Are there any mould temperature controllers specifically for the automotive industry?
2025/01/27 By Topstar
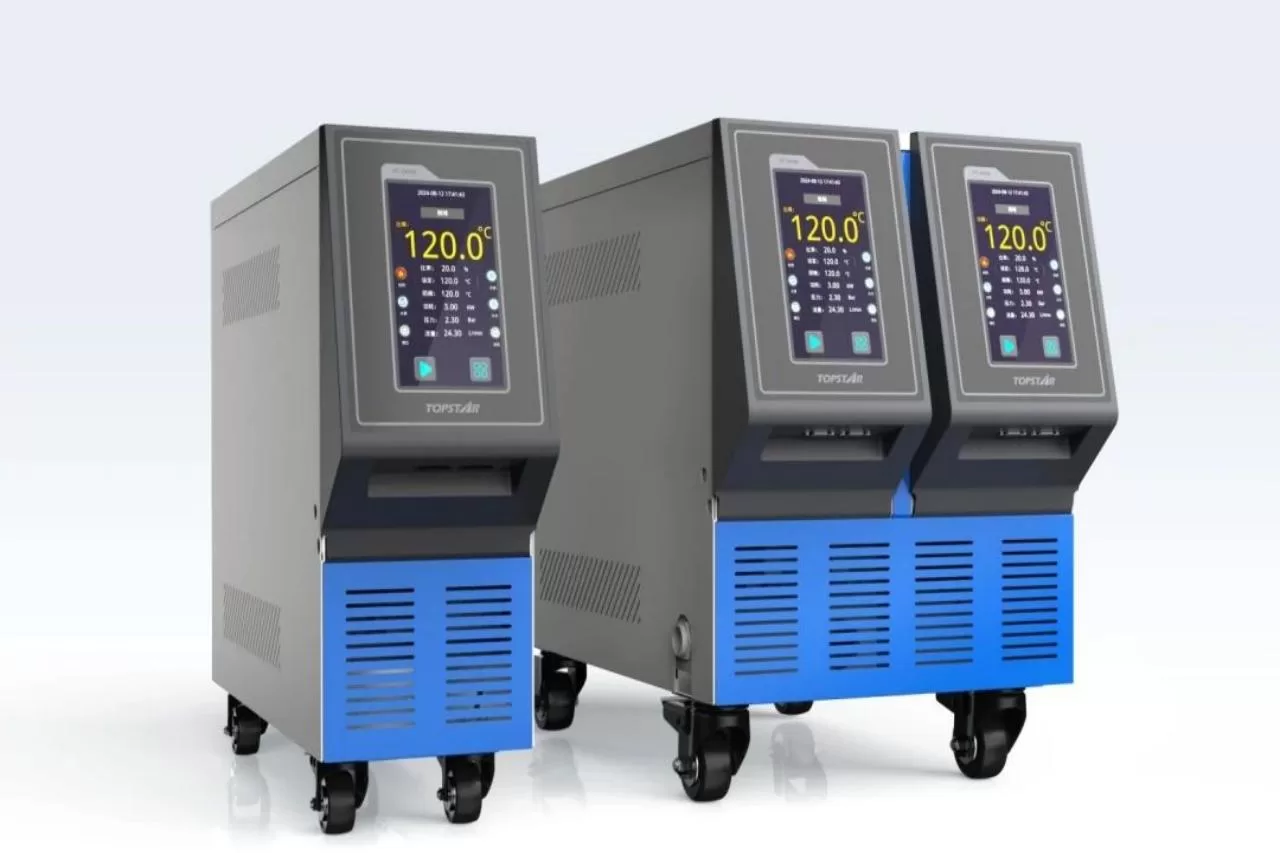
Every component in the automotive industry, whether it is an interior part or a thick-walled product, requires strict moulding standards, especially in terms of temperature control. But is there a mould temperature controller designed specifically for the automotive industry? The answer is yes. This year, Topstar also launched two sets of injection moulding solutions that can meet the injection moulding requirements of headlight plastic products. Then, we will share with you how the mould temperature controllers in the two solutions optimize and assist the production of thick-walled products in the automotive industry.
The automotive industry has problems with temperature control.
The automotive industry faces unique challenges in temperature control during manufacturing. Automotive parts are usually large in size and thick in the wall and need to be cooled or heated quickly during production. Traditional mould temperature controllers have difficulty meeting these challenges, especially when manufacturers deal with materials such as high-strength polymers, composites, and rubbers commonly used in automotive parts.
In addition, thick-walled automotive products must adhere to strict tolerances to ensure proper fit, function, and safety. Temperature changes during injection moulding can cause these parts to shrink, warp, or have other problems that affect the final product. The industry also faces the need for large-scale, high-speed production and minimal downtime, which increases the need for efficient temperature regulation. For these reasons, Topstar’s mould temperature controllers, designed specifically for the automotive industry, are able to handle high flow rates, provide faster temperature changes, and provide precise control over a wide temperature range.
