How to evaluate the performance of a Plastic chair making machine?
2024/07/03 By Topstar
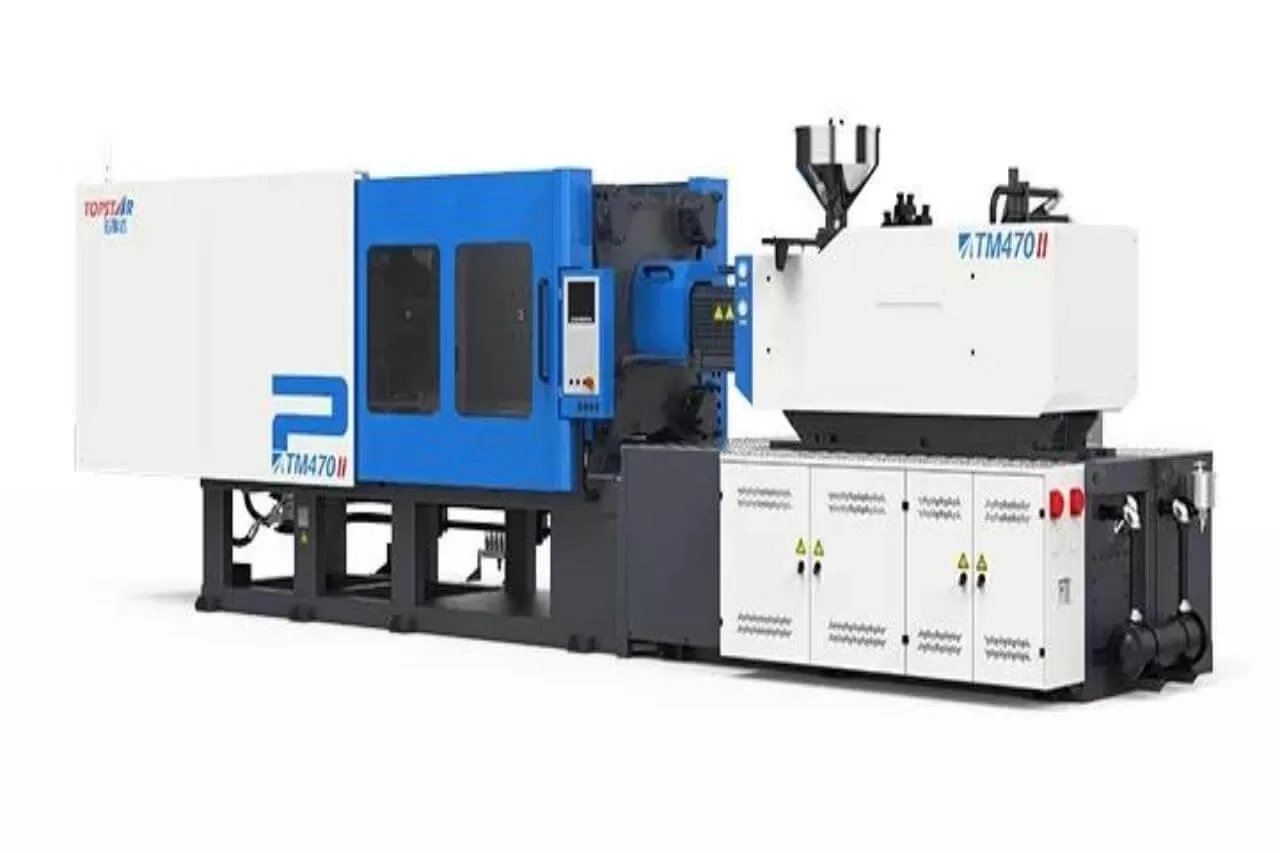
Plastic chair making machine can produce high-quality plastic chairs efficiently and economically on a large scale. There are many different models of plastic chair-making machines for plastic chair manufacturers, and we can evaluate their performance through stability, precision, energy efficiency, and other aspects. This guide will tell you the fundamental aspects of the performance of plastic chair making machines at Topstar.
