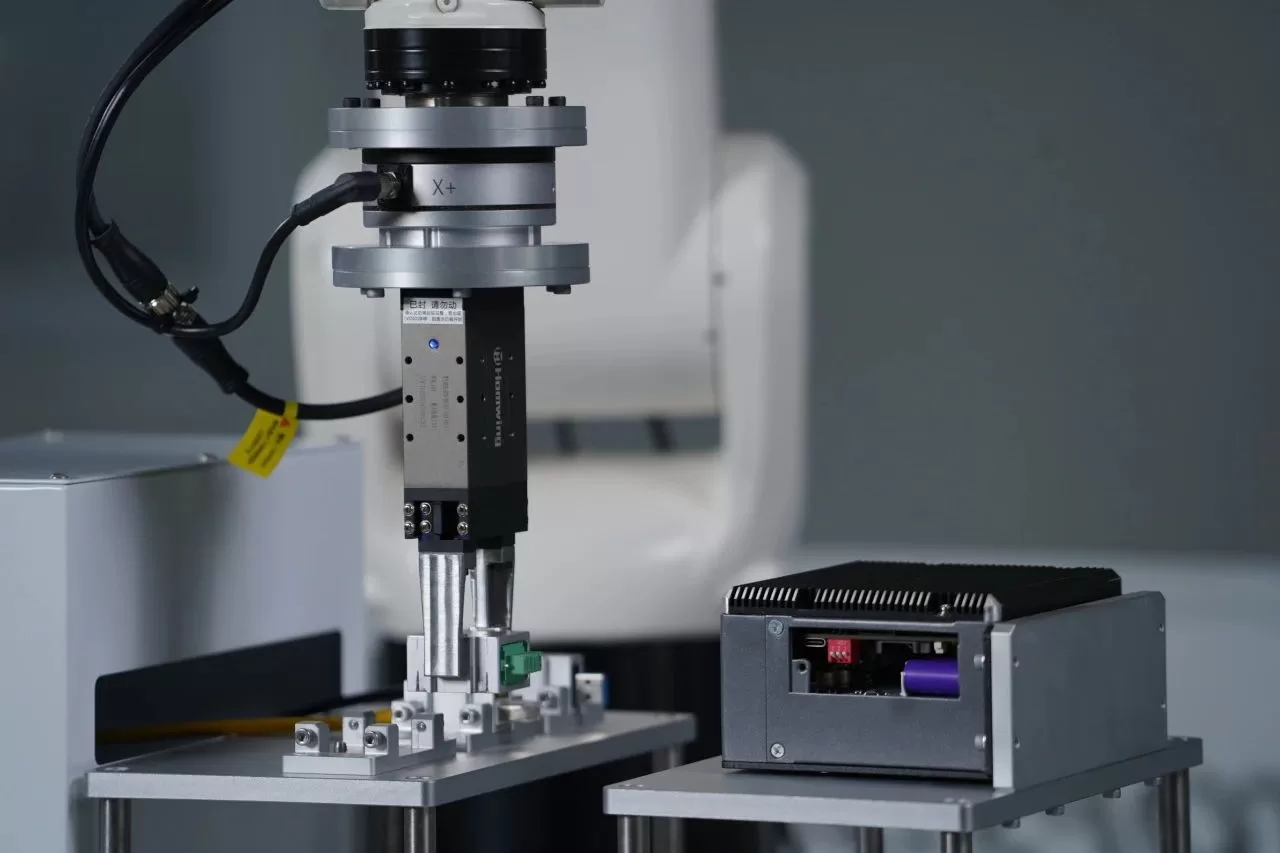
The entire industrial control market has problems such as fragmented standards, closed protocols, and difficulty integrating IT and OT systems. There is an urgent need for a standardized, universal, highly stable, and reliable control solution that lowers the threshold for use so that non-industry technicians can easily operate and maintain it. This year, the new generation of the X5 industrial robot control platform launched by the Topstar Control Platform R&D Center is a core product that realizes full-chain autonomous control from the underlying hardware to upper-level software.
