Why do plastics manufacturers prefer a servo-driven 3-axis robot?
- 3-axis robot
- 3-axis robots
- energy-efficient injection molding robot
- injection molding robots
- servo-driven 3-axis robot
2025/05/19 By Topstar
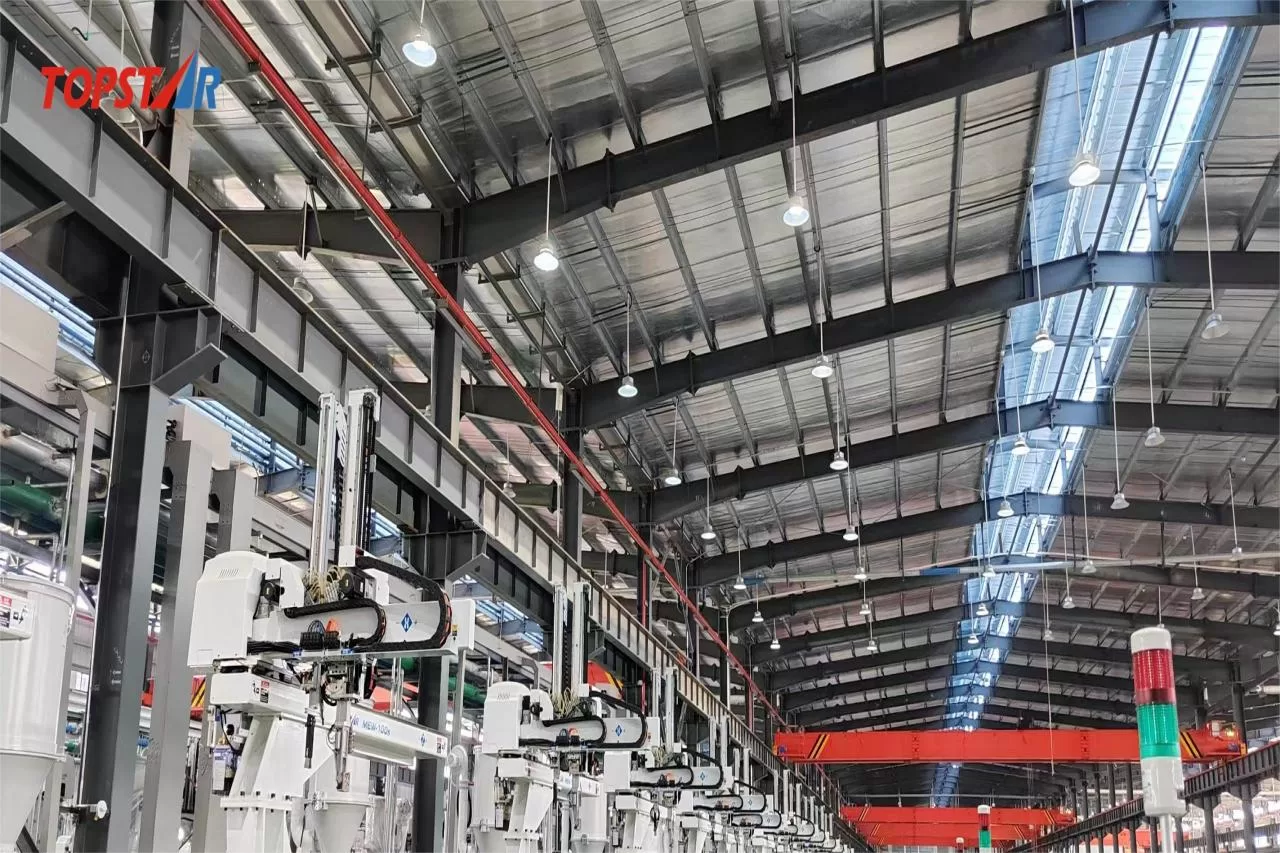
Unlike pneumatic or hydraulic robots, susceptible to compressibility, heat, and operating noise, servo-driven 3-axis robot provide clean, quiet, and highly repeatable motion with tight and precise speed control. This level of precision makes it easy to handle precision-molded parts, reduce scrap, and increase overall production. In addition, servo drives support complex motion trajectories. In high-speed injection molding, servo drives can improve product quality and simplify workflow integration, enabling plastic product manufacturers to consistently complete insert embedding and post-molding pick-up, tray placement, and boxing.