Adopting Diagonal double injection mold shift oil cylinders and linear guides
In terms of injection stability of plastic chair making machines, we use diagonal double injection mold shift oil cylinders and linear guides. The diagonal direction of the diagonal double shot cylinders makes the injection force more evenly distributed in the mold. This makes the performance of the injection process more stable, reduces the risk of defects, and ensures consistent quality of plastic chair production. At the same time, the double shot mechanism can accurately control the injection volume and pressure. It can produce chairs with uniform wall thickness and consistent structural integrity, meeting the high standards required by the industry. In addition, it helps to shorten the cycle time. The use of linear guides further improves the stability and precision of the injection process.
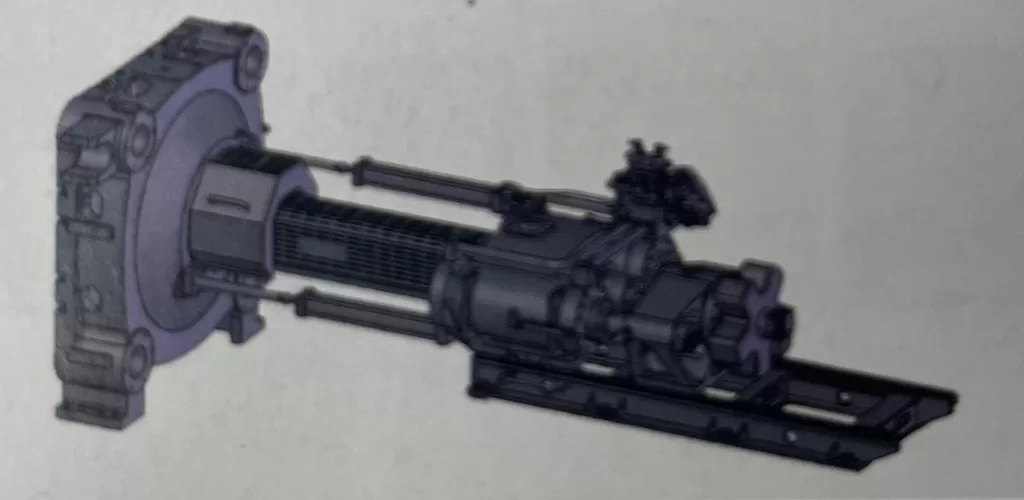
Central direct press clamping structure for plastic chair making machine
In terms of high product molding accuracy, we use a central direct press clamping structure, which applies uniform clamping force across the entire mold through a central direct press clamping structure. This uniform force distribution ensures that the mold halves are perfectly aligned during injection. This distributes the clamping force in the center of the mold plate, minimizes the deformation of the machine plate, prevents the mold from being affected by the machine plate’s deformation, and ensures high product molding accuracy. Minimizing die deflection and deformation and applying constant clamping pressure also helps eliminate common defects such as burrs, dents, etc. The efficiency of the clamping mechanism helps reduce cycle times by ensuring fast and stable clamping and unclamping actions.
