How to choose injection molding machines with different clamping forces?
2025/04/28 By Topstar
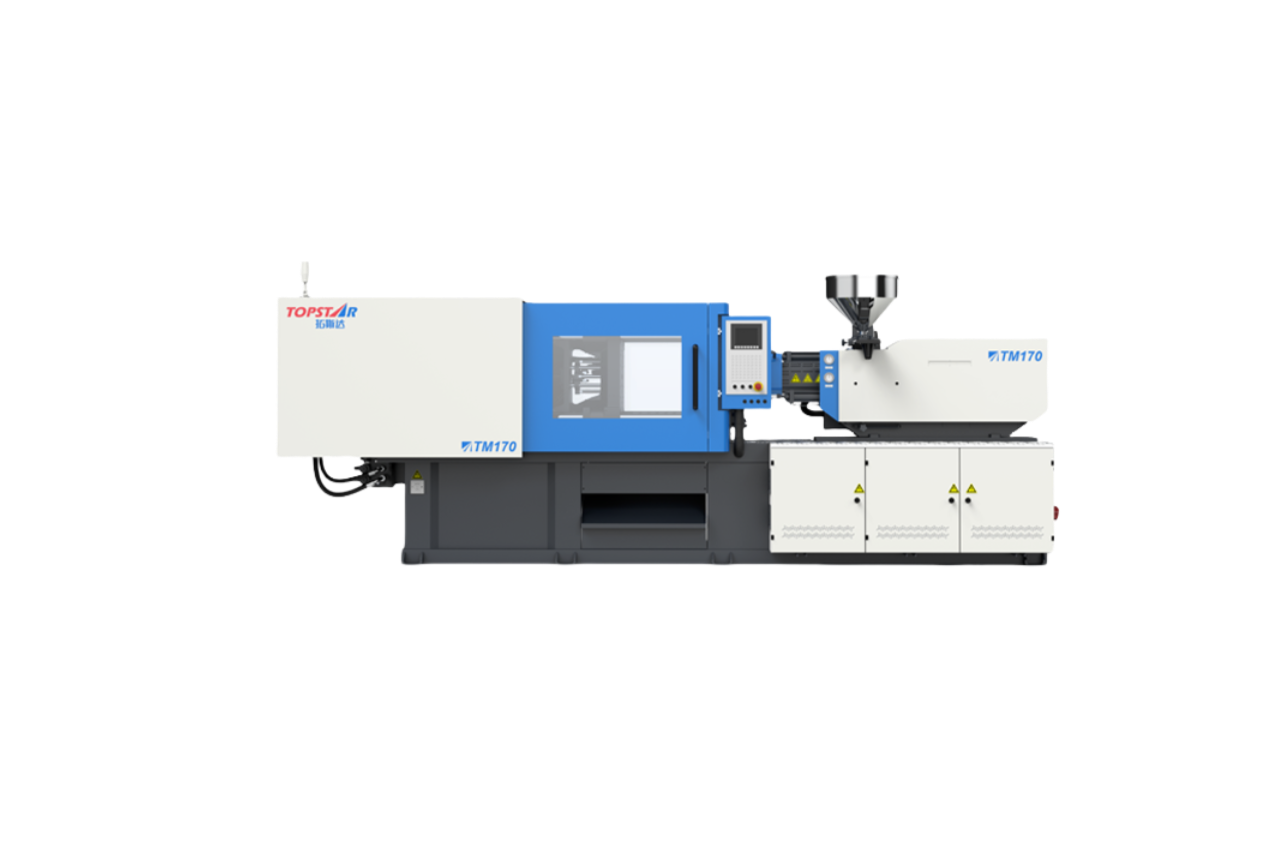
Clamping force refers to the force applied by the machine during the injection molding process to hold the two halves of the mold together and prevent them from separating under the pressure of the molten plastic. When purchasing injection molding machines, choosing the right clamping force ensures the molded part is formed accurately without defects such as flash or incomplete filling.
Topstar offers a wide range of clamping force options in its injection molding machine range, from 90 tons to 470 tons, and from 550 tons to 2800 tons for larger injection molding machines. Choosing the right clamping force is essential to producing high-quality products in various industries, from automotive parts to medical devices. This guide will outline the key factors to consider when selecting clamping force and provide specific product examples to help you decide.
