What injection molding equipment is needed for the production of plastic seats
2023/08/30 By Topstar
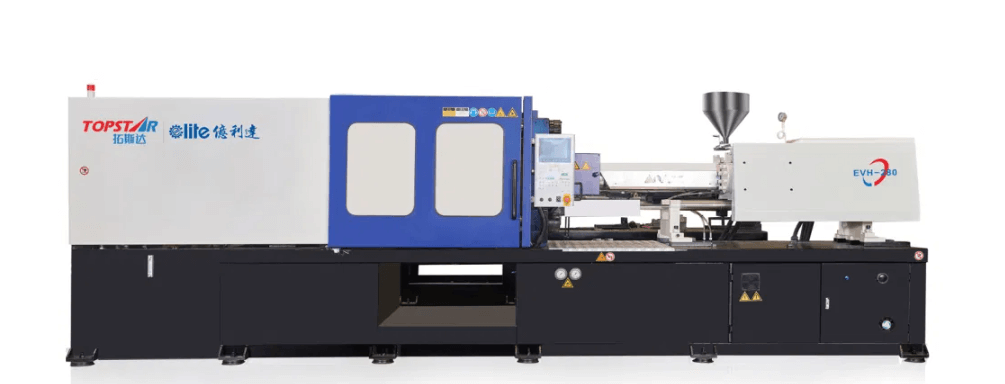
One of the customers that Topstar has contacted the most is the production of plastic seats, and we know very well what injection molding equipment they need. We share this article mainly to let more people who don’t understand what equipment is used in injection molding production and better understand the process and equipment flow. These small actions can pile up the growth of the injection molding industry.
Production of plastic seats requires injection molding machines!
The first equipment for producing plastic seats is an injection molding machine, injecting raw materials into molds. The raw material is then molded into the shape of your choice to create different items. The process begins by loading raw materials into an injection molding machine, which uses heat and pressure to transform them into their final form. These devices vary in size, complexity, and price point depending on the type of part you want to produce, but all are essential components of this complex manufacturing process.
Production of plastic seats also needs molds.
The production of plastic seats also requires molds. Molds come in various shapes and are manufactured in factories by mold makers. These people use their skills and knowledge to create the perfect mold for each plastic seat. They do this with special machines that allow them to create exact replicas of natural objects, which are then used as molds when producing plastic seats. The molds can vary in size, from small plastic parts like buttons or nuts to more significant automotive parts like engines or transmissions; they also come in many different shapes.
There is also a Material feeding system.
The Material feeding system transports the plastic pellets from the storage chamber to the injection molding machine. It consists of a hopper, a screw conveyor, and a screw feeder in an air-conditioned room. The melting screw in the injection chamber is suitable for material mixing at high temperatures. The heating of the barrel is done with thermal oil or electricity. A hydraulic system controls the pressure inside the inner cylinder. When the mold cools enough to open, the inner barrel pushes the molten plastic into the mold so that after each shot, the vertical stem of the punch presses down on the mold without material flowing out of the mold.