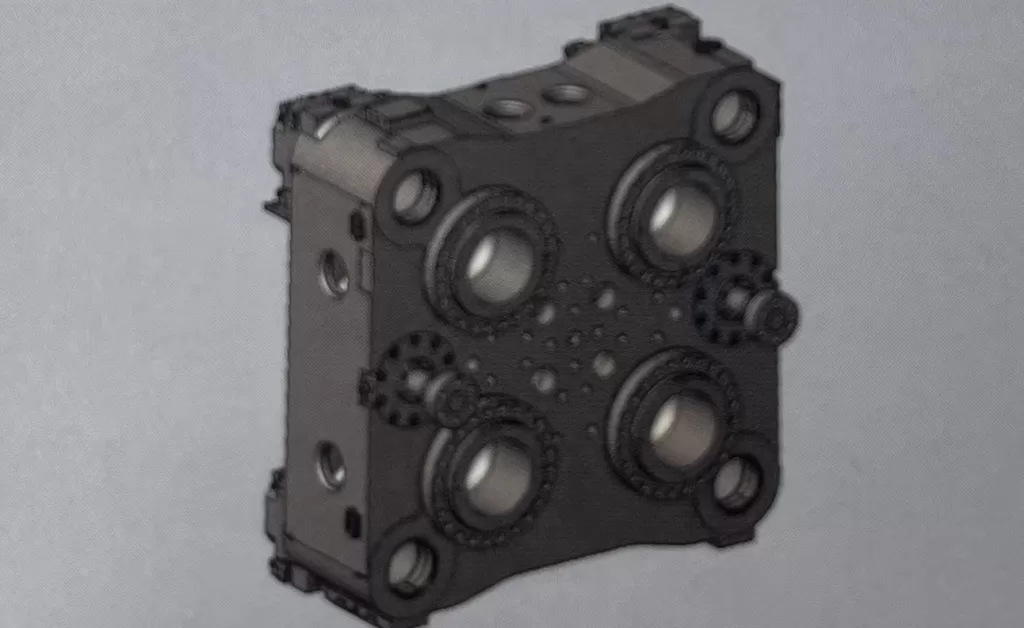
Using CNC proportional back pressure
CNC proportional back pressure control in the plastic chair making machine allows precise adjustment of the melt-back pressure during the injection molding process. This precision ensures the melt is always uniform, reducing the risk of air entrapment and material inconsistency. Maintaining a consistent back pressure, CNC control ensures that the plastic melt is well-mixed and uniform. This uniformity is essential for producing plastic chairs with uniform strength, color, and surface finish. Precise back pressure control minimizes defects such as voids, sink marks, and warping. The result is a higher quality product with excellent appearance and structural performance.
Equipped with professional plasticizing components
Topstar’s plastic chair making machines have state-of-the-art plasticizing units to ensure optimal processing of different materials. The plasticizing unit uses high-performance chrome-plated screws to process a variety of materials, from standard thermoplastics to engineering resins. Designers have designed these screws to ensure efficient melting and homogenization of plastic materials to meet the unique requirements of various polymers. They have also designed the metering section of the screw to accurately control the material flow and ensure that the correct amount of material is delivered to the mold. In addition, the plasticizing unit also uses a high-color mixing/high-mixing screw to enhance the mixing of colorants and base materials to meet high-color mixing products. These components ensure uniform color distribution, eliminating streaks and color changes.
Plastic Chair Making Machine with More User Experience Focus
Our designers prioritized operator comfort and accessibility in the industrial design of our plastic chair making machines. Designers carefully arrange the control panel and maintenance points to minimize operator strain and improve ease of use, creating a more ergonomic layout. A better user experience requires an intuitive user interface. It allows operators to navigate settings easily, quickly access them, monitor parameters, and troubleshoot. Real-time data visualization helps operators make informed decisions and maintain optimal production conditions.
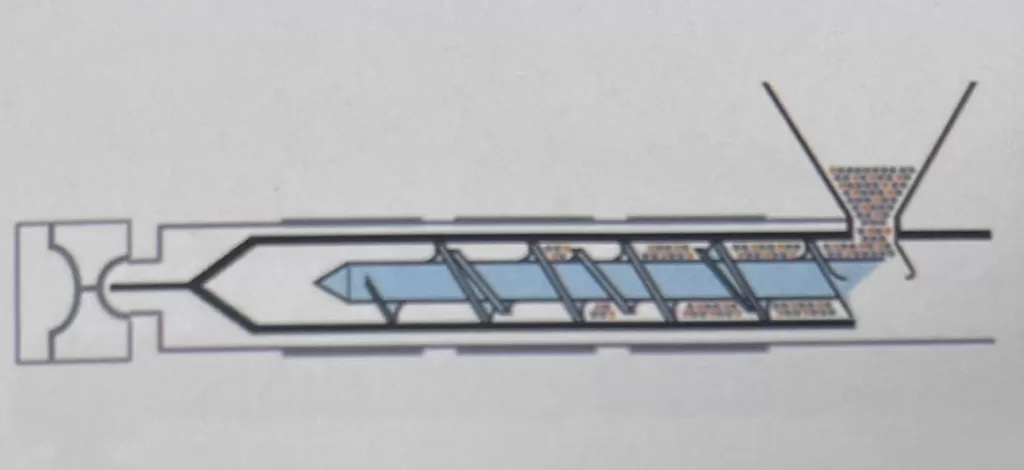
Give you a better experience
The performance of plastic chair making machines involves a comprehensive evaluation of various factors, including stability, product molding accuracy, precision, user experience, etc. Through these comprehensive performances, the plastic chairs they produce can have a smoother surface and more uniform quality.
