The importance of a 3 axis robot for injection molding in the high-speed packaging industry
2025/05/12 By Topstar
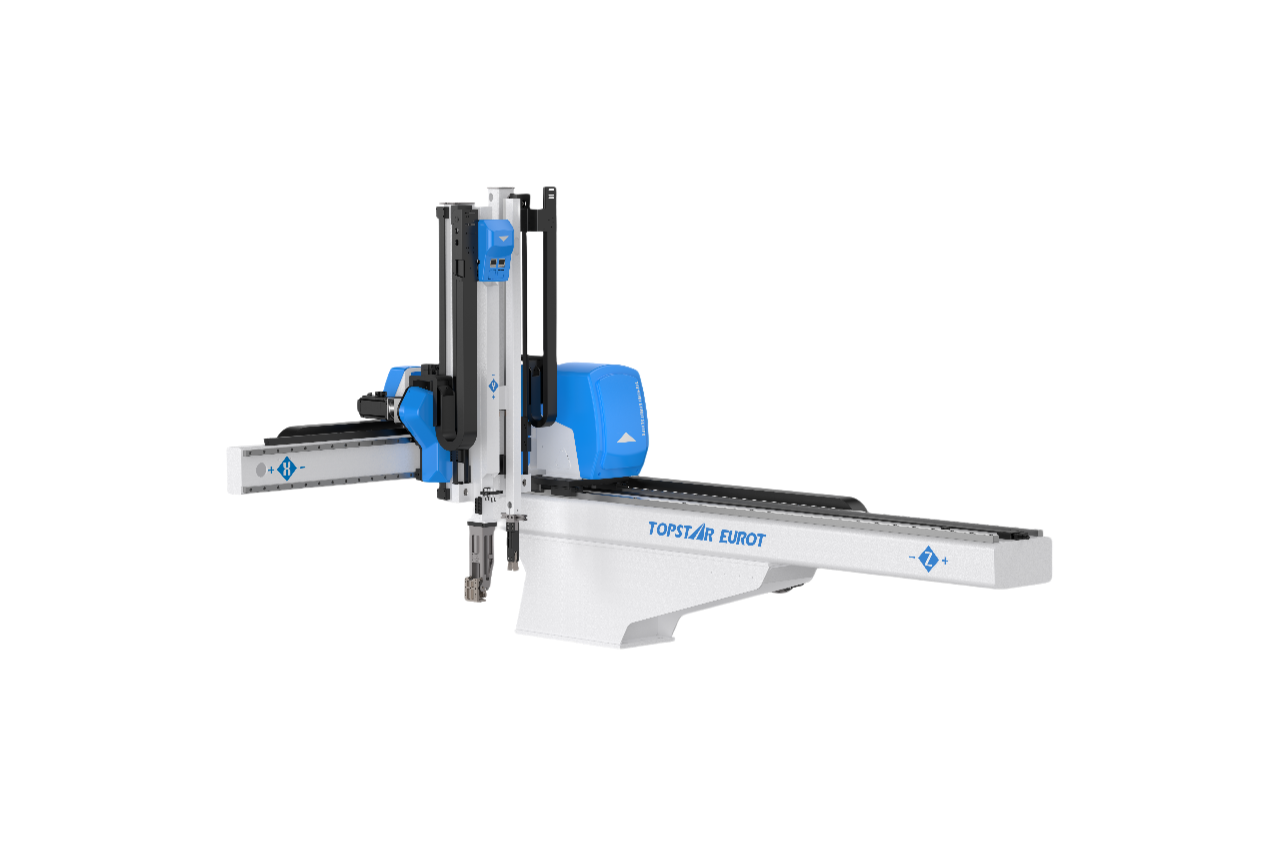
When facing the injection molding production of high-speed and surging industries such as the high-speed packaging industry, it is necessary to make our injection molding equipment capable of large-order production and efficient intelligence. In addition to the core injection molding machine, a 3 axis robot is also required and integrated with the injection molding machine to complete the injection molding. The high-speed packaging industry’s output per shift usually exceeds tens of thousands of parts. Topstar’s three-axis robot is built on a powerful open control system and a five-in-one servo drive to provide the speed and precision required for continuous production. The uninterrupted workflow is maintained by coordinating precise part removal, handling, and transfer tasks in sync with the injection cycle, significantly reducing cycle time and labor dependence.
