm
- Injection robot manufacturer
- Injection robot wholesale
- injection robots
- intelligent injection molding machines
- intelligent mold temperature
- intelligent mold temperature controller
- Intelligent mould temperature controller
- Introducing Injection Robot
- It is the best choice for drying large quantities of material at once. Cabinetmakers use these machines because they are fast
- Large flow water type mold temperature controller
- large injection molding machine
- large injection molding machines
- Learn what industrial automation and robotics is
- linear robot
- linear robots
- low speed sound-proof granulator
- machine plastic molding
- make sure to add some! Improvements (2) Keyphrase in introduction: Your keyphrase or its synonyms appear in the first paragraph of the copy
- manipulator machine
- manufacturing
- medical grade injection molding machines
- medical injection molding machine
- medical injection molding machines
- micro injection molding machine
- middle speed granulator
- Mini CNC machine manufacturers.
- Mold Temperature Control System
- mold temperature controller
- mold temperature controllers
- molding material Dehumidifying System
- mould temperature control system
- mould temperature controller
- mould temperature controllers
- New electric injection molding machine
- nitrogen dryer manufacturer
- nitrogen dryer system manufacturer
- Oil type mold temperature controller
- Oil type mold temperature controllers
- open day
- Outbound links: No outbound links appear in this page. Add some! Images: No images appear on this page. Add some! Internal links: No internal links appear in this page
- PET Preform injection molding
- phone case maker machine
- phone case making machine
- phone cover making machine
- plastic bottle making machine
- plastic bottle manufacturing
- plastic bucket making machine
- plastic bucket manufacturing
- Plastic chair making machine
- plastic forming equipment
- plastic hopper dryer
- plastic injection machine
- plastic injection machines
- plastic injection molding
- Plastic injection molding equipment
- Plastic injection molding machine
- Plastic Injection Molding Machines
- plastic injection moulding machine
- plastic injection moulding machines
- plastic injection robot
- plastic molding
- Plastic Molding machine
- plastic molding machine 1
- Plastic Molding Machines
- plastic molding press
- plastic moulding machine
- plastic phone case making machine
- plastic-molding machine
- powerful granulator
- Powerful Type Sound-Proof Granulator
- precision injection molding
- precision injection molding machines
- production of plastic seats
- pure water mould temperature controller
- Robot injection molding
- robot injection molding machine
- robot manufacturing companies
- Robotic arm for injection molding machine
- robotic injection molding machines
- robotics in injection molding
- SCARA robot
- SCARA robots
- Service-oriented manufacturing
- Servo Cylinder Robot
- servo driven robot
- Servo Driven Robots
- servo injection molding machine
- servo injection robots
- servo motor-driven linear robots
- servo-driven 3-axis robot
- Servo-Driven Robot
- Setup of injection machine
- Silicone Injection Molding Machine
- six-axis industrial robot
- Stainless Hopper Dryer
- Stainless Hopper Dryers
- star club
- swing arm robot
- take-out robot
- take-out robots
- the choice between servo-driven robots and hydraulic robots will have a certain impact on efficiency
- the most popular injection molding machine
- the type of injection molding robot
- TMII injection molding machine
- toggle clamp injection molding machine
- Toggle Hydraulic Injection Molding Machines
- toggle injection molding machine
- Top 10 brands of injection robots
- Topstar
- Topstar Engineering
- Topstar Industrial Robots
- Topstar injection molding intelligent
- Topstar Scara Robots
- Useful Injection molding machine
- Vertical machining centers
- volumetric type blender
- water chiller
- water chillers
- water distributor
- water type mold temperature controller
- Water Type MoldTemperature Controller
- Water-Type Mould Temperature Controllers
- We often face choices when performing injection molding. We will choose the type of injection molding machine
- wholesale of injection molding machines
- x carve CNC
- 热门查询 点击次数 展示 排名 topstar