Solve the problems of ejection failure and mold sticking of hydraulic injection molding machine
2025/05/21 By Topstar
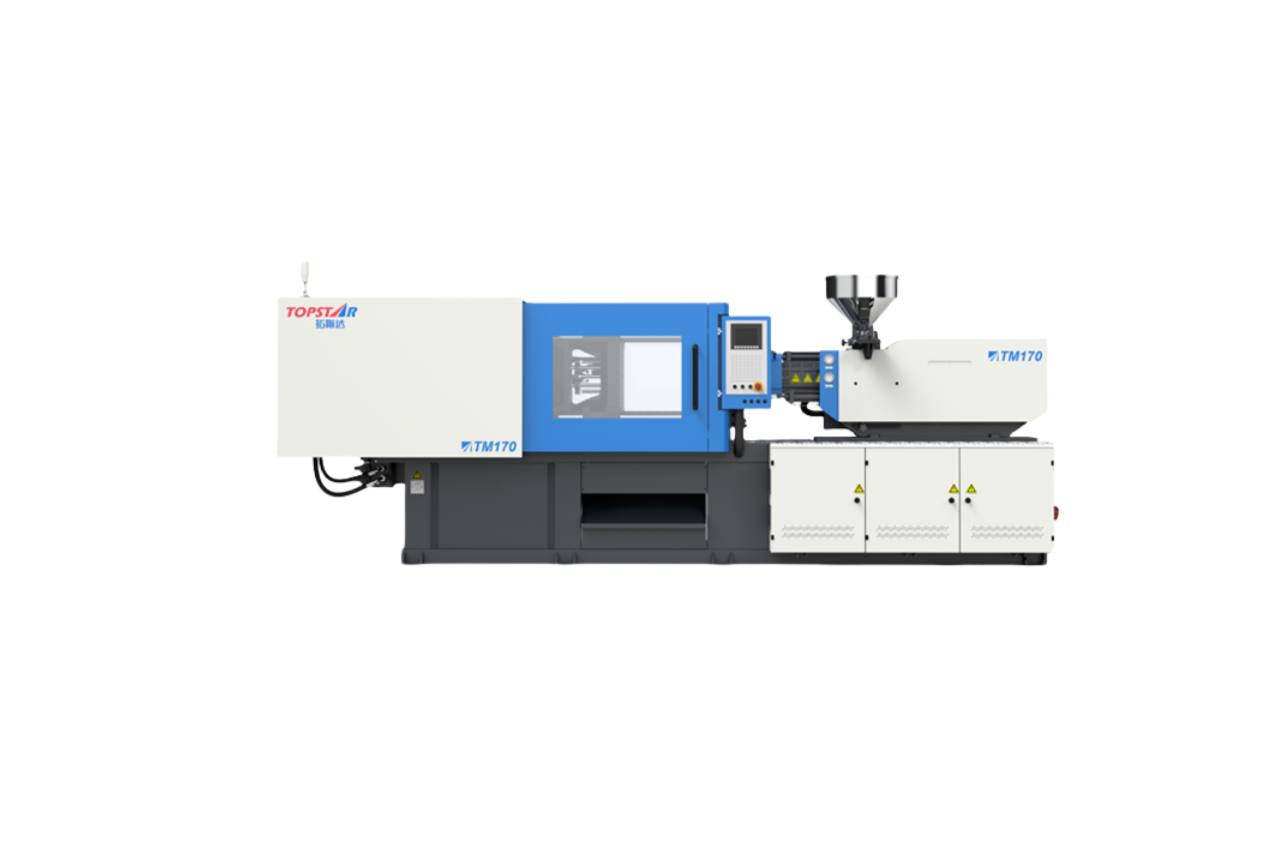
Ejector failure and mold sticking are common problems when using hydraulic injection molding machines, which often lead to production downtime, manual part removal, and increased material waste. And these problems are particularly serious in South American manufacturing environments, where high humidity and temperature changes can exacerbate resin adhesion to the mold surface. The main reasons include insufficient ejector force, poor mold opening stroke, large temperature differences in the mold, and uneven clamping pressure. Topstar will comprehensively solve this problem by combining the causes of the problem and leveraging the advantages of the hydraulic injection molding machine.