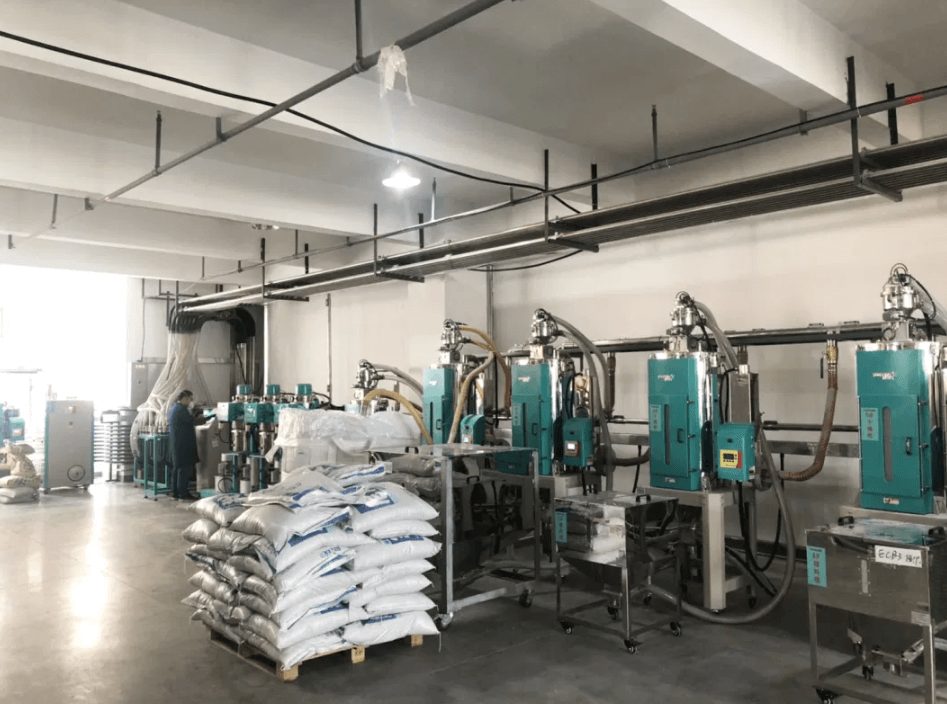
The cooling system is also one of the
The cooling system is also one of the most essential parts of plastic seat injection molding equipment. Its purpose is to remove heat from the mold and prevent warping and shrinkage. Heat can warp your product, meaning it won’t fit perfectly into its intended space when assembled or installed. The seat can suffer from dimensional instability or deformation without a proper cooling system to control this process. Controlling the temperature, cooling time, and other parameters of the cooling system can effectively reduce the plastic seat’s shrinkage rate and ensure the product size’s accuracy and consistency. Cooling systems also increase productivity and reduce costs. Increase production efficiency using an efficient cooling system to speed up and minimize injection cycle times.
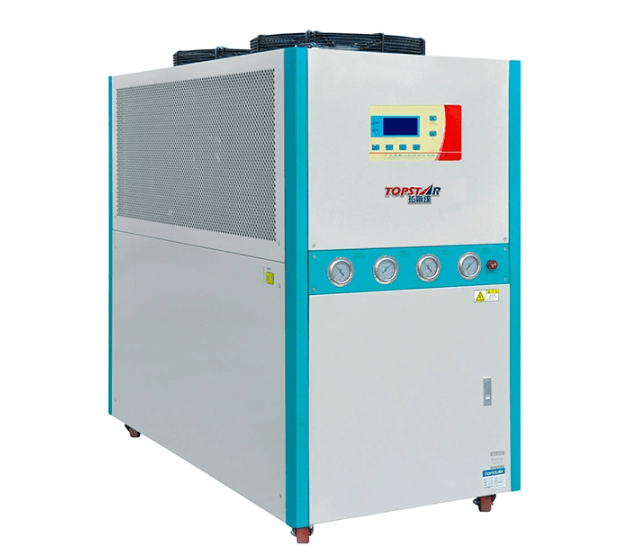
Finally, there are auxiliary equipment!
The production of plastic seats also requires auxiliary equipment, which plays a vital role in improving production efficiency, optimizing process flow, and so on. For example, automatic reclaiming robots are a joint aid that plays a crucial role in producing plastic seats. They can precisely remove the injection molded seat parts from the injection molding machine and move on to the next production stage. Nozzle cleaners are another essential accessory. During injection molding, plastic material may stick to the injection nozzle, affecting quality and results. Clean injection nozzles thoroughly to keep them in good working order by spraying high-pressure water or other cleaning agents.
In addition, auxiliary equipment includes automatic control systems, testing instruments, safety equipment, etc. A complete production line is indispensable for the existence of these equipment and machines, and they all serve as a link between the preceding and the following.
