Injection Molding Machine Manufacture and Mold
2022/12/09 By Topstar
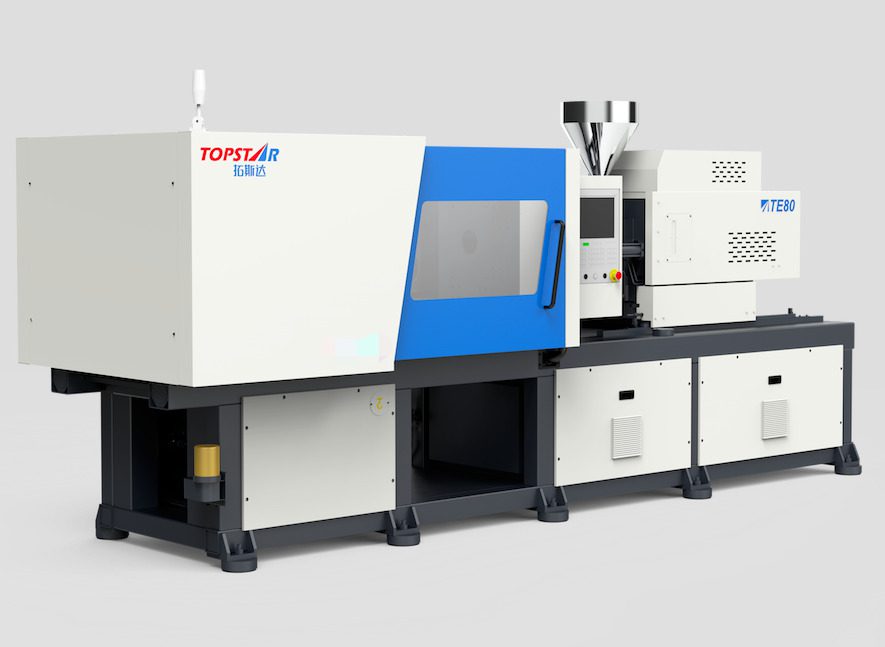
Injection Molding Machine Manufacture and Mold
Injection molding manufacturing produces plastic parts by injecting liquid plastic into a mold cavity. They help improve the speed, accuracy, and automation of operations.
Manufacturing – in the manufacturing process of injection molding machine
In manufacturing injection molding machines, a series of essential functions must be carried out. Forging, casting, milling, threading, and turning are all part of this process. Most often, these processes are done on machines designed specifically for each operation, and if you want your device done right, it is essential to have the right equipment.
Hand forging is one way these parts can be made, but other methods, such as die forging or drop hammer forging, may be better suited for different circumstances or jobs. Die forging tends to create better quality parts than hand-forged ones do because they use more exact measurements when making them (as opposed to just hitting something hard with a hammer until it looks right), but drop hammers tend to work faster, so cost less per unit produced despite being slower overall than die forging which makes up for a lost time in higher quality products at a lower cost per unit multiplied by taking more extended amounts of time altogether.
Injection Molding Machine Manufacture must go through various processes
There are a variety of techniques that a manufacturer must go through when making injection molding machines. These processes include forging, casting, milling, and turning the various parts.
Forging: The process of forging is used to create metal parts for injection molding machines. It involves heating the metal to a high temperature and hammering it into shape using hardened dies made from tool or tungsten carbide steel.
Casting: Casting is also used in manufacturing injection molding machines but instead uses molten metal poured into a mold prepared with wax or another material that will not be affected by heat or pressure during pouring.
Various forging processes
Forging is the process of shaping metal by compressing it with hammers. The material to be forged is placed on an anvil or workbench and repeatedly struck with a hammer. This is known as hand forging and can be used for smaller objects or delicate pieces that require more finesse than other processes allow.
Forging can also be performed using a die set in a press, which will shape large pieces at high speeds without damaging the piece’s surface as hand forging can. Because dies are cheaper than anvils and presses are faster than hammers when it comes to producing large masses of parts, die forging has become widely used in modern manufacturing techniques such as injection molding because they result in more robust products while requiring less labor from workers who operate these machines (and thus less cost).
Hand forging is carried out on an anvil.
Hand Forging: Hand forging is carried out on an anvil. This process is used for smaller parts and may be done in the field. The details are heated, placed into a die, and hammered by hand using tongs (hand tools).
Forging is a process that uses heat and force to shape metal into new forms. Forging can be done by hand or with the aid of machines.
Die forging uses a die set in a press.
Die forging is a molding process that uses a die set in a press to shape metal parts. The metal is placed in the dice and heated to high temperatures. Then pressure is applied by the media, and the amount is shaped as it’s pressed into the mold.
