Injection molding machine for medical device production: key factors
2025/01/29 By Topstar
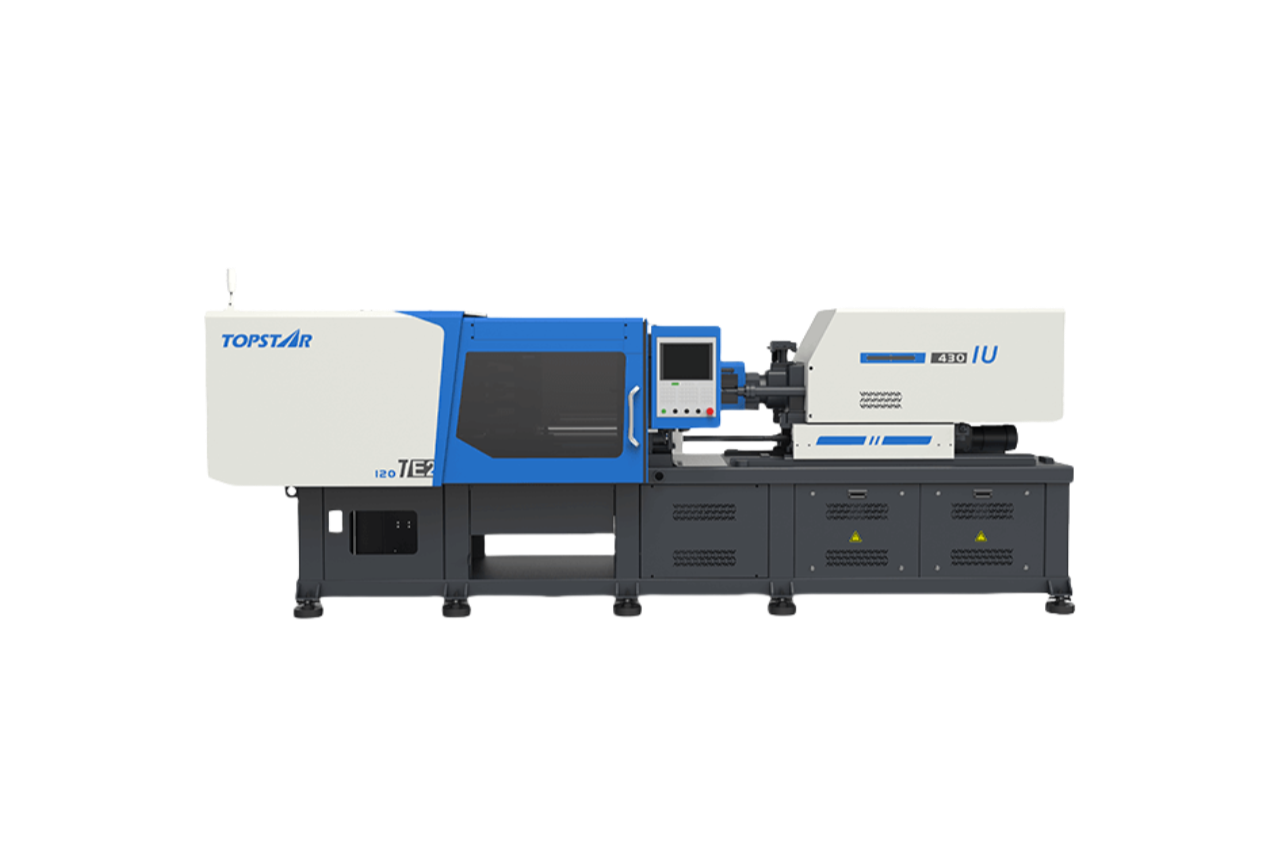
Since medical products are sterile and clean, the production environment must be a dust-free workshop. To adapt to the requirements of dust-free workshops, various medical products must use injection molding machines that can reduce the generation of pollutants and complete the injection molding of products. After fully understanding the precision injection molding requirements and dust-free workshop standards of medical products, Topstar launched the TEⅡ injection molding machine. In this article, we will introduce the highlights and key factors.