Final summary
Plastic seats require a lot of production equipment, with many different types of machines used in the process. What we mentioned in this article is just one of the most common equipment. Understanding the injection molding work of these standard equipment can make everyone more aware of producing a product by injection molding and allow more people to join this large industry. Middle.
TRENDING POSTS
- What factors can cause delays in the injection molding process of plastic molding machine? 2023/08/30
- Exhibition Review| Topstar participates in InterPlas Thailand 2024 2023/08/30
- Star Case | Topstar helps Santong upgrade its intelligent plant 2023/08/30
- Topstar Special | National Science and Technology Workers Day 2023/08/30
HOT TOPIC
- .ervo motor-driven linear robots
- 3 axis robot
- 3 axis robots
- 3 in 1 Compact Dehumidifying Dryer
- 3-axis robot
- 3-axis robots
- 5-axis CNC machine
- accuracy
- Air Chillers
- all electric injection molding machine
- all electric injection molding machines
- All-electric injection molding machines
- and overall production quality. Therefore
- AP-RubberPlas
- automated injection molding machine
- Automation changed engineering
- automation of injection molding robots
- auxiliary machine
- Bench Injection Molding Machine
- Cabinet dryer manufacturers
- Cabinet dryers
- chiller
- CNC Drilling Machine
- CNC Drilling Machines
- cnc engraving machine manufacturer
- cnc laser cutting machine manufacturer
- CNC machine
- CNC Machine Center
- CNC Machine for Sale
- CNC Machine Manufacturing
- CNC Machine Tool
- CNC machine tool product
- CNC Machining Center
- CNC wood carving machine
- Cooling system
- Cross-Walking Single Axis Servo Cylinder Robot
- Cross-Walking Single-Axis Servo Cylinder Robot
- Cross-Walking Three-Axis/Five-Axis Servo Driven Robot
- cross-walking three-axis/five-axis servo-driven robot
- Dehumidifier Dryer
- Dehumidifying Dryer
- delta parallel robot
- Desktop Injection Molding Machine
- Desktop injection molding machines
- Desktop Molding Machine
- desktop plastic injection machine
- Desktop Plastic Injection Molding Machine
- direct clamp injection molding machine
- Direct clamp injection molding machines
- Dosing & mixing system
- Drilling Centers
- Drying and dehumidification system
- drying and dehumidifying equipment
- Drying and Dehumidifying System
- drying system
- effective and efficient. Cabinet dryers are also used in other industries where large quantities of material need to be dried
- efficient injection molding machine
- elbow hydraulic injection molding machines
- electric injection molding machine
- electric injection molding machines
- energy-efficient injection molding robot
- energy-saving injection molding machine
- etc. Among injection molding robots
- exhibition
- features of CNC machine
- Feeding And Conveying System
- Five Axis Machine Center
- Fully automatic injection molding machine
- Gathering Topstar
- giant injection molding machine
- GMU-600 5-Axis Machining Center
- Granulating & Recycling System
- Heavy duty injection molding machine
- High-precision electric molding machines
- high-precision plastic molding machines
- high-speed all electric injection molding machine
- Honeycomb rotor dehumidifier
- horizontal injection molding machine
- Horizontal Injection Molding Machines
- Horizontal Injection Moulding Machine
- Horizontal Mixer manufacturer
- How The CNC Machine Works
- hybrid injection molding machine
- hydraulic injection molding machine
- Hydraulic Injection Molding Machines
- in this article
- Industrial robot
- Industrial Robot Chinese brand
- industrial robot parts
- industrial robot supplier
- Industrial robots
- Industry Chain
- Injection Manipulator
- injection manipulator robot
- injection mold machines
- Injection molding
- Injection molding automation
- Injection Molding Automation Solution
- injection molding dryer
- Injection molding equipment
- injection molding hopper dryer
- Injection molding machine
- injection molding machine brand
- Injection Molding Machine Factory
- Injection Molding Machine Manufacture
- Injection molding machine manufacturer
- injection molding machine manufacturers
- Injection molding machine procurement
- injection molding machine robotic arm
- injection molding machine with a robot
- Injection molding machines
- injection molding material dehumidifying
- injection molding plant
- Injection Molding Robot
- injection molding robot arm
- Injection molding robot automation
- Injection molding robotic arm
- injection molding robots
- Injection moulding machine
- Injection Moulding Robots
- Injection Robot
- Injection robot arm
- Injection robot manufacturer
- Injection robot wholesale
- injection robots
- intelligent injection molding machines
- Introducing Injection Robot
- It is the best choice for drying large quantities of material at once. Cabinetmakers use these machines because they are fast
- large injection molding machine
- Learn what industrial automation and robotics is
- linear robot
- linear robots
- low speed sound-proof granulator
- machine plastic molding
- make sure to add some! Improvements (2) Keyphrase in introduction: Your keyphrase or its synonyms appear in the first paragraph of the copy
- manipulator machine
- manufacturing
- medical grade injection molding machines
- medical injection molding machine
- medical injection molding machines
- micro injection molding machine
- middle speed granulator
- Mini CNC machine manufacturers.
