Achieving high precision with six-axis industrial robot technology
2023/12/29 By Topstar
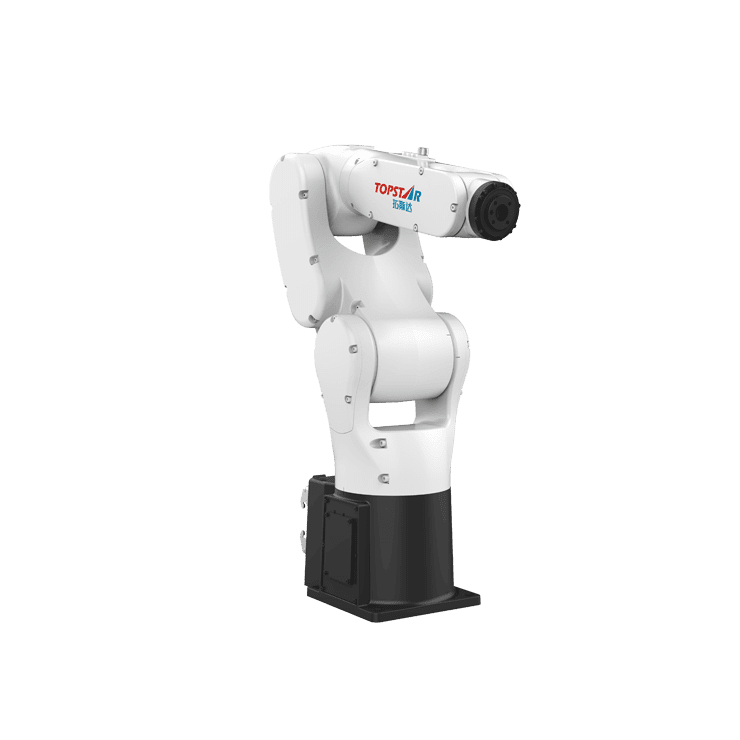
In modern manufacturing, precision is the foundation of excellence. This blog post explores how a six-axis industrial robot enables unprecedented levels of precision across different industries and the impact this is having. Manufacturers, engineers, and researchers can gain more detailed insights by delving into these robotic systems’ complex capabilities and applications. This makes it easier to operate them.
Understand the mechanical structure of a six-axis industrial robot
Six-axis industrial robots have a unique mechanical design with six rotating joints, giving them six degrees of freedom. Joints are usually numbered 1 to 6, starting at the base joint and working up to the wrist joint. Each joint has a different range of motion, and this joint structure enables the robot to achieve complex movements in three-dimensional space. These robotic arm parts provide the necessary connections between joints, allowing the robot to reach different positions and directions, and their protection levels are IP40/IP67 optional.
The end effector is located at the end of the robot arm and is a tool or device used to perform specific tasks. Depending on the application, end effectors can include clamps, welding guns, or other means. Its design and connection methods affect the overall functionality of the robot. Their mechanical structure determines the robot’s axis configuration. Standard configurations include anthropomorphic or cylindrical, while common materials for structural components include aluminum and steel, and lightweight materials can enhance flexibility.
Cross-industry application of six-axis industrial robots
They have a wide range of cross-industry applications, and in the aerospace sector, six-axis robots excel at tasks such as assembly, welding, and precision machining of complex parts. At the base of the automotive assembly line, perform tasks such as welding, painting, and assembling components. Their ability to adapt to different tasks increases productivity and quality. Six-axis robots are used for injection molding, material handling, and assembly in the plastics and rubber industry. Their agility and speed increase production line efficiency. Industries in metal fabrication benefit from them performing tasks such as welding, cutting, and polishing. Their precision and ability to handle heavy loads contribute to efficient metalworking processes.
The role of advanced sensors in six-axis industrial robots
Advanced sensors enable them to perform precision, adaptability, and safety tasks. These sensors provide real-time data, allowing the robot to respond to environmental changes dynamically. Encoders and resolver sensors accurately measure the position and orientation of robot joints and end effectors. Integrating force/torque sensors into a robot’s end effector can provide feedback on the forces and torques exerted during object interactions. This tactile feedback enables robots to perform tasks that require delicate touch, such as assembly or handling fragile items. In addition, visual, proximity, and thermal sensors allow the robot to perceive and interpret the surrounding environment and detect whether objects are near the robot. Helps avoid collisions, monitors the temperature of robot components, prevents overheating, and ensures optimal operating conditions.