Intelligent drive control mode of injection molding machine
Precision is one of the most critical factors in the production of medical devices. Even slight deviations in size, shape, or material composition can cause product failures, endangering patient safety. The intelligent drive control mode is adopted on the TEⅡ electric injection molding machine, which reduces the impact of communication delay on the high-speed operation of the servo motor, realizes real-time control of the servo motor, improves the accuracy of position, speed, and pressure control, and increases the response speed by 8-16 times. In this control mode, the parameters can be saved in the internal latch so that the servo drive can directly produce the motor speed curve to execute the corresponding process during each cycle reciprocating operation, making the control process more efficient.
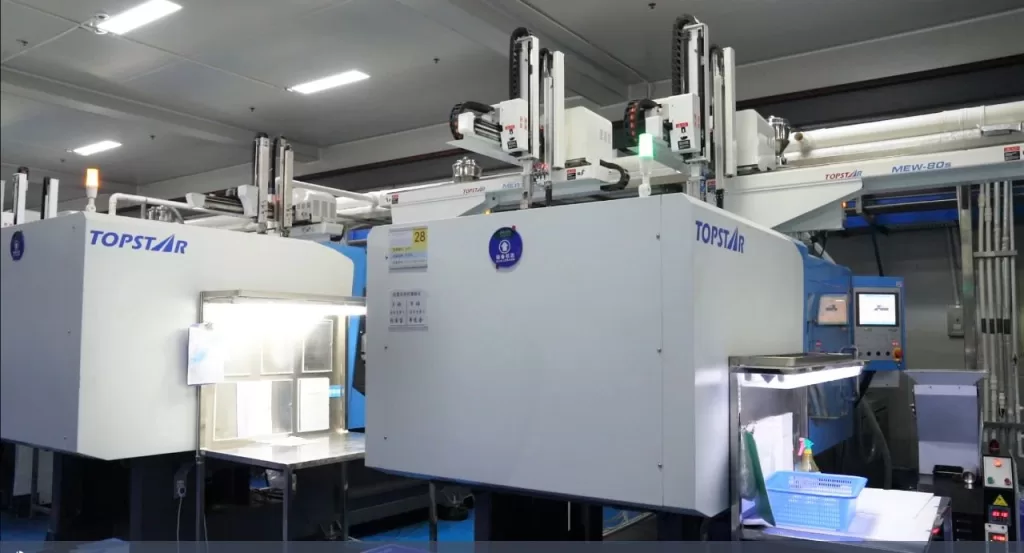
Reduce costs and improve efficiency.
Reducing costs and improving efficiency has become the most crucial point for global companies to operate and produce, and using low-energy production equipment is the tool to implement this means. TEⅡ electric injection molding machines not only consider the complex indicators of dust-free workshops and the needs of product precision injection molding but also significantly affect energy saving and cost reduction. Big data shows that electric injection molding machines can save at least 50% of electricity compared to hydraulic injection molding machines and up to 60%. This can enable manufacturers to reduce operating costs significantly. The intelligent drive control mode can improve cost-effectiveness by automatically adjusting key parameters, ensuring that production is fast and energy-saving. At the same time, the production efficiency of TEⅡ electric injection molding machines has increased by about 10% compared to the past.
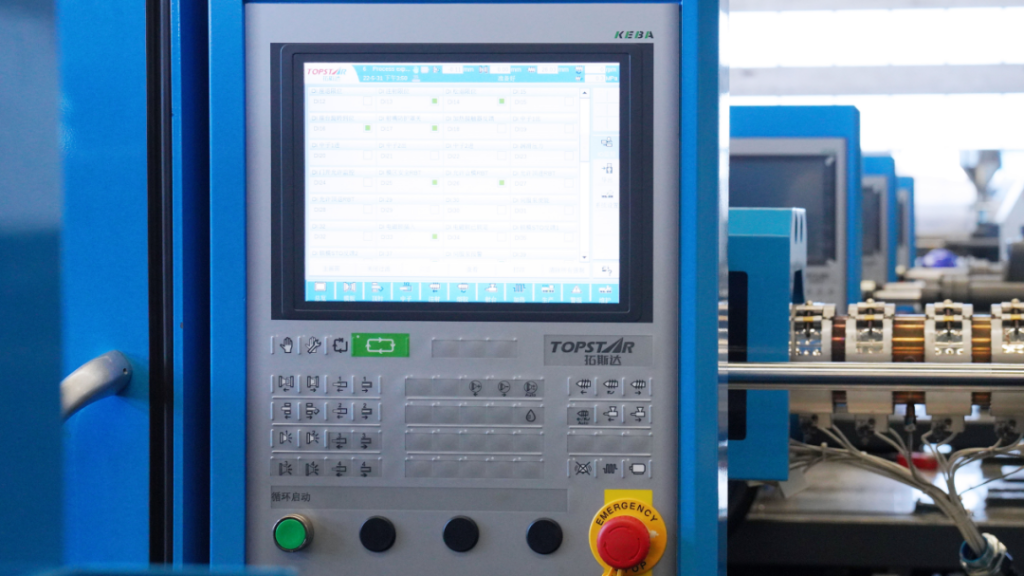
Space-saving injection molding machine design
The design of the injection molding machine plays a vital role in its efficiency, especially in the clean room environment familiar in medical device manufacturing. These environments require equipment that can operate efficiently while minimizing the risk of contamination. TEⅡ electric injection molding machines are also designed with compactness in mind, providing excellent performance while taking up less space.
