How To Choose A Horizontal Injection Molding Machine?
2024/03/11 By Topstar
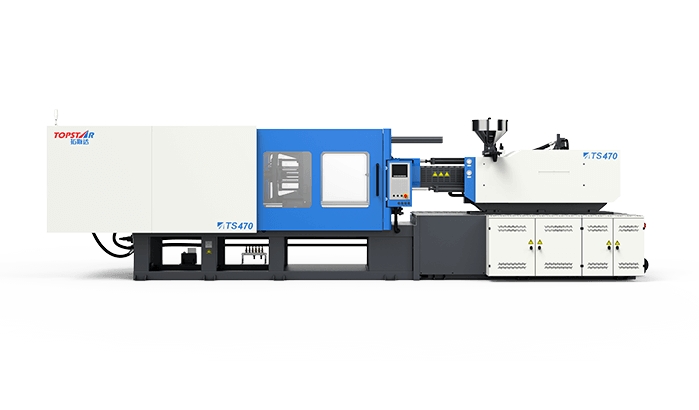
Choosing a suitable horizontal injection molding machine is critical for companies needing an injection molding manufacturing business. The wrong horizontal injection molding machine choice will directly affect the finished product and cause quality problems. So, a suitable horizontal injection molding machine ensures efficient production, high-quality parts, and optimal performance. This comprehensive guide discusses the key factors when choosing a horizontal injection molding machine.
Know your production requirements: capacity, speed, and accuracy
Your production requirements must be carefully evaluated before selecting a horizontal injection molding machine. This includes your requirements for capacity, speed, and accuracy. Capacity refers to the maximum volume of material that a horizontal injection molding machine can hold per cycle or unit time. Matching the capacity of a horizontal injection molding machine to production demand ensures efficient operation without overloading or underutilizing the equipment.
Speed indicates how fast the machine completes each injection molding cycle. Higher speeds increase productivity but must be balanced with other factors such as material flow, cooling time, and part quality. Precision refers to factors such as the consistency of each injection of the machine during the injection process, mold alignment, and control of temperature and pressure.
Choosing the proper horizontal injection molding machine configuration
For their configuration, you can choose hydraulic, electric, or hybrid, depending on your situation. Hydraulics utilize hydraulic power to drive the injection process. Their main features are robustness, high clamping force, and the ability to handle various materials. However, they are less energy efficient and have slower cycle times than electric motors.
Electric injection molding machines use electric servo motors to drive the injection, mold clamping, and ejection systems. They offer faster cycle times, precise control of speed and pressure, and lower energy consumption than hydraulic presses. The motor is also quieter and cleaner.
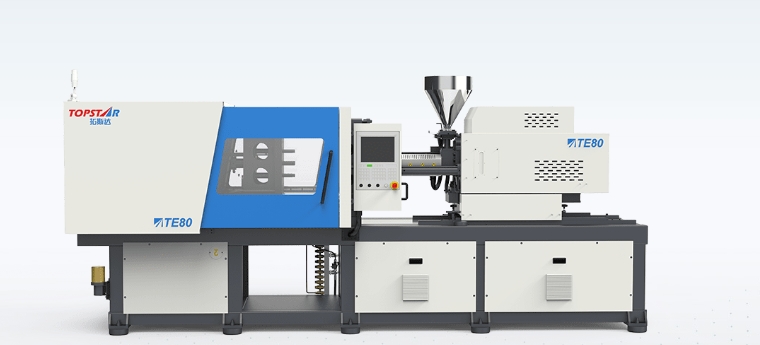
Hybrid injection molding machines combine the advantages of hydraulic and electric systems. They typically use electric servo motors for injection and mold opening/closing motion, while hydraulic power provides clamping force. This configuration is designed to balance energy efficiency, speed, and cost-effectiveness.
