What kind of positioning accuracy can an all electric injection molding machine achieve?
2025/07/14 By Topstar
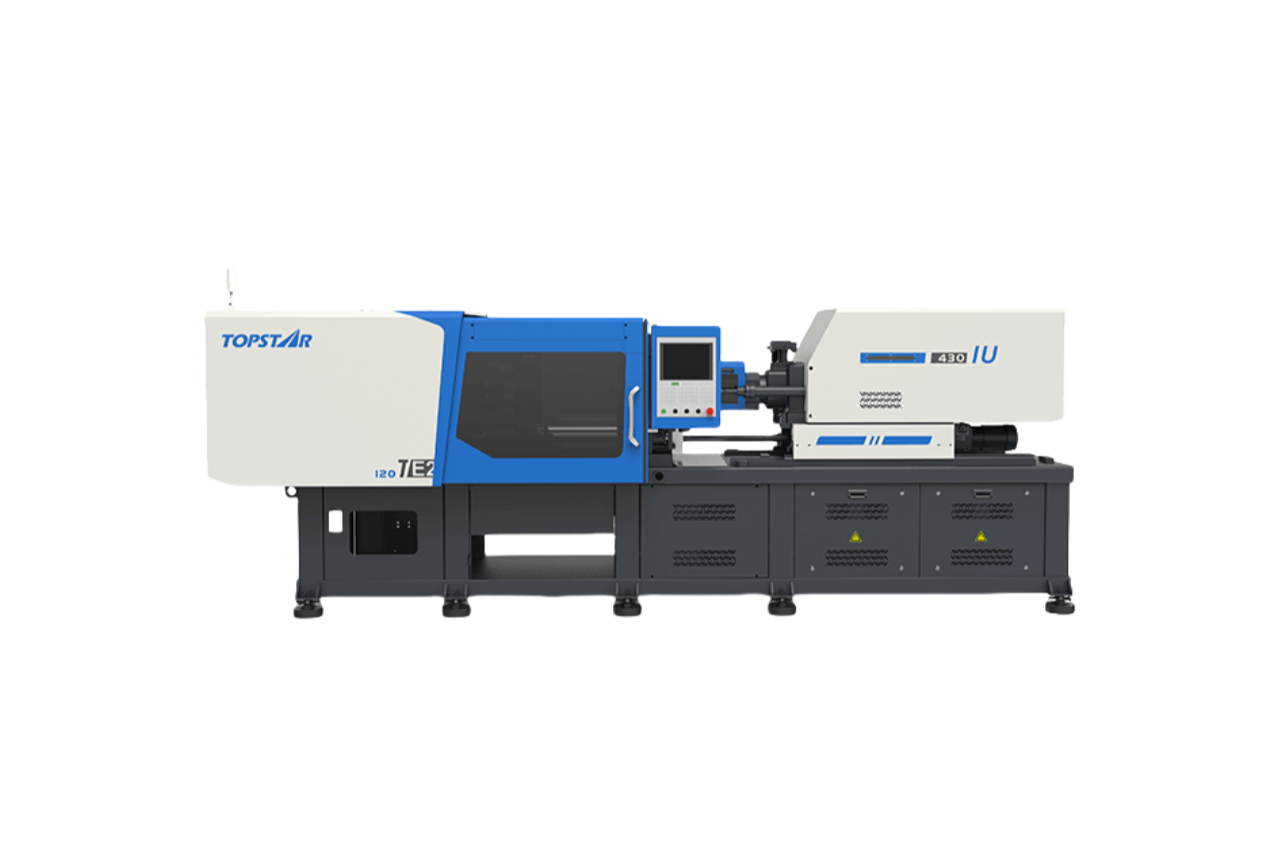
All electric injection molding machines are a more suitable solution for the injection molding of ultra-precision plastic parts. According to our customer feedback, electric drives can reduce position deviations by up to 40% compared to hydraulic systems under the same load. The intelligent servo drive architecture on the Topstar all electric injection molding machine reduces communication delays and enables real-time control of the injection, clamping, and ejection axes. The real-time servo control of the all-electric injection molding machine improves response time by 8 to 16 times, with repeatability of less than 0.1 mm, and the integrated rigid injection unit ensures mechanical stability with positioning accuracy of ±0.1mm.
