CNC Drilling and Tapping Machine Worth Investing in
2022/08/13 By Topstar
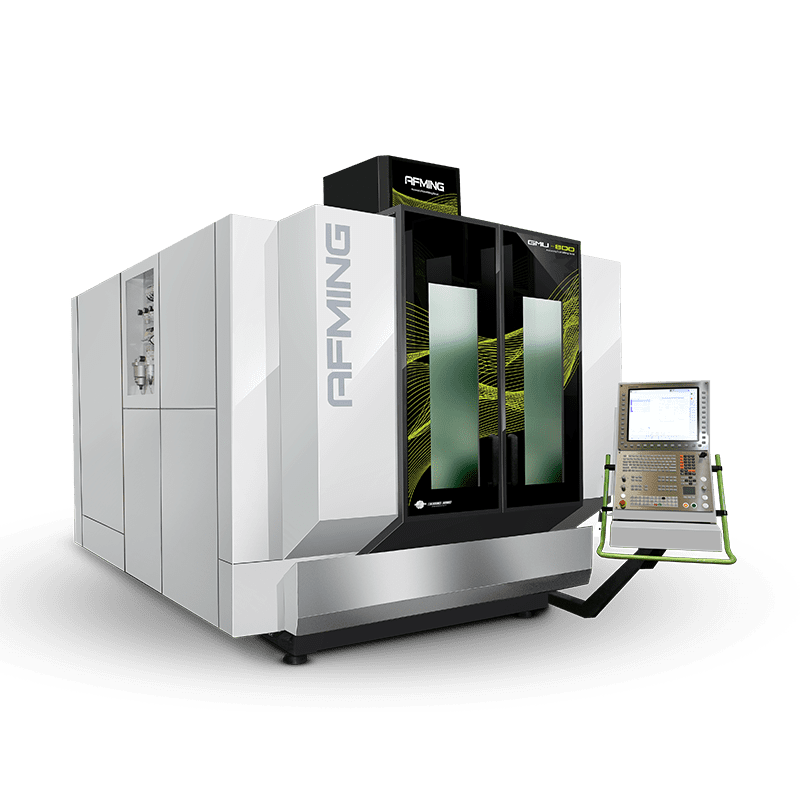
CNC drilling and tapping machines are a worthwhile investment. If you also want to invest in a CNC drilling and tapping machine but are unsure where to start, this article is for you! In it, we’ll take a deep dive into how these machines work. Here are a few reasons why it’s worth the investment so you can make an informed decision on whether it’s worth investing in one of these machines for your business.
It’s one of the best decisions to make for a high-quality product!
Investing in a CNC drilling and tapping machine is one of the best decisions when manufacturing high-quality products. They can perform and tap tasks quickly and accurately, which is why so many manufacturers rely on them for their production needs.
CNC Drilling & Tapping Machines: Why You Need One
The main benefit of investing in a CNC drilling & tapping machine is that these machines can do this quickly and accurately. Because they have specific instructions programmed for each task, the operator doesn’t have to control them manually. The computer does all this work for them! This leaves less time on repetitive tasks, such as drilling holes or tapping threads into place, and instead allows you to focus more on other areas that may require human input.
How does a CNC drilling and tapping machine work?
A CNC drilling and tapping machine, or CNC D&T, is a computer-controlled machine that uses a rotary spindle to perform drilling and tapping operations. The spindle has an attached tool bit (usually made from carbide) with a cutting edge sharpened by grinding. The spindle is mounted on a vertical or horizontal base depending on the task. For example, a vertical is better suited to your needs if you want equipment that can drill and tap simultaneously in one operation. Because it is easier to access during installation or removal and when changing bits.
The speed of these machines is CAM controlled, and the program considers factors such as material type and thickness before determining the appropriate feed rate based on these inputs and other elements in the assembly line setup. Multiple parts of it need to go through a similar process simultaneously. So, when downstream needs them, they are ready. Efficiently complete the work and better meet the quality control standards set by customers so that every new product ordered by customers is perfect!
When should I consider the purchase of a CNC drilling and tapping machine?
If you are a manufacturer or contractor and want to make high-quality products, purchasing a CNC drilling and tapping machine is worth investing in. This is because these machines can help you save time, money and improve productivity.
When saving time, CNC drilling and tapping machines are much faster than manual operations because they do not require as much human intervention. When saving time, CNC drilling and tapping machines are much faster than manual operations because they require less human intervention. For example, if an 8mm hole is drilled into a sheet metal at a 45-degree angle from both sides of a container, it would take a person 3 minutes with a hand tool but 15 seconds with a CNC drill!
