Choosing Between Vertical and Heavy duty injection molding machine
2024/01/08 By Topstar
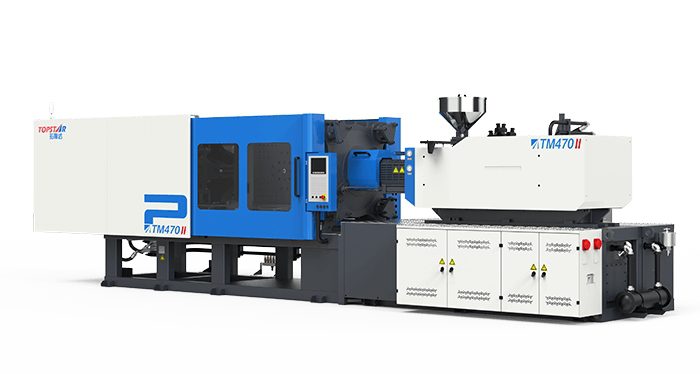
Vertical injection molding machines and Heavy duty injection molding machine have many differences in their functionality and features. Our selection is based on the manufacturing efficiency, price difference, and final product quality they provide. In this guide, we will analyze the differences between the two so that injection molding manufacturers and buyers can make wise choices based on their needs.
Power and versatility in heavy duty injection molding machine
Heavy duty injection molding machines boast robust hydraulic systems and precise servo-electric drive mechanisms in power. These power systems deliver formidable injection forces, ensuring the efficient molding of complex and sizable parts. Advanced control algorithms enhance energy efficiency, enabling versatility across various materials—from traditional thermoplastics to cutting-edge composites—catering to diverse industrial applications. Moreover, their adaptability extends to intricate molding processes such as gas-assisted molding, co-injection molding, and multi-material molding, providing manufacturers with a comprehensive solution for complex part production.
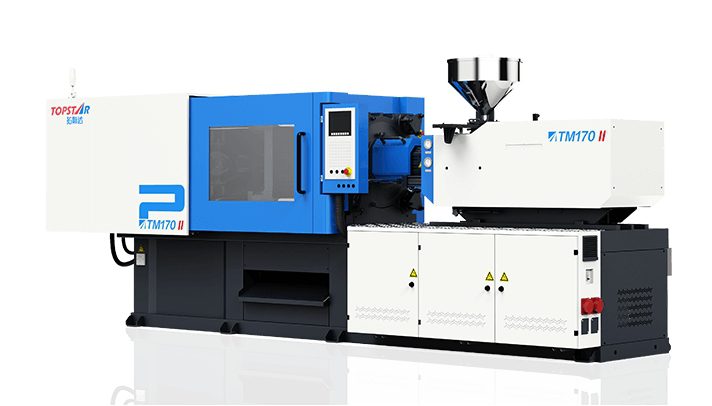
Heavy Duty Injection Molding Machine Dimensions and Capacities
Heavy duty injection molding machines exhibit variations in size and tonnage, typically ranging from 500 to 6,000 tons, tailored to specific production requirements. Higher tonnage machines are favored for their augmented clamping force for intricate and more extensive plastic parts, ensuring the successful molding of complex molds and more significant components. Conversely, smaller tonnage machines prove ideal for less complicated and smaller parts, optimizing efficiency for such applications. The ultimate choice hinges on mold size, weight, and component complexity, empowering manufacturers to optimize their production processes.
Precision and space efficiency of vertical injection molding machine
In contrast to heavy-duty injection molding machines, vertical injection molding machines underscore their space efficiency and precision molding applicability. Featuring a distinctive vertical clamping and injection unit configuration, these machines offer advantages in terms of precision and space utilization. Precision is a defining trait of vertical injection molding machines due to the downward force exerted during mold closure. This setup ensures consistent and even pressure on the mold, facilitating the precise molding of intricate and detailed parts. The vertical orientation minimizes mold distortion, enhancing part quality and dimensional accuracy.