Enhanced hydraulic injection molding machine ejector thrust for reliable demolding
One of the most common causes of hydraulic injection molding machine ejector failure is insufficient ejector force, causing the molded part to stick to the core or cavity surface. To solve this problem, Topstar’s hydraulic injection molding machine will increase the ejector thrust by 20%, using a large-capacity ejector cylinder driven by an oversized piston and reinforced seals to achieve consistent, repeatable, and powerful ejector force. The upgraded ejector assembly contains hardened steel rails and precision linear guides to minimize friction and deflection under load, ensuring that the mold ejector plate moves at a perfect angle. This improvement is particularly beneficial when working with high-shrinkage materials, such as nylon or glass-filled polymers, which are common in the automotive sector and electronics manufacturing. The result is cleaner part demolding, fewer mold interventions, and significantly reduced scrap and downtime.
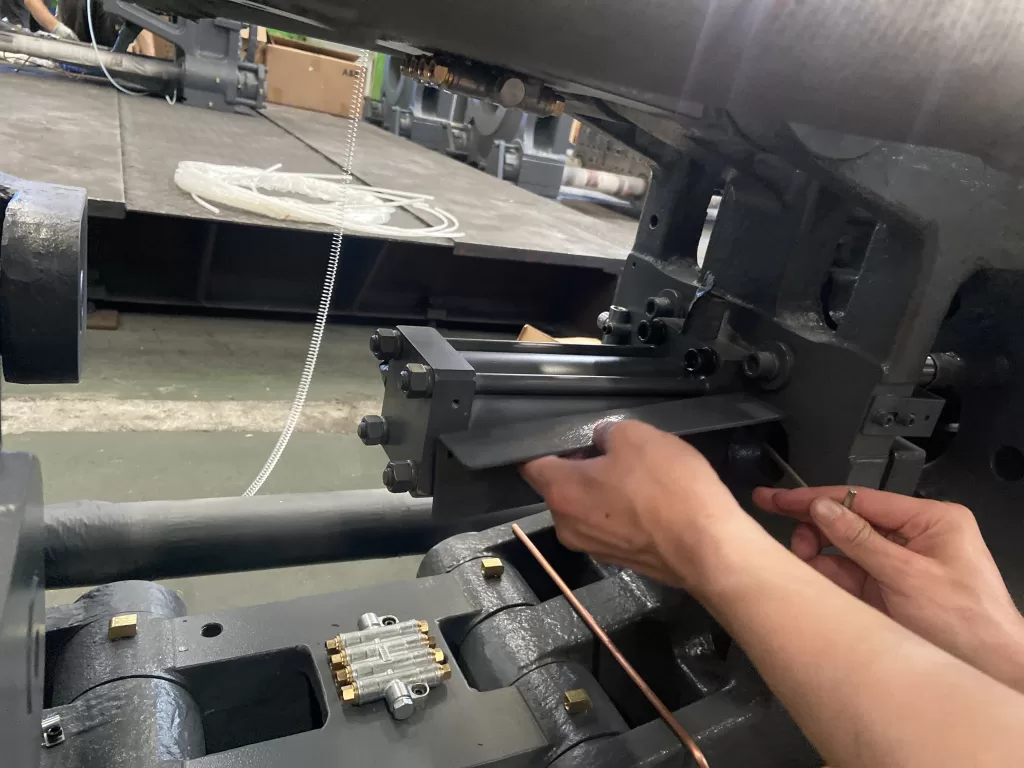
Extra-long stroke opening accuracy for the hydraulic injection molding machine
Reliable part demolding also depends on the mold opening completely and accurately to prevent part ejection and residual clamping. With extra-long mold opening strokes, Topstar’s hydraulic injection molding machines can easily handle even the largest and most complex multi-cavity molds, ensuring mold opening position accuracy within ±1 mm. At the same time, high-response proportional valves regulate the hydraulic flow to the tie rod cylinders for smooth, vibration-free movement. This extended mold opening stroke ensures that the part has ample space to drop by gravity or be picked up by an injection robot, reducing the risk of damage. Fast, controlled mold movement reduces cycle times because the system avoids the dwell time required by traditional hydraulic units, thereby increasing overall output.