The role of 120°C high-flow mould temperature controllers in automotive manufacturing
Designed for industries such as automotive manufacturing, the 120°C high-flow mould temperature controller is able to handle high flow rates and high-pressure heads, making it ideal for thick-walled products common in the automotive industry. This mould temperature controller can circulate coolant at a higher flow rate, allowing it to more effectively regulate the temperature of thicker moulds, which require more heat energy to maintain a constant temperature. This is particularly important for automotive parts, which produce thick-walled parts such as PMMA thick-walled headlights. Manufacturers need to cool these parts evenly to prevent warping or dimensional inaccuracies. At the same time, the use of a 20mm diameter cooling solenoid valve helps to speed up cooling.
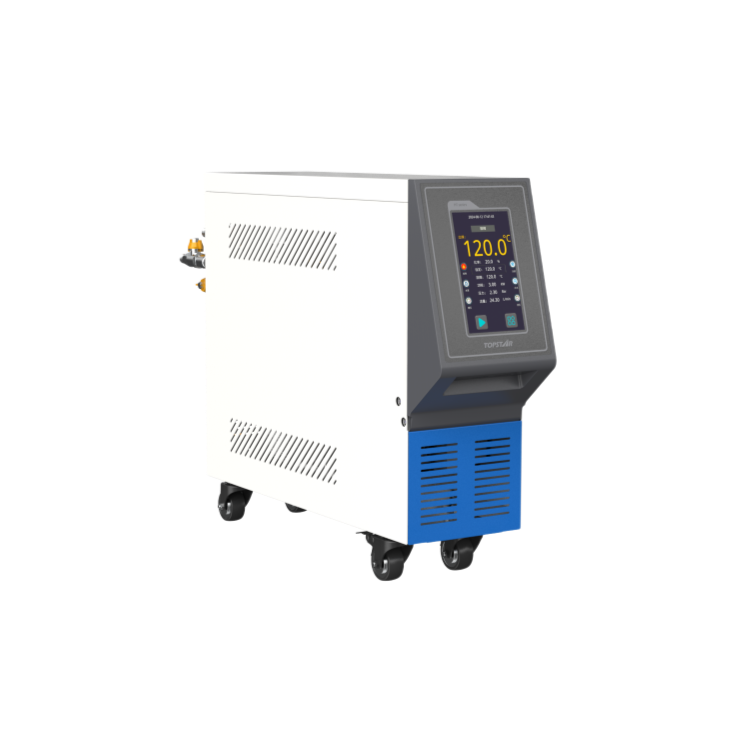
The advantage of mould temperature controllers with large flow rates
One of the main challenges in producing thick-walled products in the automotive industry is ensuring that the mould cools effectively, especially when dealing with thicker parts. The 120°C high-flow mould temperature controller excels in this regard because it has a high flow rate and high head. These features allow the system to provide consistent temperature regulation even in thicker, larger moulds.
High Flow Rates and High Heads pump large volumes of coolant, which helps distribute heat evenly throughout the mould.
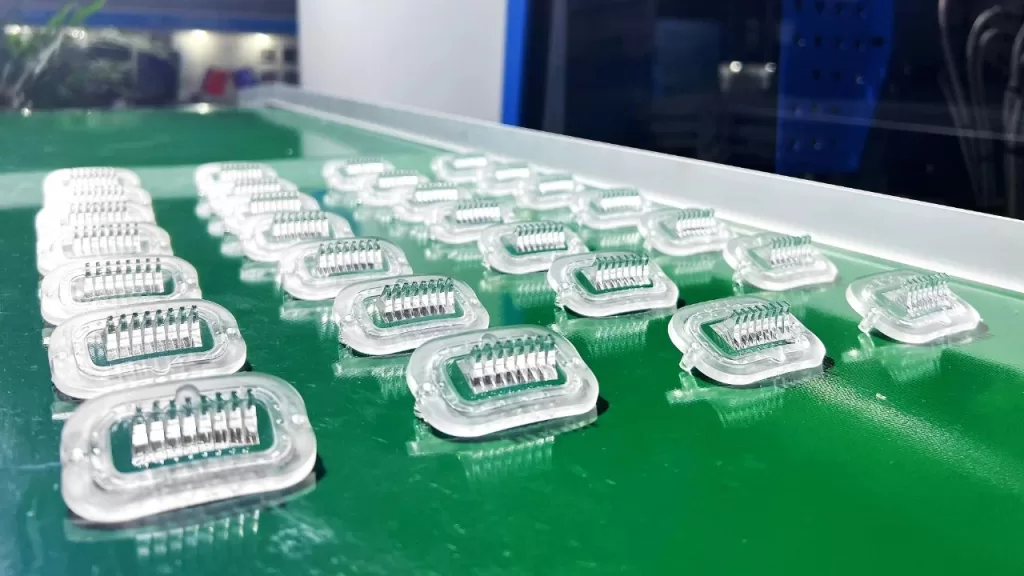
Impact of Faster Cooling Rates on Production Efficiency
One of the standout features of the 120°C High Flow Temperature Controller is its ability to provide faster cooling rates, which is critical in the high-speed manufacturing environment of the automotive industry. Faster cooling helps reduce cycle times, which directly affects overall production efficiency. In the automotive manufacturing field, where production volumes often reach thousands of parts per day, reducing mould cooling time can significantly increase production. This is especially beneficial when manufacturers are using materials with high thermal conductivity, which may take longer to cool and solidify. Faster cooling with high-flow mould temperature controllers not only reduces cycle time but also improves part quality by preventing defects such as dents, warping or internal stress.
