Why are servo drives better than stepper motor drives in an injection robot?
2025/05/23 By Topstar
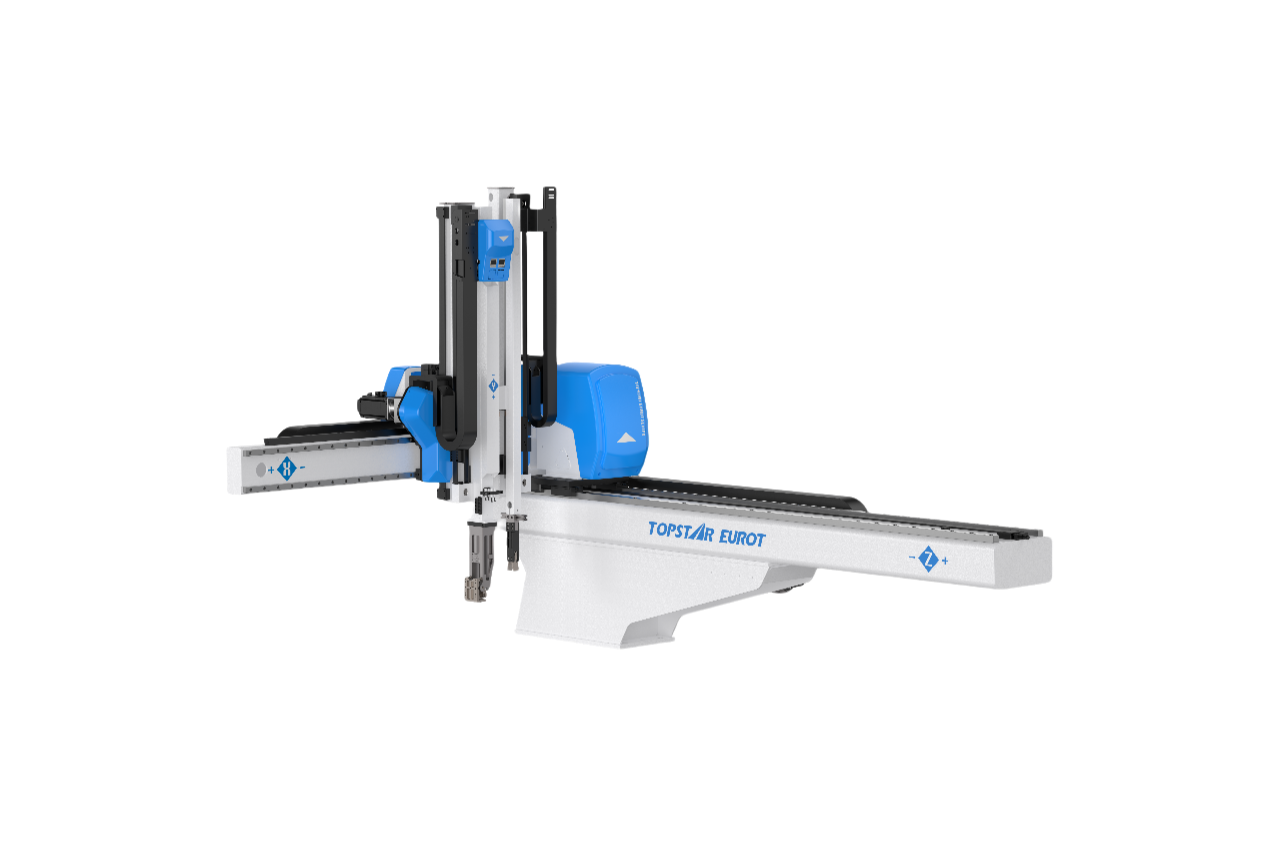
Injection robots are responsible for precise part removal, placement, and secondary operations such as insert loading, stacking, and quality inspection in injection molding. When purchasing or configuring an injection robot, there are two different drive options: a stepper motor drive and a servo drive to drive each axis, whether a simple take-out robot or a 3-axis robot. The advantage of using a stepper motor is that it provides basic cost advantages and simple open-loop control. Still, it is often unable to meet the requirements under more demanding production conditions. In contrast, servo drives provide closed-loop feedback, greater torque, and more precise control capabilities.
Bringing stable torque and high-speed capabilities to the injection robot
One of the main reasons for choosing to use servo drives in injection robots is to maintain torque consistency over a wide speed range. Stepper motor drives produce peak torque at low speeds, but the torque is quickly lost as speed increases, limiting cycle time and robot throughput, which can affect production issues on high-volume molding lines. In contrast, servo drives maintain nearly constant torque at rated speeds, allowing three-axis robot arms to rapidly accelerate and decelerate without sacrificing strength. This consistent high-speed capability directly translates into faster pick-and-place operations and reduced machine idle time. At the same time, Topstar’s servo injection robots have cycle times that are 20-30% faster than equivalent stepper-driven models. For production results, it can directly improve overall equipment efficiency and handle more complex parts.