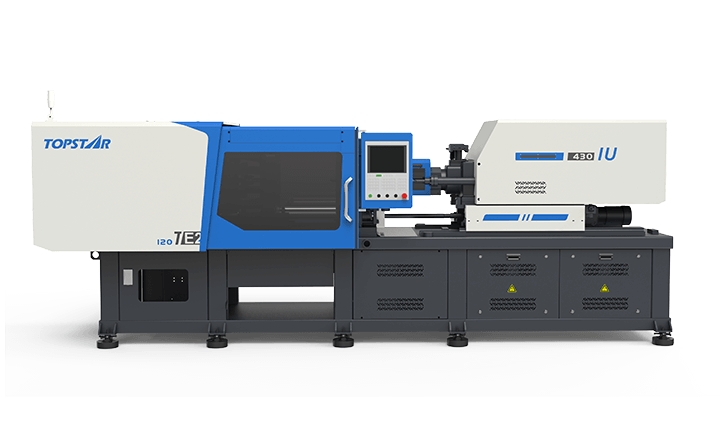
The choice between these three configurations depends on various factors, with hydraulics being more suitable for high clamping force applications. At the same time, electric motors are ideal for precision molding and energy-saving operations. The versatility and flexibility of hybrid machines are viable for various applications, but they also come at a higher price.
Evaluate the capabilities and technology of horizontal injection molding machines
We must also evaluate functionality and technology, including automation, control systems, and safety features. Most suppliers now offer integrated injection molding machine solutions that incorporate automation features such as injection molding robots, auxiliary equipment, and conveyor integration to significantly shorten cycle times, reduce manual labor, and increase overall productivity.
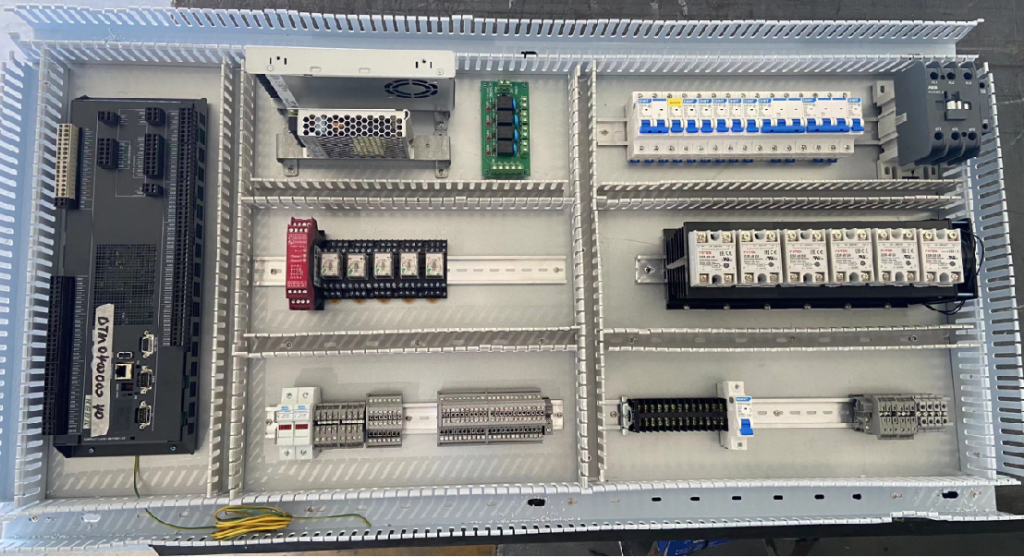
It is also necessary to determine whether they have advanced control systems that provide comprehensive monitoring, adjustment, and optimization functions. These systems enable operators to fine-tune parameters such as injection speed, pressure, temperature, and cooling time to achieve optimal part quality and cycle times. The second is to determine whether it has safety functions. Various safety features are used to protect the operator and equipment.
Consider horizontal injection molding machine reliability and maintenance
Factors such as material quality, construction, and engineering design all affect a machine’s durability. Robust components, corrosion-resistant surfaces, and reinforced construction extend service life and minimize the risk of mechanical failure or damage. Can the supplier provide timely maintenance when problems occur with the injection molding machine? And support services are essential. Reliable customer support services, troubleshooting guides, and remote assistance ensure operators can quickly resolve issues and optimize machine performance. In addition, comprehensive warranty coverage, service contracts, and after-sales support reinforce confidence in the machine’s reliability and long-term value.