Integration and interaction of the new generation of X5 industrial robot control platform
At the technical architecture level, the new generation of X5 industrial robots adopts a cloud-edge-end architecture. By optimizing the coordination of cloud-side and edge-side computing resources, this architecture uploads the data collected by the end-side equipment to the cloud and edge in real time and accurately, providing strong, high-quality data support for accurate and rapid decision-making on the cloud and edge sides, and providing strong support for enterprises to optimize productivity and improve operational efficiency. At the same time, relying on the mighty computing power of the cloud-edge side, decision results, and intelligent control data can quickly empower the end-side data through the cloud-edge-end architecture, further improving the intelligence of the end-side equipment.
Intelligent large models are no longer limited to a few single data types in their training and reasoning process but must integrate multiple data resources such as images, videos, ultrasound, lidar, infrared, etc. Therefore, they can process and integrate fragmented data formats and efficiently send them to large models for training and reasoning.
More suitable for extremely high-requirement stable control scenarios
The hybrid deployment technology is used in the new generation X5 industrial robot control platform so that algorithm processing and preliminary data processing can be completed efficiently within the general operating system without affecting the stability and real-time operation of the industrial robot. This means that they can perform two tasks, industrial robot control, and data collection and processing, in a single controller, including compression and transmission of multimedia data such as images. In this way, industrial robots or other industrial equipment can use large models for real-time reasoning, allowing the physical world and the virtual world to merge seamlessly, making it suitable for stable control scenarios with extremely high requirements for accuracy and real-time performance.
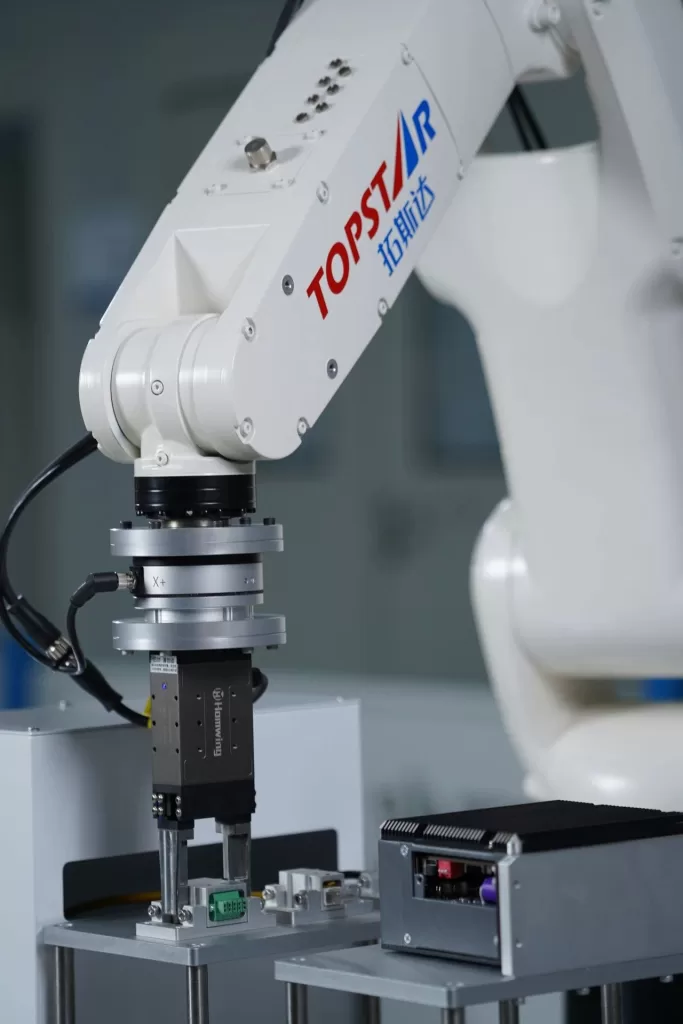
Achieve integration with IT.