Using 3 axis robot to achieve continuous production of injection molding
A significant advantage of 3 axis injection molding robots is that they can achieve continuous production. Clearing jams, changing molds, or adjusting part positions in high-speed packaging may lead to production interruptions and affect the final production delivery. Topstar tightly integrates its 3 axis robot with the injection molding machine’s control system. It can adjust its pick-and-place trajectory based on real-time signals from the two unified communication languages. This synchronization ensures that the three-axis robot can quickly remove the finished part after completing a cycle, place it on the conveyor or secondary operation, and return to its position for the next cycle without human intervention. Achieving a seamless, 24/7 production line that can handle many orders is critical for brands to scale up in response to market demand surges. In addition, built-in diagnostics monitor cycle variations to improve overall equipment efficiency.
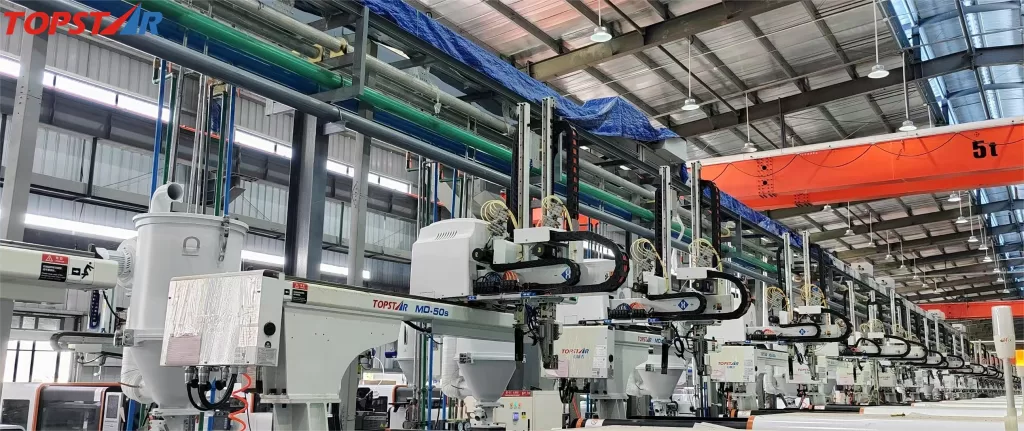
Unlocking multi-track applications for 3 axis robot
Beyond simple demolding, high-speed packaging and even some other high-speed molding applications require 3 axis robots to achieve multi-track applications to handle different part geometries and processes. Under the self-developed open system, users can write applications tasks such as pulling, undercutting, slips, diagonal lines, and even irregular removal paths. Specialized end-of-arm tools on the 3 axis robot can perform in-line arrangement, precise stacking, batch counting, and statistical sampling for quality control in a single unit. This flexibility enables a single automation workstation to accommodate multiple product lines, thereby reducing capital expenditures and factory footprint, while maintaining high accuracy and adaptability as packaging designs evolve, thereby reducing setup time and achieving seasonal order fluctuations.
Vibration suppression for high-precision molding
High-speed molding inevitably brings vibration problems, affecting part quality and triggering system alarms. The vibration suppression function integrated on the 3 axis robot can actively suppress vibration during rapid acceleration and deceleration. By analyzing the feedback from the high-resolution encoder and the 3 axis inertial measurement unit, the control system of the injection molding manipulator can modify the motion trajectory in real time, smooth the transition, and prevent resonance, thereby avoiding resonance that causes part misalignment, fixture wear, and even micro-cracks in precision parts. For the injection molding of precision packaging parts (such as thin milk tea cups and milk tea cup lids), the discount technology ensures excellent product consistency and reduces downtime caused by vibration alarms. In addition, reducing mechanical stress extends maintenance intervals, lowers the full life cycle service cost, and improves uptime for high-end, high-precision industries.