Precise control with servo-driven 3-axis robot
Precision and repeatability are the core of injection molding robots. Controlled by high-resolution encoders and closed-loop feedback, servo drives provide consistent positioning in every cycle, ensuring that every part is treated the same. This repeatability can directly translate into uniform part quality, reduced rework, and minimized inspection costs. Servo drives can maintain a path accuracy of ±0.05 mm even at high speeds. This precision is critical for micro-molding applications, thin-wall packaging components, and medical device housings. In addition, this precision control facilitates seamless integration with vision systems and force sensors for adaptive pick-and-place and in-line quality verification, allowing plastic producers to benefit from fewer defective parts and higher yields due to reduced scrap.
3-axis robot’s five-in-one servo drive architecture
The highlight of the Topstar servo-driven 3-axis robot is the “five-in-one servo drive” architecture, which integrates the control of five servo motors into a compact drive unit. By integrating multiple axes into one powerful drive, the three-axis robot achieves truly synchronous multi-axis motion without delay, enabling precise coordination of auxiliary tasks such as mold opening, part extraction, and transfer. Plastic product manufacturers will benefit from smaller production space, simpler power wiring, and less spare parts management. The integrated drive communicates via a high-speed fieldbus, providing real-time current, speed, and position diagnostics for all five channels, enabling predictive maintenance and rapid troubleshooting. This integration also minimizes electromagnetic interference and simplifies the integration of the entire injection molding system, allowing engineers to deploy advanced motion trajectories and safety interlocks with fewer components. This enables plastics manufacturers to achieve higher system reliability and lower total cost of ownership.
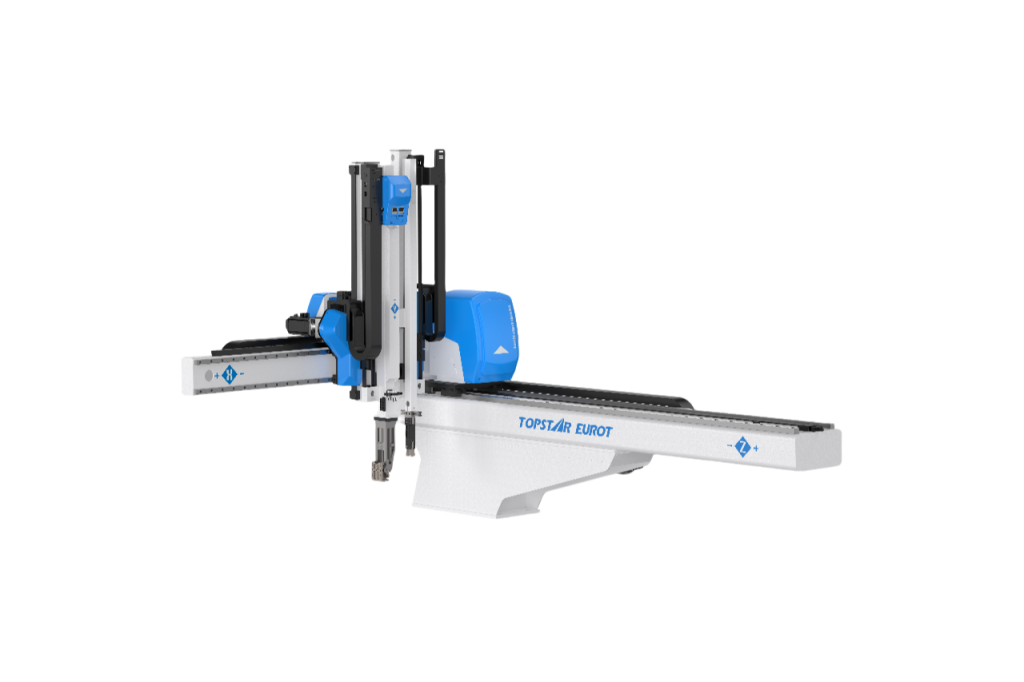
Multi-axis control by CPU chip allocation
The unique feature of the “Five-in-One Servo Drive” architecture is the unique CPU architecture that manages five independent servo axes using only three high-performance chips. Each CPU controls two axes, combining computational efficiency with powerful real-time processing capabilities. The third central processor monitors master coordination, safety protocols, and human-machine interface tasks. This streamlined control topology reduces inter-axis latency, achieving smoother acceleration curves and more accurate contour tracking capabilities in delicate demolding operations. In addition, by distributing processing tasks to multiple CPUs, the 3-axis robot can maintain high throughput even under high loads and complex motion sequences.
