Do you want the best tips and tricks for 5-axis CNC machines in 2022?
2022/03/24 By Topstar
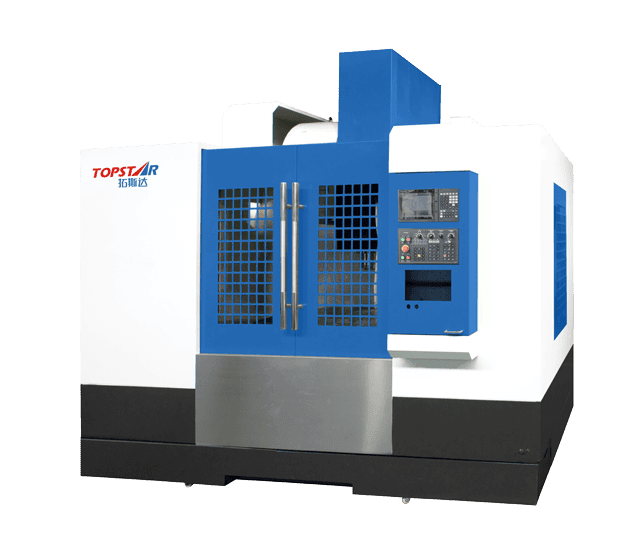
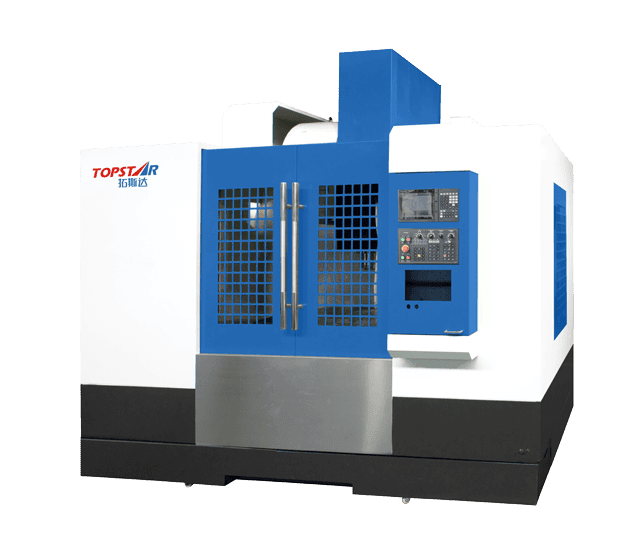
In the hardware processing manufacturing industry, 5-axis CNC machine tools can move along five axes simultaneously to complete complex cutting and forming tasks. However, mastering the operation of a 5-axis CNC machine requires a detailed understanding of its basic structure, operating skills, and details of control. In this blog post, I share the basic structure of 5-axis CNC machines and tips and tricks on better operating them for optimal performance and efficiency.
The basic structure of a 5-axis CNC milling machine
Simply put, a 5-axis CNC machine tool’s basic structure comprises multiple components, including the bed, five motion axes, spindle, tool changer, control system, etc.
Its bed is usually made of cast iron or welded steel, which provides stability and rigidity to support the entire structure while absorbing vibrations during machining operations. The five motion axes equipped are responsible for movement in different directions:
X-axis: Horizontal movement from left to right.
Y-axis: Horizontal movement from front to back.
Z axis: vertical up and down movement.
A-axis: rotate around the X-axis.
B axis: Rotate around the Y axis.
These axes cooperate with each other to enable the machine to approach the workpiece at any angle and direction to perform complex machining operations.
In a 5-axis CNC machine tool, a multi-axis or rotary head mounts the spindle, allowing it to simultaneously move and orient relative to the workpiece along multiple axes. Also, 5-axis CNC machines often have automatic tool changers (ATC) that accommodate multiple cutting tools in a carousel or tool magazine. The entire 5-axis machine tool’s control system consists of a CNC unit and software that converts digital instructions into precise movements of the machine tool’s axes. Workpiece holding system: To secure the workpiece during machining, a workpiece holding system, such as a vise, clamp, or fixture, is also used to prevent the quality of the part from being affected or deformed.