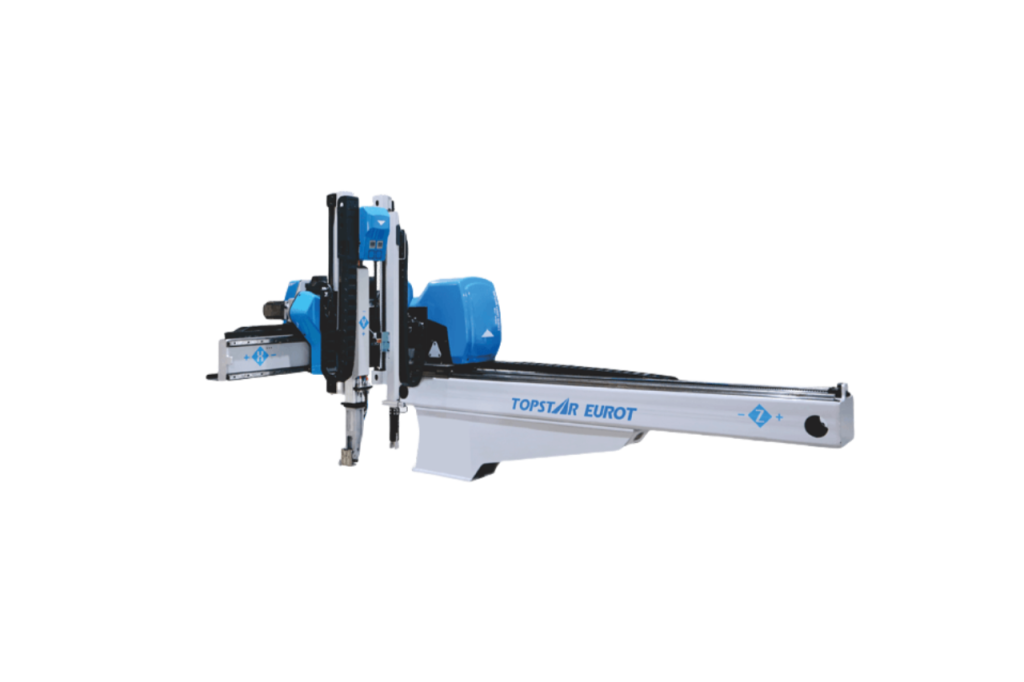
Servo drive and multi-axis standard bus design
Traditional linear robots or take-out robots usually use multiple dedicated drives, which cause problems such as equipment heating, complex wiring, and redundancy. Topstar’s 3 axis robot series adopts a five-in-one servo drive architecture, equipped with a multi-axis common bus, which can centrally distribute three-axis power. This design reduces electrical losses, reduces cable clutter, and supports regenerative braking, capturing kinetic energy during deceleration and returning it to the DC bus for reuse in subsequent acceleration phases. As a result, the system can be up to 20% more energy efficient, reducing the operating costs of production facilities. Combined with high-torque servo motors, the three-axis robot provides the dynamic performance required for fast injection molding cycles while maintaining a lean energy profile.
Special movements and high precision for packaging parts
The high-speed packaging industry often requires specialized post-molding operations directly in the molding cell. The 3 axis robot series supports various modular end-of-arm tools, such as heat staking for fixing inserts and in-line labeling for product identification, completing these tasks immediately after part ejection. The high-precision 3 axis robot maintains position repeatability within ±0.01 mm, ensuring it accurately places each packaging component for subsequent operations. For example, in milk tea cup production, a 3 axis robot can take out multiple cups, invert them to the rinsing station, stack them into crates, and then feed them into the filling line – all in the same cycle. This level of automation reduces cycle time and enhances quality control, resulting in a truly end-to-end automated high-speed packaging solution.
Improve efficiency in high-speed molding
The importance of 3 axis robots in the high-speed molding industry lies in their continuous production capacity, multi-track flexibility, vibration suppression, and energy-saving servo drive design, allowing manufacturers to meet seasonal order fluctuations and order surges while maintaining excellent quality and uptime. By integrating these linear robots into their molding lines, packaging companies can quickly scale up, ensure continuous production without interruption, and reduce the total cost of ownership.