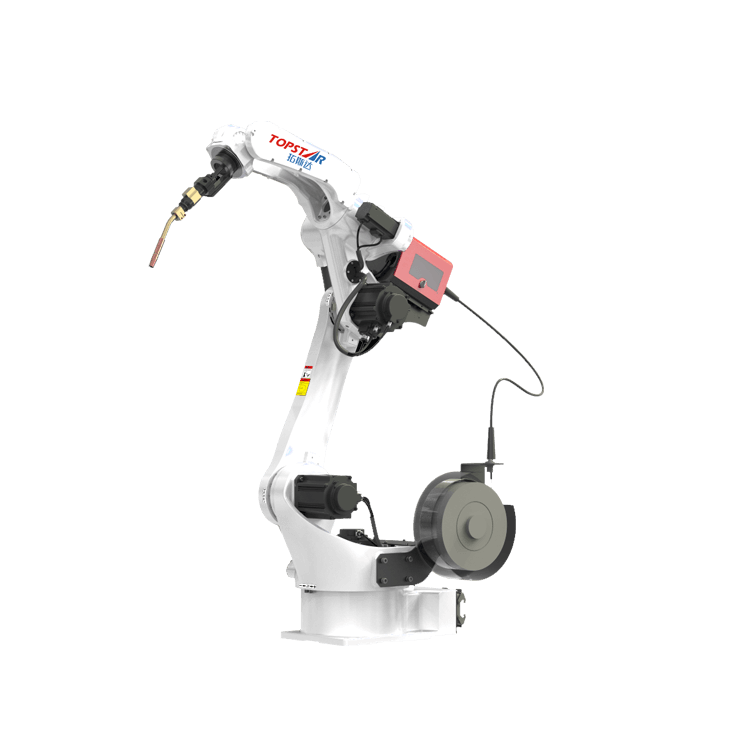
Programming of a six-axis industrial robot
Six-axis robot programming requires a rigorous approach to ensure accurate and efficient task execution. They typically program the interface using a specific or vendor-specific programming language. Generating precise trajectories for robot end effectors requires careful path planning. This includes defining the required path, velocity, and acceleration profiles to ensure smooth and accurate movement. Programmers can simulate and verify robot motion before implementation using offline programming software. This allows the program to be fine-tuned to achieve the desired accuracy without physical trial and error.
A holistic approach to efficiency
Start by analyzing the task to identify optimization opportunities. Simplifying and refining task sequences can significantly reduce cycle times and improve efficiency. Operators use programming languages and technologies to enhance precision, control, and versatility. Implementing continuous and smooth motion trajectories minimizes acceleration and deceleration times. Energy-saving components can also be used, utilizing regenerative braking systems and incorporating sleep modes during idle periods to optimize energy consumption and reduce operating costs. In addition, we need to calibrate the robot to ensure accurate positioning and movement regularly. System calibration minimizes errors and discrepancies, maintaining high accuracy in mission execution.
Final
In this article, we describe how six-axis industrial robotics enables high precision in industrial environments, allowing our industrial manufacturers to understand the capabilities these robotic systems bring to us. Using these robots can make our production process more efficient and reduce errors.
TRENDING POSTS
- What factors can cause delays in the injection molding process of plastic molding machine? 2023/12/29
- Exhibition Review| Topstar participates in InterPlas Thailand 2024 2023/12/29
- Star Case | Topstar helps Santong upgrade its intelligent plant 2023/12/29
- Topstar Special | National Science and Technology Workers Day 2023/12/29
HOT TOPIC
- .ervo motor-driven linear robots
- 3 axis robot
- 3 axis robots
- 3 in 1 Compact Dehumidifying Dryer
- 3-axis robot
- 3-axis robots
- 5-axis CNC machine
- accuracy
- Air Chillers
- all electric injection molding machine
- all electric injection molding machines
- All-electric injection molding machines
- and overall production quality. Therefore
- AP-RubberPlas
- automated injection molding machine
- Automation changed engineering
- automation of injection molding robots
- auxiliary machine
- Bench Injection Molding Machine
- Cabinet dryer manufacturers
- Cabinet dryers
- chiller
- CNC Drilling Machine
- CNC Drilling Machines
- cnc engraving machine manufacturer
- cnc laser cutting machine manufacturer
- CNC machine
- CNC Machine Center
- CNC Machine for Sale
- CNC Machine Manufacturing
- CNC Machine Tool
- CNC machine tool product
- CNC Machining Center
- CNC wood carving machine
- Cooling system
- Cross-Walking Single Axis Servo Cylinder Robot
- Cross-Walking Single-Axis Servo Cylinder Robot
- Cross-Walking Three-Axis/Five-Axis Servo Driven Robot
- cross-walking three-axis/five-axis servo-driven robot
- Dehumidifier Dryer
- Dehumidifying Dryer
- delta parallel robot
- Desktop Injection Molding Machine
- Desktop injection molding machines
- Desktop Molding Machine
- desktop plastic injection machine
- Desktop Plastic Injection Molding Machine
- direct clamp injection molding machine
- Direct clamp injection molding machines
- Dosing & mixing system
- Drilling Centers
- Drying and dehumidification system
- drying and dehumidifying equipment
- Drying and Dehumidifying System
- drying system
- effective and efficient. Cabinet dryers are also used in other industries where large quantities of material need to be dried
- efficient injection molding machine
- elbow hydraulic injection molding machines
- electric injection molding machine
- electric injection molding machines
- energy-efficient injection molding robot
- energy-saving injection molding machine
- etc. Among injection molding robots
- exhibition
- features of CNC machine
- Feeding And Conveying System
- Five Axis Machine Center
- Fully automatic injection molding machine
- Gathering Topstar
- giant injection molding machine
- GMU-600 5-Axis Machining Center
- Granulating & Recycling System
- Heavy duty injection molding machine
- High-precision electric molding machines
- high-precision plastic molding machines
- high-speed all electric injection molding machine
- Honeycomb rotor dehumidifier
- horizontal injection molding machine
- Horizontal Injection Molding Machines
- Horizontal Injection Moulding Machine
- Horizontal Mixer manufacturer
- How The CNC Machine Works
- hybrid injection molding machine
- hydraulic injection molding machine
- Hydraulic Injection Molding Machines
- in this article
- Industrial robot
