How to achieve high precision with an injection molding machine?
2024/06/21 By Topstar
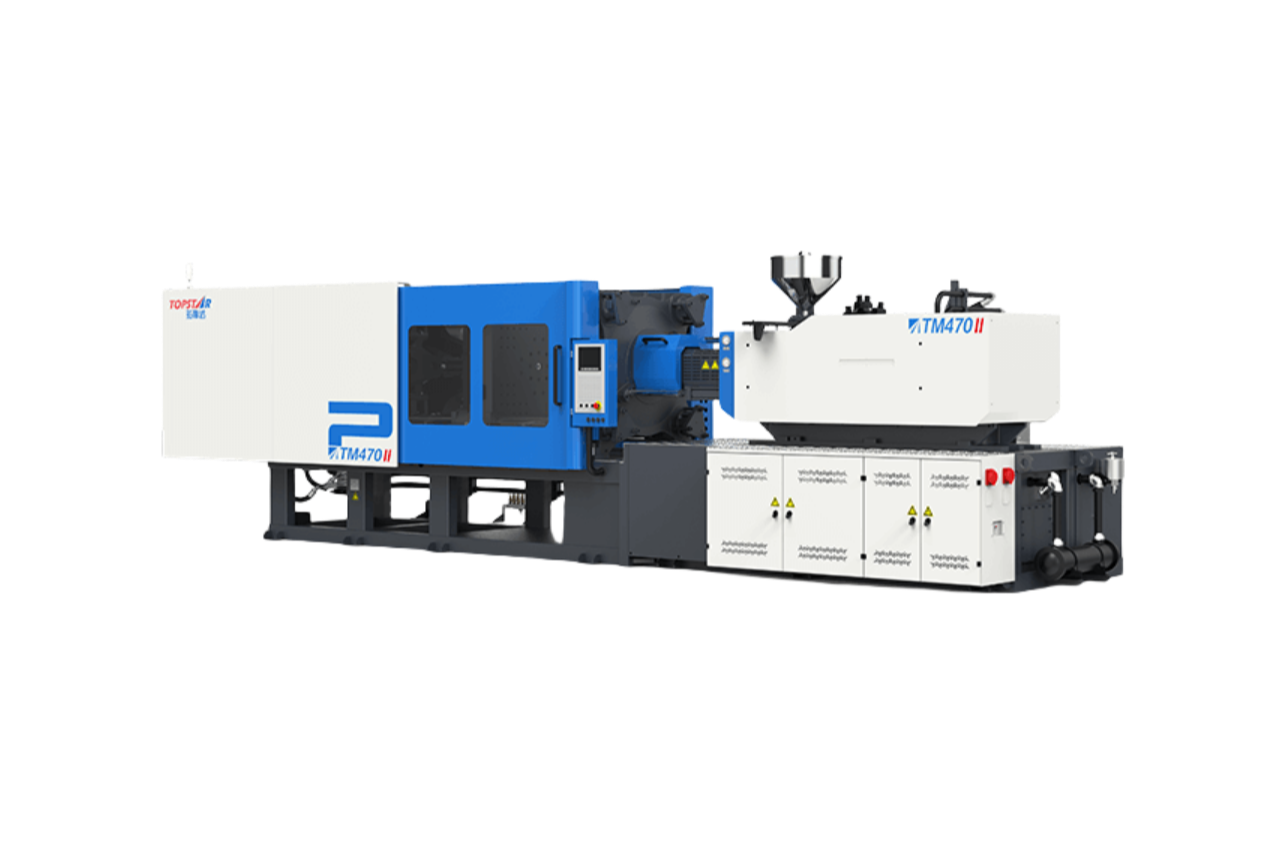
Companies that manufacture high-precision plastic products are often more favored by users, and the high precision of parts is also a standard for judging a manufacturing company and the equipment they use. So for injection molding, how can the injection molding machine achieve high precision to produce high-quality parts? In this guide, we will share several aspects so that you can understand systematically how to achieve high accuracy.
Choose the right injection molding machine
If you want to achieve high precision in injection molding, the first step is choosing a suitable injection molding machine. Because the control and drive systems of different types of machines are different, the various factors in them will affect the precision capabilities of the machine.
Machine type: Different injection molding machines, such as hydraulic, electric, and hybrid, can provide different degrees of precision.
Electric machines:
They use servo motors for all significant injection, clamping, ejection, and other movements and can accurately control speed, pressure, and position. Electric machines have the characteristics of accuracy, repeatability, and high energy efficiency.