TRENDING POSTS
- What factors can cause delays in the injection molding process of plastic molding machine? 2025/05/12
- Exhibition Review| Topstar participates in InterPlas Thailand 2024 2025/05/12
- Star Case | Topstar helps Santong upgrade its intelligent plant 2025/05/12
- Topstar Special | National Science and Technology Workers Day 2025/05/12
HOT TOPIC
- .ervo motor-driven linear robots
- 1.0 guangdong topstar technology co. ltd
- 1.0 topstar china
- 1.0 topstar robot
- 11
- 2
- 21
- 23
- 3 axis robot
- 3 axis robots
- 3 in 1 Compact Dehumidifying Dryer
- 3-axis robot
- 3-axis robots
- 39
- 41
- 5-axis CNC machine
- 62
- accuracy
- Air Chillers
- all electric injection molding machine
- all electric injection molding machines
- All-electric injection molding machines
- and overall production quality. Therefore
- AP-RubberPlas
- automated injection molding machine
- Automation changed engineering
- automation of injection molding robots
- auxiliary machine
- Bench Injection Molding Machine
- Cabinet dryer manufacturers
- Cabinet dryers
- chiller
- CNC Drilling Machine
- CNC Drilling Machines
- cnc engraving machine manufacturer
- cnc laser cutting machine manufacturer
- CNC machine
- CNC Machine Center
- CNC Machine for Sale
- CNC Machine Manufacturing
- CNC Machine Tool
- CNC machine tool product
- CNC Machining Center
- CNC wood carving machine
- Cooling system
- Cross-Walking Single Axis Servo Cylinder Robot
- Cross-Walking Single-Axis Servo Cylinder Robot
- Cross-Walking Three-Axis/Five-Axis Servo Driven Robot
- cross-walking three-axis/five-axis servo-driven robot
- Dehumidifier Dryer
- Dehumidifying Dryer
- delta parallel robot
- Desktop Injection Molding Machine
- Desktop injection molding machines
- Desktop Molding Machine
- desktop plastic injection machine
- Desktop Plastic Injection Molding Machine
- direct clamp injection molding machine
- Direct clamp injection molding machines
- Dosing & mixing system
- Drilling Centers
- Drying and dehumidification system
- drying and dehumidifying equipment
- Drying and Dehumidifying System
- drying system
- effective and efficient. Cabinet dryers are also used in other industries where large quantities of material need to be dried
- efficient injection molding machine
- elbow hydraulic injection molding machines
- electric injection molding machine
- electric injection molding machines
- energy-efficient injection molding robot
- energy-efficient water chiller
- energy-efficient water chillers
- energy-saving injection molding machine
- etc. Among injection molding robots
- exhibition
- features of CNC machine
- Feeding And Conveying System
- Five Axis Machine Center
- Fully automatic injection molding machine
- Gathering Topstar
- giant injection molding machine
- GMU-600 5-Axis Machining Center
- Granulating & Recycling System
- Heavy duty injection molding machine
- High-precision electric molding machines
- high-precision plastic molding machines
- high-speed all electric injection molding machine
- high-speed electric injection molding machine
- High-Speed Packaging Injection Molding
- Honeycomb rotor dehumidifier
- horizontal injection molding machine
- Horizontal Injection Molding Machines
- Horizontal Injection Moulding Machine
- Horizontal Mixer manufacturer
- How The CNC Machine Works
- hybrid injection molding machine
- hydraulic injection molding machine
- Hydraulic Injection Molding Machines
- in this article
- Industrial robot
- Industrial Robot Chinese brand
- industrial robot parts
- industrial robot supplier
- Industrial robots
- Industry Chain
- Injection Manipulator
- injection manipulator robot
- injection mold machines
- Injection molding
- Injection molding automation
- Injection Molding Automation Solution
- injection molding dryer
- Injection molding equipment
- injection molding hopper dryer
- Injection molding machine
- injection molding machine brand
- Injection Molding Machine Factory
- Injection Molding Machine Manufacture
- Injection molding machine manufacturer
- injection molding machine manufacturers
- Injection molding machine procurement
- injection molding machine robotic arm
- injection molding machine with a robot
- Injection molding machines
- injection molding material dehumidifying
- injection molding plant
- injection molding process
- Injection Molding Robot
- injection molding robot arm
- Injection molding robot automation
- Injection molding robotic arm
- injection molding robots
- Injection moulding machine
- injection moulding machines
- Injection Moulding Robots
- Injection Robot
- Injection robot arm
- Injection robot manufacturer
- Injection robot wholesale
- injection robots
- intelligent injection molding machines
- Intelligent mould temperature controller
- Introducing Injection Robot
- It is the best choice for drying large quantities of material at once. Cabinetmakers use these machines because they are fast
- Large flow water type mold temperature controller
- large injection molding machine
- large injection molding machines
- Learn what industrial automation and robotics is
- linear robot
- linear robots
- low speed sound-proof granulator
- machine plastic molding
- make sure to add some! Improvements (2) Keyphrase in introduction: Your keyphrase or its synonyms appear in the first paragraph of the copy
- manipulator machine
- manufacturing
- medical grade injection molding machines
- medical injection molding machine
- medical injection molding machines
- micro injection molding machine
- middle speed granulator
- Mini CNC machine manufacturers.
