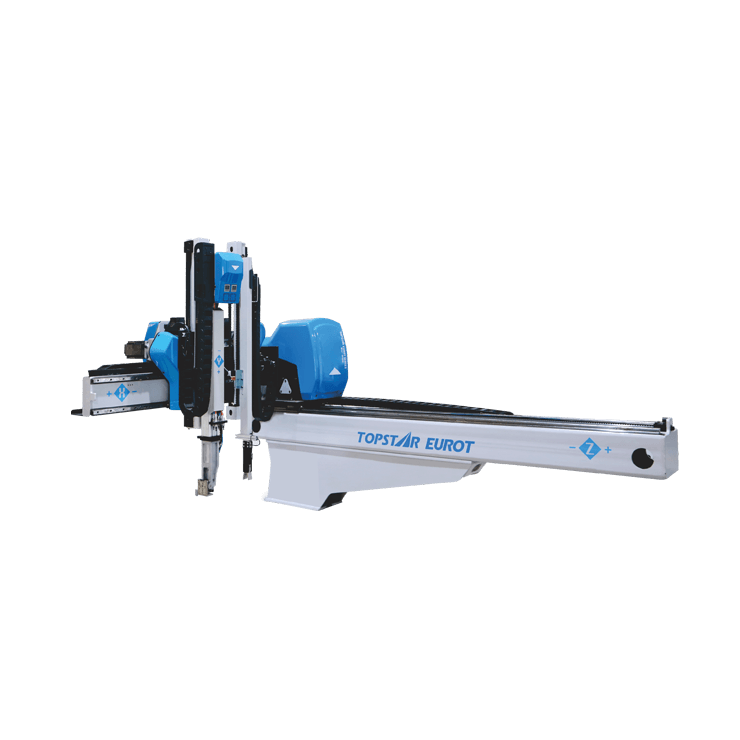
The injection robot in the injection molding machine is used to put product parts into the injection molding machine in the early stage of product molding. After molding, through the multi-angle expansion and contraction of the robotic arm, different products are taken out and placed on the automated conveyor belt to achieve high positioning accuracy. Fully automated injection molding process with faster speed and safer performance.
What is the injection molding process of the injection robot?
Manufacturers use injection robots in the production phase of the injection molding process to increase overall productivity by automating repetitive tasks. Injection molding robots can handle raw materials such as plastic pellets or pellets by loading them into the hopper of an injection molding machine. They can assist in setting up injection molds by accurately positioning them in the molding machine and holding them in place. After the injection molding, the injection robot can remove the newly formed parts from the mold cavity and place them on a conveyor belt or designated location for further processing or packaging.
Topstar’s injection molding robot series
Topstar’s main injection robot series is EURO Cross-walking three-axis/five-axis servo robots. Unlike traditional robots, they use our “5-in-1 servo-driven robot” technology to achieve customer goals. There are demands for precision, energy saving, and intelligence. By upgrading core component technologies such as self-developed control systems and servo drives, we have achieved precise energy saving in hardware, integrated software communication, and a more comprehensive range of application scenarios.
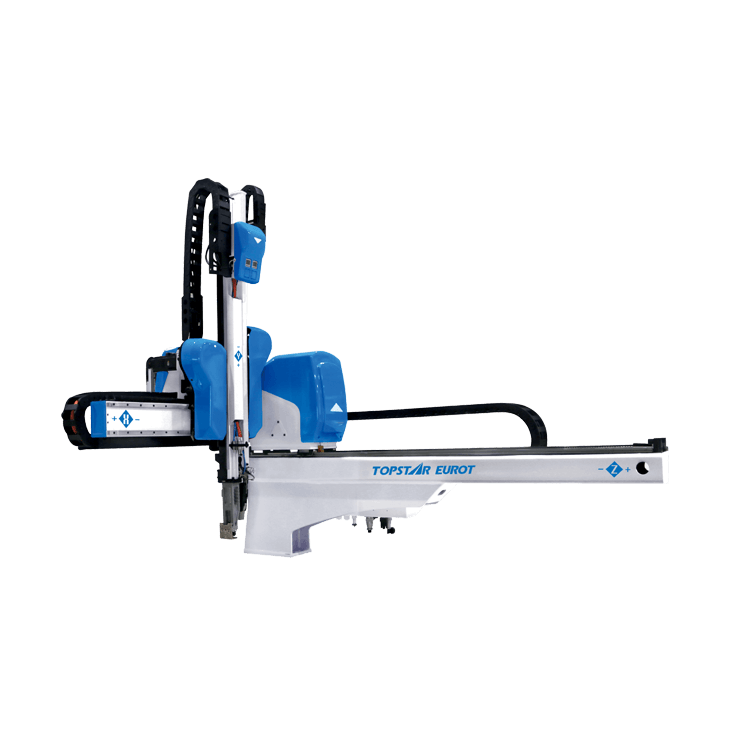
Their main features
- Ejector linkage, defective product discharge, conveyor belt start signal output, internal memory function (100 groups)
- Adopt high-rigidity precision slide rails, high-strength steel belt drive, high speed, low noise, and long life.