They can seamlessly integrate into clean room environments with limited space. This is particularly beneficial for medical device manufacturers, who must optimize their production lines to maximize production while maintaining a clean and sterile environment. In addition, this space-saving design makes it easier to integrate with other injection molding auxiliary equipment.
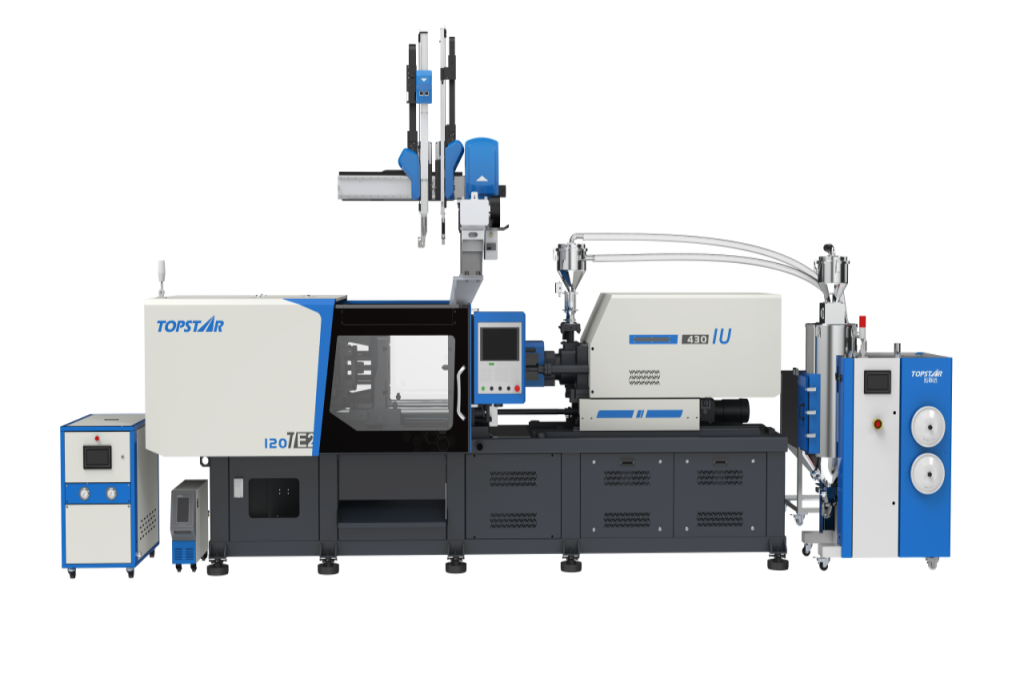
Ensure the cleanliness of the mold area.
The second plate and guide pins of the TEⅡ injection molding machine adopt a non-contact design, without the need for separate lubrication, to ensure the cleanliness of the mold area to the greatest extent. In hydraulic injection molding machines, lubricants will contaminate the mold area and increase the possibility of surface defects and contamination of the final molded parts. By eliminating the need for separate lubrication, the TEⅡ injection molding machine ensures that the mold area remains clean throughout the production cycle, which is particularly important in the medical industry. Engineers specially design the second plate and guide pins to minimize physical contact between these key components and reduce friction. In addition, the non-contact design of the second plate and guide pins ensures more accurate alignment of the mold and machine components, resulting in higher cycle efficiency.