Space efficiency is advantageous in constrained environments, enabling manufacturers to optimize their production layouts. Vertical machines seamlessly integrate into existing manufacturing installations, providing versatility and adaptability to diverse production environments. Vertical injection molding machines offer convenient mold replacement and maintenance benefits, streamlining workflow and reducing downtime. The vertical orientation further facilitates the efficient utilization of molds.
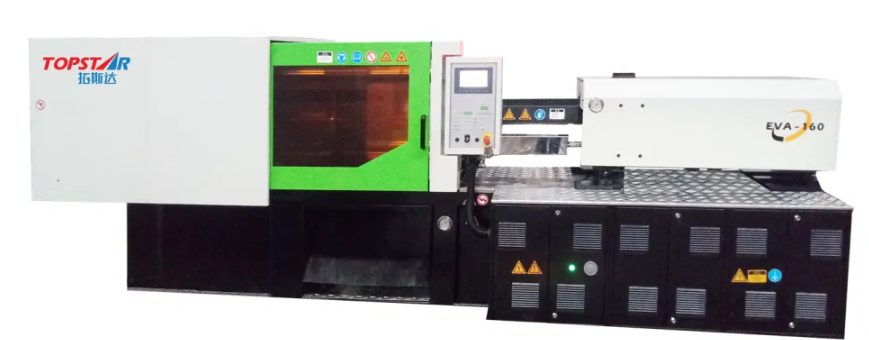
Understand the configuration of vertical injection molding machines
The configuration of a vertical injection molding machine plays a pivotal role in determining its performance. The single-slide configuration incorporates a vertically movable mold-carrying platen, suitable for simpler molds and applications. This design offers a cost-effective solution while maintaining accuracy and minimizing mold wear. The turret configuration features a rotating platform that moves the mold between injection and clamping units, simultaneously allowing multiple molds on the rotary table, enhancing production efficiency. The shuttle table configuration utilizes a horizontal table for shuttle movements, proving advantageous for larger molds or handling multiple molds of different sizes. It streamlines loading and unloading, reducing downtime and boosting overall productivity.
When to choose heavy-duty injection molding machine or a vertical?
Considerations for Yield
Heavy-duty injection molding machines are favored for high-volume production requiring large quantities of identical or similar parts. These machines ensure efficient and continuous production with fast cycle times and high clamping force. The horizontal configuration accommodates multi-cavity molds, enabling simultaneous production of multiple parts in each cycle—a cost-effective and time-efficient solution for large-scale manufacturing.
Vertical injection molding machines excel in applications with low to medium volumes and varying part geometries. Their vertical setup allows easier mold access, simplifying tool changes and maintenance. Ideal for molding complex parts with intricate details, they are suitable for specialty or custom production where versatility and precision are paramount. The compact footprint of vertical machines proves advantageous in facilities with limited space, particularly for setting up production lines in smaller shops or integrating injection molding into existing manufacturing setups.