3.32-bit CPU, complete functions, switchable multi-language operation interface, separate host design, easy to control
- Posture part combination design, 90-degree rotation to match different product removal; double-arm structure suitable for simultaneous use or separate use
- Each axis is driven by a brand-name AC servo motor and precision-grade reducer for variable speed, fast speed, and accurate positioning, and the accuracy can reach ±0.1mm.
injection robot realizes equipment management interconnection
When traditional device management realizes cross-system interconnection through network protocols, there will be factors such as signal delay, poor compatibility, and low stability. Through the open architecture of the underlying control system, Topstar enables injection molding peripheral auxiliary machines and injection molding machines to have a native language for system integration, making equipment interconnection an extension of the system. Topstar’s injection manipulator can support the host’s call signal to achieve integrated operation, and the control system automatically optimizes the removal process, thereby improving the injection molding efficiency of the production line. It solves problems such as failure to take out and equipment alarm shutdown due to ejection position deviation and uncoordinated suction time.
Benefits of using injection robots
Unlike in the past, injection robots on injection molding machines can perform repetitive automated plastic part-picking tasks with high speed and precision, thereby reducing downtime and optimizing production throughput. Unlike manual labor, they do not suffer from fatigue or performance changes, resulting in more predictable and reliable results. Consistent part quality is critical to meeting customer specifications and minimizing defects during production. They also offer more flexibility than humans and can perform various tasks, from simple pick-and-place operations to complex assembly tasks, by programming them using servo-driven control systems. This flexibility allows them to adapt to different industries’ production requirements quickly.
Implementation considerations
Don’t forget that there are several things to pay attention to when implementing an injection robot in an injection molding machine. First, one must consider factors such as machine size, configuration, and control interface compatibility to ensure integration and compatibility between the injection molding machine and the injection robot. Secondly, we must conduct a thorough risk assessment of the injection molding process. We need to consider safety during the implementation of the injection molding robot and improve safety measures such as machine protection, interlocking, and emergency stop systems. Third, when integrating the injection robot with the injection molding machine control system, one must coordinate the communication between the two systems to ensure compatibility between the robot and machine controller, facilitating data exchange and operation synchronization.
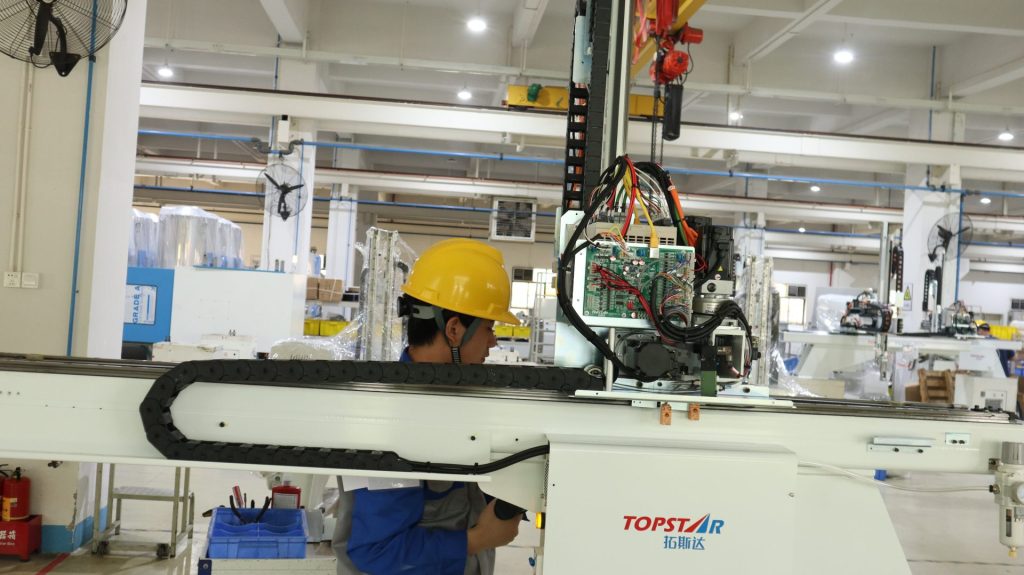
Ultimately
This is an injection robot suitable for most injection molding machines. They play a crucial role in injection molding operations, and their seamless integration with the injection molding machine successfully streamlines the production process and delivers high-quality, cost-effective plastic parts.