- Industrial Robot Chinese brand
- industrial robot parts
- industrial robot supplier
- Industrial robots
- Industry Chain
- Injection Manipulator
- injection manipulator robot
- injection mold machines
- Injection molding
- Injection molding automation
- Injection Molding Automation Solution
- injection molding dryer
- Injection molding equipment
- injection molding hopper dryer
- Injection molding machine
- injection molding machine brand
- Injection Molding Machine Factory
- Injection Molding Machine Manufacture
- Injection molding machine manufacturer
- injection molding machine manufacturers
- Injection molding machine procurement
- injection molding machine robotic arm
- injection molding machine with a robot
- Injection molding machines
- injection molding material dehumidifying
- injection molding plant
- Injection Molding Robot
- injection molding robot arm
- Injection molding robot automation
- Injection molding robotic arm
- injection molding robots
- Injection moulding machine
- Injection Moulding Robots
- Injection Robot
- Injection robot arm
- Injection robot manufacturer
- Injection robot wholesale
- injection robots
- intelligent injection molding machines
- Introducing Injection Robot
- It is the best choice for drying large quantities of material at once. Cabinetmakers use these machines because they are fast
- large injection molding machine
- large injection molding machines
- Learn what industrial automation and robotics is
- linear robot
- linear robots
- low speed sound-proof granulator
- machine plastic molding
- make sure to add some! Improvements (2) Keyphrase in introduction: Your keyphrase or its synonyms appear in the first paragraph of the copy
- manipulator machine
- manufacturing
- medical grade injection molding machines
- medical injection molding machine
- medical injection molding machines
- micro injection molding machine
- middle speed granulator
- Mini CNC machine manufacturers.
- Mold Temperature Control System
- mold temperature controller
- mold temperature controllers
- molding material Dehumidifying System
- mould temperature control system
- mould temperature controller
- mould temperature controllers
- New electric injection molding machine
- nitrogen dryer manufacturer
- nitrogen dryer system manufacturer
- Oil type mold temperature controller
- Oil type mold temperature controllers
- open day
- Outbound links: No outbound links appear in this page. Add some! Images: No images appear on this page. Add some! Internal links: No internal links appear in this page
- PET Preform injection molding
- phone case maker machine
- phone case making machine
- plastic bottle making machine
- plastic bottle manufacturing
- plastic bucket making machine
- plastic bucket manufacturing
- Plastic chair making machine
- plastic forming equipment
- plastic hopper dryer
- plastic injection machine
- plastic injection machines
- plastic injection molding
- Plastic injection molding equipment
- Plastic injection molding machine
- Plastic Injection Molding Machines
- plastic injection moulding machine
- plastic injection robot
- Plastic Molding machine
- Plastic Molding Machines
- plastic molding press
- plastic moulding machine
- plastic phone case making machine
- plastic-molding machine
- powerful granulator
- Powerful Type Sound-Proof Granulator
- precision injection molding
- precision injection molding machines
- production of plastic seats
- pure water mould temperature controller
- Robot injection molding
- robot injection molding machine
- robot manufacturing companies
- Robotic arm for injection molding machine
- robotic injection molding machines
- robotics in injection molding
- SCARA robot
- SCARA robots
- Service-oriented manufacturing
- Servo Cylinder Robot
- servo driven robot
- Servo Driven Robots
- servo injection robots
- servo motor-driven linear robots
- servo-driven 3-axis robot
- Servo-Driven Robot
- Setup of injection machine
- Silicone Injection Molding Machine
- six-axis industrial robot
- Stainless Hopper Dryer
- Stainless Hopper Dryers
- star club
- swing arm robot
- take-out robots
- the choice between servo-driven robots and hydraulic robots will have a certain impact on efficiency
- the most popular injection molding machine
- the type of injection molding robot
- toggle clamp injection molding machine
- Toggle Hydraulic Injection Molding Machines
- toggle injection molding machine
- Top 10 brands of injection robots
- Topstar
- Topstar Engineering
- Topstar Industrial Robots
- Topstar injection molding intelligent
- Topstar Scara Robots
- Useful Injection molding machine
- Vertical machining centers
- volumetric type blender
- water chiller
- water chillers
- water distributor
- water type mold temperature controller
- Water Type MoldTemperature Controller
- Water-Type Mould Temperature Controllers
- We often face choices when performing injection molding. We will choose the type of injection molding machine
- wholesale of injection molding machines
- x carve CNC