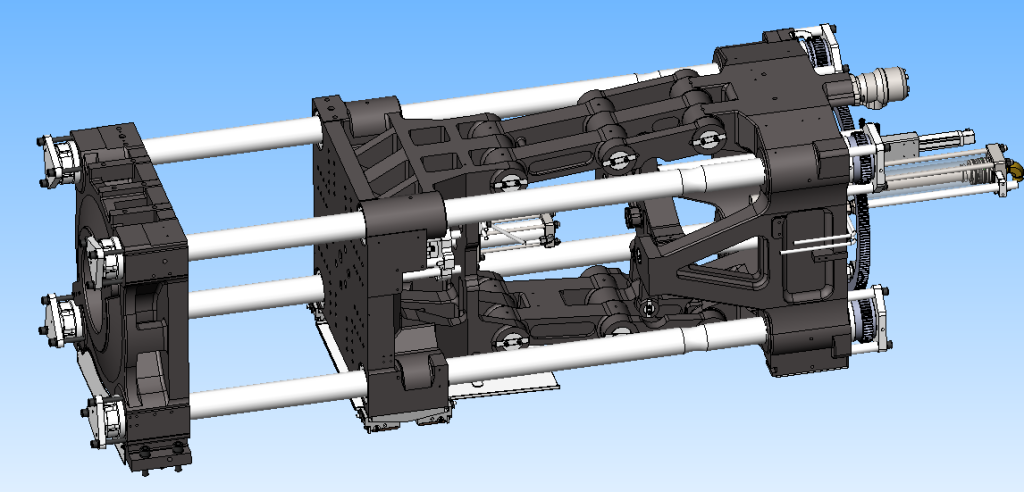
Angled five-point tether design for greater stability
The angled five-point tether design maintains platen parallelism at maximum clamping force, which avoids uneven cavity pressure that causes sticking. Hydraulic injection molding machines use an angled five-point tether design that combines angled links and spherical bearings into a compact, highly rigid frame. This configuration provides excellent load-bearing capacity and evenly distributes clamping pressure across the mold surface, maintaining parallelism within 0.05 mm. The compact linkage minimizes deflection and optimizes space efficiency on the factory floor. In addition, high-strength steel platens and sturdy tie rods resist bending under cyclic loads, maintaining long-term alignment. This structural integrity makes it easier and ensures efficient generation of large-volume production.
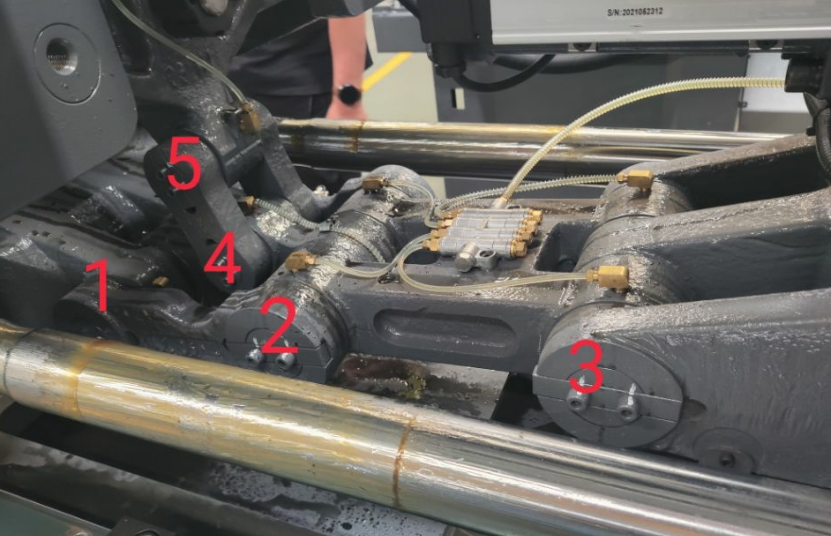
Fast, stable platen movement for increased throughput
High-speed mold opening and closing without overshoot or vibration maintains hydraulic injection molding machines’ cycle time and part quality. Topstar solves this problem by using high-flow proportional servo valves to control the clamping and injection circuits, combined with large-diameter tie rod cylinders for fast platen acceleration. Oil accumulators complement these valves, providing instant hydraulic oil during the acceleration phase to meet peak demands and ensure smooth deceleration. The result is a mold opening and closing time of less than 1.2 seconds and minimized mechanical shocks that could cause part deformation or mis-ejection. This ensures high throughput production, reduces wear on injection molding machine components, and improves part consistency in every cycle by providing consistent, controlled platen movement.