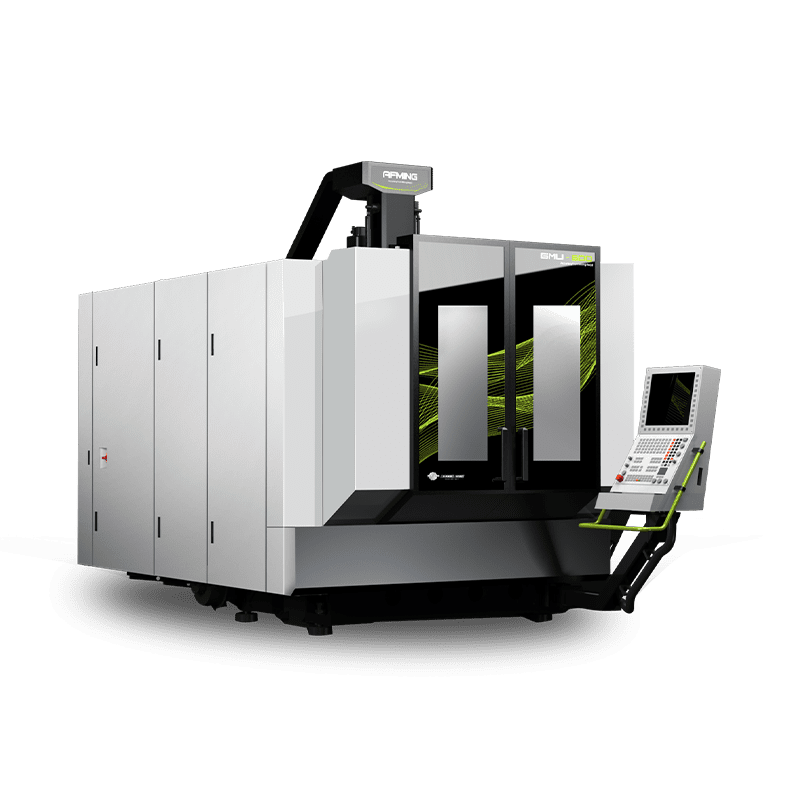
Movements on a 5-axis CNC machine
The motion of a 5-axis CNC machine is similar to that of a traditional 3-axis CNC machine, with two additional axes (called the A and B axes) performing rotational motion in addition to movement along the X, Y, and Z directions. This allows the cutting tool to approach the part from different angles and directions, expanding the range of processing. What really makes it stand out is the ability to perform combined linear and rotational motion along multiple axes simultaneously, enabling complex 3D machining operations.
What is the default in a 5-axis CNC machine?
After understanding the basic structure and motion of a 5-axis CNC machine tool, you need to know its default configuration, including the orientation of each axis relative to the workpiece and cutting tool. This orientation determines each axis’s direction and range of motion during the machining operation. For example, the A and B axes can be positioned perpendicular to each other, allowing simultaneous rotation about the X and Y axes respectively. Another default configuration is to ensure adequate tool clearance and workspace around the workpiece. Check to position machine components, such as spindle heads and rotary axes, to avoid collisions with workpieces or fixtures during machining operations.
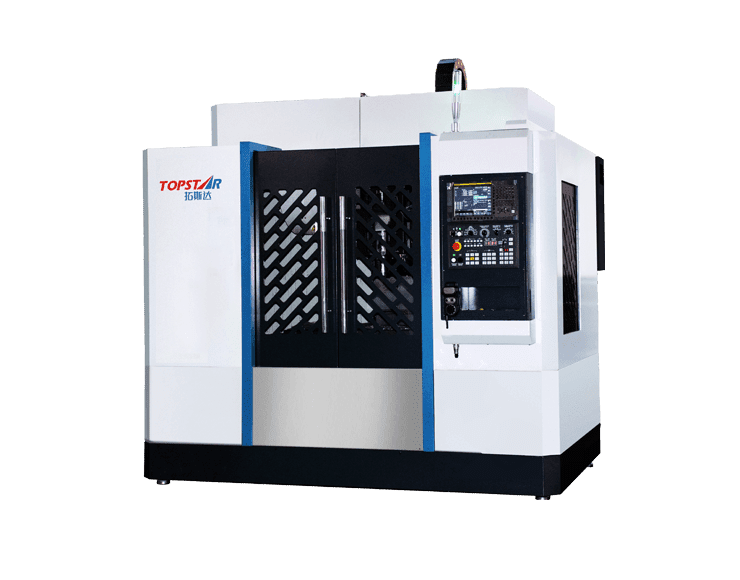
Better machined surface quality
To ensure the accuracy and precision of machined parts, users can take advantage of optical precision measurement systems integrated directly into 5-axis CNC machines. These systems utilize advanced imaging technology, such as laser scanners or optical sensors, to perform real-time measurement and feedback control during machining operations. Users can achieve tighter tolerances and higher-quality surface finishes by continuously monitoring and adjusting machining parameters based on optical measurements.