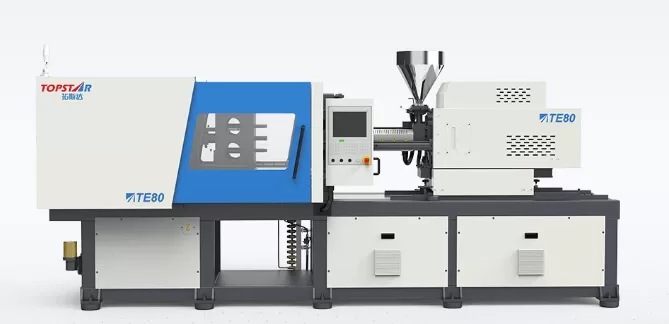
Hydraulic press:
Traditional hydraulic presses are not as accurate as electric machines, but hydraulic presses using related technologies can also improve precision to a certain extent. In comparison, it is more cost-effective and suitable for more significant parts that require high strength.
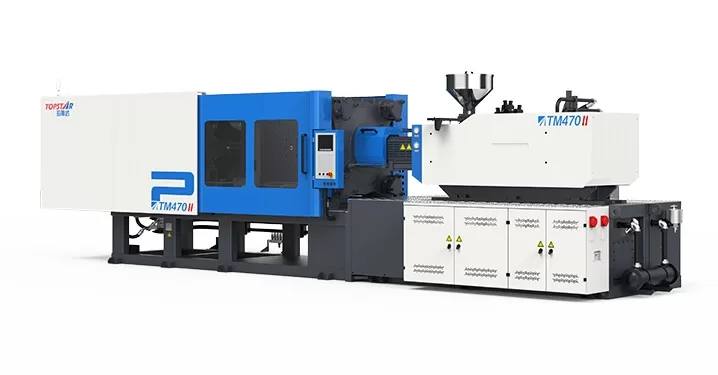
Hybrid machines:
Hybrid machines combine the best of both worlds, using electric drives for precision control and hydraulic systems for high-intensity control, making them versatile and capable of achieving high precision in various applications.
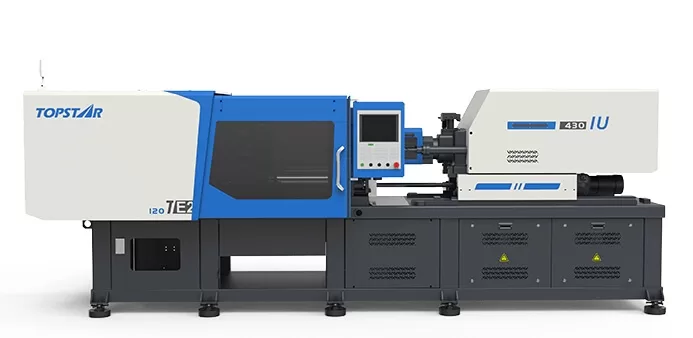
Optimize molding parameters for precision
After selecting the suitable injection molding machine, optimizing molding parameters during the injection molding process is necessary to achieve higher precision. Key parameters that must be carefully controlled include temperature, pressure, speed, etc.
Temperature control: Precise control of melt and mold temperature is essential to ensure consistent material flow and avoid defects such as dents and warping while ensuring the regular operation of the heating and cooling systems. This can be achieved by using different mould temperature controllers.
Injection pressure and speed: On the one hand, the intelligent electric injection motion can control time, pressure, position PV, and speed conversion to accurately balance thoroughly filling the mold and avoiding excessive pressure on the material. On the other hand, the automatic compensation function of the manipulator mold opening position can achieve accurate grasping and placement of the manipulator.
Back pressure: Applying the correct back pressure during the plasticization stage helps achieve uniform melt density and avoid problems such as air entrapment and material degradation. You can adjust the back pressure according to the material properties and the specific requirements of the molded part.
Select high-quality injection molding materials
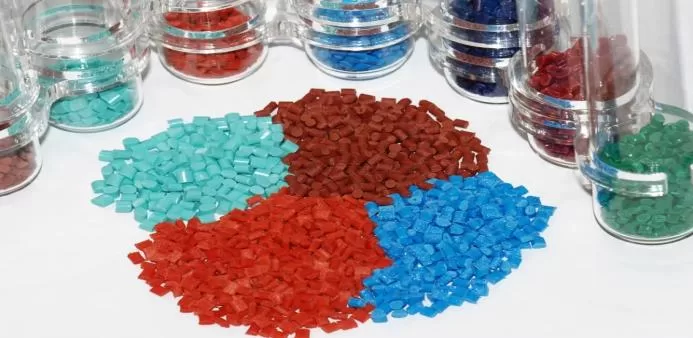
The material selection in the injection molding process also has a certain degree of influence on the precision and quality of the parts. High-quality materials often ensure the product’s consistent performance.