Thermal and mold maintenance considerations
Even with optimized mechanical structures, mold sticking can occur if mold temperature control and maintenance programs are inadequate. Topstar’s hydraulic injection molding machines integrate seamless interfaces with mold temperature controllers to precisely regulate cooling circuits and maintain constant cavity temperatures. At the same time, thermocouples embedded near critical areas provide real-time feedback to the machine to adjust process parameters to eliminate cold spots and reduce resin sticking. In addition, the system features an automatic lubrication program for guide rails and ejector components that is scheduled according to cycle times to maintain smooth operation. These maintenance alerts, combined with modular hydraulic power units, allow technicians to quickly make repairs without extended downtime, ensuring that the entire line in injection molding can be maintained in optimal condition and virtually eliminating mold sticking incidents.
Ensure consistent demolding performance
From the 20% increase in ejector thrust, the ultra-long mold opening stroke with an accuracy of up to ±1 mm, to the stability of the inclined five-point machine twist design, and the high-speed servo-driven platen movement, the hydraulic injection molding machine works together to provide consistent demolding reliability. For South American plastics manufacturers facing strict production targets and quality requirements, Topstar’s hydraulic injection molding machines can minimize scrap, reduce manual intervention, and maintain high production.
TRENDING POSTS
- What factors can cause delays in the injection molding process of plastic molding machine? 2025/05/21
- Exhibition Review| Topstar participates in InterPlas Thailand 2024 2025/05/21
- Star Case | Topstar helps Santong upgrade its intelligent plant 2025/05/21
- Topstar Special | National Science and Technology Workers Day 2025/05/21
HOT TOPIC
- .ervo motor-driven linear robots
- 3 axis robot
- 3 axis robots
- 3 in 1 Compact Dehumidifying Dryer
- 3-axis robot
- 3-axis robots
- 5-axis CNC machine
- accuracy
- Air Chillers
- all electric injection molding machine
- all electric injection molding machines
- All-electric injection molding machines
- and overall production quality. Therefore
- AP-RubberPlas
- automated injection molding machine
- Automation changed engineering
- automation of injection molding robots
- auxiliary machine
- Bench Injection Molding Machine
- Cabinet dryer manufacturers
- Cabinet dryers
- chiller
- CNC Drilling Machine
- CNC Drilling Machines
- cnc engraving machine manufacturer
- cnc laser cutting machine manufacturer
- CNC machine
- CNC Machine Center
- CNC Machine for Sale
- CNC Machine Manufacturing
- CNC Machine Tool
- CNC machine tool product
- CNC Machining Center
- CNC wood carving machine
- Cooling system
- Cross-Walking Single Axis Servo Cylinder Robot
- Cross-Walking Single-Axis Servo Cylinder Robot
- Cross-Walking Three-Axis/Five-Axis Servo Driven Robot
- cross-walking three-axis/five-axis servo-driven robot
- Dehumidifier Dryer
- Dehumidifying Dryer
- delta parallel robot
- Desktop Injection Molding Machine
- Desktop injection molding machines
- Desktop Molding Machine
- desktop plastic injection machine
- Desktop Plastic Injection Molding Machine
- direct clamp injection molding machine
- Direct clamp injection molding machines
- Dosing & mixing system
- Drilling Centers
- Drying and dehumidification system
- drying and dehumidifying equipment
- Drying and Dehumidifying System
- drying system
- effective and efficient. Cabinet dryers are also used in other industries where large quantities of material need to be dried
- efficient injection molding machine
- elbow hydraulic injection molding machines
- electric injection molding machine
- electric injection molding machines
- energy-efficient injection molding robot
- energy-saving injection molding machine
- etc. Among injection molding robots
- exhibition
- features of CNC machine
- Feeding And Conveying System
- Five Axis Machine Center
- Fully automatic injection molding machine
- Gathering Topstar
- giant injection molding machine
- GMU-600 5-Axis Machining Center
- Granulating & Recycling System
- Heavy duty injection molding machine
- High-precision electric molding machines
- high-precision plastic molding machines
- high-speed all electric injection molding machine
- Honeycomb rotor dehumidifier
- horizontal injection molding machine
- Horizontal Injection Molding Machines
- Horizontal Injection Moulding Machine
- Horizontal Mixer manufacturer
- How The CNC Machine Works
- hybrid injection molding machine
- hydraulic injection molding machine
- Hydraulic Injection Molding Machines
- in this article
- Industrial robot
- Industrial Robot Chinese brand
- industrial robot parts
- industrial robot supplier
- Industrial robots
