What type of large injection molding machine is best?
2024/05/01 By Topstar
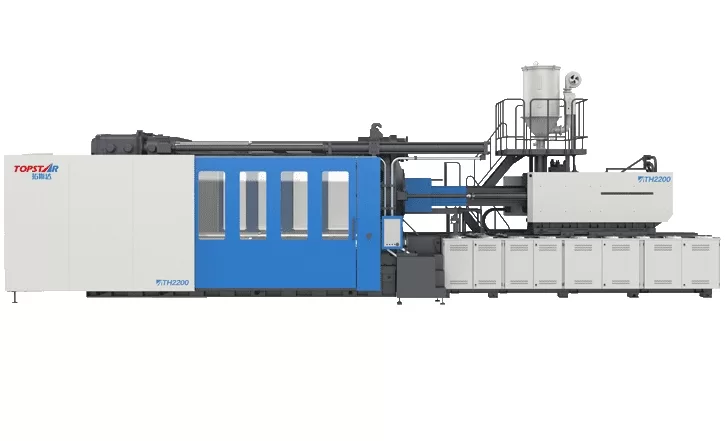
When faced with applications requiring large plastic parts, choosing the type of large injection molding machine is critical for manufacturers. If the choice is inappropriate, it will directly affect the final product molding. In this guide, we will share with you which type of large injection molding machine is best and what conditions and capabilities it has.
TH large injection molding machine type
Among Topstar, the TH series is the most suitable and best large injection molding machine type. They are direct-pressure injection molding machines with a clamping force ranging from 550T to 2800 T. Its function is determined by several core attributes, including mold clamping structure, platen size, and injection cylinder structure. The TH series can produce products with complex shapes and high dimensional accuracy, especially for products with thin walls, deep cavities, multiple cavities, and high dynamic balance requirements. They adopt advanced oil circuit designs in their product accessories and have European professional controllers to stabilize machine movements. At the same time, we also pay more attention to the actual customer experience and add many details of human-computer interaction to the design.
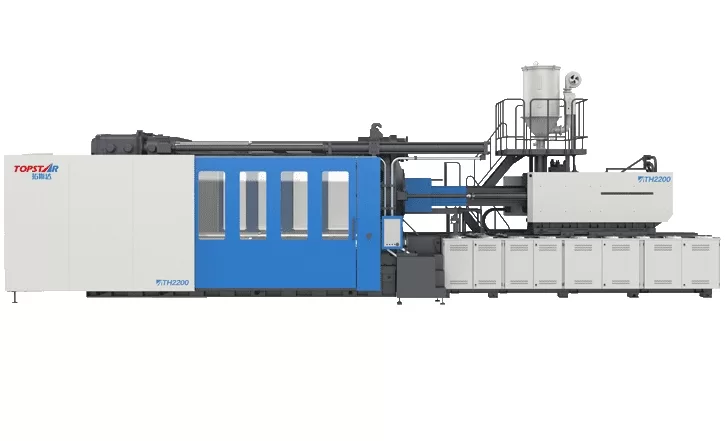
Large injection molding machines adopt CNC proportional back pressure technology
Large injection molding machines equipped with CNC proportional back pressure technology enable fine control of back pressure during the plasticizing phase of the molding cycle. Back pressure occurs when the screw encounters resistance as it rotates and pushes the molten plastic forward in the barrel. Unlike traditionally, back pressure can now be adjusted and controlled electronically with high precision through CNC integration. A key component of the technology is the proportional solenoid valve, which regulates the hydraulic pressure applied to the screw based on real-time feedback and preset parameters. This precise control ensures consistent plastic melt density and uniformity while reducing potential defects in the product.
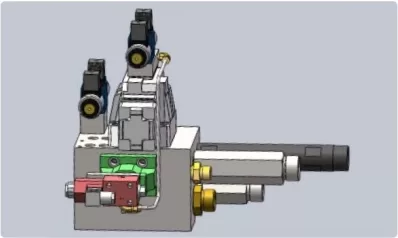
Bi-directional synchronous injection cylinder structure
The bi-directional synchronous injection cylinder structure in large injection molding machines usually involves two identical hydraulic cylinders positioned relative to each other, which can prevent an unbalanced load from damaging the screw and linear rail. There are many advantages to using a bi-directional synchronous injection cylinder structure in large injection molding machines. First, it can balance force distribution, reduce wear on mechanical components of the machine, and extend the service life of the equipment. Second, it injects molten plastic with precise force and speed, thereby improving product quality and reducing defects such as warping or sink marks. Its advanced CNC or PLC-based control system controls the synchronization of the two cylinders. You can adjust the speed and pressure of each individual cylinder while ensuring they operate in complete harmony.