TRENDING POSTS
- What factors can cause delays in the injection molding process of plastic molding machine? 2024/02/20
- Exhibition Review| Topstar participates in InterPlas Thailand 2024 2024/02/20
- Star Case | Topstar helps Santong upgrade its intelligent plant 2024/02/20
- Topstar Special | National Science and Technology Workers Day 2024/02/20
HOT TOPIC
- .ervo motor-driven linear robots
- 3 axis robot
- 3 axis robots
- 3 in 1 Compact Dehumidifying Dryer
- 3-axis robot
- 3-axis robots
- 5-axis CNC machine
- accuracy
- Air Chillers
- all electric injection molding machine
- all electric injection molding machines
- All-electric injection molding machines
- and overall production quality. Therefore
- AP-RubberPlas
- automated injection molding machine
- Automation changed engineering
- automation of injection molding robots
- auxiliary machine
- Bench Injection Molding Machine
- Cabinet dryer manufacturers
- Cabinet dryers
- chiller
- CNC Drilling Machine
- CNC Drilling Machines
- cnc engraving machine manufacturer
- cnc laser cutting machine manufacturer
- CNC machine
- CNC Machine Center
- CNC Machine for Sale
- CNC Machine Manufacturing
- CNC Machine Tool
- CNC machine tool product
- CNC Machining Center
- CNC wood carving machine
- Cooling system
- Cross-Walking Single Axis Servo Cylinder Robot
- Cross-Walking Single-Axis Servo Cylinder Robot
- Cross-Walking Three-Axis/Five-Axis Servo Driven Robot
- cross-walking three-axis/five-axis servo-driven robot
- Dehumidifier Dryer
- Dehumidifying Dryer
- delta parallel robot
- Desktop Injection Molding Machine
- Desktop injection molding machines
- Desktop Molding Machine
- desktop plastic injection machine
- Desktop Plastic Injection Molding Machine
- direct clamp injection molding machine
- Direct clamp injection molding machines
- Dosing & mixing system
- Drilling Centers
- Drying and dehumidification system
- drying and dehumidifying equipment
- Drying and Dehumidifying System
- drying system
- effective and efficient. Cabinet dryers are also used in other industries where large quantities of material need to be dried
- efficient injection molding machine
- elbow hydraulic injection molding machines
- electric injection molding machine
- electric injection molding machines
- energy-efficient injection molding robot
- energy-saving injection molding machine
- etc. Among injection molding robots
- exhibition
- features of CNC machine
- Feeding And Conveying System
- Five Axis Machine Center
- Fully automatic injection molding machine
- Gathering Topstar
- giant injection molding machine
- GMU-600 5-Axis Machining Center
- Granulating & Recycling System
- Heavy duty injection molding machine
- High-precision electric molding machines
- high-precision plastic molding machines
- high-speed all electric injection molding machine
- Honeycomb rotor dehumidifier
- horizontal injection molding machine
- Horizontal Injection Molding Machines
- Horizontal Injection Moulding Machine
- Horizontal Mixer manufacturer
- How The CNC Machine Works
- hybrid injection molding machine
- hydraulic injection molding machine
- Hydraulic Injection Molding Machines
- in this article
- Industrial robot
- Industrial Robot Chinese brand
- industrial robot parts
- industrial robot supplier
- Industrial robots
- Industry Chain
- Injection Manipulator
- injection manipulator robot
- injection mold machines
- Injection molding
- Injection molding automation
- Injection Molding Automation Solution
- injection molding dryer
- Injection molding equipment
- injection molding hopper dryer
- Injection molding machine
- injection molding machine brand
- Injection Molding Machine Factory
- Injection Molding Machine Manufacture
- Injection molding machine manufacturer
- injection molding machine manufacturers
- Injection molding machine procurement
- injection molding machine robotic arm
- injection molding machine with a robot
- Injection molding machines
- injection molding material dehumidifying
- injection molding plant
- Injection Molding Robot
- injection molding robot arm