Although industrial protocols traditionally provide high real-time performance, they limit integration with IT. In order to better solve the problems of conventional equipment communication interface and system data compatibility and improve the efficiency of cross-platform data transmission, dynamic operation, and configuration, the X5 industrial robot control platform provides more intuitive and easy-to-use communication protocols such as Lua, Python, C#, open more than 400 functional interfaces, and support a variety of communication protocols such as free protocols and SDKs, further broadening the compatibility of industry data, effectively simplifying the data communication process, and significantly improving efficiency. Achieve smooth data interaction between large models and controllers.
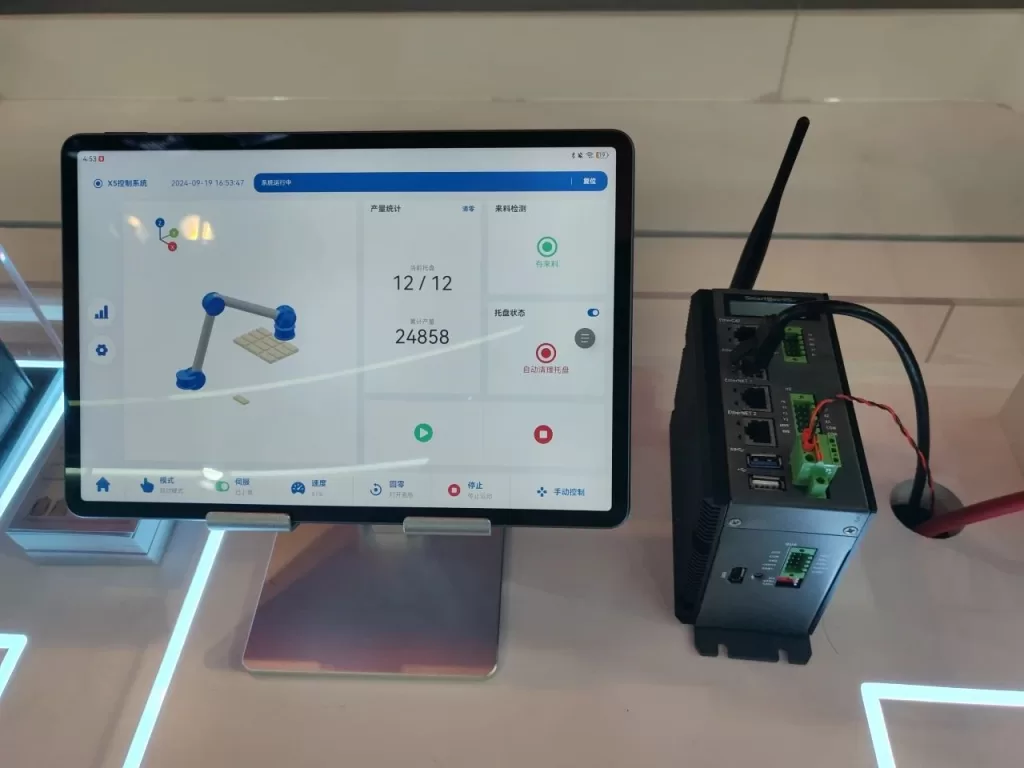
AI and industrial applications
The X5 industrial robot control platform can support a variety of industrial robot models, such as six-axis industrial robots, SCARA, collaborative robots, parallel robots, and palletizing robots, which can meet more than 90% of the robot needs in the industrial field. The platform can make industrial robots smarter, better understand customer needs, and bring customers more efficient and intelligent production solutions. For example, in the robot palletizing scenario, the new generation of motion controller platforms combines large AI models. It takes advantage of code-free development to achieve efficient delivery, low-cost migration and reduced skill requirements for operation and maintenance personnel. Compared with traditional pure code development, the system simplifies the development process, and operators can quickly complete robot palletizing tasks in only three steps.