Controlling the all electric injection molding machine with a servo drive
The high-speed servo drive system of the all electric injection molding machine ensures real-time monitoring and adjustment of each axis. Unlike injection molding machines that rely on proportional valves and are affected by fluid compressibility, servo motors communicate via a high-bandwidth bus that can transmit position commands and encoder feedback within 1 millisecond. First, the servo drive controller issues torque and position targets. Then, encoder feedback allows for instant correction. At the same time, the servo drive parameters are finely tuned, which can be adjusted according to the inertia and load of each axis, making the response time 8 to 16 times faster than that of traditional hydraulic drives. In addition, feedforward compensation predicts dynamic loads and reduces overshoot by 70%. This real-time control almost eliminates stabilization time and ensures consistent injection weight and dimensional consistency over tens of thousands of cycles on any injection molding machine production line.
High-rigidity integrated injection unit
Precision mechanical stability demands led us to integrate a high-rigidity injection seat into our all electric injection molding machine. Under sufficient stress analysis, we reinforced the injection frame to reduce the deflection under peak pressure by 60%; in addition, the beam reinforcement ribs and optimized wall thickness can suppress vibrations up to 150 Hz. At the same time, during the manufacturing process, our engineers verified the frame stiffness through modal testing to ensure that the first-order natural frequency is much higher than the working bandwidth. The direct-drive injection screw mounted on this rigid platform maintains precise screw positioning and melt control, converting electronic instruction fidelity into material consistency. These design choices maintain position accuracy and prevent minute fluctuations that can cause flash or undershot, even at high injection speeds of 200 mm/s.
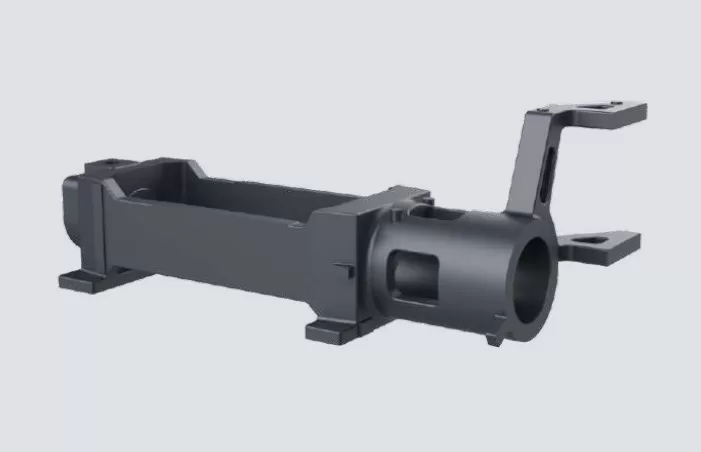
Shorter feedback cycles, higher precision
Hydraulic systems rely on feedback cycles of 10 to 20 milliseconds. However, our all electric injection molding machine reduces latency to less than 1 millisecond by sending a synchronization signal containing the servo motor’s working conditions to the upper controller under a self-developed system. Following a shortened cycle means that the system can detect and correct position drift before errors accumulate; as a result, positioning is maintained within ±0.5 mm, even during rapid acceleration. In addition, I implemented proprietary firmware that synchronizes sensor readings with actuator commands every 500 microseconds, reducing total control loop latency by 94%. Real-time metrics from each axis are fed into a deterministic scheduler that prioritizes critical motion tasks, ensuring that clamping, injection, and ejection phases proceed seamlessly without noticeable delays at transition points.
Accurate speed and pressure control
In addition to positioning, accurate speed and pressure regulation directly affect part quality, filling consistency, and mechanical stress. Driven by a servo, the injection screw achieves a speed accuracy of ±0.1%, enabling a smooth lift curve that reduces shear and improves melt uniformity; in addition, an integrated high-frequency pressure sensor samples at 5 kHz to ensure that the holding and holding pressures are within ±0.5 bar. At the same time, I designed a cascade control loop that tightly combines position, speed, and pressure to ensure a seamless transition from high-speed injection to low-speed holding without overshoot. This coordination prevents defects such as sink marks and internal stresses, achieving repeatable cycle-to-cycle consistency that hydraulic systems cannot match.