What does the clamping force do for an injection molding machine?
The clamping force of an injection molding machine is a key factor in ensuring that the mold remains firmly closed during the injection process, allowing the plastic to be injected into the mold cavity at the correct pressure. If the clamping force is insufficient, the mold may open slightly, resulting in defects such as flash, excess plastic around the part, or incomplete molding. If the clamping force is too high, it will increase cycle time, energy consumption, and wear on the machine.
Topstar injection molding machines have clamping forces between 90 tons and 470 tons for products that require less clamping force, and large injection molding machines have clamping forces between 550 tons and 2800 tons for heavier and more complex molds. When you purchase an injection molding machine, you will base the clamping force on the size and complexity of the mold, the injection molding material, and the product you produce.
Injection molding machines with clamping forces between 90t and 470t: suitable products and applications
Manufacturers generally use injection molding machines with clamping forces ranging from 90 to 470 tons to produce small and medium-sized products. These machines are versatile and can process a variety of plastics, including thermoplastics, elastomers and engineering plastics. Clamping forces in this range are ideal for manufacturers producing the following products:
- Consumer electronics: Components such as smartphone housings, tablet housings and remote control parts require medium precision and efficient production cycles.
- Small household appliances: Plastic parts for coffee machines, blenders, or vacuum cleaners require good surface quality and dimensional accuracy.
- Packaging materials, such as lids, closures, and caps for containers of daily necessities, usually require a low to medium clamping force to ensure a seal without deformation.
- Automotive parts: Small parts such as knobs, buttons or decorative parts do not require heavy clamping force but still require accuracy and consistency.
These injection molding machines can produce parts of medium complexity, and their size and efficiency make them ideal for high-volume production. Choose an injection molding machine with a clamping force of 90 tons to 470 tons to meet the injection molding needs of industries such as electronics, household goods and packaging.
Injection molding machines with a clamping force of 550t-2800t: heavy-duty applications
For larger and more complex molds, injection molding machines with a clamping force between 550 tons and 2800 tons are required to ensure the mold is closed correctly and the part is formed. These injection molding machines are designed to handle the higher pressures and larger volumes of material required to produce heavy, high-performance parts. Products that typically require this clamping force include:
- Automotive parts: Larger bumpers, dashboards, and interior trims require higher clamping forces to ensure accurate molding and durability.
- Industrial equipment parts, such as housings, brackets, or gears used in heavy machinery and industrial applications, need to be produced with high precision and strength.
- Medical devices: Larger medical parts, such as injection sites, diagnostic equipment parts, and even medical device housings, require strict precision and material requirements.
- Packaging housing solutions: Larger packaging products, such as industrial containers or housings for large household appliances, require heavy molds to achieve the correct strength and function.
These high-tonnage injection molding machines are particularly suitable for industries that require complex and large products, which demand high injection forces and advanced features such as multi-cavity molds, automation, and precise material handling. Their higher clamping forces can ensure consistent product quality and efficiency in large-scale production.
Relationship between material type and clamping force
The type of material used in the injection molding process plays a vital role in determining the required clamping force. Due to viscosity differences during the injection molding process, thermoplastics require less clamping force than engineering plastics. Materials with higher viscosities generally require more clamping force to prevent the mold from separating under pressure.
Generally speaking, a machine with a clamping force in the 90ton to 470ton range is sufficient for lighter materials or smaller products. However, for materials that require higher injection pressures, such as high-performance plastics used in the automotive or medical industries, you need a machine with a clamping force in the 550ton to 2,800ton range to ensure controllable and stable molding processes. The balance between material selection and clamping force can achieve the desired product quality and minimize defects during production.
Choosing the right clamping force
Choosing the right injection molding machine and the correct clamping force at purchase can lead to high-quality, cost-effective production. The right clamping force ensures consistent results, reduces defects, and increases production efficiency. Whether you are producing small consumer products or large industrial parts, the right choice will contribute to the long-term success of your manufacturing process and cost savings.
