Why to Consider a Vertical Machine Center?
2022/08/14 By Topstar
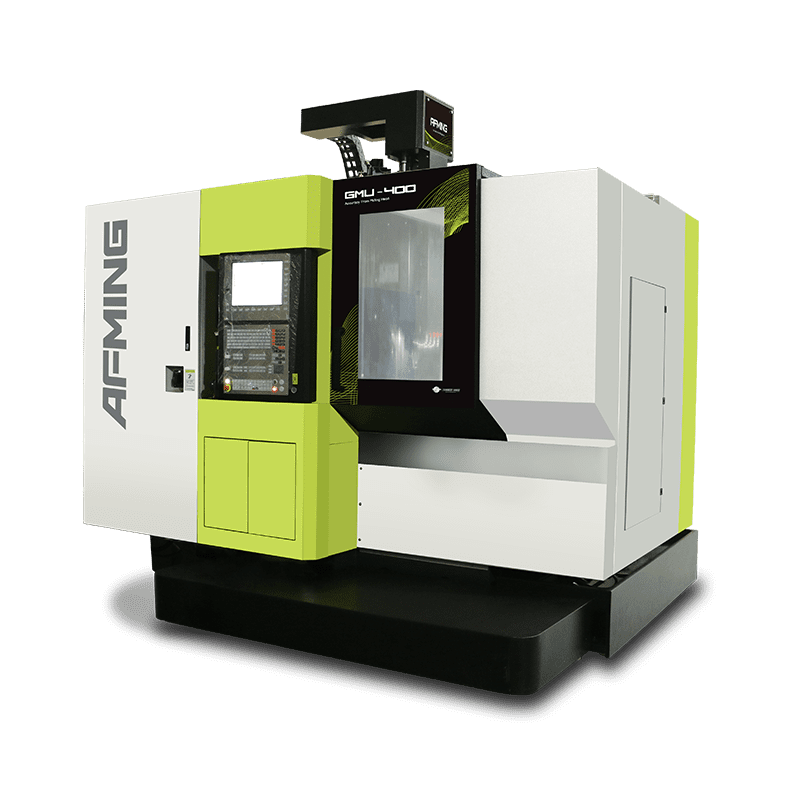
A numerically controlled Vertical Machine Center is a tool that features vertically oriented spindles and approach workpieces mounted on worktables from the top. Vertical Machine Center is ideal for processing workpieces with great accuracy and precision, even when they require many processes and have complex designs.
What is Vertical Machine Center?
Vertical Machine Center is a tool used to carry out a variety of operations, including milling, boring, drilling, tapping, and thread cutting. These tools are used in VMCs. A VMC is frequently employed in the manufacturing sector for the high-precision fabrication of parts for flatwork that calls for tool access from the top, such as mold and die cavities and sizable plane parts.
The spindle axis of vertical machining centers is vertically orientated. It revolves on its axis while having its milling cutters held in the spindle. The material to be treated will be supported on a table in a CNC vertical milling center while the cylinder-shaped blades are mounted perpendicularly over the spindle axis.
What is a VMC Machine?
VMC machines typically consist of three components: the x, y, and z-axis, in which the cutter remains upright. An axis is the number of motors that can be individually controlled to control a tool’s location. The x-axis moves from right to leave, the y-axis moves to and fro, and the z-axis moves up and down.
VMCs can have more than three axes; adding a fourth or fifth axis can boost the VMC’s advantages. Ancillary equipment and rotary indexers permit four-axes or five-axes machining work that increases the versatility and capability of VMC machines.
The addition of the fourth axis enables the cutter to spin around the x-axis, enabling the VMC machine to drill holes in the product’s front and back. The fifth axis can further complicate the machine.
Vertical Machine Center typically produces a metal cutting tool for forming steel, aluminum, and other hard materials into precisely shaped or machined surfaces. It is employed in several high precision, mass production, and machinery manufacturing industries, including automotive, handicrafts, mold making, defense products, electronics, electrical, lighting, and textile.
Applications & Uses for VMC Machines
CNC Vertical Machining Center can be used to fabricate machinery for trades that require extraordinary levels of accuracy. It is used in mass production, including locomotives, equipment, fabric, microelectronics, soldierly products, handicrafts, etc. VMC is an excellent option for manufacturing workpieces demanding high precision and complex forms.
Box Type CNC Machining Parts
Box CNC machinery parts, such as gearboxes, engine blocks, spindle boxes, diesel engine blocks, etc., refer to the workpiece with more than a sole hole system and numerous fissures inside. These parts are typically used in machine tools, cars, and airplanes.
Due to the high accuracy, productivity, stiffness, and programming tool change mechanism of CNC VMC. Many problems in machining box-type parts can be solved. It is valid if the process flow is well-designed and the right fixtures and tools are employed.
Extensive Curved Parts
Cams, integrated engine impellers, propellers, mold cavities, and other complicated curved surfaces are frequently utilized in the aviation and transportation sectors.