TRENDING POSTS
- What factors can cause delays in the injection molding process of plastic molding machine? 2024/07/03
- Exhibition Review| Topstar participates in InterPlas Thailand 2024 2024/07/03
- Star Case | Topstar helps Santong upgrade its intelligent plant 2024/07/03
- Topstar Special | National Science and Technology Workers Day 2024/07/03
HOT TOPIC
- .ervo motor-driven linear robots
- 3 axis robot
- 3 axis robots
- 3 in 1 Compact Dehumidifying Dryer
- 3-axis robot
- 3-axis robots
- 5-axis CNC machine
- accuracy
- Air Chillers
- all electric injection molding machine
- all electric injection molding machines
- All-electric injection molding machines
- and overall production quality. Therefore
- AP-RubberPlas
- automated injection molding machine
- Automation changed engineering
- automation of injection molding robots
- auxiliary machine
- Bench Injection Molding Machine
- Cabinet dryer manufacturers
- Cabinet dryers
- chiller
- CNC Drilling Machine
- CNC Drilling Machines
- cnc engraving machine manufacturer
- cnc laser cutting machine manufacturer
- CNC machine
- CNC Machine Center
- CNC Machine for Sale
- CNC Machine Manufacturing
- CNC Machine Tool
- CNC machine tool product
- CNC Machining Center
- CNC wood carving machine
- Cooling system
- Cross-Walking Single Axis Servo Cylinder Robot
- Cross-Walking Single-Axis Servo Cylinder Robot
- Cross-Walking Three-Axis/Five-Axis Servo Driven Robot
- cross-walking three-axis/five-axis servo-driven robot
- Dehumidifier Dryer
- Dehumidifying Dryer
- delta parallel robot
- Desktop Injection Molding Machine
- Desktop injection molding machines
- Desktop Molding Machine
- desktop plastic injection machine
- Desktop Plastic Injection Molding Machine
- direct clamp injection molding machine
- Direct clamp injection molding machines
- Dosing & mixing system
- Drilling Centers
- Drying and dehumidification system
- drying and dehumidifying equipment
- Drying and Dehumidifying System
- drying system
- effective and efficient. Cabinet dryers are also used in other industries where large quantities of material need to be dried
- efficient injection molding machine
- elbow hydraulic injection molding machines
- electric injection molding machine
- electric injection molding machines
- energy-efficient injection molding robot
- energy-saving injection molding machine
- etc. Among injection molding robots
- exhibition
- features of CNC machine
- Feeding And Conveying System
- Five Axis Machine Center
- Fully automatic injection molding machine
- Gathering Topstar
- giant injection molding machine
- GMU-600 5-Axis Machining Center
- Granulating & Recycling System
- Heavy duty injection molding machine
- High-precision electric molding machines
- high-precision plastic molding machines
- high-speed all electric injection molding machine
- Honeycomb rotor dehumidifier
- horizontal injection molding machine
- Horizontal Injection Molding Machines
- Horizontal Injection Moulding Machine
- Horizontal Mixer manufacturer
- How The CNC Machine Works
- hybrid injection molding machine
- hydraulic injection molding machine
- Hydraulic Injection Molding Machines
- in this article
- Industrial robot
- Industrial Robot Chinese brand
- industrial robot parts
- industrial robot supplier
- Industrial robots
- Industry Chain
- Injection Manipulator
- injection manipulator robot
- injection mold machines
- Injection molding
- Injection molding automation
- Injection Molding Automation Solution
- injection molding dryer
- Injection molding equipment
- injection molding hopper dryer
- Injection molding machine
- injection molding machine brand
- Injection Molding Machine Factory
- Injection Molding Machine Manufacture
- Injection molding machine manufacturer
- injection molding machine manufacturers
- Injection molding machine procurement
- injection molding machine robotic arm
- injection molding machine with a robot
- Injection molding machines
- injection molding material dehumidifying
- injection molding plant
- Injection Molding Robot
- injection molding robot arm