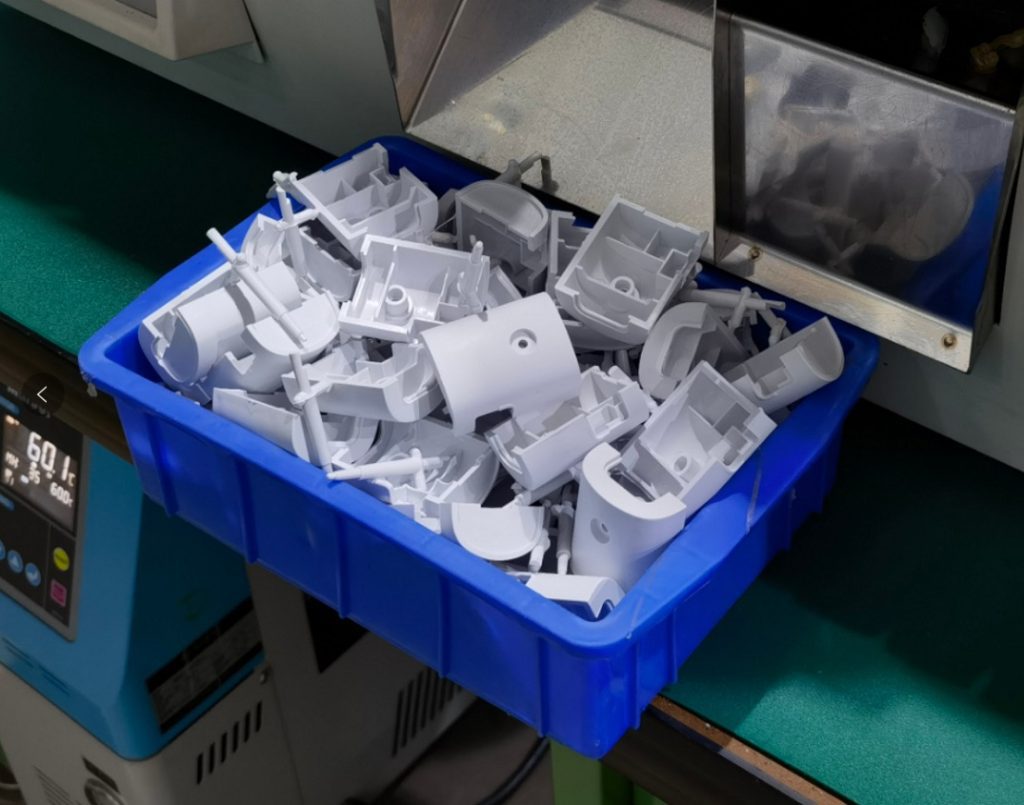
Materials and Application Properties
Heavy-duty horizontal machines handle a range of materials, including commodity plastics and engineering plastics. They excel with high-viscosity materials like polyethylene, polypropylene, and various thermoplastic resins, making them ideal for molding large and robust parts in the automotive, packaging, and consumer products industries. With their unique configurations, vertical injection molding machines cater to specialized applications and specific material properties. Efficient mold channels and reduced mold wear make them ideal for molding thermosets, elastomers, and silicone rubbers—particularly suitable for precision molding of complex and small parts in the medical, electronics, and aerospace industries.
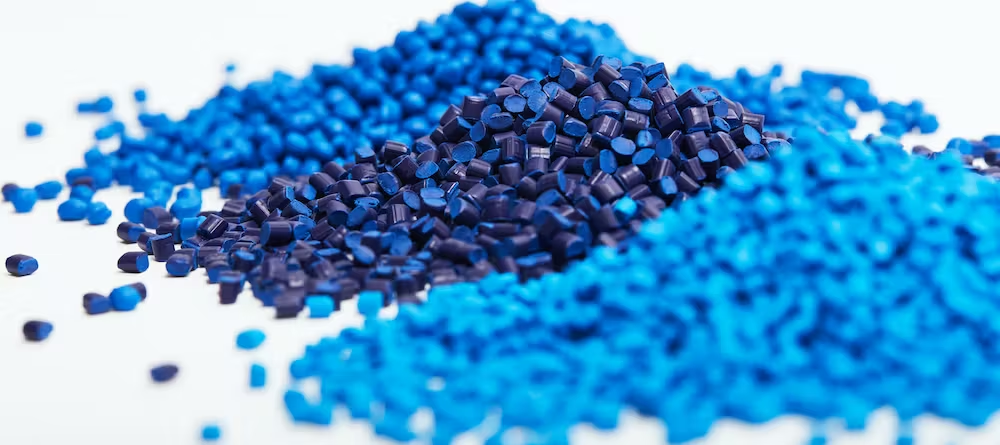
In the end
Selecting between heavy-duty horizontal injection molding machines and vertical injection molding machines hinges on diverse factors, each tailored to specific work environments. Opting for heavy-duty machines proves advantageous in scenarios demanding high-volume production of identical or similar parts. Conversely, vertical injection molding machines offer benefits in applications characterized by low to medium volumes and diverse part geometries. Regardless of the chosen approach, astute decision-making remains crucial for optimal outcomes.