- Mold Temperature Control System
- mold temperature controller
- mold temperature controllers
- molding material Dehumidifying System
- mould temperature control system
- mould temperature controller
- mould temperature controllers
- New electric injection molding machine
- nitrogen dryer manufacturer
- nitrogen dryer system manufacturer
- Oil type mold temperature controller
- Oil type mold temperature controllers
- open day
- Outbound links: No outbound links appear in this page. Add some! Images: No images appear on this page. Add some! Internal links: No internal links appear in this page
- PET Preform injection molding
- phone case maker machine
- phone case making machine
- phone cover making machine
- plastic bottle making machine
- plastic bottle manufacturing
- plastic bucket making machine
- plastic bucket manufacturing
- Plastic chair making machine
- plastic forming equipment
- plastic hopper dryer
- plastic injection machine
- plastic injection machines
- plastic injection molding
- Plastic injection molding equipment
- Plastic injection molding machine
- Plastic Injection Molding Machines
- plastic injection moulding machine
- plastic injection moulding machines
- plastic injection robot
- plastic molding
- Plastic Molding machine
- Plastic Molding Machines
- plastic molding press
- plastic moulding machine
- plastic phone case making machine
- plastic-molding machine
- powerful granulator
- Powerful Type Sound-Proof Granulator
- precision injection molding
- precision injection molding machines
- production of plastic seats
- pure water mould temperature controller
- Robot injection molding
- robot injection molding machine
- robot manufacturing companies
- Robotic arm for injection molding machine
- robotic injection molding machines
- robotics in injection molding
- SCARA robot
- SCARA robots
- Service-oriented manufacturing
- Servo Cylinder Robot
- servo driven robot
- Servo Driven Robots
- servo injection molding machine
- servo injection robots
- servo motor-driven linear robots
- servo-driven 3-axis robot
- Servo-Driven Robot
- Setup of injection machine
- Silicone Injection Molding Machine
- six-axis industrial robot
- Stainless Hopper Dryer
- Stainless Hopper Dryers
- star club
- swing arm robot
- take-out robot
- take-out robots
- the choice between servo-driven robots and hydraulic robots will have a certain impact on efficiency
- the most popular injection molding machine
- the type of injection molding robot
- TMII injection molding machine
- toggle clamp injection molding machine
- Toggle Hydraulic Injection Molding Machines
- toggle injection molding machine
- Top 10 brands of injection robots
- Topstar
- Topstar Engineering
- Topstar Industrial Robots
- Topstar injection molding intelligent
- Topstar Scara Robots
- Useful Injection molding machine
- Vertical machining centers
- volumetric type blender
- water chiller
- water chillers
- water distributor
- water type mold temperature controller
- Water Type MoldTemperature Controller
- Water-Type Mould Temperature Controllers
- We often face choices when performing injection molding. We will choose the type of injection molding machine
- wholesale of injection molding machines
- x carve CNC
- 热门查询 点击次数 展示 排名 topstar