The Future of industrial robot and Control Platforms
The new generation of industrial robot control platforms combines artificial intelligence, cloud computing, and enhanced flexibility, enabling companies to meet the needs of modern manufacturing. It is not just a tool to control industrial robots but also a comprehensive solution that integrates advanced technology, precision, and flexibility into the core of industrial operations. In the future, Topstar will continue to explore the integration of IT and OT to bring more growth and innovation possibilities.
TRENDING POSTS
- What factors can cause delays in the injection molding process of plastic molding machine? 2025/01/24
- Exhibition Review| Topstar participates in InterPlas Thailand 2024 2025/01/24
- Star Case | Topstar helps Santong upgrade its intelligent plant 2025/01/24
- Topstar Special | National Science and Technology Workers Day 2025/01/24
HOT TOPIC
- .ervo motor-driven linear robots
- 3 axis robot
- 3 axis robots
- 3 in 1 Compact Dehumidifying Dryer
- 3-axis robot
- 3-axis robots
- 5-axis CNC machine
- accuracy
- Air Chillers
- all electric injection molding machine
- all electric injection molding machines
- All-electric injection molding machines
- and overall production quality. Therefore
- AP-RubberPlas
- automated injection molding machine
- Automation changed engineering
- automation of injection molding robots
- auxiliary machine
- Bench Injection Molding Machine
- Cabinet dryer manufacturers
- Cabinet dryers
- chiller
- CNC Drilling Machine
- CNC Drilling Machines
- cnc engraving machine manufacturer
- cnc laser cutting machine manufacturer
- CNC machine
- CNC Machine Center
- CNC Machine for Sale
- CNC Machine Manufacturing
- CNC Machine Tool
- CNC machine tool product
- CNC Machining Center
- CNC wood carving machine
- Cooling system
- Cross-Walking Single Axis Servo Cylinder Robot
- Cross-Walking Single-Axis Servo Cylinder Robot
- Cross-Walking Three-Axis/Five-Axis Servo Driven Robot
- cross-walking three-axis/five-axis servo-driven robot
- Dehumidifier Dryer
- Dehumidifying Dryer
- delta parallel robot
- Desktop Injection Molding Machine
- Desktop injection molding machines
- Desktop Molding Machine
- desktop plastic injection machine
- Desktop Plastic Injection Molding Machine
- direct clamp injection molding machine
- Direct clamp injection molding machines
- Dosing & mixing system
- Drilling Centers
- Drying and dehumidification system
- drying and dehumidifying equipment
- Drying and Dehumidifying System
- drying system
- effective and efficient. Cabinet dryers are also used in other industries where large quantities of material need to be dried
- efficient injection molding machine
- elbow hydraulic injection molding machines
- electric injection molding machine
- electric injection molding machines
- energy-efficient injection molding robot
- energy-saving injection molding machine
- etc. Among injection molding robots
- exhibition
- features of CNC machine
- Feeding And Conveying System
- Five Axis Machine Center
- Fully automatic injection molding machine
- Gathering Topstar
- giant injection molding machine
- GMU-600 5-Axis Machining Center
- Granulating & Recycling System
- Heavy duty injection molding machine
- High-precision electric molding machines
- high-precision plastic molding machines
- high-speed all electric injection molding machine
- Honeycomb rotor dehumidifier
- horizontal injection molding machine
- Horizontal Injection Molding Machines
- Horizontal Injection Moulding Machine
- Horizontal Mixer manufacturer
- How The CNC Machine Works
- hybrid injection molding machine
- hydraulic injection molding machine
- Hydraulic Injection Molding Machines
- in this article
- Industrial robot
- Industrial Robot Chinese brand
- industrial robot parts
- industrial robot supplier
- Industrial robots
- Industry Chain
- Injection Manipulator
- injection manipulator robot
- injection mold machines
- Injection molding
- Injection molding automation
- Injection Molding Automation Solution
- injection molding dryer
- Injection molding equipment
- injection molding hopper dryer
- Injection molding machine
- injection molding machine brand
- Injection Molding Machine Factory
- Injection Molding Machine Manufacture
- Injection molding machine manufacturer
- injection molding machine manufacturers