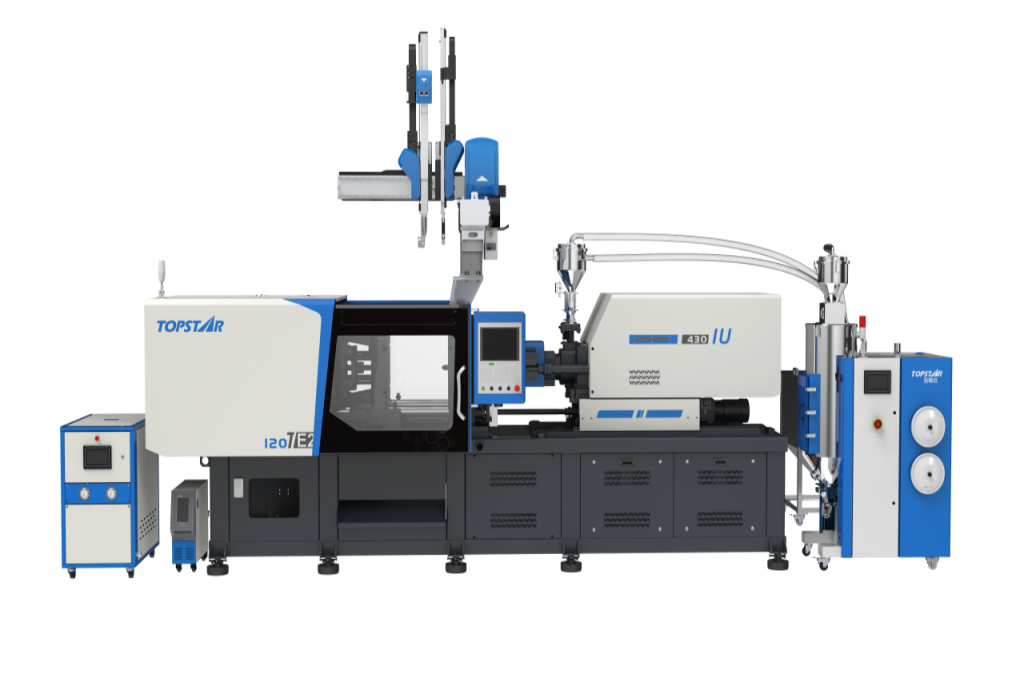
Bringing Smart Integration and Data Collection to All Electric Injection Molding Machine
Topstar’s all electric injection molding machines go beyond mere mechanical performance by embedding innovative hardware for real-time data collection and adaptive control. In addition, onboard IoT modules collect vibration, temperature, and torque data, enabling AI-driven analysis to predict maintenance needs before accuracy degrades. I oversee the implementation of servers that transmit high-resolution sensor data to the MES system to provide actionable insights into the injection molding machine. Machine learning algorithms dynamically adjust parameters to compensate for thermal expansion and wear, maintaining ±0.5mm accuracy over thousands of hours of operation. This overall intelligence ensures that the machine not only performs precise cycles but also maintains optimal performance with minimal human intervention.
Bringing ±0.1mm positioning accuracy
Topstar’s all electric injection molding machine uses real-time servo drives, high-rigidity mechanical design, ultra-short feedback cycles, precision speeds, and intelligent data integration to enable ±0.01mm repeatability, 8 to 16 times faster response speeds than hydraulic systems, and seamless connectivity for predictive maintenance. These features translate into shorter cycle times, lower scrap rates, and consistent part quality.