It is a challenge to use traditional machine tools or precision casting to obtain the required machining accuracy and identify these parts. Because they have complex curves, irregular surfaces, or closed cavities
The automatic machining of complex parts is made simple by a multi Axes machining center equipped with auto. Programmed technology and specialized apparatuses can significantly increase fabrication competence and guarantee surface form correctness.
Plate, Sleeve & Board Components
Keyway and radial holes are frequently present in this form of the workpiece. Vertical machining centers are ordinarily used for making objects with radial holes. In contrast, horizontal machining centers are often used for parts with end faces with hole systems or curved plates and shafts, such as shaft sleeves, plates with numerous holes, and motor covers.
Test Production Components
The machining center is highly flexible and adaptable. You can only create and input new programs when the machining item changes. Occasionally modifying specific programmed segments or using special instructions.
For instance, by using the Zooming Feature. It is possible to obtain machine parts with identical shapes but diverse sizes, which is appropriate for the production process and new artifact trials. It also significantly reduces the time needed for production planning and trial manufacturing.
How Vertical Machine Center Works?
A rotating spindle that can accommodate various cutting tools and is perpendicular to the table or work area is one of the significant elements of a VMC. The workpiece is also linked to a moveable work table by various fittings. Including machined aluminum plates or strong clamping vices, or they may be attached directly.
The tool changer realizes various operations, from rough cutting to fine-hole tedious, and the computer automatically controls the whole process. Significantly improves VMC efficiency. Coolant systems are also required to keep components and cutters cold and lubricated. Most VMCs employ soluble oil and water as their coolant system, although other liquids may also be used.
Various chip augers and conveyors are used to remove the chips from the work area, which boosts productivity and decreases downtime associated with manually shoveling away waste chips. It also provides a full cover or shell to reduce the splash generated by milling operations. And protect the environment during processing.
Adding shuttle tables or other automatic component loading systems is an excellent way to boost productivity. Reduce downtime, and extend the spindle’s “ON” time in most VMC systems.
I suggest you visit Topstar.
Vertical Machine Center is a less expensive, adaptable, affordable, effective, and extensively used tool in the market. And as technology develops, Topstar provides room for more advanced features to boost the VMC’s productivity. I recommend you visit Topstar to buy reliable. Inexpensive and worthwhile CNC Machine Tools.
TRENDING POSTS
- What factors can cause delays in the injection molding process of plastic molding machine? 2022/08/14
- Exhibition Review| Topstar participates in InterPlas Thailand 2024 2022/08/14
- Star Case | Topstar helps Santong upgrade its intelligent plant 2022/08/14
- Topstar Special | National Science and Technology Workers Day 2022/08/14
HOT TOPIC
- .ervo motor-driven linear robots
- 3 axis robot
- 3 axis robots
- 3 in 1 Compact Dehumidifying Dryer
- 3-axis robot
- 3-axis robots
- 5-axis CNC machine
- accuracy
- Air Chillers
- all electric injection molding machine
- all electric injection molding machines
- All-electric injection molding machines
- and overall production quality. Therefore
- AP-RubberPlas
- automated injection molding machine
- Automation changed engineering
- automation of injection molding robots
- auxiliary machine
- Bench Injection Molding Machine
- Cabinet dryer manufacturers
- Cabinet dryers
- chiller
- CNC Drilling Machine
- CNC Drilling Machines
- cnc engraving machine manufacturer
- cnc laser cutting machine manufacturer
- CNC machine
- CNC Machine Center
- CNC Machine for Sale
- CNC Machine Manufacturing
- CNC Machine Tool
- CNC machine tool product
- CNC Machining Center
- CNC wood carving machine
- Cooling system
- Cross-Walking Single Axis Servo Cylinder Robot
- Cross-Walking Single-Axis Servo Cylinder Robot
- Cross-Walking Three-Axis/Five-Axis Servo Driven Robot
- cross-walking three-axis/five-axis servo-driven robot
- Dehumidifier Dryer
- Dehumidifying Dryer
- delta parallel robot
- Desktop Injection Molding Machine
- Desktop injection molding machines
- Desktop Molding Machine
- desktop plastic injection machine
- Desktop Plastic Injection Molding Machine
- direct clamp injection molding machine
- Direct clamp injection molding machines
- Dosing & mixing system
- Drilling Centers
- Drying and dehumidification system
- drying and dehumidifying equipment
- Drying and Dehumidifying System
- drying system
- effective and efficient. Cabinet dryers are also used in other industries where large quantities of material need to be dried
- efficient injection molding machine
- elbow hydraulic injection molding machines
- electric injection molding machine
- electric injection molding machines
- energy-efficient injection molding robot
- energy-saving injection molding machine
- etc. Among injection molding robots
- exhibition
- features of CNC machine
- Feeding And Conveying System
- Five Axis Machine Center
- Fully automatic injection molding machine
- Gathering Topstar
- giant injection molding machine
- GMU-600 5-Axis Machining Center