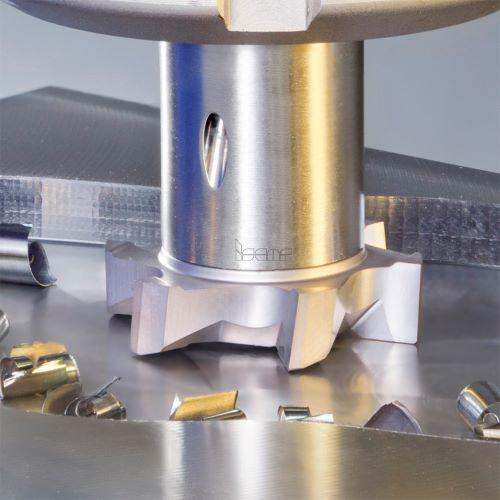
Improve processing performance
Before machining a part, be very familiar with the material’s properties, such as hardness, toughness, and machinability, as different materials require different cutting speeds, feed rates, and tool geometries for optimal machining performance. Then choose the correct cutting tool for them, including tool material, coating, geometry, and setting cutting-related parameters. While processing, adjust the cutting speed and feed rate parameters as appropriate, to reduce the processing cycle time and improve the surface finish and processing performance.
Use the best techniques to get the best product
5-axis CNC machine tools have better flexibility, accuracy, and efficiency in machining than 3-axis CNC machine tools. Before you officially start processing, you can refer to the best tips and tricks mentioned in the article, and make full use of the machine tool’s capabilities based on understanding its structure to create higher surface finish quality and accuracy and smaller error sizes.
TRENDING POSTS
- What factors can cause delays in the injection molding process of plastic molding machine? 2022/03/24
- Exhibition Review| Topstar participates in InterPlas Thailand 2024 2022/03/24
- Star Case | Topstar helps Santong upgrade its intelligent plant 2022/03/24
- Topstar Special | National Science and Technology Workers Day 2022/03/24
HOT TOPIC
- .ervo motor-driven linear robots
- 3 axis robot
- 3 axis robots
- 3 in 1 Compact Dehumidifying Dryer
- 3-axis robot
- 3-axis robots
- 5-axis CNC machine
- accuracy
- Air Chillers
- all electric injection molding machine
- all electric injection molding machines
- All-electric injection molding machines
- and overall production quality. Therefore
- AP-RubberPlas
- automated injection molding machine
- Automation changed engineering
- automation of injection molding robots
- auxiliary machine
- Bench Injection Molding Machine
- Cabinet dryer manufacturers
- Cabinet dryers
- chiller
- CNC Drilling Machine
- CNC Drilling Machines
- cnc engraving machine manufacturer
- cnc laser cutting machine manufacturer
- CNC machine
- CNC Machine Center
- CNC Machine for Sale
- CNC Machine Manufacturing
- CNC Machine Tool
- CNC machine tool product
- CNC Machining Center
- CNC wood carving machine
- Cooling system
- Cross-Walking Single Axis Servo Cylinder Robot
- Cross-Walking Single-Axis Servo Cylinder Robot
- Cross-Walking Three-Axis/Five-Axis Servo Driven Robot
- cross-walking three-axis/five-axis servo-driven robot
- Dehumidifier Dryer
- Dehumidifying Dryer
- delta parallel robot
- Desktop Injection Molding Machine
- Desktop injection molding machines
- Desktop Molding Machine
- desktop plastic injection machine
- Desktop Plastic Injection Molding Machine
- direct clamp injection molding machine
- Direct clamp injection molding machines
- Dosing & mixing system
- Drilling Centers
- Drying and dehumidification system
- drying and dehumidifying equipment
- Drying and Dehumidifying System
- drying system
- effective and efficient. Cabinet dryers are also used in other industries where large quantities of material need to be dried
- efficient injection molding machine
- elbow hydraulic injection molding machines
- electric injection molding machine
- electric injection molding machines
- energy-efficient injection molding robot
- energy-saving injection molding machine
- etc. Among injection molding robots
- exhibition
- features of CNC machine
- Feeding And Conveying System
- Five Axis Machine Center
- Fully automatic injection molding machine
- Gathering Topstar
- giant injection molding machine
- GMU-600 5-Axis Machining Center
- Granulating & Recycling System
- Heavy duty injection molding machine
- High-precision electric molding machines
- high-precision plastic molding machines
- high-speed all electric injection molding machine
- Honeycomb rotor dehumidifier
- horizontal injection molding machine
- Horizontal Injection Molding Machines
- Horizontal Injection Moulding Machine
- Horizontal Mixer manufacturer
- How The CNC Machine Works
- hybrid injection molding machine
- hydraulic injection molding machine
- Hydraulic Injection Molding Machines
- in this article
- Industrial robot
- Industrial Robot Chinese brand
- industrial robot parts
- industrial robot supplier
- Industrial robots
- Industry Chain
- Injection Manipulator
- injection manipulator robot
- injection mold machines
- Injection molding
- Injection molding automation
- Injection Molding Automation Solution
- injection molding dryer
- Injection molding equipment