TRENDING POSTS
- What factors can cause delays in the injection molding process of plastic molding machine? 2025/07/14
- Exhibition Review| Topstar participates in InterPlas Thailand 2024 2025/07/14
- Star Case | Topstar helps Santong upgrade its intelligent plant 2025/07/14
- Topstar Special | National Science and Technology Workers Day 2025/07/14
HOT TOPIC
- .ervo motor-driven linear robots
- 1.0 guangdong topstar technology co. ltd
- 1.0 topstar china
- 1.0 topstar robot
- 11
- 2
- 21
- 23
- 3 axis robot
- 3 axis robots
- 3 in 1 Compact Dehumidifying Dryer
- 3-axis robot
- 3-axis robots
- 39
- 41
- 5-axis CNC machine
- 62
- accuracy
- Air Chillers
- all electric injection molding machine
- all electric injection molding machines
- All-electric injection molding machines
- and overall production quality. Therefore
- AP-RubberPlas
- automated injection molding machine
- Automation changed engineering
- automation of injection molding robots
- auxiliary machine
- Bench Injection Molding Machine
- Cabinet dryer manufacturers
- Cabinet dryers
- chiller
- CNC Drilling Machine
- CNC Drilling Machines
- cnc engraving machine manufacturer
- cnc laser cutting machine manufacturer
- CNC machine
- CNC Machine Center
- CNC Machine for Sale
- CNC Machine Manufacturing
- CNC Machine Tool
- CNC machine tool product
- CNC Machining Center
- CNC wood carving machine
- Cooling system
- Cross-Walking Single Axis Servo Cylinder Robot
- Cross-Walking Single-Axis Servo Cylinder Robot
- Cross-Walking Three-Axis/Five-Axis Servo Driven Robot
- cross-walking three-axis/five-axis servo-driven robot
- Dehumidifier Dryer
- Dehumidifying Dryer
- delta parallel robot
- Desktop Injection Molding Machine
- Desktop injection molding machines
- Desktop Molding Machine
- desktop plastic injection machine
- Desktop Plastic Injection Molding Machine
- direct clamp injection molding machine
- Direct clamp injection molding machines
- Dosing & mixing system
- Drilling Centers
- Drying and dehumidification system
- drying and dehumidifying equipment
- Drying and Dehumidifying System
- drying system
- effective and efficient. Cabinet dryers are also used in other industries where large quantities of material need to be dried
- efficient injection molding machine
- elbow hydraulic injection molding machines
- electric injection molding machine
- electric injection molding machines
- energy-efficient injection molding robot
- energy-efficient water chiller
- energy-efficient water chillers
- energy-saving injection molding machine
- etc. Among injection molding robots
- exhibition
- features of CNC machine
- Feeding And Conveying System
- Five Axis Machine Center
- Fully automatic injection molding machine
- Gathering Topstar
- giant injection molding machine
- GMU-600 5-Axis Machining Center
- Granulating & Recycling System
- Heavy duty injection molding machine
- High-precision electric molding machines
- high-precision plastic molding machines
- high-speed all electric injection molding machine
- high-speed electric injection molding machine
- High-Speed Packaging Injection Molding
- Honeycomb rotor dehumidifier
- horizontal injection molding machine
- Horizontal Injection Molding Machines
- Horizontal Injection Moulding Machine
- Horizontal Mixer manufacturer
- How The CNC Machine Works
- hybrid injection molding machine
- hydraulic injection molding machine
- Hydraulic Injection Molding Machines
- in this article
- Industrial robot
- Industrial Robot Chinese brand
- industrial robot parts
- industrial robot supplier
- Industrial robots
- Industry Chain
- Injection Manipulator
- injection manipulator robot
- injection mold machines
- Injection molding
- Injection molding automation
- Injection Molding Automation Solution
- injection molding dryer
- Injection molding equipment
- injection molding hopper dryer
- Injection molding machine
- injection molding machine brand
- Injection Molding Machine Factory
- Injection Molding Machine Manufacture
- Injection molding machine manufacturer
- injection molding machine manufacturers
- Injection molding machine procurement
- injection molding machine robotic arm
- injection molding machine with a robot
- Injection molding machines
- injection molding material dehumidifying
- injection molding plant
- injection molding process
- Injection Molding Robot
- injection molding robot arm
- Injection molding robot automation
- Injection molding robotic arm
- injection molding robots
- Injection moulding machine
- injection moulding machines
- Injection Moulding Robots
- Injection Robot
- Injection robot arm
- Injection robot manufacturer
- Injection robot wholesale
- injection robots
- intelligent injection molding machines
- intelligent mold temperature
- intelligent mold temperature controller
- Intelligent mould temperature controller
- Introducing Injection Robot
- It is the best choice for drying large quantities of material at once. Cabinetmakers use these machines because they are fast
- Large flow water type mold temperature controller
- large injection molding machine
- large injection molding machines
- Learn what industrial automation and robotics is
- linear robot
- linear robots
- low speed sound-proof granulator
- machine plastic molding
- make sure to add some! Improvements (2) Keyphrase in introduction: Your keyphrase or its synonyms appear in the first paragraph of the copy
- manipulator machine
- manufacturing
- medical grade injection molding machines
- medical injection molding machine
- medical injection molding machines
- micro injection molding machine
- middle speed granulator
- Mini CNC machine manufacturers.