Another benefit of this tool is increased accuracy levels and efficiency, especially when working with significant components.
A cnc drilling and tapping machine can help businesses with the production process!
It can help enterprises complete the production process. They are faster than traditional methods and don’t require as much labor.
Why is CNC drilling and tapping machines better than traditional methods?
The main benefit of using these machines is that they can drill holes faster than people can do it manually. Additionally, they are more precise than hand tools because their operation does not involve human error. Some more points to cover in this section include:
What is CNC drilling and tapping machines used for?
They primarily punch holes in materials such as metal or woodwork to securely secure screws to these materials during assembly in a manufacturing facility. These factories or warehouses quickly assemble many products before shipping them out, then sell them online on the website!
Investing in your business’s best CNC drilling and tapping machine is essential!
The CNC drilling and tapping machine is integral to any business’s production process. It allows you to save time, money and increase the quality of your products while increasing profits.
The CNC drilling and tapping machine can help you with all these things:
Save Time – CNC Drilling and Tapping Machines Let You Be More Productive! That means more opportunities for mistakes during a busy workday. Also, having such a device simultaneously will not present any problem if you are dealing with emergencies.
To sum up
CNC drilling and tapping machines are indispensable tools in your workshop. You can tell from the above that they speed up production, save time and money, enable you to make more accurate parts, and more. These reasons make it one of the most worthwhile investment machines; we will have a professional team and service to help you choose the suitable machine!
TRENDING POSTS
- What factors can cause delays in the injection molding process of plastic molding machine? 2022/08/13
- Exhibition Review| Topstar participates in InterPlas Thailand 2024 2022/08/13
- Star Case | Topstar helps Santong upgrade its intelligent plant 2022/08/13
- Topstar Special | National Science and Technology Workers Day 2022/08/13
HOT TOPIC
- .ervo motor-driven linear robots
- 1.0 guangdong topstar technology co. ltd
- 1.0 topstar china
- 1.0 topstar robot
- 11
- 2
- 21
- 23
- 3 axis robot
- 3 axis robots
- 3 in 1 Compact Dehumidifying Dryer
- 3-axis robot
- 3-axis robots
- 39
- 41
- 5-axis CNC machine
- 62
- accuracy
- Air Chillers
- all electric injection molding machine
- all electric injection molding machines
- All-electric injection molding machines
- and overall production quality. Therefore
- AP-RubberPlas
- automated injection molding machine
- Automation changed engineering
- automation of injection molding robots
- auxiliary machine
- Bench Injection Molding Machine
- Cabinet dryer manufacturers
- Cabinet dryers
- chiller
- CNC Drilling Machine
- CNC Drilling Machines
- cnc engraving machine manufacturer
- cnc laser cutting machine manufacturer
- CNC machine
- CNC Machine Center
- CNC Machine for Sale
- CNC Machine Manufacturing
- CNC Machine Tool
- CNC machine tool product
- CNC Machining Center
- CNC wood carving machine
- Cooling system
- Cross-Walking Single Axis Servo Cylinder Robot
- Cross-Walking Single-Axis Servo Cylinder Robot
- Cross-Walking Three-Axis/Five-Axis Servo Driven Robot
- cross-walking three-axis/five-axis servo-driven robot
- Dehumidifier Dryer
- Dehumidifying Dryer
- delta parallel robot
- Desktop Injection Molding Machine
- Desktop injection molding machines
- Desktop Molding Machine
- desktop plastic injection machine
- Desktop Plastic Injection Molding Machine
- direct clamp injection molding machine
- Direct clamp injection molding machines
- Dosing & mixing system
- Drilling Centers
- Drying and dehumidification system
- drying and dehumidifying equipment
- Drying and Dehumidifying System
- drying system
- effective and efficient. Cabinet dryers are also used in other industries where large quantities of material need to be dried
- efficient injection molding machine
- elbow hydraulic injection molding machines
- electric injection molding machine
- electric injection molding machines
- energy-efficient injection molding robot
- energy-saving injection molding machine
- etc. Among injection molding robots
- exhibition
- features of CNC machine
- Feeding And Conveying System
- Five Axis Machine Center
- Fully automatic injection molding machine
- Gathering Topstar
- giant injection molding machine
- GMU-600 5-Axis Machining Center
- Granulating & Recycling System
- Heavy duty injection molding machine
- High-precision electric molding machines
- high-precision plastic molding machines
- high-speed all electric injection molding machine
- Honeycomb rotor dehumidifier
- horizontal injection molding machine
- Horizontal Injection Molding Machines
- Horizontal Injection Moulding Machine
- Horizontal Mixer manufacturer
- How The CNC Machine Works
- hybrid injection molding machine