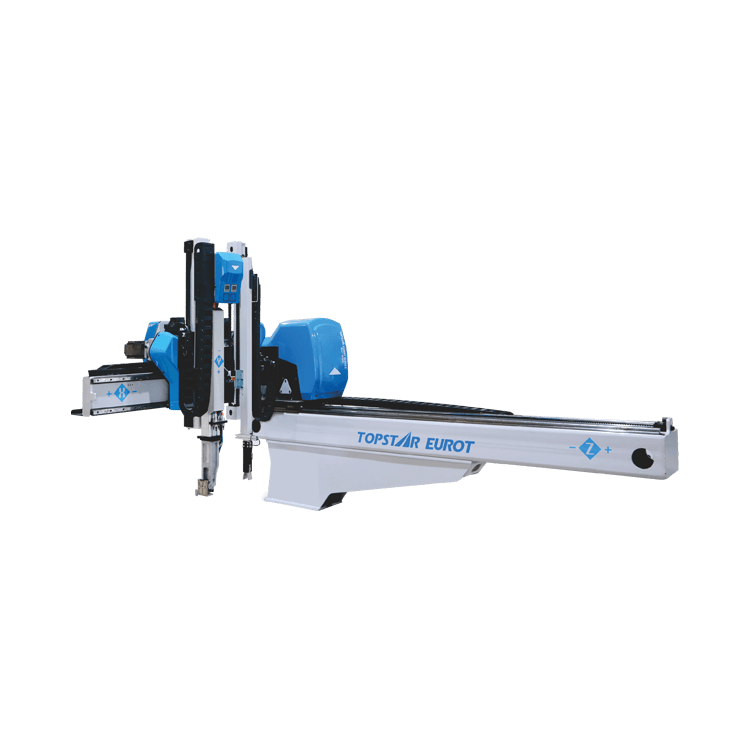
More precise positioning can be obtained
Servo-driven injection robots use control systems and communication protocols to achieve accurate closed-loop feedback control. This enables the injection robot controller to continuously compare the actual position with the command trajectory and correct any deviations in real-time. In contrast, stepper-driven robots usually operate in an open loop, assuming that the steps have been successfully executed without verifying the actual movement; this can lead to missed steps, accumulated positioning errors, and part misalignment. Servo robots provide precise position, speed, and torque control. Handling precision molds, coordinating synchronous multi-axis motion, or integrating visual guided part removal can bring a more stable and precise level of control. By maintaining absolute position integrity, servo injection molding robots ensure consistent part quality, minimize secondary rework, and support high-precision molding requirements in the automotive, medical, and electronics industries.
Bringing Dynamic Response and Vibration Suppression to Injection Robot
Dynamic response is required when injection robots quickly start, stop, or change complex directions between mold opening and closing cycles. Servo drives with advanced control loops and vibration suppression for injection robots can actively suppress mechanical resonances and prevent overshoot or ringing during rapid motion. This results in smoother, jitter-free operation, reduced wear on mechanical components, and position accuracy at accelerations exceeding 5 g. In contrast, stepper drive systems often experience significant oscillations at high speeds due to their inherent step-like motion profiles. Topstar’s range of servo robots exhibits good cycle stability at high accelerations, extending actuator life by 30% and shortening maintenance intervals. This smooth dynamic behavior also protects delicate molded parts from mechanical shock.
Improving Energy Efficiency and Regenerative Braking for Injection Robot
Energy efficiency is another area where servo drives excel in injection molding robots. Many servo systems use a common DC bus and regenerative braking to capture kinetic energy during deceleration and feed it back into the facility grid or shared bus instead of dissipating it as heat. This regeneration capability can reduce overall drive energy consumption by up to 20%, equating to significant energy savings over thousands of daily cycles. In contrast, stepper motors consume constant current to maintain torque even when idling and lack regeneration, resulting in higher continuous energy consumption and increased heat generation in the control cabinet. In addition, servo drives can achieve more precise torque control, eliminating energy waste during low-load motion. The energy-saving advantages of servo injection robots can significantly lower operating expenses and reduce environmental impact.
Seamless integration and control flexibility
Modern injection molding production lines require seamless integration of injection robots with the control system of the injection molding machine and even the enterprise-level MES system. Servo drives provide advanced motion control functions such as electronic cams, multi-axis interpolation, and automatic tuning, simplifying programming and reducing the need for external motion controllers. The servo-driven injection robots equipped by Topstar can perform complex pick-and-place trajectories, undercutting movements, and synchronized mold opening links with millisecond accuracy. Integrating communication protocols such as Modbus RTU facilitates real-time data exchange, remote diagnostics, and firmware updates. Stepper motor-based settings lack many advanced features and usually require additional hardware or software for synchronization. Topstar’s 3-axis robot solution leverages servo drives to provide a flexible, scalable automation architecture that can quickly adapt to mold and product mix changes.