Lower temperature control for thick-walled products
In the automotive industry, it is often necessary to control the temperature of thick-walled products at lower temperatures to ensure that the material crystallizes or solidifies correctly. The 120°C high-flow mould temperature controller excels in this regard, with a 10% increase in temperature control efficiency through the latest PID temperature control algorithm, allowing a temperature control accuracy of ±0.1°C, allowing lower temperature control settings, which is critical for certain automotive applications. Automotive parts that require high strength and durability, such as PMMA thick-walled headlights, often have thick walls, so precise temperature management is required during the moulding process. Lowering the mould temperature allows manufacturers to achieve the best cooling curve for thick materials, ensuring that the parts are cooled evenly without compromising their mechanical properties.
Better temperature control for thick-walled products in the automotive industry
In the automotive industry, it is essential to ensure the highest precision, efficiency and safety in production. Using a dedicated mould temperature controller, such as the 120°C high-flow model, is essential to achieving these goals. 120°C High Flow Temperature Controller features high flow, faster cooling, and the ability to handle thick-walled moulds, which can reduce cycle time, improve part quality, and increase overall production efficiency.
TRENDING POSTS
- What factors can cause delays in the injection molding process of plastic molding machine? 2025/01/27
- Exhibition Review| Topstar participates in InterPlas Thailand 2024 2025/01/27
- Star Case | Topstar helps Santong upgrade its intelligent plant 2025/01/27
- Topstar Special | National Science and Technology Workers Day 2025/01/27
HOT TOPIC
- .ervo motor-driven linear robots
- 3 axis robot
- 3 axis robots
- 3 in 1 Compact Dehumidifying Dryer
- 3-axis robot
- 3-axis robots
- 5-axis CNC machine
- accuracy
- Air Chillers
- all electric injection molding machine
- all electric injection molding machines
- All-electric injection molding machines
- and overall production quality. Therefore
- AP-RubberPlas
- automated injection molding machine
- Automation changed engineering
- automation of injection molding robots
- auxiliary machine
- Bench Injection Molding Machine
- Cabinet dryer manufacturers
- Cabinet dryers
- chiller
- CNC Drilling Machine
- CNC Drilling Machines
- cnc engraving machine manufacturer
- cnc laser cutting machine manufacturer
- CNC machine
- CNC Machine Center
- CNC Machine for Sale
- CNC Machine Manufacturing
- CNC Machine Tool
- CNC machine tool product
- CNC Machining Center
- CNC wood carving machine
- Cooling system
- Cross-Walking Single Axis Servo Cylinder Robot
- Cross-Walking Single-Axis Servo Cylinder Robot
- Cross-Walking Three-Axis/Five-Axis Servo Driven Robot
- cross-walking three-axis/five-axis servo-driven robot
- Dehumidifier Dryer
- Dehumidifying Dryer
- delta parallel robot
- Desktop Injection Molding Machine
- Desktop injection molding machines
- Desktop Molding Machine
- desktop plastic injection machine
- Desktop Plastic Injection Molding Machine
- direct clamp injection molding machine
- Direct clamp injection molding machines
- Dosing & mixing system
- Drilling Centers
- Drying and dehumidification system
- drying and dehumidifying equipment
- Drying and Dehumidifying System
- drying system
- effective and efficient. Cabinet dryers are also used in other industries where large quantities of material need to be dried
- efficient injection molding machine
- elbow hydraulic injection molding machines
- electric injection molding machine
- electric injection molding machines
- energy-efficient injection molding robot
- energy-saving injection molding machine
- etc. Among injection molding robots
- exhibition
- features of CNC machine
- Feeding And Conveying System
- Five Axis Machine Center
- Fully automatic injection molding machine
- Gathering Topstar
- giant injection molding machine
- GMU-600 5-Axis Machining Center
- Granulating & Recycling System
- Heavy duty injection molding machine
- High-precision electric molding machines
- high-precision plastic molding machines
- high-speed all electric injection molding machine
- Honeycomb rotor dehumidifier
- horizontal injection molding machine
- Horizontal Injection Molding Machines
- Horizontal Injection Moulding Machine
- Horizontal Mixer manufacturer
- How The CNC Machine Works
- hybrid injection molding machine
- hydraulic injection molding machine
- Hydraulic Injection Molding Machines
- in this article
- Industrial robot
- Industrial Robot Chinese brand
- industrial robot parts
- industrial robot supplier
- Industrial robots
- Industry Chain
- Injection Manipulator