- Injection molding robot automation
- Injection molding robotic arm
- injection molding robots
- Injection moulding machine
- Injection Moulding Robots
- Injection Robot
- Injection robot arm
- Injection robot manufacturer
- Injection robot wholesale
- injection robots
- intelligent injection molding machines
- Introducing Injection Robot
- It is the best choice for drying large quantities of material at once. Cabinetmakers use these machines because they are fast
- large injection molding machine
- Learn what industrial automation and robotics is
- linear robot
- linear robots
- low speed sound-proof granulator
- machine plastic molding
- make sure to add some! Improvements (2) Keyphrase in introduction: Your keyphrase or its synonyms appear in the first paragraph of the copy
- manipulator machine
- manufacturing
- medical grade injection molding machines
- medical injection molding machine
- medical injection molding machines
- micro injection molding machine
- middle speed granulator
- Mini CNC machine manufacturers.
- Mold Temperature Control System
- mold temperature controller
- mold temperature controllers
- molding material Dehumidifying System
- mould temperature control system
- mould temperature controller
- mould temperature controllers
- New electric injection molding machine
- nitrogen dryer manufacturer
- nitrogen dryer system manufacturer
- Oil type mold temperature controller
- Oil type mold temperature controllers
- open day
- Outbound links: No outbound links appear in this page. Add some! Images: No images appear on this page. Add some! Internal links: No internal links appear in this page
- PET Preform injection molding
- phone case maker machine
- phone case making machine
- plastic bottle making machine
- plastic bottle manufacturing
- plastic bucket making machine
- plastic bucket manufacturing
- Plastic chair making machine
- plastic forming equipment
- plastic hopper dryer
- plastic injection machine
- plastic injection machines
- plastic injection molding
- Plastic injection molding equipment
- Plastic injection molding machine
- Plastic Injection Molding Machines
- plastic injection moulding machine
- plastic injection robot
- Plastic Molding machine
- Plastic Molding Machines
- plastic molding press
- plastic moulding machine
- plastic phone case making machine
- plastic-molding machine
- powerful granulator
- Powerful Type Sound-Proof Granulator
- precision injection molding
- production of plastic seats
- pure water mould temperature controller
- Robot injection molding
- robot injection molding machine
- robot manufacturing companies
- Robotic arm for injection molding machine
- robotic injection molding machines
- robotics in injection molding
- SCARA robot
- SCARA robots
- Service-oriented manufacturing
- Servo Cylinder Robot
- servo driven robot
- Servo Driven Robots
- servo injection robots
- servo motor-driven linear robots
- servo-driven 3-axis robot
- Servo-Driven Robot
- Setup of injection machine
- Silicone Injection Molding Machine
- six-axis industrial robot
- Stainless Hopper Dryer
- Stainless Hopper Dryers
- star club
- swing arm robot
- take-out robots
- the choice between servo-driven robots and hydraulic robots will have a certain impact on efficiency
- the most popular injection molding machine
- the type of injection molding robot
- toggle clamp injection molding machine
- Toggle Hydraulic Injection Molding Machines
- toggle injection molding machine
- Top 10 brands of injection robots
- Topstar
- Topstar Engineering
- Topstar Industrial Robots
- Topstar injection molding intelligent
- Topstar Scara Robots
- Useful Injection molding machine
- Vertical machining centers
- volumetric type blender
- water chiller
- water chillers
- water distributor
- water type mold temperature controller
- Water Type MoldTemperature Controller
- Water-Type Mould Temperature Controllers
- We often face choices when performing injection molding. We will choose the type of injection molding machine
- wholesale of injection molding machines
- x carve CNC