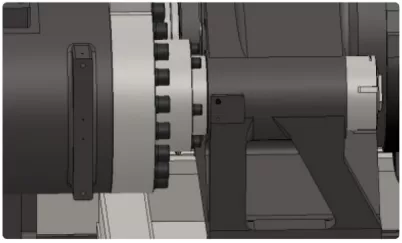
Large injection molding machine adopts central four-cylinder mold clamping
The use of central four-cylinder clamping is the core of large-scale injection molding machines, which can achieve uniform force distribution and a strong clamping mechanism. The central four-cylinder clamping force can evenly distribute the clamping force in the center of the template, which can directly reduce mold wear and improve product consistency. One of the main advantages of this technology is that the direct clamping force exerted by the cylinder eliminates the mechanical stress and strain commonly observed in toggle systems. This technology not only extends the life of the mold but also speeds up the clamping cycle.
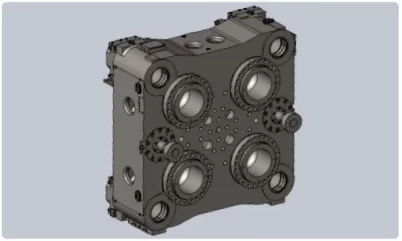
Patented sealing structure
In large injection molding machines, the sealing structure mainly enhances the sealing ability around the injection unit, a key component where we heat plastic materials and inject them into the mold. This sealing structure solves the problem of easy wear and leakage due to the high pressure and temperature involved by incorporating advanced materials and unique configurations. The materials chosen in the seal construction are high-performance polymers and elastomers that offer excellent resistance to thermal degradation and chemical wear. They ensure that seals maintain their integrity and elasticity even under extreme temperature and pressure conditions.
This is the best choice
The best type of large injection molding machine in Topstar is the TH series, which is the best choice for large plastic product manufacturers. Their sol back pressure technology, two-way synchronous injection cylinder structure, and central four-cylinder mold locking structure can prevent the mold from being affected by the deformation of the machine plate. The product has high molding accuracy and a high pass rate of the final product. You can also go to our official website to get more relevant information.
TRENDING POSTS
- What factors can cause delays in the injection molding process of plastic molding machine? 2024/05/01
- Exhibition Review| Topstar participates in InterPlas Thailand 2024 2024/05/01
- Star Case | Topstar helps Santong upgrade its intelligent plant 2024/05/01
- Topstar Special | National Science and Technology Workers Day 2024/05/01
HOT TOPIC
- .ervo motor-driven linear robots
- 3 axis robot
- 3 axis robots
- 3 in 1 Compact Dehumidifying Dryer
- 3-axis robot
- 3-axis robots
- 5-axis CNC machine
- accuracy
- Air Chillers
- all electric injection molding machine
- all electric injection molding machines
- All-electric injection molding machines
- and overall production quality. Therefore
- AP-RubberPlas
- automated injection molding machine
- Automation changed engineering
- automation of injection molding robots
- auxiliary machine
- Bench Injection Molding Machine
- Cabinet dryer manufacturers
- Cabinet dryers
- chiller
- CNC Drilling Machine
- CNC Drilling Machines
- cnc engraving machine manufacturer
- cnc laser cutting machine manufacturer
- CNC machine
- CNC Machine Center
- CNC Machine for Sale
- CNC Machine Manufacturing
- CNC Machine Tool
- CNC machine tool product
- CNC Machining Center
- CNC wood carving machine
- Cooling system
- Cross-Walking Single Axis Servo Cylinder Robot
- Cross-Walking Single-Axis Servo Cylinder Robot
- Cross-Walking Three-Axis/Five-Axis Servo Driven Robot
- cross-walking three-axis/five-axis servo-driven robot
- Dehumidifier Dryer
- Dehumidifying Dryer
- delta parallel robot
- Desktop Injection Molding Machine
- Desktop injection molding machines
- Desktop Molding Machine
- desktop plastic injection machine
- Desktop Plastic Injection Molding Machine
- direct clamp injection molding machine
- Direct clamp injection molding machines
- Dosing & mixing system
- Drilling Centers
- Drying and dehumidification system
- drying and dehumidifying equipment
- Drying and Dehumidifying System
- drying system
- effective and efficient. Cabinet dryers are also used in other industries where large quantities of material need to be dried
- efficient injection molding machine
- elbow hydraulic injection molding machines
- electric injection molding machine
- electric injection molding machines
- energy-efficient injection molding robot
- energy-saving injection molding machine
- etc. Among injection molding robots
- exhibition
- features of CNC machine
- Feeding And Conveying System
- Five Axis Machine Center
- Fully automatic injection molding machine
- Gathering Topstar
- giant injection molding machine
- GMU-600 5-Axis Machining Center
- Granulating & Recycling System
- Heavy duty injection molding machine
- High-precision electric molding machines
- high-precision plastic molding machines
- high-speed all electric injection molding machine
- Honeycomb rotor dehumidifier
- horizontal injection molding machine
- Horizontal Injection Molding Machines
- Horizontal Injection Moulding Machine
- Horizontal Mixer manufacturer
- How The CNC Machine Works
- hybrid injection molding machine