Servo drives for optimal performance
Generally, stepper motor drives suit cost-sensitive or low-duty-cycle injection robot applications. In contrast, servo drives provide excellent torque consistency, positioning accuracy, dynamic response, energy efficiency, integration flexibility, and reliability. Investing in servo-driven or 3-axis robots is a wise choice for manufacturers seeking to maximize production, maintain tight tolerances, and achieve long-term operating cost savings. Topstar’s servo-driven injection robot solution fully reflects these advantages, providing the performance, adaptability, and sustainability required to excel in today’s high-volume, precision-driven injection molding field. By leveraging servo technology, companies can shorten cycle times, reduce defects, simplify maintenance processes, and ensure that their production lines meet changing market demands.
Utilize servo drives for optimal performance
Stepper motor drives are suitable for cost-sensitive or low-duty-cycle injection molding robot applications. In contrast, servo drives provide excellent torque consistency, positioning accuracy, dynamic response, energy efficiency, integration flexibility, and reliability. Topstar’s servo robots fully reflect these advantages, providing the performance and adaptability required to stand out in today’s high-volume, precision-driven injection molding field.
TRENDING POSTS
- What factors can cause delays in the injection molding process of plastic molding machine? 2025/05/23
- Exhibition Review| Topstar participates in InterPlas Thailand 2024 2025/05/23
- Star Case | Topstar helps Santong upgrade its intelligent plant 2025/05/23
- Topstar Special | National Science and Technology Workers Day 2025/05/23
HOT TOPIC
- .ervo motor-driven linear robots
- 1.0 guangdong topstar technology co. ltd
- 1.0 topstar china
- 1.0 topstar robot
- 11
- 2
- 21
- 23
- 3 axis robot
- 3 axis robots
- 3 in 1 Compact Dehumidifying Dryer
- 3-axis robot
- 3-axis robots
- 39
- 41
- 5-axis CNC machine
- 62
- accuracy
- Air Chillers
- all electric injection molding machine
- all electric injection molding machines
- All-electric injection molding machines
- and overall production quality. Therefore
- AP-RubberPlas
- automated injection molding machine
- Automation changed engineering
- automation of injection molding robots
- auxiliary machine
- Bench Injection Molding Machine
- Cabinet dryer manufacturers
- Cabinet dryers
- chiller
- CNC Drilling Machine
- CNC Drilling Machines
- cnc engraving machine manufacturer
- cnc laser cutting machine manufacturer
- CNC machine
- CNC Machine Center
- CNC Machine for Sale
- CNC Machine Manufacturing
- CNC Machine Tool
- CNC machine tool product
- CNC Machining Center
- CNC wood carving machine
- Cooling system
- Cross-Walking Single Axis Servo Cylinder Robot
- Cross-Walking Single-Axis Servo Cylinder Robot
- Cross-Walking Three-Axis/Five-Axis Servo Driven Robot
- cross-walking three-axis/five-axis servo-driven robot
- Dehumidifier Dryer
- Dehumidifying Dryer
- delta parallel robot
- Desktop Injection Molding Machine
- Desktop injection molding machines
- Desktop Molding Machine
- desktop plastic injection machine
- Desktop Plastic Injection Molding Machine
- direct clamp injection molding machine
- Direct clamp injection molding machines
- Dosing & mixing system
- Drilling Centers
- Drying and dehumidification system
- drying and dehumidifying equipment
- Drying and Dehumidifying System
- drying system
- effective and efficient. Cabinet dryers are also used in other industries where large quantities of material need to be dried
- efficient injection molding machine
- elbow hydraulic injection molding machines
- electric injection molding machine
- electric injection molding machines
- energy-efficient injection molding robot
- energy-efficient water chiller
- energy-efficient water chillers
- energy-saving injection molding machine
- etc. Among injection molding robots
- exhibition
- features of CNC machine
- Feeding And Conveying System
- Five Axis Machine Center
- Fully automatic injection molding machine
- Gathering Topstar
- giant injection molding machine
- GMU-600 5-Axis Machining Center
- Granulating & Recycling System
- Heavy duty injection molding machine
- High-precision electric molding machines
- high-precision plastic molding machines
- high-speed all electric injection molding machine
- high-speed electric injection molding machine
- High-Speed Packaging Injection Molding
- Honeycomb rotor dehumidifier
- horizontal injection molding machine
- Horizontal Injection Molding Machines
- Horizontal Injection Moulding Machine
- Horizontal Mixer manufacturer
- How The CNC Machine Works
- hybrid injection molding machine
- hydraulic injection molding machine
- Hydraulic Injection Molding Machines
- in this article
- Industrial robot
- Industrial Robot Chinese brand
- industrial robot parts
- industrial robot supplier
- Industrial robots
- Industry Chain
- Injection Manipulator
- injection manipulator robot
- injection mold machines
- Injection molding
- Injection molding automation
- Injection Molding Automation Solution
- injection molding dryer