- Injection molding machine procurement
- injection molding machine robotic arm
- injection molding machine with a robot
- Injection molding machines
- injection molding material dehumidifying
- injection molding plant
- Injection Molding Robot
- injection molding robot arm
- Injection molding robot automation
- Injection molding robotic arm
- injection molding robots
- Injection moulding machine
- Injection Moulding Robots
- Injection Robot
- Injection robot arm
- Injection robot manufacturer
- Injection robot wholesale
- injection robots
- intelligent injection molding machines
- Introducing Injection Robot
- It is the best choice for drying large quantities of material at once. Cabinetmakers use these machines because they are fast
- large injection molding machine
- Learn what industrial automation and robotics is
- linear robot
- linear robots
- low speed sound-proof granulator
- machine plastic molding
- make sure to add some! Improvements (2) Keyphrase in introduction: Your keyphrase or its synonyms appear in the first paragraph of the copy
- manipulator machine
- manufacturing
- medical grade injection molding machines
- medical injection molding machine
- medical injection molding machines
- micro injection molding machine
- middle speed granulator
- Mini CNC machine manufacturers.
- Mold Temperature Control System
- mold temperature controller
- mold temperature controllers
- molding material Dehumidifying System
- mould temperature control system
- mould temperature controller
- mould temperature controllers
- New electric injection molding machine
- nitrogen dryer manufacturer
- nitrogen dryer system manufacturer
- Oil type mold temperature controller
- Oil type mold temperature controllers
- open day
- Outbound links: No outbound links appear in this page. Add some! Images: No images appear on this page. Add some! Internal links: No internal links appear in this page
- PET Preform injection molding
- phone case maker machine
- phone case making machine
- plastic bottle making machine
- plastic bottle manufacturing
- plastic bucket making machine
- plastic bucket manufacturing
- Plastic chair making machine
- plastic forming equipment
- plastic hopper dryer
- plastic injection machine
- plastic injection machines
- plastic injection molding
- Plastic injection molding equipment
- Plastic injection molding machine
- Plastic Injection Molding Machines
- plastic injection moulding machine
- plastic injection robot
- Plastic Molding machine
- Plastic Molding Machines
- plastic molding press
- plastic moulding machine
- plastic phone case making machine
- plastic-molding machine
- powerful granulator
- Powerful Type Sound-Proof Granulator
- precision injection molding
- precision injection molding machines
- production of plastic seats
- pure water mould temperature controller
- Robot injection molding
- robot injection molding machine
- robot manufacturing companies
- Robotic arm for injection molding machine
- robotic injection molding machines
- robotics in injection molding
- SCARA robot
- SCARA robots
- Service-oriented manufacturing
- Servo Cylinder Robot
- servo driven robot
- Servo Driven Robots
- servo injection robots
- servo motor-driven linear robots
- servo-driven 3-axis robot
- Servo-Driven Robot
- Setup of injection machine
- Silicone Injection Molding Machine
- six-axis industrial robot
- Stainless Hopper Dryer
- Stainless Hopper Dryers
- star club
- swing arm robot
- take-out robots
- the choice between servo-driven robots and hydraulic robots will have a certain impact on efficiency
- the most popular injection molding machine
- the type of injection molding robot
- toggle clamp injection molding machine
- Toggle Hydraulic Injection Molding Machines
- toggle injection molding machine
- Top 10 brands of injection robots
- Topstar
- Topstar Engineering
- Topstar Industrial Robots
- Topstar injection molding intelligent
- Topstar Scara Robots
- Useful Injection molding machine
- Vertical machining centers
- volumetric type blender
- water chiller
- water chillers
- water distributor
- water type mold temperature controller
- Water Type MoldTemperature Controller
- Water-Type Mould Temperature Controllers
- We often face choices when performing injection molding. We will choose the type of injection molding machine
- wholesale of injection molding machines
- x carve CNC