- Injection molding robot automation
- Injection molding robotic arm
- injection molding robots
- Injection moulding machine
- Injection Moulding Robots
- Injection Robot
- Injection robot arm
- Injection robot manufacturer
- Injection robot wholesale
- injection robots
- intelligent injection molding machines
- Introducing Injection Robot
- It is the best choice for drying large quantities of material at once. Cabinetmakers use these machines because they are fast
- large injection molding machine
- Learn what industrial automation and robotics is
- linear robot
- linear robots
- low speed sound-proof granulator
- machine plastic molding
- make sure to add some! Improvements (2) Keyphrase in introduction: Your keyphrase or its synonyms appear in the first paragraph of the copy
- manipulator machine
- manufacturing
- medical grade injection molding machines
- medical injection molding machine
- medical injection molding machines
- micro injection molding machine
- middle speed granulator
- Mini CNC machine manufacturers.
- Mold Temperature Control System
- mold temperature controller
- mold temperature controllers
- molding material Dehumidifying System
- mould temperature control system
- mould temperature controller
- mould temperature controllers
- New electric injection molding machine
- nitrogen dryer manufacturer
- nitrogen dryer system manufacturer
- Oil type mold temperature controller
- Oil type mold temperature controllers
- open day
- Outbound links: No outbound links appear in this page. Add some! Images: No images appear on this page. Add some! Internal links: No internal links appear in this page
- PET Preform injection molding
- phone case maker machine
- phone case making machine
- plastic bottle making machine
- plastic bottle manufacturing
- plastic bucket making machine
- plastic bucket manufacturing
- Plastic chair making machine
- plastic forming equipment
- plastic hopper dryer
- plastic injection machine
- plastic injection machines
- plastic injection molding
- Plastic injection molding equipment
- Plastic injection molding machine
- Plastic Injection Molding Machines
- plastic injection moulding machine
- plastic injection robot
- Plastic Molding machine
- Plastic Molding Machines
- plastic molding press
- plastic moulding machine
- plastic phone case making machine
- plastic-molding machine
- powerful granulator
- Powerful Type Sound-Proof Granulator
- precision injection molding
- production of plastic seats
- pure water mould temperature controller
- Robot injection molding
- robot injection molding machine
- robot manufacturing companies
- Robotic arm for injection molding machine
- robotic injection molding machines
- robotics in injection molding
- SCARA robot
- SCARA robots
- Service-oriented manufacturing
- Servo Cylinder Robot
- servo driven robot
- Servo Driven Robots
- servo injection robots
- servo motor-driven linear robots
- servo-driven 3-axis robot
- Servo-Driven Robot
- Setup of injection machine
- Silicone Injection Molding Machine
- six-axis industrial robot
- Stainless Hopper Dryer
- Stainless Hopper Dryers
- star club
- swing arm robot
- take-out robots
- the choice between servo-driven robots and hydraulic robots will have a certain impact on efficiency
- the most popular injection molding machine
- the type of injection molding robot
- toggle clamp injection molding machine
- Toggle Hydraulic Injection Molding Machines
- toggle injection molding machine
- Top 10 brands of injection robots
- Topstar
- Topstar Engineering
- Topstar Industrial Robots
- Topstar injection molding intelligent
- Topstar Scara Robots
- Useful Injection molding machine
- Vertical machining centers
- volumetric type blender
- water chiller
- water chillers
- water distributor
- water type mold temperature controller
- Water Type MoldTemperature Controller
- Water-Type Mould Temperature Controllers
- We often face choices when performing injection molding. We will choose the type of injection molding machine
- wholesale of injection molding machines
- x carve CNC