- Mold Temperature Control System
- mold temperature controller
- mold temperature controllers
- molding material Dehumidifying System
- mould temperature control system
- mould temperature controller
- mould temperature controllers
- New electric injection molding machine
- nitrogen dryer manufacturer
- nitrogen dryer system manufacturer
- Oil type mold temperature controller
- Oil type mold temperature controllers
- open day
- optical component injection molding
- Outbound links: No outbound links appear in this page. Add some! Images: No images appear on this page. Add some! Internal links: No internal links appear in this page
- PET Preform injection molding
- phone case maker machine
- phone case making machine
- phone cover making machine
- plastic bottle making machine
- plastic bottle manufacturing
- plastic bucket making machine
- plastic bucket manufacturing
- Plastic chair making machine
- plastic forming equipment
- plastic hopper dryer
- plastic injection machine
- plastic injection machines
- plastic injection molding
- Plastic injection molding equipment
- Plastic injection molding machine
- Plastic Injection Molding Machines
- plastic injection moulding machine
- plastic injection moulding machines
- plastic injection robot
- plastic molding
- Plastic Molding machine
- plastic molding machine 1
- Plastic Molding Machines
- plastic molding press
- plastic moulding machine
- plastic phone case making machine
- plastic-molding machine
- powerful granulator
- Powerful Type Sound-Proof Granulator
- precision injection molding
- precision injection molding machines
- production of plastic seats
- pure water mould temperature controller
- Robot injection molding
- robot injection molding machine
- robot manufacturing companies
- Robotic arm for injection molding machine
- robotic injection molding machines
- robotics in injection molding
- SCARA robot
- SCARA robots
- Service-oriented manufacturing
- Servo Cylinder Robot
- servo driven robot
- Servo Driven Robots
- servo injection molding machine
- servo injection robots
- servo motor-driven linear robots
- servo-driven 3-axis robot
- Servo-Driven Robot
- Setup of injection machine
- Silicone Injection Molding Machine
- six-axis industrial robot
- Stainless Hopper Dryer
- Stainless Hopper Dryers
- star club
- swing arm robot
- take-out robot
- take-out robots
- the choice between servo-driven robots and hydraulic robots will have a certain impact on efficiency
- the most popular injection molding machine
- the type of injection molding robot
- TMII injection molding machine
- toggle clamp injection molding machine
- Toggle Hydraulic Injection Molding Machines
- toggle injection molding machine
- Top 10 brands of injection robots
- Topstar
- Topstar Engineering
- Topstar Industrial Robots
- Topstar injection molding intelligent
- Topstar Scara Robots
- Useful Injection molding machine
- Vertical machining centers
- volumetric type blender
- water chiller
- water chillers
- water distributor
- water type mold temperature controller
- Water Type MoldTemperature Controller
- Water-Type Mould Temperature Controllers
- We often face choices when performing injection molding. We will choose the type of injection molding machine
- wholesale of injection molding machines
- x carve CNC
- 热门查询 点击次数 展示 排名 topstar