- Industry Chain
- Injection Manipulator
- injection manipulator robot
- injection mold machines
- Injection molding
- Injection molding automation
- Injection Molding Automation Solution
- injection molding dryer
- Injection molding equipment
- injection molding hopper dryer
- Injection molding machine
- injection molding machine brand
- Injection Molding Machine Factory
- Injection Molding Machine Manufacture
- Injection molding machine manufacturer
- injection molding machine manufacturers
- Injection molding machine procurement
- injection molding machine robotic arm
- injection molding machine with a robot
- Injection molding machines
- injection molding material dehumidifying
- injection molding plant
- Injection Molding Robot
- injection molding robot arm
- Injection molding robot automation
- Injection molding robotic arm
- injection molding robots
- Injection moulding machine
- Injection Moulding Robots
- Injection Robot
- Injection robot arm
- Injection robot manufacturer
- Injection robot wholesale
- injection robots
- intelligent injection molding machines
- Introducing Injection Robot
- It is the best choice for drying large quantities of material at once. Cabinetmakers use these machines because they are fast
- large injection molding machine
- large injection molding machines
- Learn what industrial automation and robotics is
- linear robot
- linear robots
- low speed sound-proof granulator
- machine plastic molding
- make sure to add some! Improvements (2) Keyphrase in introduction: Your keyphrase or its synonyms appear in the first paragraph of the copy
- manipulator machine
- manufacturing
- medical grade injection molding machines
- medical injection molding machine
- medical injection molding machines
- micro injection molding machine
- middle speed granulator
- Mini CNC machine manufacturers.
- Mold Temperature Control System
- mold temperature controller
- mold temperature controllers
- molding material Dehumidifying System
- mould temperature control system
- mould temperature controller
- mould temperature controllers
- New electric injection molding machine
- nitrogen dryer manufacturer
- nitrogen dryer system manufacturer
- Oil type mold temperature controller
- Oil type mold temperature controllers
- open day
- Outbound links: No outbound links appear in this page. Add some! Images: No images appear on this page. Add some! Internal links: No internal links appear in this page
- PET Preform injection molding
- phone case maker machine
- phone case making machine
- plastic bottle making machine
- plastic bottle manufacturing
- plastic bucket making machine
- plastic bucket manufacturing
- Plastic chair making machine
- plastic forming equipment
- plastic hopper dryer
- plastic injection machine
- plastic injection machines
- plastic injection molding
- Plastic injection molding equipment
- Plastic injection molding machine
- Plastic Injection Molding Machines
- plastic injection moulding machine
- plastic injection robot
- Plastic Molding machine
- Plastic Molding Machines
- plastic molding press
- plastic moulding machine
- plastic phone case making machine
- plastic-molding machine
- powerful granulator
- Powerful Type Sound-Proof Granulator
- precision injection molding
- precision injection molding machines
- production of plastic seats
- pure water mould temperature controller
- Robot injection molding
- robot injection molding machine
- robot manufacturing companies
- Robotic arm for injection molding machine
- robotic injection molding machines
- robotics in injection molding
- SCARA robot
- SCARA robots
- Service-oriented manufacturing
- Servo Cylinder Robot
- servo driven robot
- Servo Driven Robots
- servo injection robots
- servo motor-driven linear robots
- servo-driven 3-axis robot
- Servo-Driven Robot
- Setup of injection machine
- Silicone Injection Molding Machine
- six-axis industrial robot
- Stainless Hopper Dryer
- Stainless Hopper Dryers
- star club
- swing arm robot
- take-out robots
- the choice between servo-driven robots and hydraulic robots will have a certain impact on efficiency
- the most popular injection molding machine
- the type of injection molding robot
- toggle clamp injection molding machine
- Toggle Hydraulic Injection Molding Machines
- toggle injection molding machine
- Top 10 brands of injection robots
- Topstar
- Topstar Engineering
- Topstar Industrial Robots
- Topstar injection molding intelligent
- Topstar Scara Robots
- Useful Injection molding machine
- Vertical machining centers
- volumetric type blender
- water chiller
- water chillers
- water distributor
- water type mold temperature controller
- Water Type MoldTemperature Controller
- Water-Type Mould Temperature Controllers
- We often face choices when performing injection molding. We will choose the type of injection molding machine
- wholesale of injection molding machines
- x carve CNC