At the same time, this compact CPU layout simplifies firmware updates, allows deployment to all axes, and speeds up diagnostic procedures, allowing maintenance personnel to pinpoint abnormal conditions in specific axes quickly. And under the integrated control system, hardware costs are reduced, cooling requirements within the drive housing are reduced, and long-term reliability is improved, enabling complex multi-axis coordination with minimal infrastructure.
High power output and stable torque output
To meet the dynamic needs of injection molding, fast part extraction, transfer to overcome cyclic inertia, and precise deposition. Topstar’s servo-driven 3-axis robot is rated for up to 750 W of continuous torque per axis and higher peak torque. Such a powerful rated power ensures that the 3-axis robot maintains consistent torque under different payloads, completing the grasping of lightweight micro-molded connectors to larger housings and components. In addition, high power density also means faster cycle times, enabling 3-axis robots to accelerate and decelerate quickly without sacrificing position accuracy or generating mechanical clearance. The transmission system uses low-inertia servo motors and precision planetary gearboxes. It uses a rack and pinion meshing transmission before and after, which has high stiffness and can respond immediately to motion commands. As a result, plastic product manufacturers can confidently increase productivity, optimize mold cycle sequences, and reduce reliance on secondary manual operations.
Improve the overall energy efficiency of 3-axis robot
Topstar’s servo-driven 3-axis robot adopts a multi-axis common DC bus architecture, which can achieve up to 20% energy savings. When one axis decelerates, its regenerative energy is fed back to the shared DC bus and immediately provided to other axes that need to accelerate, reducing the total power consumption of the facility grid. This regenerative braking function reduces operating energy costs and the heat generated inside the drive electronics, extends the life of the robot, and reduces the load brought by production, thus realizing a more energy-efficient injection molding robot. In addition, the integrated bus design simplifies power distribution, reduces wiring complexity, and allows users to easily expand it to other axes or peripheral auxiliary equipment.

Servo automatic shutdown, reducing standby power consumption
To further optimize efficiency, the servo-driven 3-axis robot is equipped with a servo automatic shutdown function, which automatically cuts off the power supply to the servo motor during long periods of idleness without manual intervention. In standby mode, the servo drive senses that the motor has stopped running and automatically cuts off the power supply to the motor, eliminating the load. This feature alone can save up to 10% of electricity in a typical production shift, especially when operators frequently shut down equipment in a high-variety injection molding production environment. The extremely low delay in restarting the servo motor ensures the 3-axis robot can resume high-speed operation almost immediately, thereby maintaining fast cycle response capabilities.
Faster response time and energy saving
3-axis robots in injection molding under servo drive can combine precision, repeatability, and power with advanced control and energy savings. Under the Topstar 5-in-1 servo drive, 750 W power per axis, common bus energy recovery, and servo automatic shutdown function can greatly shorten cycle time, reduce scrap, reduce energy consumption, and improve production flexibility.