- injection molding hopper dryer
- Injection molding machine
- injection molding machine brand
- Injection Molding Machine Factory
- Injection Molding Machine Manufacture
- Injection molding machine manufacturer
- injection molding machine manufacturers
- Injection molding machine procurement
- injection molding machine robotic arm
- injection molding machine with a robot
- Injection molding machines
- injection molding material dehumidifying
- injection molding plant
- Injection Molding Robot
- injection molding robot arm
- Injection molding robot automation
- Injection molding robotic arm
- injection molding robots
- Injection moulding machine
- Injection Moulding Robots
- Injection Robot
- Injection robot arm
- Injection robot manufacturer
- Injection robot wholesale
- injection robots
- intelligent injection molding machines
- Introducing Injection Robot
- It is the best choice for drying large quantities of material at once. Cabinetmakers use these machines because they are fast
- large injection molding machine
- Learn what industrial automation and robotics is
- linear robot
- linear robots
- low speed sound-proof granulator
- machine plastic molding
- make sure to add some! Improvements (2) Keyphrase in introduction: Your keyphrase or its synonyms appear in the first paragraph of the copy
- manipulator machine
- manufacturing
- medical grade injection molding machines
- medical injection molding machine
- medical injection molding machines
- micro injection molding machine
- middle speed granulator
- Mini CNC machine manufacturers.
- Mold Temperature Control System
- mold temperature controller
- mold temperature controllers
- molding material Dehumidifying System
- mould temperature control system
- mould temperature controller
- mould temperature controllers
- New electric injection molding machine
- nitrogen dryer manufacturer
- nitrogen dryer system manufacturer
- Oil type mold temperature controller
- Oil type mold temperature controllers
- open day
- Outbound links: No outbound links appear in this page. Add some! Images: No images appear on this page. Add some! Internal links: No internal links appear in this page
- PET Preform injection molding
- phone case maker machine
- phone case making machine
- plastic bottle making machine
- plastic bottle manufacturing
- plastic bucket making machine
- plastic bucket manufacturing
- Plastic chair making machine
- plastic forming equipment
- plastic hopper dryer
- plastic injection machine
- plastic injection machines
- plastic injection molding
- Plastic injection molding equipment
- Plastic injection molding machine
- Plastic Injection Molding Machines
- plastic injection moulding machine
- plastic injection robot
- Plastic Molding machine
- Plastic Molding Machines
- plastic molding press
- plastic moulding machine
- plastic phone case making machine
- plastic-molding machine
- powerful granulator
- Powerful Type Sound-Proof Granulator
- precision injection molding
- precision injection molding machines
- production of plastic seats
- pure water mould temperature controller
- Robot injection molding
- robot injection molding machine
- robot manufacturing companies
- Robotic arm for injection molding machine
- robotic injection molding machines
- robotics in injection molding
- SCARA robot
- SCARA robots
- Service-oriented manufacturing
- Servo Cylinder Robot
- servo driven robot
- Servo Driven Robots
- servo injection robots
- servo motor-driven linear robots
- servo-driven 3-axis robot
- Servo-Driven Robot
- Setup of injection machine
- Silicone Injection Molding Machine
- six-axis industrial robot
- Stainless Hopper Dryer
- Stainless Hopper Dryers
- star club
- swing arm robot
- take-out robots
- the choice between servo-driven robots and hydraulic robots will have a certain impact on efficiency
- the most popular injection molding machine
- the type of injection molding robot
- toggle clamp injection molding machine
- Toggle Hydraulic Injection Molding Machines
- toggle injection molding machine
- Top 10 brands of injection robots
- Topstar
- Topstar Engineering
- Topstar Industrial Robots
- Topstar injection molding intelligent
- Topstar Scara Robots
- Useful Injection molding machine
- Vertical machining centers
- volumetric type blender
- water chiller
- water chillers
- water distributor
- water type mold temperature controller
- Water Type MoldTemperature Controller
- Water-Type Mould Temperature Controllers
- We often face choices when performing injection molding. We will choose the type of injection molding machine
- wholesale of injection molding machines
- x carve CNC