Injection Molding Machine Manufacture and Mold
Injection molding machines are made of several pieces that fit together to create the mold. The details include a barrel, screw, clamping system, and more. Here’s how they work:
Casting is used for many parts but often for the machine’s frame
Casting is a process used to shape molten metal into the desired form. It differs from other methods by using a mold to create the final product rather than shaping it directly with tools, as in forging or machining. Casting can be used for many parts but often for the machine’s frame.
The casting process begins by pouring liquid metal into a mold created by an engineer or designer. Once the metal hardens, the mold is removed, and only its impression remains within the casted piece. Injection Molding Machines are made with this exact process; however, instead of being made from iron or steel (foundry metals), injection molds are made from polymers that are then melted down and reformed into their desired shapes before cooling again into their final state after being removed from their molds once more!
In molding, large molds with many cavities are used.
Injection molding machines are used to make both large and small parts. The device’s size depends on how many features must be produced in one operation. Injection molds are made from either metal or plastic. Plastic molds can be used for small-scale production, which saves time because it does not require finishing work or polishing operations before making the product.
These molds can be made of any material.
Wood molds are the most popular choice for smaller items, such as wooden toys and jewelry. They are simple to work with and require less equipment, so your injection molding machine will be less expensive overall. These molds also tend to be more durable than plastic molds because they won’t crack or break during use.
Greater quantity and higher quality
Plastic molds are usually used for more oversized items because they require less maintenance and can be molded in larger quantities with higher quality results than wood molds. These molds are also more durable and able to withstand the wear and tear of injection molding operations. Most plastic injection molds cost more than wooden ones, but they are worth the investment as they will last much longer.
Wooden molds tend to warp or break if you use them too often, so if you plan on making a lot of one type of product over time, it may be better suited to invest in plastic rather than wood.
Raw materials for injection molding
The materials needed for injection molding manufacturing are metal ores and plastic pellets.
Metal ores are used to make the metal alloys used in the machine. Plastic pellets are used to make the plastic parts of the device.
On the whole
Injection molding machine manufacturing requires a lot of steps and some specialized equipment, but overall it is a relatively straightforward process. The first step is ensuring that your materials are suitable for injection molding. You’ll need plastic pellets or metal ores for this process.
TRENDING POSTS
- What factors can cause delays in the injection molding process of plastic molding machine? 2022/12/09
- Exhibition Review| Topstar participates in InterPlas Thailand 2024 2022/12/09
- Star Case | Topstar helps Santong upgrade its intelligent plant 2022/12/09
- Topstar Special | National Science and Technology Workers Day 2022/12/09
HOT TOPIC
- .ervo motor-driven linear robots
- 3 axis robot
- 3 axis robots
- 3 in 1 Compact Dehumidifying Dryer
- 3-axis robot
- 3-axis robots
- 5-axis CNC machine
- accuracy
- Air Chillers
- all electric injection molding machine
- all electric injection molding machines
- All-electric injection molding machines
- and overall production quality. Therefore
- AP-RubberPlas
- automated injection molding machine
- Automation changed engineering
- automation of injection molding robots
- auxiliary machine
- Bench Injection Molding Machine
- Cabinet dryer manufacturers
- Cabinet dryers
- chiller
- CNC Drilling Machine
- CNC Drilling Machines
- cnc engraving machine manufacturer
- cnc laser cutting machine manufacturer
- CNC machine
- CNC Machine Center
- CNC Machine for Sale
- CNC Machine Manufacturing
- CNC Machine Tool
- CNC machine tool product
- CNC Machining Center
- CNC wood carving machine
- Cooling system
- Cross-Walking Single Axis Servo Cylinder Robot
- Cross-Walking Single-Axis Servo Cylinder Robot
- Cross-Walking Three-Axis/Five-Axis Servo Driven Robot
- cross-walking three-axis/five-axis servo-driven robot
- Dehumidifier Dryer
- Dehumidifying Dryer
- delta parallel robot
- Desktop Injection Molding Machine
- Desktop injection molding machines
- Desktop Molding Machine
- desktop plastic injection machine
- Desktop Plastic Injection Molding Machine
- direct clamp injection molding machine
- Direct clamp injection molding machines
- Dosing & mixing system
- Drilling Centers
- Drying and dehumidification system
- drying and dehumidifying equipment
- Drying and Dehumidifying System
- drying system
- effective and efficient. Cabinet dryers are also used in other industries where large quantities of material need to be dried
- efficient injection molding machine
- elbow hydraulic injection molding machines
- electric injection molding machine
- electric injection molding machines
- energy-efficient injection molding robot
- energy-saving injection molding machine
- etc. Among injection molding robots
- exhibition
- features of CNC machine
- Feeding And Conveying System
- Five Axis Machine Center
- Fully automatic injection molding machine
- Gathering Topstar