- hydraulic injection molding machine
- Hydraulic Injection Molding Machines
- in this article
- Industrial robot
- Industrial Robot Chinese brand
- industrial robot parts
- industrial robot supplier
- Industrial robots
- Industry Chain
- Injection Manipulator
- injection manipulator robot
- injection mold machines
- Injection molding
- Injection molding automation
- Injection Molding Automation Solution
- injection molding dryer
- Injection molding equipment
- injection molding hopper dryer
- Injection molding machine
- injection molding machine brand
- Injection Molding Machine Factory
- Injection Molding Machine Manufacture
- Injection molding machine manufacturer
- injection molding machine manufacturers
- Injection molding machine procurement
- injection molding machine robotic arm
- injection molding machine with a robot
- Injection molding machines
- injection molding material dehumidifying
- injection molding plant
- Injection Molding Robot
- injection molding robot arm
- Injection molding robot automation
- Injection molding robotic arm
- injection molding robots
- Injection moulding machine
- Injection Moulding Robots
- Injection Robot
- Injection robot arm
- Injection robot manufacturer
- Injection robot wholesale
- injection robots
- intelligent injection molding machines
- Introducing Injection Robot
- It is the best choice for drying large quantities of material at once. Cabinetmakers use these machines because they are fast
- large injection molding machine
- large injection molding machines
- Learn what industrial automation and robotics is
- linear robot
- linear robots
- low speed sound-proof granulator
- machine plastic molding
- make sure to add some! Improvements (2) Keyphrase in introduction: Your keyphrase or its synonyms appear in the first paragraph of the copy
- manipulator machine
- manufacturing
- medical grade injection molding machines
- medical injection molding machine
- medical injection molding machines
- micro injection molding machine
- middle speed granulator
- Mini CNC machine manufacturers.
- Mold Temperature Control System
- mold temperature controller
- mold temperature controllers
- molding material Dehumidifying System
- mould temperature control system
- mould temperature controller
- mould temperature controllers
- New electric injection molding machine
- nitrogen dryer manufacturer
- nitrogen dryer system manufacturer
- Oil type mold temperature controller
- Oil type mold temperature controllers
- open day
- Outbound links: No outbound links appear in this page. Add some! Images: No images appear on this page. Add some! Internal links: No internal links appear in this page
- PET Preform injection molding
- phone case maker machine
- phone case making machine
- plastic bottle making machine
- plastic bottle manufacturing
- plastic bucket making machine
- plastic bucket manufacturing
- Plastic chair making machine
- plastic forming equipment
- plastic hopper dryer
- plastic injection machine
- plastic injection machines
- plastic injection molding
- Plastic injection molding equipment
- Plastic injection molding machine
- Plastic Injection Molding Machines
- plastic injection moulding machine
- plastic injection robot
- Plastic Molding machine
- Plastic Molding Machines
- plastic molding press
- plastic moulding machine
- plastic phone case making machine
- plastic-molding machine
- powerful granulator
- Powerful Type Sound-Proof Granulator
- precision injection molding
- precision injection molding machines
- production of plastic seats
- pure water mould temperature controller
- Robot injection molding
- robot injection molding machine
- robot manufacturing companies
- Robotic arm for injection molding machine
- robotic injection molding machines
- robotics in injection molding
- SCARA robot
- SCARA robots
- Service-oriented manufacturing
- Servo Cylinder Robot
- servo driven robot
- Servo Driven Robots
- servo injection robots
- servo motor-driven linear robots
- servo-driven 3-axis robot
- Servo-Driven Robot
- Setup of injection machine
- Silicone Injection Molding Machine
- six-axis industrial robot
- Stainless Hopper Dryer
- Stainless Hopper Dryers
- star club
- swing arm robot
- take-out robots
- the choice between servo-driven robots and hydraulic robots will have a certain impact on efficiency
- the most popular injection molding machine
- the type of injection molding robot
- toggle clamp injection molding machine
- Toggle Hydraulic Injection Molding Machines
- toggle injection molding machine
- Top 10 brands of injection robots
- Topstar
- Topstar Engineering
- Topstar Industrial Robots
- Topstar injection molding intelligent
- Topstar Scara Robots
- Useful Injection molding machine
- Vertical machining centers
- volumetric type blender
- water chiller
- water chillers
- water distributor
- water type mold temperature controller
- Water Type MoldTemperature Controller
- Water-Type Mould Temperature Controllers
- We often face choices when performing injection molding. We will choose the type of injection molding machine
- wholesale of injection molding machines
- x carve CNC
- 热门查询 点击次数 展示 排名 topstar