- Injection molding equipment
- injection molding hopper dryer
- Injection molding machine
- injection molding machine brand
- Injection Molding Machine Factory
- Injection Molding Machine Manufacture
- Injection molding machine manufacturer
- injection molding machine manufacturers
- Injection molding machine procurement
- injection molding machine robotic arm
- injection molding machine with a robot
- Injection molding machines
- injection molding material dehumidifying
- injection molding plant
- injection molding process
- Injection Molding Robot
- injection molding robot arm
- Injection molding robot automation
- Injection molding robotic arm
- injection molding robots
- Injection moulding machine
- injection moulding machines
- Injection Moulding Robots
- Injection Robot
- Injection robot arm
- Injection robot manufacturer
- Injection robot wholesale
- injection robots
- intelligent injection molding machines
- intelligent mold temperature
- intelligent mold temperature controller
- Intelligent mould temperature controller
- Introducing Injection Robot
- It is the best choice for drying large quantities of material at once. Cabinetmakers use these machines because they are fast
- Large flow water type mold temperature controller
- large injection molding machine
- large injection molding machines
- Learn what industrial automation and robotics is
- linear robot
- linear robots
- low speed sound-proof granulator
- machine plastic molding
- make sure to add some! Improvements (2) Keyphrase in introduction: Your keyphrase or its synonyms appear in the first paragraph of the copy
- manipulator machine
- manufacturing
- medical grade injection molding machines
- medical injection molding machine
- medical injection molding machines
- micro injection molding machine
- middle speed granulator
- Mini CNC machine manufacturers.
- Mold Temperature Control System
- mold temperature controller
- mold temperature controllers
- molding material Dehumidifying System
- mould temperature control system
- mould temperature controller
- mould temperature controllers
- New electric injection molding machine
- nitrogen dryer manufacturer
- nitrogen dryer system manufacturer
- Oil type mold temperature controller
- Oil type mold temperature controllers
- open day
- optical component injection molding
- Outbound links: No outbound links appear in this page. Add some! Images: No images appear on this page. Add some! Internal links: No internal links appear in this page
- PET Preform injection molding
- phone case maker machine
- phone case making machine
- phone cover making machine
- plastic bottle making machine
- plastic bottle manufacturing
- plastic bucket making machine
- plastic bucket manufacturing
- Plastic chair making machine
- plastic forming equipment
- plastic hopper dryer
- plastic injection machine
- plastic injection machines
- plastic injection molding
- Plastic injection molding equipment
- Plastic injection molding machine
- Plastic Injection Molding Machines
- plastic injection moulding machine
- plastic injection moulding machines
- plastic injection robot
- plastic molding
- Plastic Molding machine
- plastic molding machine 1
- Plastic Molding Machines
- plastic molding press
- plastic moulding machine
- plastic phone case making machine
- plastic-molding machine
- powerful granulator
- Powerful Type Sound-Proof Granulator
- precision injection molding
- precision injection molding machines
- production of plastic seats
- pure water mould temperature controller
- Robot injection molding
- robot injection molding machine
- robot manufacturing companies
- Robotic arm for injection molding machine
- robotic injection molding machines
- robotics in injection molding
- SCARA robot
- SCARA robots
- Service-oriented manufacturing
- Servo Cylinder Robot
- servo driven robot
- Servo Driven Robots
- servo injection molding machine
- servo injection robots
- servo motor-driven linear robots
- servo-driven 3-axis robot
- Servo-Driven Robot
- Setup of injection machine
- Silicone Injection Molding Machine
- six-axis industrial robot
- Stainless Hopper Dryer
- Stainless Hopper Dryers
- star club
- swing arm robot
- take-out robot
- take-out robots
- the choice between servo-driven robots and hydraulic robots will have a certain impact on efficiency
- the most popular injection molding machine
- the type of injection molding robot
- TMII injection molding machine
- toggle clamp injection molding machine
- Toggle Hydraulic Injection Molding Machines
- toggle injection molding machine
- Top 10 brands of injection robots
- Topstar
- Topstar Engineering
- Topstar Industrial Robots
- Topstar injection molding intelligent
- Topstar Scara Robots
- Useful Injection molding machine
- Vertical machining centers
- volumetric type blender
- water chiller
- water chillers
- water distributor
- water type mold temperature controller
- Water Type MoldTemperature Controller
- Water-Type Mould Temperature Controllers
- We often face choices when performing injection molding. We will choose the type of injection molding machine
- wholesale of injection molding machines
- x carve CNC
- 热门查询 点击次数 展示 排名 topstar