- Granulating & Recycling System
- Heavy duty injection molding machine
- High-precision electric molding machines
- high-precision plastic molding machines
- high-speed all electric injection molding machine
- Honeycomb rotor dehumidifier
- horizontal injection molding machine
- Horizontal Injection Molding Machines
- Horizontal Injection Moulding Machine
- Horizontal Mixer manufacturer
- How The CNC Machine Works
- hybrid injection molding machine
- hydraulic injection molding machine
- Hydraulic Injection Molding Machines
- in this article
- Industrial robot
- Industrial Robot Chinese brand
- industrial robot parts
- industrial robot supplier
- Industrial robots
- Industry Chain
- Injection Manipulator
- injection manipulator robot
- injection mold machines
- Injection molding
- Injection molding automation
- Injection Molding Automation Solution
- injection molding dryer
- Injection molding equipment
- injection molding hopper dryer
- Injection molding machine
- injection molding machine brand
- Injection Molding Machine Factory
- Injection Molding Machine Manufacture
- Injection molding machine manufacturer
- injection molding machine manufacturers
- Injection molding machine procurement
- injection molding machine robotic arm
- injection molding machine with a robot
- Injection molding machines
- injection molding material dehumidifying
- injection molding plant
- Injection Molding Robot
- injection molding robot arm
- Injection molding robot automation
- Injection molding robotic arm
- injection molding robots
- Injection moulding machine
- Injection Moulding Robots
- Injection Robot
- Injection robot arm
- Injection robot manufacturer
- Injection robot wholesale
- injection robots
- intelligent injection molding machines
- Introducing Injection Robot
- It is the best choice for drying large quantities of material at once. Cabinetmakers use these machines because they are fast
- large injection molding machine
- large injection molding machines
- Learn what industrial automation and robotics is
- linear robot
- linear robots
- low speed sound-proof granulator
- machine plastic molding
- make sure to add some! Improvements (2) Keyphrase in introduction: Your keyphrase or its synonyms appear in the first paragraph of the copy
- manipulator machine
- manufacturing
- medical grade injection molding machines
- medical injection molding machine
- medical injection molding machines
- micro injection molding machine
- middle speed granulator
- Mini CNC machine manufacturers.
- Mold Temperature Control System
- mold temperature controller
- mold temperature controllers
- molding material Dehumidifying System
- mould temperature control system
- mould temperature controller
- mould temperature controllers
- New electric injection molding machine
- nitrogen dryer manufacturer
- nitrogen dryer system manufacturer
- Oil type mold temperature controller
- Oil type mold temperature controllers
- open day
- Outbound links: No outbound links appear in this page. Add some! Images: No images appear on this page. Add some! Internal links: No internal links appear in this page
- PET Preform injection molding
- phone case maker machine
- phone case making machine
- plastic bottle making machine
- plastic bottle manufacturing
- plastic bucket making machine
- plastic bucket manufacturing
- Plastic chair making machine
- plastic forming equipment
- plastic hopper dryer
- plastic injection machine
- plastic injection machines
- plastic injection molding
- Plastic injection molding equipment
- Plastic injection molding machine
- Plastic Injection Molding Machines
- plastic injection moulding machine
- plastic injection robot
- Plastic Molding machine
- Plastic Molding Machines
- plastic molding press
- plastic moulding machine
- plastic phone case making machine
- plastic-molding machine
- powerful granulator
- Powerful Type Sound-Proof Granulator
- precision injection molding
- precision injection molding machines
- production of plastic seats
- pure water mould temperature controller
- Robot injection molding
- robot injection molding machine
- robot manufacturing companies
- Robotic arm for injection molding machine
- robotic injection molding machines
- robotics in injection molding
- SCARA robot
- SCARA robots
- Service-oriented manufacturing
- Servo Cylinder Robot
- servo driven robot
- Servo Driven Robots
- servo injection robots
- servo motor-driven linear robots
- servo-driven 3-axis robot
- Servo-Driven Robot
- Setup of injection machine
- Silicone Injection Molding Machine
- six-axis industrial robot
- Stainless Hopper Dryer
- Stainless Hopper Dryers
- star club
- swing arm robot
- take-out robots
- the choice between servo-driven robots and hydraulic robots will have a certain impact on efficiency
- the most popular injection molding machine
- the type of injection molding robot
- toggle clamp injection molding machine
- Toggle Hydraulic Injection Molding Machines
- toggle injection molding machine
- Top 10 brands of injection robots
- Topstar
- Topstar Engineering
- Topstar Industrial Robots
- Topstar injection molding intelligent
- Topstar Scara Robots
- Useful Injection molding machine
- Vertical machining centers
- volumetric type blender
- water chiller
- water chillers
- water distributor
- water type mold temperature controller
- Water Type MoldTemperature Controller
- Water-Type Mould Temperature Controllers
- We often face choices when performing injection molding. We will choose the type of injection molding machine
- wholesale of injection molding machines
- x carve CNC