Evaluate the total cost of ownership
Evaluating the total cost of ownership of a horizontal injection molding machine must consider the entire life cycle, including depreciation, resale value, and financing options. Additionally, factors such as regulatory compliance, market trends, and technological advancements should be considered to make informed decisions and maximize the value of your machine over time. By evaluating initial investment, operating costs, and return on investment, strategic decisions can be made regarding machine selection, optimization, and utilization to achieve their production goals while maximizing profitability and market competitiveness.
Make the choice that’s right for you
Choosing the suitable horizontal injection molding machine is a critical decision that can impact the success and profitability of your manufacturing operation. As this guide mentions, you can make informed decisions that meet your business needs and goals by carefully evaluating your production requirements, machine capabilities, technology, reliability, maintenance, and more.
TRENDING POSTS
- What factors can cause delays in the injection molding process of plastic molding machine? 2024/03/11
- Exhibition Review| Topstar participates in InterPlas Thailand 2024 2024/03/11
- Star Case | Topstar helps Santong upgrade its intelligent plant 2024/03/11
- Topstar Special | National Science and Technology Workers Day 2024/03/11
HOT TOPIC
- .ervo motor-driven linear robots
- 3 axis robot
- 3 axis robots
- 3 in 1 Compact Dehumidifying Dryer
- 3-axis robot
- 3-axis robots
- 5-axis CNC machine
- accuracy
- Air Chillers
- all electric injection molding machine
- all electric injection molding machines
- All-electric injection molding machines
- and overall production quality. Therefore
- AP-RubberPlas
- automated injection molding machine
- Automation changed engineering
- automation of injection molding robots
- auxiliary machine
- Bench Injection Molding Machine
- Cabinet dryer manufacturers
- Cabinet dryers
- chiller
- CNC Drilling Machine
- CNC Drilling Machines
- cnc engraving machine manufacturer
- cnc laser cutting machine manufacturer
- CNC machine
- CNC Machine Center
- CNC Machine for Sale
- CNC Machine Manufacturing
- CNC Machine Tool
- CNC machine tool product
- CNC Machining Center
- CNC wood carving machine
- Cooling system
- Cross-Walking Single Axis Servo Cylinder Robot
- Cross-Walking Single-Axis Servo Cylinder Robot
- Cross-Walking Three-Axis/Five-Axis Servo Driven Robot
- cross-walking three-axis/five-axis servo-driven robot
- Dehumidifier Dryer
- Dehumidifying Dryer
- delta parallel robot
- Desktop Injection Molding Machine
- Desktop injection molding machines
- Desktop Molding Machine
- desktop plastic injection machine
- Desktop Plastic Injection Molding Machine
- direct clamp injection molding machine
- Direct clamp injection molding machines
- Dosing & mixing system
- Drilling Centers
- Drying and dehumidification system
- drying and dehumidifying equipment
- Drying and Dehumidifying System
- drying system
- effective and efficient. Cabinet dryers are also used in other industries where large quantities of material need to be dried
- efficient injection molding machine
- elbow hydraulic injection molding machines
- electric injection molding machine
- electric injection molding machines
- energy-efficient injection molding robot
- energy-saving injection molding machine
- etc. Among injection molding robots
- exhibition
- features of CNC machine
- Feeding And Conveying System
- Five Axis Machine Center
- Fully automatic injection molding machine
- Gathering Topstar
- giant injection molding machine
- GMU-600 5-Axis Machining Center
- Granulating & Recycling System
- Heavy duty injection molding machine
- High-precision electric molding machines
- high-precision plastic molding machines
- high-speed all electric injection molding machine
- Honeycomb rotor dehumidifier
- horizontal injection molding machine
- Horizontal Injection Molding Machines
- Horizontal Injection Moulding Machine
- Horizontal Mixer manufacturer
- How The CNC Machine Works
- hybrid injection molding machine
- hydraulic injection molding machine
- Hydraulic Injection Molding Machines
- in this article
- Industrial robot
- Industrial Robot Chinese brand
- industrial robot parts
- industrial robot supplier
- Industrial robots
- Industry Chain
- Injection Manipulator
- injection manipulator robot
- injection mold machines
- Injection molding
- Injection molding automation
- Injection Molding Automation Solution
- injection molding dryer