Versatility for different medical applications
Topstar designs its injection molding machines with versatility in mind, allowing users to select different screw designs based on the materials used. They can process various materials, including medical-grade plastics, elastomers, and composites, to meet the various needs of the medical industry. Whether producing respiratory products, IV connectors, or other plastic medical products, these machines can produce parts with the necessary precision and quality. In addition, they have the flexibility to handle small and large batches, making them ideal for prototype development and mass production.
More suitable for injection molding of medical products
Choosing the right injection molding machine is crucial for medical device manufacturers. The selected injection molding equipment must meet the specific needs of medical device production. Topstar can provide more professional and efficient solutions and technical support based on the exact standards required for the processing of plastic products in the medical industry.
TRENDING POSTS
- What factors can cause delays in the injection molding process of plastic molding machine? 2025/01/29
- Exhibition Review| Topstar participates in InterPlas Thailand 2024 2025/01/29
- Star Case | Topstar helps Santong upgrade its intelligent plant 2025/01/29
- Topstar Special | National Science and Technology Workers Day 2025/01/29
HOT TOPIC
- .ervo motor-driven linear robots
- 3 axis robot
- 3 axis robots
- 3 in 1 Compact Dehumidifying Dryer
- 3-axis robot
- 3-axis robots
- 5-axis CNC machine
- accuracy
- Air Chillers
- all electric injection molding machine
- all electric injection molding machines
- All-electric injection molding machines
- and overall production quality. Therefore
- AP-RubberPlas
- automated injection molding machine
- Automation changed engineering
- automation of injection molding robots
- auxiliary machine
- Bench Injection Molding Machine
- Cabinet dryer manufacturers
- Cabinet dryers
- chiller
- CNC Drilling Machine
- CNC Drilling Machines
- cnc engraving machine manufacturer
- cnc laser cutting machine manufacturer
- CNC machine
- CNC Machine Center
- CNC Machine for Sale
- CNC Machine Manufacturing
- CNC Machine Tool
- CNC machine tool product
- CNC Machining Center
- CNC wood carving machine
- Cooling system
- Cross-Walking Single Axis Servo Cylinder Robot
- Cross-Walking Single-Axis Servo Cylinder Robot
- Cross-Walking Three-Axis/Five-Axis Servo Driven Robot
- cross-walking three-axis/five-axis servo-driven robot
- Dehumidifier Dryer
- Dehumidifying Dryer
- delta parallel robot
- Desktop Injection Molding Machine
- Desktop injection molding machines
- Desktop Molding Machine
- desktop plastic injection machine
- Desktop Plastic Injection Molding Machine
- direct clamp injection molding machine
- Direct clamp injection molding machines
- Dosing & mixing system
- Drilling Centers
- Drying and dehumidification system
- drying and dehumidifying equipment
- Drying and Dehumidifying System
- drying system
- effective and efficient. Cabinet dryers are also used in other industries where large quantities of material need to be dried
- efficient injection molding machine
- elbow hydraulic injection molding machines
- electric injection molding machine
- electric injection molding machines
- energy-efficient injection molding robot
- energy-saving injection molding machine
- etc. Among injection molding robots
- exhibition
- features of CNC machine
- Feeding And Conveying System
- Five Axis Machine Center
- Fully automatic injection molding machine
- Gathering Topstar
- giant injection molding machine
- GMU-600 5-Axis Machining Center
- Granulating & Recycling System
- Heavy duty injection molding machine
- High-precision electric molding machines
- high-precision plastic molding machines
- high-speed all electric injection molding machine
- Honeycomb rotor dehumidifier
- horizontal injection molding machine
- Horizontal Injection Molding Machines
- Horizontal Injection Moulding Machine
- Horizontal Mixer manufacturer
- How The CNC Machine Works
- hybrid injection molding machine
- hydraulic injection molding machine
- Hydraulic Injection Molding Machines
- in this article
- Industrial robot
- Industrial Robot Chinese brand
- industrial robot parts
- industrial robot supplier
- Industrial robots
- Industry Chain
- Injection Manipulator
- injection manipulator robot
- injection mold machines
- Injection molding
- Injection molding automation
- Injection Molding Automation Solution
- injection molding dryer
- Injection molding equipment
- injection molding hopper dryer