TRENDING POSTS
- What factors can cause delays in the injection molding process of plastic molding machine? 2025/05/19
- Exhibition Review| Topstar participates in InterPlas Thailand 2024 2025/05/19
- Star Case | Topstar helps Santong upgrade its intelligent plant 2025/05/19
- Topstar Special | National Science and Technology Workers Day 2025/05/19
HOT TOPIC
- .ervo motor-driven linear robots
- 1.0 guangdong topstar technology co. ltd
- 1.0 topstar china
- 1.0 topstar robot
- 11
- 2
- 21
- 23
- 3 axis robot
- 3 axis robots
- 3 in 1 Compact Dehumidifying Dryer
- 3-axis robot
- 3-axis robots
- 39
- 41
- 5-axis CNC machine
- 62
- accuracy
- Air Chillers
- all electric injection molding machine
- all electric injection molding machines
- All-electric injection molding machines
- and overall production quality. Therefore
- AP-RubberPlas
- automated injection molding machine
- Automation changed engineering
- automation of injection molding robots
- automotive parts injection molding
- auxiliary machine
- Bench Injection Molding Machine
- Cabinet dryer manufacturers
- Cabinet dryers
- chiller
- CNC Drilling Machine
- CNC Drilling Machines
- cnc engraving machine manufacturer
- cnc laser cutting machine manufacturer
- CNC machine
- CNC Machine Center
- CNC Machine for Sale
- CNC Machine Manufacturing
- CNC Machine Tool
- CNC machine tool product
- CNC Machining Center
- CNC wood carving machine
- Cooling system
- Cross-Walking Single Axis Servo Cylinder Robot
- Cross-Walking Single-Axis Servo Cylinder Robot
- Cross-Walking Three-Axis/Five-Axis Servo Driven Robot
- cross-walking three-axis/five-axis servo-driven robot
- Dehumidifier Dryer
- Dehumidifying Dryer
- delta parallel robot
- Desktop Injection Molding Machine
- Desktop injection molding machines
- Desktop Molding Machine
- desktop plastic injection machine
- Desktop Plastic Injection Molding Machine
- direct clamp injection molding machine
- Direct clamp injection molding machines
- Dosing & mixing system
- Drilling Centers
- Drying and dehumidification system
- drying and dehumidifying equipment
- Drying and Dehumidifying System
- drying system
- effective and efficient. Cabinet dryers are also used in other industries where large quantities of material need to be dried
- efficient injection molding machine
- elbow hydraulic injection molding machines
- electric injection molding machine
- electric injection molding machines
- energy-efficient injection molding robot
- energy-efficient water chiller
- energy-efficient water chillers
- energy-saving injection molding machine
- etc. Among injection molding robots
- exhibition
- features of CNC machine
- Feeding And Conveying System
- Five Axis Machine Center
- Fully automatic injection molding machine
- Gathering Topstar
- giant injection molding machine
- GMU-600 5-Axis Machining Center
- Granulating & Recycling System
- Heavy duty injection molding machine
- High-precision electric molding machines
- high-precision plastic molding machines
- high-speed all electric injection molding machine
- high-speed electric injection molding machine
- High-Speed Packaging Injection Molding
- Honeycomb rotor dehumidifier
- horizontal injection molding machine
- Horizontal Injection Molding Machines
- Horizontal Injection Moulding Machine
- Horizontal Mixer manufacturer
- How The CNC Machine Works
- hybrid injection molding machine
- hydraulic injection molding machine
- Hydraulic Injection Molding Machines
- in this article
- Industrial robot
- Industrial Robot Chinese brand
- industrial robot parts
- industrial robot supplier
- Industrial robots
- Industry Chain
- Injection Manipulator
- injection manipulator robot
- injection mold machines
- Injection molding
- Injection molding automation
- Injection Molding Automation Solution
- injection molding dryer
- Injection molding equipment
- injection molding hopper dryer
- Injection molding machine
- injection molding machine brand
- Injection Molding Machine Factory
- Injection Molding Machine Manufacture
- Injection molding machine manufacturer
- injection molding machine manufacturers
- Injection molding machine procurement
- injection molding machine robotic arm
- injection molding machine with a robot
- Injection molding machines
- injection molding material dehumidifying
- injection molding plant
- injection molding process
- Injection Molding Robot
- injection molding robot arm
- Injection molding robot automation
- Injection molding robotic arm
- injection molding robots
- Injection moulding machine
- injection moulding machines
- Injection Moulding Robots
- Injection Robot
- Injection robot arm
- Injection robot manufacturer
- Injection robot wholesale
- injection robots
- intelligent injection molding machines
- intelligent mold temperature
- intelligent mold temperature controller
- Intelligent mould temperature controller
- Introducing Injection Robot
- It is the best choice for drying large quantities of material at once. Cabinetmakers use these machines because they are fast
- Large flow water type mold temperature controller
- large injection molding machine
- large injection molding machines
- Learn what industrial automation and robotics is
- linear robot
- linear robots
- low speed sound-proof granulator
- machine plastic molding
- make sure to add some! Improvements (2) Keyphrase in introduction: Your keyphrase or its synonyms appear in the first paragraph of the copy
- manipulator machine
- manufacturing
- medical grade injection molding machines
- medical injection molding machine
- medical injection molding machines
- micro injection molding machine
- middle speed granulator
- Mini CNC machine manufacturers.