- Mold Temperature Control System
- mold temperature controller
- mold temperature controllers
- molding material Dehumidifying System
- mould temperature control system
- mould temperature controller
- mould temperature controllers
- New electric injection molding machine
- nitrogen dryer manufacturer
- nitrogen dryer system manufacturer
- Oil type mold temperature controller
- Oil type mold temperature controllers
- open day
- Outbound links: No outbound links appear in this page. Add some! Images: No images appear on this page. Add some! Internal links: No internal links appear in this page
- PET Preform injection molding
- phone case maker machine
- phone case making machine
- plastic bottle making machine
- plastic bottle manufacturing
- plastic bucket making machine
- plastic bucket manufacturing
- Plastic chair making machine
- plastic forming equipment
- plastic hopper dryer
- plastic injection machine
- plastic injection machines
- plastic injection molding
- Plastic injection molding equipment
- Plastic injection molding machine
- Plastic Injection Molding Machines
- plastic injection moulding machine
- plastic injection robot
- Plastic Molding machine
- Plastic Molding Machines
- plastic molding press
- plastic moulding machine
- plastic phone case making machine
- plastic-molding machine
- powerful granulator
- Powerful Type Sound-Proof Granulator
- precision injection molding
- precision injection molding machines
- production of plastic seats
- pure water mould temperature controller
- Robot injection molding
- robot injection molding machine
- robot manufacturing companies
- Robotic arm for injection molding machine
- robotic injection molding machines
- robotics in injection molding
- SCARA robot
- SCARA robots
- Service-oriented manufacturing
- Servo Cylinder Robot
- servo driven robot
- Servo Driven Robots
- servo injection robots
- servo motor-driven linear robots
- servo-driven 3-axis robot
- Servo-Driven Robot
- Setup of injection machine
- Silicone Injection Molding Machine
- six-axis industrial robot
- Stainless Hopper Dryer
- Stainless Hopper Dryers
- star club
- swing arm robot
- take-out robots
- the choice between servo-driven robots and hydraulic robots will have a certain impact on efficiency
- the most popular injection molding machine
- the type of injection molding robot
- toggle clamp injection molding machine
- Toggle Hydraulic Injection Molding Machines
- toggle injection molding machine
- Top 10 brands of injection robots
- Topstar
- Topstar Engineering
- Topstar Industrial Robots
- Topstar injection molding intelligent
- Topstar Scara Robots
- Useful Injection molding machine
- Vertical machining centers
- volumetric type blender
- water chiller
- water chillers
- water distributor
- water type mold temperature controller
- Water Type MoldTemperature Controller
- Water-Type Mould Temperature Controllers
- We often face choices when performing injection molding. We will choose the type of injection molding machine
- wholesale of injection molding machines
- x carve CNC