TRENDING POSTS
- What factors can cause delays in the injection molding process of plastic molding machine? 2024/01/08
- Exhibition Review| Topstar participates in InterPlas Thailand 2024 2024/01/08
- Star Case | Topstar helps Santong upgrade its intelligent plant 2024/01/08
- Topstar Special | National Science and Technology Workers Day 2024/01/08
HOT TOPIC
- .ervo motor-driven linear robots
- 3 axis robot
- 3 axis robots
- 3 in 1 Compact Dehumidifying Dryer
- 3-axis robot
- 3-axis robots
- 5-axis CNC machine
- accuracy
- Air Chillers
- all electric injection molding machine
- all electric injection molding machines
- All-electric injection molding machines
- and overall production quality. Therefore
- AP-RubberPlas
- automated injection molding machine
- Automation changed engineering
- automation of injection molding robots
- auxiliary machine
- Bench Injection Molding Machine
- Cabinet dryer manufacturers
- Cabinet dryers
- chiller
- CNC Drilling Machine
- CNC Drilling Machines
- cnc engraving machine manufacturer
- cnc laser cutting machine manufacturer
- CNC machine
- CNC Machine Center
- CNC Machine for Sale
- CNC Machine Manufacturing
- CNC Machine Tool
- CNC machine tool product
- CNC Machining Center
- CNC wood carving machine
- Cooling system
- Cross-Walking Single Axis Servo Cylinder Robot
- Cross-Walking Single-Axis Servo Cylinder Robot
- Cross-Walking Three-Axis/Five-Axis Servo Driven Robot
- cross-walking three-axis/five-axis servo-driven robot
- Dehumidifier Dryer
- Dehumidifying Dryer
- delta parallel robot
- Desktop Injection Molding Machine
- Desktop injection molding machines
- Desktop Molding Machine
- desktop plastic injection machine
- Desktop Plastic Injection Molding Machine
- direct clamp injection molding machine
- Direct clamp injection molding machines
- Dosing & mixing system
- Drilling Centers
- Drying and dehumidification system
- drying and dehumidifying equipment
- Drying and Dehumidifying System
- drying system
- effective and efficient. Cabinet dryers are also used in other industries where large quantities of material need to be dried
- efficient injection molding machine
- elbow hydraulic injection molding machines
- electric injection molding machine
- electric injection molding machines
- energy-efficient injection molding robot
- energy-saving injection molding machine
- etc. Among injection molding robots
- exhibition
- features of CNC machine
- Feeding And Conveying System
- Five Axis Machine Center
- Fully automatic injection molding machine
- Gathering Topstar
- giant injection molding machine
- GMU-600 5-Axis Machining Center
- Granulating & Recycling System
- Heavy duty injection molding machine
- High-precision electric molding machines
- high-precision plastic molding machines
- high-speed all electric injection molding machine
- Honeycomb rotor dehumidifier
- horizontal injection molding machine
- Horizontal Injection Molding Machines
- Horizontal Injection Moulding Machine
- Horizontal Mixer manufacturer
- How The CNC Machine Works
- hybrid injection molding machine
- hydraulic injection molding machine
- Hydraulic Injection Molding Machines
- in this article
- Industrial robot
- Industrial Robot Chinese brand
- industrial robot parts
- industrial robot supplier
- Industrial robots
- Industry Chain
- Injection Manipulator
- injection manipulator robot
- injection mold machines
- Injection molding
- Injection molding automation
- Injection Molding Automation Solution
- injection molding dryer
- Injection molding equipment
- injection molding hopper dryer
- Injection molding machine
- injection molding machine brand
- Injection Molding Machine Factory
- Injection Molding Machine Manufacture
- Injection molding machine manufacturer
- injection molding machine manufacturers
- Injection molding machine procurement
- injection molding machine robotic arm
- injection molding machine with a robot
- Injection molding machines
- injection molding material dehumidifying
- injection molding plant
- Injection Molding Robot
- injection molding robot arm
- Injection molding robot automation
- Injection molding robotic arm
- injection molding robots
- Injection moulding machine
- Injection Moulding Robots
- Injection Robot
- Injection robot arm
- Injection robot manufacturer
- Injection robot wholesale
- injection robots
- intelligent injection molding machines
- Introducing Injection Robot
- It is the best choice for drying large quantities of material at once. Cabinetmakers use these machines because they are fast
- large injection molding machine
- large injection molding machines
- Learn what industrial automation and robotics is
- linear robot
- linear robots
- low speed sound-proof granulator
- machine plastic molding
- make sure to add some! Improvements (2) Keyphrase in introduction: Your keyphrase or its synonyms appear in the first paragraph of the copy
- manipulator machine
- manufacturing
- medical grade injection molding machines
- medical injection molding machine
- medical injection molding machines
- micro injection molding machine
- middle speed granulator
- Mini CNC machine manufacturers.