- Injection molding equipment
- injection molding hopper dryer
- Injection molding machine
- injection molding machine brand
- Injection Molding Machine Factory
- Injection Molding Machine Manufacture
- Injection molding machine manufacturer
- injection molding machine manufacturers
- Injection molding machine procurement
- injection molding machine robotic arm
- injection molding machine with a robot
- Injection molding machines
- injection molding material dehumidifying
- injection molding plant
- Injection Molding Robot
- injection molding robot arm
- Injection molding robot automation
- Injection molding robotic arm
- injection molding robots
- Injection moulding machine
- Injection Moulding Robots
- Injection Robot
- Injection robot arm
- Injection robot manufacturer
- Injection robot wholesale
- injection robots
- intelligent injection molding machines
- Introducing Injection Robot
- It is the best choice for drying large quantities of material at once. Cabinetmakers use these machines because they are fast
- large injection molding machine
- Learn what industrial automation and robotics is
- linear robot
- linear robots
- low speed sound-proof granulator
- machine plastic molding
- make sure to add some! Improvements (2) Keyphrase in introduction: Your keyphrase or its synonyms appear in the first paragraph of the copy
- manipulator machine
- manufacturing
- medical grade injection molding machines
- medical injection molding machine
- medical injection molding machines
- micro injection molding machine
- middle speed granulator
- Mini CNC machine manufacturers.
- Mold Temperature Control System
- mold temperature controller
- mold temperature controllers
- molding material Dehumidifying System
- mould temperature control system
- mould temperature controller
- mould temperature controllers
- New electric injection molding machine
- nitrogen dryer manufacturer
- nitrogen dryer system manufacturer
- Oil type mold temperature controller
- Oil type mold temperature controllers
- open day
- Outbound links: No outbound links appear in this page. Add some! Images: No images appear on this page. Add some! Internal links: No internal links appear in this page
- PET Preform injection molding
- phone case maker machine
- phone case making machine
- plastic bottle making machine
- plastic bottle manufacturing
- plastic bucket making machine
- plastic bucket manufacturing
- Plastic chair making machine
- plastic forming equipment
- plastic hopper dryer
- plastic injection machine
- plastic injection machines
- plastic injection molding
- Plastic injection molding equipment
- Plastic injection molding machine
- Plastic Injection Molding Machines
- plastic injection moulding machine
- plastic injection robot
- Plastic Molding machine
- Plastic Molding Machines
- plastic molding press
- plastic moulding machine
- plastic phone case making machine
- plastic-molding machine
- powerful granulator
- Powerful Type Sound-Proof Granulator
- precision injection molding
- production of plastic seats
- pure water mould temperature controller
- Robot injection molding
- robot injection molding machine
- robot manufacturing companies
- Robotic arm for injection molding machine
- robotic injection molding machines
- robotics in injection molding
- SCARA robot
- SCARA robots
- Service-oriented manufacturing
- Servo Cylinder Robot
- servo driven robot
- Servo Driven Robots
- servo injection robots
- servo motor-driven linear robots
- servo-driven 3-axis robot
- Servo-Driven Robot
- Setup of injection machine
- Silicone Injection Molding Machine
- six-axis industrial robot
- Stainless Hopper Dryer
- Stainless Hopper Dryers
- star club
- swing arm robot
- take-out robots
- the choice between servo-driven robots and hydraulic robots will have a certain impact on efficiency
- the most popular injection molding machine
- the type of injection molding robot
- toggle clamp injection molding machine
- Toggle Hydraulic Injection Molding Machines
- toggle injection molding machine
- Top 10 brands of injection robots
- Topstar
- Topstar Engineering
- Topstar Industrial Robots
- Topstar injection molding intelligent
- Topstar Scara Robots
- Useful Injection molding machine
- Vertical machining centers
- volumetric type blender
- water chiller
- water chillers
- water distributor
- water type mold temperature controller
- Water Type MoldTemperature Controller
- Water-Type Mould Temperature Controllers
- We often face choices when performing injection molding. We will choose the type of injection molding machine
- wholesale of injection molding machines
- x carve CNC