- Mold Temperature Control System
- mold temperature controller
- mold temperature controllers
- molding material Dehumidifying System
- mould temperature control system
- mould temperature controller
- mould temperature controllers
- New electric injection molding machine
- nitrogen dryer manufacturer
- nitrogen dryer system manufacturer
- Oil type mold temperature controller
- Oil type mold temperature controllers
- open day
- optical component injection molding
- Outbound links: No outbound links appear in this page. Add some! Images: No images appear on this page. Add some! Internal links: No internal links appear in this page
- PET Preform injection molding
- phone case maker machine
- phone case making machine
- phone cover making machine
- plastic bottle making machine
- plastic bottle manufacturing
- plastic bucket making machine
- plastic bucket manufacturing
- Plastic chair making machine
- plastic forming equipment
- plastic hopper dryer
- plastic injection machine
- plastic injection machines
- plastic injection molding
- Plastic injection molding equipment
- Plastic injection molding machine
- Plastic Injection Molding Machines
- plastic injection moulding machine
- plastic injection moulding machines
- plastic injection robot
- plastic molding
- Plastic Molding machine
- plastic molding machine 1
- Plastic Molding Machines
- plastic molding press
- plastic moulding machine
- plastic phone case making machine
- plastic-molding machine
- powerful granulator
- Powerful Type Sound-Proof Granulator
- precision injection molding
- precision injection molding machines
- production of plastic seats
- pure water mould temperature controller
- Robot injection molding
- robot injection molding machine
- robot manufacturing companies
- Robotic arm for injection molding machine
- robotic injection molding machines
- robotics in injection molding
- SCARA robot
- SCARA robots
- Service-oriented manufacturing
- Servo Cylinder Robot
- servo driven robot
- Servo Driven Robots
- servo injection molding machine
- servo injection robots
- servo motor-driven linear robots
- servo-driven 3-axis robot
- Servo-Driven Robot
- Setup of injection machine
- Silicone Injection Molding Machine
- six-axis industrial robot
- Stainless Hopper Dryer
- Stainless Hopper Dryers
- star club
- swing arm robot
- take-out robot
- take-out robots
- the choice between servo-driven robots and hydraulic robots will have a certain impact on efficiency
- the most popular injection molding machine
- the type of injection molding robot
- TMII injection molding machine
- toggle clamp injection molding machine
- Toggle Hydraulic Injection Molding Machines
- toggle injection molding machine
- Top 10 brands of injection robots
- Topstar
- Topstar Engineering
- Topstar Industrial Robots
- Topstar injection molding intelligent
- Topstar Scara Robots
- Useful Injection molding machine
- Vertical machining centers
- volumetric type blender
- water chiller
- water chillers
- water distributor
- water type mold temperature controller
- Water Type MoldTemperature Controller
- Water-Type Mould Temperature Controllers
- We often face choices when performing injection molding. We will choose the type of injection molding machine
- wholesale of injection molding machines
- x carve CNC
- 热门查询 点击次数 展示 排名 topstar