TRENDING POSTS
- What factors can cause delays in the injection molding process of plastic molding machine? 2025/04/28
- Exhibition Review| Topstar participates in InterPlas Thailand 2024 2025/04/28
- Star Case | Topstar helps Santong upgrade its intelligent plant 2025/04/28
- Topstar Special | National Science and Technology Workers Day 2025/04/28
HOT TOPIC
- .ervo motor-driven linear robots
- 1.0 guangdong topstar technology co. ltd
- 1.0 topstar china
- 1.0 topstar robot
- 11
- 2
- 21
- 23
- 3 axis robot
- 3 axis robots
- 3 in 1 Compact Dehumidifying Dryer
- 3-axis robot
- 3-axis robots
- 39
- 41
- 5-axis CNC machine
- 62
- accuracy
- Air Chillers
- all electric injection molding machine
- all electric injection molding machines
- All-electric injection molding machines
- and overall production quality. Therefore
- AP-RubberPlas
- automated injection molding machine
- Automation changed engineering
- automation of injection molding robots
- auxiliary machine
- Bench Injection Molding Machine
- Cabinet dryer manufacturers
- Cabinet dryers
- chiller
- CNC Drilling Machine
- CNC Drilling Machines
- cnc engraving machine manufacturer
- cnc laser cutting machine manufacturer
- CNC machine
- CNC Machine Center
- CNC Machine for Sale
- CNC Machine Manufacturing
- CNC Machine Tool
- CNC machine tool product
- CNC Machining Center
- CNC wood carving machine
- Cooling system
- Cross-Walking Single Axis Servo Cylinder Robot
- Cross-Walking Single-Axis Servo Cylinder Robot
- Cross-Walking Three-Axis/Five-Axis Servo Driven Robot
- cross-walking three-axis/five-axis servo-driven robot
- Dehumidifier Dryer
- Dehumidifying Dryer
- delta parallel robot
- Desktop Injection Molding Machine
- Desktop injection molding machines
- Desktop Molding Machine
- desktop plastic injection machine
- Desktop Plastic Injection Molding Machine
- direct clamp injection molding machine
- Direct clamp injection molding machines
- Dosing & mixing system
- Drilling Centers
- Drying and dehumidification system
- drying and dehumidifying equipment
- Drying and Dehumidifying System
- drying system
- effective and efficient. Cabinet dryers are also used in other industries where large quantities of material need to be dried
- efficient injection molding machine
- elbow hydraulic injection molding machines
- electric injection molding machine
- electric injection molding machines
- energy-efficient injection molding robot
- energy-efficient water chiller
- energy-efficient water chillers
- energy-saving injection molding machine
- etc. Among injection molding robots
- exhibition
- features of CNC machine
- Feeding And Conveying System
- Five Axis Machine Center
- Fully automatic injection molding machine
- Gathering Topstar
- giant injection molding machine
- GMU-600 5-Axis Machining Center
- Granulating & Recycling System
- Heavy duty injection molding machine
- High-precision electric molding machines
- high-precision plastic molding machines
- high-speed all electric injection molding machine
- high-speed electric injection molding machine
- High-Speed Packaging Injection Molding
- Honeycomb rotor dehumidifier
- horizontal injection molding machine
- Horizontal Injection Molding Machines
- Horizontal Injection Moulding Machine
- Horizontal Mixer manufacturer
- How The CNC Machine Works
- hybrid injection molding machine
- hydraulic injection molding machine
- Hydraulic Injection Molding Machines
- in this article
- Industrial robot
- Industrial Robot Chinese brand
- industrial robot parts
- industrial robot supplier
- Industrial robots
- Industry Chain
- Injection Manipulator
- injection manipulator robot
- injection mold machines
- Injection molding
- Injection molding automation
- Injection Molding Automation Solution
- injection molding dryer
- Injection molding equipment
- injection molding hopper dryer
- Injection molding machine
- injection molding machine brand
- Injection Molding Machine Factory
- Injection Molding Machine Manufacture
- Injection molding machine manufacturer
- injection molding machine manufacturers
- Injection molding machine procurement
- injection molding machine robotic arm
- injection molding machine with a robot
- Injection molding machines
- injection molding material dehumidifying
- injection molding plant
- injection molding process
- Injection Molding Robot
- injection molding robot arm
- Injection molding robot automation
- Injection molding robotic arm
- injection molding robots
- Injection moulding machine
- injection moulding machines
- Injection Moulding Robots
- Injection Robot
- Injection robot arm
- Injection robot manufacturer
- Injection robot wholesale
- injection robots
- intelligent injection molding machines
- intelligent mold temperature
- intelligent mold temperature controller
- Intelligent mould temperature controller
- Introducing Injection Robot
- It is the best choice for drying large quantities of material at once. Cabinetmakers use these machines because they are fast
- Large flow water type mold temperature controller
- large injection molding machine
- large injection molding machines
- Learn what industrial automation and robotics is
- linear robot
- linear robots
- low speed sound-proof granulator
- machine plastic molding
- make sure to add some! Improvements (2) Keyphrase in introduction: Your keyphrase or its synonyms appear in the first paragraph of the copy
- manipulator machine
- manufacturing
- medical grade injection molding machines
- medical injection molding machine
- medical injection molding machines
- micro injection molding machine
- middle speed granulator
- Mini CNC machine manufacturers.