Material properties: We need to consider the mechanical, thermal, and chemical properties of the materials used for injection molding. Factors such as melt flow index, shrinkage, and thermal conductivity will affect the molding process and the quality of the final part. Materials compatible with the required application and performance requirements need to be used.
Material Handling: Ensure materials are stored in a controlled environment to prevent contamination and moisture absorption. Drying equipment is required to remove moisture from hygroscopic materials before processing.
Ensure mold quality and maintenance
The quality and maintenance of the mold also help the injection molding machine achieve high precision. Well-designed and adequately maintained molds ensure consistent part quality and minimize the risk of defects.
Mold design: Factors such as gate location, venting, cooling channels, and ejection systems should be considered when designing the mold. Proper gate design ensures uniform material flow and reduces the risk of flow marks and weld lines. Adequate venting prevents cavitation and burns, while effective cooling channels ensure uniform cooling and shorten cycle times.
Maintenance practices: Regular maintenance of molds is essential to prevent wear, avoid production downtime, and maintain high precision. This includes cleaning mold surfaces, checking for wear and damage, and ensuring that cooling channels and ventilation systems function correctly.
Getting high-precision injection molding
You need a comprehensive approach to achieve high precision in injection molding machines. As mentioned in the article, selecting a suitable machine, optimizing molding parameters, ensuring mold quality, etc., are critical to ensuring the molded parts’ dimensional accuracy, consistency, and overall quality. Only by doing these details well can you get high-precision parts.
TRENDING POSTS
- What factors can cause delays in the injection molding process of plastic molding machine? 2024/06/21
- Exhibition Review| Topstar participates in InterPlas Thailand 2024 2024/06/21
- Star Case | Topstar helps Santong upgrade its intelligent plant 2024/06/21
- Topstar Special | National Science and Technology Workers Day 2024/06/21
HOT TOPIC
- .ervo motor-driven linear robots
- 3 axis robot
- 3 axis robots
- 3 in 1 Compact Dehumidifying Dryer
- 3-axis robot
- 3-axis robots
- 5-axis CNC machine
- accuracy
- Air Chillers
- all electric injection molding machine
- all electric injection molding machines
- All-electric injection molding machines
- and overall production quality. Therefore
- AP-RubberPlas
- automated injection molding machine
- Automation changed engineering
- automation of injection molding robots
- auxiliary machine
- Bench Injection Molding Machine
- Cabinet dryer manufacturers
- Cabinet dryers
- chiller
- CNC Drilling Machine
- CNC Drilling Machines
- cnc engraving machine manufacturer
- cnc laser cutting machine manufacturer
- CNC machine
- CNC Machine Center
- CNC Machine for Sale
- CNC Machine Manufacturing
- CNC Machine Tool
- CNC machine tool product
- CNC Machining Center
- CNC wood carving machine
- Cooling system
- Cross-Walking Single Axis Servo Cylinder Robot
- Cross-Walking Single-Axis Servo Cylinder Robot
- Cross-Walking Three-Axis/Five-Axis Servo Driven Robot
- cross-walking three-axis/five-axis servo-driven robot
- Dehumidifier Dryer
- Dehumidifying Dryer
- delta parallel robot
- Desktop Injection Molding Machine
- Desktop injection molding machines
- Desktop Molding Machine
- desktop plastic injection machine
- Desktop Plastic Injection Molding Machine
- direct clamp injection molding machine
- Direct clamp injection molding machines
- Dosing & mixing system
- Drilling Centers
- Drying and dehumidification system
- drying and dehumidifying equipment
- Drying and Dehumidifying System
- drying system
- effective and efficient. Cabinet dryers are also used in other industries where large quantities of material need to be dried
- efficient injection molding machine
- elbow hydraulic injection molding machines
- electric injection molding machine
- electric injection molding machines
- energy-efficient injection molding robot
- energy-saving injection molding machine
- etc. Among injection molding robots
- exhibition
- features of CNC machine
- Feeding And Conveying System
- Five Axis Machine Center
- Fully automatic injection molding machine
- Gathering Topstar
- giant injection molding machine
- GMU-600 5-Axis Machining Center
- Granulating & Recycling System
- Heavy duty injection molding machine
- High-precision electric molding machines
- high-precision plastic molding machines
- high-speed all electric injection molding machine
- Honeycomb rotor dehumidifier
- horizontal injection molding machine
- Horizontal Injection Molding Machines
- Horizontal Injection Moulding Machine
- Horizontal Mixer manufacturer
- How The CNC Machine Works
- hybrid injection molding machine
- hydraulic injection molding machine
- Hydraulic Injection Molding Machines