- Injection molding machine
- injection molding machine brand
- Injection Molding Machine Factory
- Injection Molding Machine Manufacture
- Injection molding machine manufacturer
- injection molding machine manufacturers
- Injection molding machine procurement
- injection molding machine robotic arm
- injection molding machine with a robot
- Injection molding machines
- injection molding material dehumidifying
- injection molding plant
- Injection Molding Robot
- injection molding robot arm
- Injection molding robot automation
- Injection molding robotic arm
- injection molding robots
- Injection moulding machine
- Injection Moulding Robots
- Injection Robot
- Injection robot arm
- Injection robot manufacturer
- Injection robot wholesale
- injection robots
- intelligent injection molding machines
- Introducing Injection Robot
- It is the best choice for drying large quantities of material at once. Cabinetmakers use these machines because they are fast
- large injection molding machine
- large injection molding machines
- Learn what industrial automation and robotics is
- linear robot
- linear robots
- low speed sound-proof granulator
- machine plastic molding
- make sure to add some! Improvements (2) Keyphrase in introduction: Your keyphrase or its synonyms appear in the first paragraph of the copy
- manipulator machine
- manufacturing
- medical grade injection molding machines
- medical injection molding machine
- medical injection molding machines
- micro injection molding machine
- middle speed granulator
- Mini CNC machine manufacturers.
- Mold Temperature Control System
- mold temperature controller
- mold temperature controllers
- molding material Dehumidifying System
- mould temperature control system
- mould temperature controller
- mould temperature controllers
- New electric injection molding machine
- nitrogen dryer manufacturer
- nitrogen dryer system manufacturer
- Oil type mold temperature controller
- Oil type mold temperature controllers
- open day
- Outbound links: No outbound links appear in this page. Add some! Images: No images appear on this page. Add some! Internal links: No internal links appear in this page
- PET Preform injection molding
- phone case maker machine
- phone case making machine
- plastic bottle making machine
- plastic bottle manufacturing
- plastic bucket making machine
- plastic bucket manufacturing
- Plastic chair making machine
- plastic forming equipment
- plastic hopper dryer
- plastic injection machine
- plastic injection machines
- plastic injection molding
- Plastic injection molding equipment
- Plastic injection molding machine
- Plastic Injection Molding Machines
- plastic injection moulding machine
- plastic injection robot
- Plastic Molding machine
- Plastic Molding Machines
- plastic molding press
- plastic moulding machine
- plastic phone case making machine
- plastic-molding machine
- powerful granulator
- Powerful Type Sound-Proof Granulator
- precision injection molding
- precision injection molding machines
- production of plastic seats
- pure water mould temperature controller
- Robot injection molding
- robot injection molding machine
- robot manufacturing companies
- Robotic arm for injection molding machine
- robotic injection molding machines
- robotics in injection molding
- SCARA robot
- SCARA robots
- Service-oriented manufacturing
- Servo Cylinder Robot
- servo driven robot
- Servo Driven Robots
- servo injection robots
- servo motor-driven linear robots
- servo-driven 3-axis robot
- Servo-Driven Robot
- Setup of injection machine
- Silicone Injection Molding Machine
- six-axis industrial robot
- Stainless Hopper Dryer
- Stainless Hopper Dryers
- star club
- swing arm robot
- take-out robots
- the choice between servo-driven robots and hydraulic robots will have a certain impact on efficiency
- the most popular injection molding machine
- the type of injection molding robot
- toggle clamp injection molding machine
- Toggle Hydraulic Injection Molding Machines
- toggle injection molding machine
- Top 10 brands of injection robots
- Topstar
- Topstar Engineering
- Topstar Industrial Robots
- Topstar injection molding intelligent
- Topstar Scara Robots
- Useful Injection molding machine
- Vertical machining centers
- volumetric type blender
- water chiller
- water chillers
- water distributor
- water type mold temperature controller
- Water Type MoldTemperature Controller
- Water-Type Mould Temperature Controllers
- We often face choices when performing injection molding. We will choose the type of injection molding machine
- wholesale of injection molding machines
- x carve CNC