- Mold Temperature Control System
- mold temperature controller
- mold temperature controllers
- molding material Dehumidifying System
- mould temperature control system
- mould temperature controller
- mould temperature controllers
- New electric injection molding machine
- nitrogen dryer manufacturer
- nitrogen dryer system manufacturer
- Oil type mold temperature controller
- Oil type mold temperature controllers
- open day
- Outbound links: No outbound links appear in this page. Add some! Images: No images appear on this page. Add some! Internal links: No internal links appear in this page
- PET Preform injection molding
- phone case maker machine
- phone case making machine
- phone cover making machine
- plastic bottle making machine
- plastic bottle manufacturing
- plastic bucket making machine
- plastic bucket manufacturing
- Plastic chair making machine
- plastic forming equipment
- plastic hopper dryer
- plastic injection machine
- plastic injection machines
- plastic injection molding
- Plastic injection molding equipment
- Plastic injection molding machine
- Plastic Injection Molding Machines
- plastic injection moulding machine
- plastic injection moulding machines
- plastic injection robot
- plastic molding
- Plastic Molding machine
- plastic molding machine 1
- Plastic Molding Machines
- plastic molding press
- plastic moulding machine
- plastic phone case making machine
- plastic-molding machine
- powerful granulator
- Powerful Type Sound-Proof Granulator
- precision injection molding
- precision injection molding machines
- production of plastic seats
- pure water mould temperature controller
- Robot injection molding
- robot injection molding machine
- robot manufacturing companies
- Robotic arm for injection molding machine
- robotic injection molding machines
- robotics in injection molding
- SCARA robot
- SCARA robots
- Service-oriented manufacturing
- Servo Cylinder Robot
- servo driven robot
- Servo Driven Robots
- servo injection molding machine
- servo injection robots
- servo motor-driven linear robots
- servo-driven 3-axis robot
- Servo-Driven Robot
- Setup of injection machine
- Silicone Injection Molding Machine
- six-axis industrial robot
- Stainless Hopper Dryer
- Stainless Hopper Dryers
- star club
- swing arm robot
- take-out robot
- take-out robots
- the choice between servo-driven robots and hydraulic robots will have a certain impact on efficiency
- the most popular injection molding machine
- the type of injection molding robot
- TMII injection molding machine
- toggle clamp injection molding machine
- Toggle Hydraulic Injection Molding Machines
- toggle injection molding machine
- Top 10 brands of injection robots
- Topstar
- Topstar Engineering
- Topstar Industrial Robots
- Topstar injection molding intelligent
- Topstar Scara Robots
- Useful Injection molding machine
- Vertical machining centers
- volumetric type blender
- water chiller
- water chillers
- water distributor
- water type mold temperature controller
- Water Type MoldTemperature Controller
- Water-Type Mould Temperature Controllers
- We often face choices when performing injection molding. We will choose the type of injection molding machine
- wholesale of injection molding machines
- x carve CNC
- 热门查询 点击次数 展示 排名 topstar