- giant injection molding machine
- GMU-600 5-Axis Machining Center
- Granulating & Recycling System
- Heavy duty injection molding machine
- High-precision electric molding machines
- high-precision plastic molding machines
- high-speed all electric injection molding machine
- Honeycomb rotor dehumidifier
- horizontal injection molding machine
- Horizontal Injection Molding Machines
- Horizontal Injection Moulding Machine
- Horizontal Mixer manufacturer
- How The CNC Machine Works
- hybrid injection molding machine
- hydraulic injection molding machine
- Hydraulic Injection Molding Machines
- in this article
- Industrial robot
- Industrial Robot Chinese brand
- industrial robot parts
- industrial robot supplier
- Industrial robots
- Industry Chain
- Injection Manipulator
- injection manipulator robot
- injection mold machines
- Injection molding
- Injection molding automation
- Injection Molding Automation Solution
- injection molding dryer
- Injection molding equipment
- injection molding hopper dryer
- Injection molding machine
- injection molding machine brand
- Injection Molding Machine Factory
- Injection Molding Machine Manufacture
- Injection molding machine manufacturer
- injection molding machine manufacturers
- Injection molding machine procurement
- injection molding machine robotic arm
- injection molding machine with a robot
- Injection molding machines
- injection molding material dehumidifying
- injection molding plant
- Injection Molding Robot
- injection molding robot arm
- Injection molding robot automation
- Injection molding robotic arm
- injection molding robots
- Injection moulding machine
- Injection Moulding Robots
- Injection Robot
- Injection robot arm
- Injection robot manufacturer
- Injection robot wholesale
- injection robots
- intelligent injection molding machines
- Introducing Injection Robot
- It is the best choice for drying large quantities of material at once. Cabinetmakers use these machines because they are fast
- large injection molding machine
- large injection molding machines
- Learn what industrial automation and robotics is
- linear robot
- linear robots
- low speed sound-proof granulator
- machine plastic molding
- make sure to add some! Improvements (2) Keyphrase in introduction: Your keyphrase or its synonyms appear in the first paragraph of the copy
- manipulator machine
- manufacturing
- medical grade injection molding machines
- medical injection molding machine
- medical injection molding machines
- micro injection molding machine
- middle speed granulator
- Mini CNC machine manufacturers.
- Mold Temperature Control System
- mold temperature controller
- mold temperature controllers
- molding material Dehumidifying System
- mould temperature control system
- mould temperature controller
- mould temperature controllers
- New electric injection molding machine
- nitrogen dryer manufacturer
- nitrogen dryer system manufacturer
- Oil type mold temperature controller
- Oil type mold temperature controllers
- open day
- Outbound links: No outbound links appear in this page. Add some! Images: No images appear on this page. Add some! Internal links: No internal links appear in this page
- PET Preform injection molding
- phone case maker machine
- phone case making machine
- plastic bottle making machine
- plastic bottle manufacturing
- plastic bucket making machine
- plastic bucket manufacturing
- Plastic chair making machine
- plastic forming equipment
- plastic hopper dryer
- plastic injection machine
- plastic injection machines
- plastic injection molding
- Plastic injection molding equipment
- Plastic injection molding machine
- Plastic Injection Molding Machines
- plastic injection moulding machine
- plastic injection robot
- Plastic Molding machine
- Plastic Molding Machines
- plastic molding press
- plastic moulding machine
- plastic phone case making machine
- plastic-molding machine
- powerful granulator
- Powerful Type Sound-Proof Granulator
- precision injection molding
- precision injection molding machines
- production of plastic seats
- pure water mould temperature controller
- Robot injection molding
- robot injection molding machine
- robot manufacturing companies
- Robotic arm for injection molding machine
- robotic injection molding machines
- robotics in injection molding
- SCARA robot
- SCARA robots
- Service-oriented manufacturing
- Servo Cylinder Robot
- servo driven robot
- Servo Driven Robots
- servo injection robots
- servo motor-driven linear robots
- servo-driven 3-axis robot
- Servo-Driven Robot
- Setup of injection machine
- Silicone Injection Molding Machine
- six-axis industrial robot
- Stainless Hopper Dryer
- Stainless Hopper Dryers
- star club
- swing arm robot
- take-out robots
- the choice between servo-driven robots and hydraulic robots will have a certain impact on efficiency
- the most popular injection molding machine
- the type of injection molding robot
- toggle clamp injection molding machine
- Toggle Hydraulic Injection Molding Machines
- toggle injection molding machine
- Top 10 brands of injection robots
- Topstar
- Topstar Engineering
- Topstar Industrial Robots
- Topstar injection molding intelligent
- Topstar Scara Robots
- Useful Injection molding machine
- Vertical machining centers
- volumetric type blender
- water chiller
- water chillers
- water distributor
- water type mold temperature controller
- Water Type MoldTemperature Controller
- Water-Type Mould Temperature Controllers
- We often face choices when performing injection molding. We will choose the type of injection molding machine
- wholesale of injection molding machines
- x carve CNC