- in this article
- Industrial robot
- Industrial Robot Chinese brand
- industrial robot parts
- industrial robot supplier
- Industrial robots
- Industry Chain
- Injection Manipulator
- injection manipulator robot
- injection mold machines
- Injection molding
- Injection molding automation
- Injection Molding Automation Solution
- injection molding dryer
- Injection molding equipment
- injection molding hopper dryer
- Injection molding machine
- injection molding machine brand
- Injection Molding Machine Factory
- Injection Molding Machine Manufacture
- Injection molding machine manufacturer
- injection molding machine manufacturers
- Injection molding machine procurement
- injection molding machine robotic arm
- injection molding machine with a robot
- Injection molding machines
- injection molding material dehumidifying
- injection molding plant
- Injection Molding Robot
- injection molding robot arm
- Injection molding robot automation
- Injection molding robotic arm
- injection molding robots
- Injection moulding machine
- Injection Moulding Robots
- Injection Robot
- Injection robot arm
- Injection robot manufacturer
- Injection robot wholesale
- injection robots
- intelligent injection molding machines
- Introducing Injection Robot
- It is the best choice for drying large quantities of material at once. Cabinetmakers use these machines because they are fast
- large injection molding machine
- large injection molding machines
- Learn what industrial automation and robotics is
- linear robot
- linear robots
- low speed sound-proof granulator
- machine plastic molding
- make sure to add some! Improvements (2) Keyphrase in introduction: Your keyphrase or its synonyms appear in the first paragraph of the copy
- manipulator machine
- manufacturing
- medical grade injection molding machines
- medical injection molding machine
- medical injection molding machines
- micro injection molding machine
- middle speed granulator
- Mini CNC machine manufacturers.
- Mold Temperature Control System
- mold temperature controller
- mold temperature controllers
- molding material Dehumidifying System
- mould temperature control system
- mould temperature controller
- mould temperature controllers
- New electric injection molding machine
- nitrogen dryer manufacturer
- nitrogen dryer system manufacturer
- Oil type mold temperature controller
- Oil type mold temperature controllers
- open day
- Outbound links: No outbound links appear in this page. Add some! Images: No images appear on this page. Add some! Internal links: No internal links appear in this page
- PET Preform injection molding
- phone case maker machine
- phone case making machine
- plastic bottle making machine
- plastic bottle manufacturing
- plastic bucket making machine
- plastic bucket manufacturing
- Plastic chair making machine
- plastic forming equipment
- plastic hopper dryer
- plastic injection machine
- plastic injection machines
- plastic injection molding
- Plastic injection molding equipment
- Plastic injection molding machine
- Plastic Injection Molding Machines
- plastic injection moulding machine
- plastic injection robot
- Plastic Molding machine
- Plastic Molding Machines
- plastic molding press
- plastic moulding machine
- plastic phone case making machine
- plastic-molding machine
- powerful granulator
- Powerful Type Sound-Proof Granulator
- precision injection molding
- precision injection molding machines
- production of plastic seats
- pure water mould temperature controller
- Robot injection molding
- robot injection molding machine
- robot manufacturing companies
- Robotic arm for injection molding machine
- robotic injection molding machines
- robotics in injection molding
- SCARA robot
- SCARA robots
- Service-oriented manufacturing
- Servo Cylinder Robot
- servo driven robot
- Servo Driven Robots
- servo injection robots
- servo motor-driven linear robots
- servo-driven 3-axis robot
- Servo-Driven Robot
- Setup of injection machine
- Silicone Injection Molding Machine
- six-axis industrial robot
- Stainless Hopper Dryer
- Stainless Hopper Dryers
- star club
- swing arm robot
- take-out robots
- the choice between servo-driven robots and hydraulic robots will have a certain impact on efficiency
- the most popular injection molding machine
- the type of injection molding robot
- toggle clamp injection molding machine
- Toggle Hydraulic Injection Molding Machines
- toggle injection molding machine
- Top 10 brands of injection robots
- Topstar
- Topstar Engineering
- Topstar Industrial Robots
- Topstar injection molding intelligent
- Topstar Scara Robots
- Useful Injection molding machine
- Vertical machining centers
- volumetric type blender
- water chiller
- water chillers
- water distributor
- water type mold temperature controller
- Water Type MoldTemperature Controller
- Water-Type Mould Temperature Controllers
- We often face choices when performing injection molding. We will choose the type of injection molding machine
- wholesale of injection molding machines
- x carve CNC