- injection manipulator robot
- injection mold machines
- Injection molding
- Injection molding automation
- Injection Molding Automation Solution
- injection molding dryer
- Injection molding equipment
- injection molding hopper dryer
- Injection molding machine
- injection molding machine brand
- Injection Molding Machine Factory
- Injection Molding Machine Manufacture
- Injection molding machine manufacturer
- injection molding machine manufacturers
- Injection molding machine procurement
- injection molding machine robotic arm
- injection molding machine with a robot
- Injection molding machines
- injection molding material dehumidifying
- injection molding plant
- Injection Molding Robot
- injection molding robot arm
- Injection molding robot automation
- Injection molding robotic arm
- injection molding robots
- Injection moulding machine
- Injection Moulding Robots
- Injection Robot
- Injection robot arm
- Injection robot manufacturer
- Injection robot wholesale
- injection robots
- intelligent injection molding machines
- Introducing Injection Robot
- It is the best choice for drying large quantities of material at once. Cabinetmakers use these machines because they are fast
- large injection molding machine
- large injection molding machines
- Learn what industrial automation and robotics is
- linear robot
- linear robots
- low speed sound-proof granulator
- machine plastic molding
- make sure to add some! Improvements (2) Keyphrase in introduction: Your keyphrase or its synonyms appear in the first paragraph of the copy
- manipulator machine
- manufacturing
- medical grade injection molding machines
- medical injection molding machine
- medical injection molding machines
- micro injection molding machine
- middle speed granulator
- Mini CNC machine manufacturers.
- Mold Temperature Control System
- mold temperature controller
- mold temperature controllers
- molding material Dehumidifying System
- mould temperature control system
- mould temperature controller
- mould temperature controllers
- New electric injection molding machine
- nitrogen dryer manufacturer
- nitrogen dryer system manufacturer
- Oil type mold temperature controller
- Oil type mold temperature controllers
- open day
- Outbound links: No outbound links appear in this page. Add some! Images: No images appear on this page. Add some! Internal links: No internal links appear in this page
- PET Preform injection molding
- phone case maker machine
- phone case making machine
- plastic bottle making machine
- plastic bottle manufacturing
- plastic bucket making machine
- plastic bucket manufacturing
- Plastic chair making machine
- plastic forming equipment
- plastic hopper dryer
- plastic injection machine
- plastic injection machines
- plastic injection molding
- Plastic injection molding equipment
- Plastic injection molding machine
- Plastic Injection Molding Machines
- plastic injection moulding machine
- plastic injection robot
- Plastic Molding machine
- Plastic Molding Machines
- plastic molding press
- plastic moulding machine
- plastic phone case making machine
- plastic-molding machine
- powerful granulator
- Powerful Type Sound-Proof Granulator
- precision injection molding
- precision injection molding machines
- production of plastic seats
- pure water mould temperature controller
- Robot injection molding
- robot injection molding machine
- robot manufacturing companies
- Robotic arm for injection molding machine
- robotic injection molding machines
- robotics in injection molding
- SCARA robot
- SCARA robots
- Service-oriented manufacturing
- Servo Cylinder Robot
- servo driven robot
- Servo Driven Robots
- servo injection robots
- servo motor-driven linear robots
- servo-driven 3-axis robot
- Servo-Driven Robot
- Setup of injection machine
- Silicone Injection Molding Machine
- six-axis industrial robot
- Stainless Hopper Dryer
- Stainless Hopper Dryers
- star club
- swing arm robot
- take-out robots
- the choice between servo-driven robots and hydraulic robots will have a certain impact on efficiency
- the most popular injection molding machine
- the type of injection molding robot
- toggle clamp injection molding machine
- Toggle Hydraulic Injection Molding Machines
- toggle injection molding machine
- Top 10 brands of injection robots
- Topstar
- Topstar Engineering
- Topstar Industrial Robots
- Topstar injection molding intelligent
- Topstar Scara Robots
- Useful Injection molding machine
- Vertical machining centers
- volumetric type blender
- water chiller
- water chillers
- water distributor
- water type mold temperature controller
- Water Type MoldTemperature Controller
- Water-Type Mould Temperature Controllers
- We often face choices when performing injection molding. We will choose the type of injection molding machine
- wholesale of injection molding machines
- x carve CNC