- hydraulic injection molding machine
- Hydraulic Injection Molding Machines
- in this article
- Industrial robot
- Industrial Robot Chinese brand
- industrial robot parts
- industrial robot supplier
- Industrial robots
- Industry Chain
- Injection Manipulator
- injection manipulator robot
- injection mold machines
- Injection molding
- Injection molding automation
- Injection Molding Automation Solution
- injection molding dryer
- Injection molding equipment
- injection molding hopper dryer
- Injection molding machine
- injection molding machine brand
- Injection Molding Machine Factory
- Injection Molding Machine Manufacture
- Injection molding machine manufacturer
- injection molding machine manufacturers
- Injection molding machine procurement
- injection molding machine robotic arm
- injection molding machine with a robot
- Injection molding machines
- injection molding material dehumidifying
- injection molding plant
- Injection Molding Robot
- injection molding robot arm
- Injection molding robot automation
- Injection molding robotic arm
- injection molding robots
- Injection moulding machine
- Injection Moulding Robots
- Injection Robot
- Injection robot arm
- Injection robot manufacturer
- Injection robot wholesale
- injection robots
- intelligent injection molding machines
- Introducing Injection Robot
- It is the best choice for drying large quantities of material at once. Cabinetmakers use these machines because they are fast
- large injection molding machine
- large injection molding machines
- Learn what industrial automation and robotics is
- linear robot
- linear robots
- low speed sound-proof granulator
- machine plastic molding
- make sure to add some! Improvements (2) Keyphrase in introduction: Your keyphrase or its synonyms appear in the first paragraph of the copy
- manipulator machine
- manufacturing
- medical grade injection molding machines
- medical injection molding machine
- medical injection molding machines
- micro injection molding machine
- middle speed granulator
- Mini CNC machine manufacturers.
- Mold Temperature Control System
- mold temperature controller
- mold temperature controllers
- molding material Dehumidifying System
- mould temperature control system
- mould temperature controller
- mould temperature controllers
- New electric injection molding machine
- nitrogen dryer manufacturer
- nitrogen dryer system manufacturer
- Oil type mold temperature controller
- Oil type mold temperature controllers
- open day
- Outbound links: No outbound links appear in this page. Add some! Images: No images appear on this page. Add some! Internal links: No internal links appear in this page
- PET Preform injection molding
- phone case maker machine
- phone case making machine
- plastic bottle making machine
- plastic bottle manufacturing
- plastic bucket making machine
- plastic bucket manufacturing
- Plastic chair making machine
- plastic forming equipment
- plastic hopper dryer
- plastic injection machine
- plastic injection machines
- plastic injection molding
- Plastic injection molding equipment
- Plastic injection molding machine
- Plastic Injection Molding Machines
- plastic injection moulding machine
- plastic injection robot
- Plastic Molding machine
- Plastic Molding Machines
- plastic molding press
- plastic moulding machine
- plastic phone case making machine
- plastic-molding machine
- powerful granulator
- Powerful Type Sound-Proof Granulator
- precision injection molding
- precision injection molding machines
- production of plastic seats
- pure water mould temperature controller
- Robot injection molding
- robot injection molding machine
- robot manufacturing companies
- Robotic arm for injection molding machine
- robotic injection molding machines
- robotics in injection molding
- SCARA robot
- SCARA robots
- Service-oriented manufacturing
- Servo Cylinder Robot
- servo driven robot
- Servo Driven Robots
- servo injection robots
- servo motor-driven linear robots
- servo-driven 3-axis robot
- Servo-Driven Robot
- Setup of injection machine
- Silicone Injection Molding Machine
- six-axis industrial robot
- Stainless Hopper Dryer
- Stainless Hopper Dryers
- star club
- swing arm robot
- take-out robots
- the choice between servo-driven robots and hydraulic robots will have a certain impact on efficiency
- the most popular injection molding machine
- the type of injection molding robot
- toggle clamp injection molding machine
- Toggle Hydraulic Injection Molding Machines
- toggle injection molding machine
- Top 10 brands of injection robots
- Topstar
- Topstar Engineering
- Topstar Industrial Robots
- Topstar injection molding intelligent
- Topstar Scara Robots
- Useful Injection molding machine
- Vertical machining centers
- volumetric type blender
- water chiller
- water chillers
- water distributor
- water type mold temperature controller
- Water Type MoldTemperature Controller
- Water-Type Mould Temperature Controllers
- We often face choices when performing injection molding. We will choose the type of injection molding machine
- wholesale of injection molding machines
- x carve CNC