- Mold Temperature Control System
- mold temperature controller
- mold temperature controllers
- molding material Dehumidifying System
- mould temperature control system
- mould temperature controller
- mould temperature controllers
- New electric injection molding machine
- nitrogen dryer manufacturer
- nitrogen dryer system manufacturer
- Oil type mold temperature controller
- Oil type mold temperature controllers
- open day
- Outbound links: No outbound links appear in this page. Add some! Images: No images appear on this page. Add some! Internal links: No internal links appear in this page
- PET Preform injection molding
- phone case maker machine
- phone case making machine
- plastic bottle making machine
- plastic bottle manufacturing
- plastic bucket making machine
- plastic bucket manufacturing
- Plastic chair making machine
- plastic forming equipment
- plastic hopper dryer
- plastic injection machine
- plastic injection machines
- plastic injection molding
- Plastic injection molding equipment
- Plastic injection molding machine
- Plastic Injection Molding Machines
- plastic injection moulding machine
- plastic injection robot
- Plastic Molding machine
- Plastic Molding Machines
- plastic molding press
- plastic moulding machine
- plastic phone case making machine
- plastic-molding machine
- powerful granulator
- Powerful Type Sound-Proof Granulator
- precision injection molding
- precision injection molding machines
- production of plastic seats
- pure water mould temperature controller
- Robot injection molding
- robot injection molding machine
- robot manufacturing companies
- Robotic arm for injection molding machine
- robotic injection molding machines
- robotics in injection molding
- SCARA robot
- SCARA robots
- Service-oriented manufacturing
- Servo Cylinder Robot
- servo driven robot
- Servo Driven Robots
- servo injection robots
- servo motor-driven linear robots
- servo-driven 3-axis robot
- Servo-Driven Robot
- Setup of injection machine
- Silicone Injection Molding Machine
- six-axis industrial robot
- Stainless Hopper Dryer
- Stainless Hopper Dryers
- star club
- swing arm robot
- take-out robots
- the choice between servo-driven robots and hydraulic robots will have a certain impact on efficiency
- the most popular injection molding machine
- the type of injection molding robot
- toggle clamp injection molding machine
- Toggle Hydraulic Injection Molding Machines
- toggle injection molding machine
- Top 10 brands of injection robots
- Topstar
- Topstar Engineering
- Topstar Industrial Robots
- Topstar injection molding intelligent
- Topstar Scara Robots
- Useful Injection molding machine
- Vertical machining centers
- volumetric type blender
- water chiller
- water chillers
- water distributor
- water type mold temperature controller
- Water Type MoldTemperature Controller
- Water-Type Mould Temperature Controllers
- We often face choices when performing injection molding. We will choose the type of injection molding machine
- wholesale of injection molding machines
- x carve CNC