Do different types of mold temperature controllers have an impact on injection molding machines?
- Injection molding machines
- mold temperature controller
- Oil type mold temperature controllers
- Plastic injection molding machine
- water type mold temperature controller
2025/05/16 By Topstar
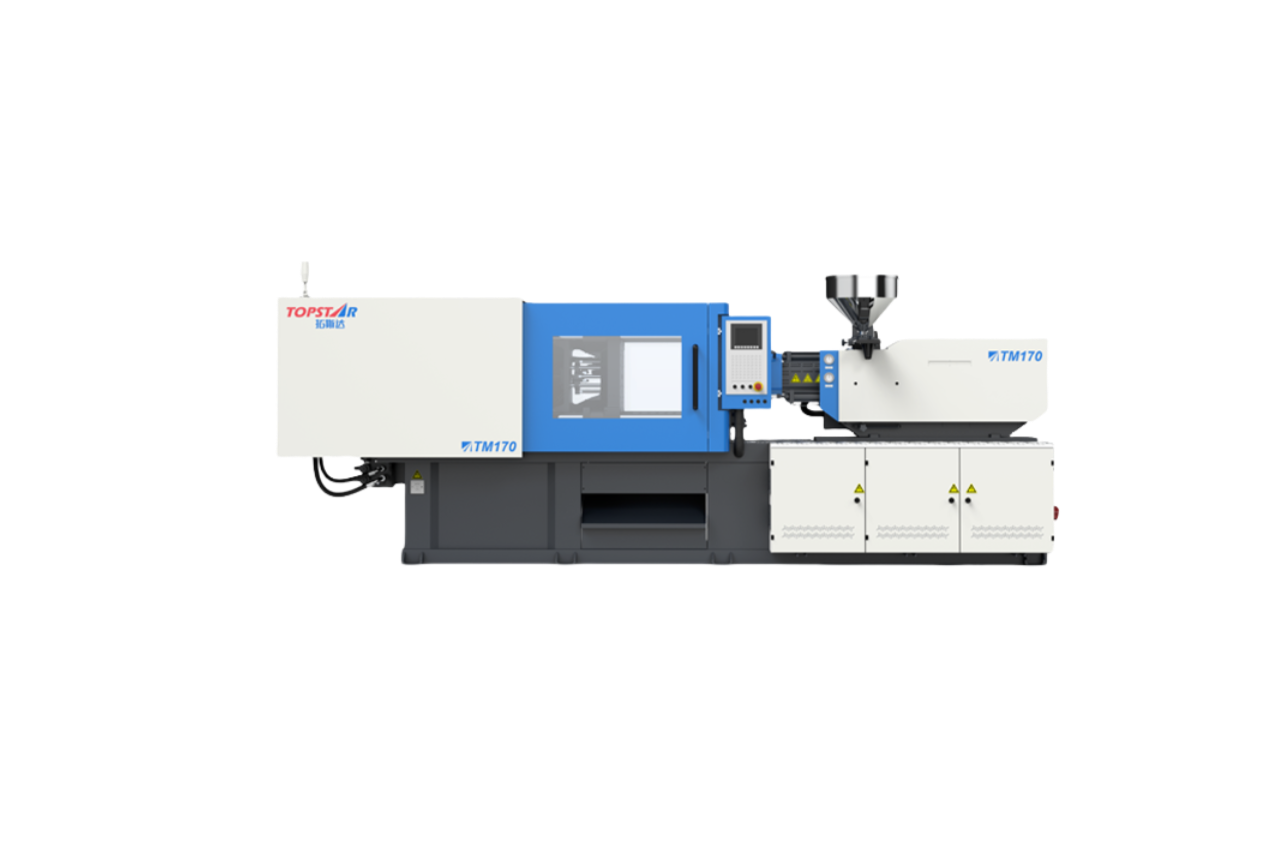
When communicating with customers at offline exhibitions and online, they often ask us questions about the impact of various mold temperature controllers on injection molding machines. As an injection molding machine manufacturer, choosing a water type or oil type mold temperature controller can significantly affect plastic injection molding machines‘ performance and production profitability. Water type mold temperature controllers perform well in the temperature range of 120°C to 180°C, using deionized water or fast heat transfer at process temperatures. Oil type mold temperature controllers operate between 200°C and 320°C, using thermally stable heat transfer oil to withstand high-temperature applications. Either type of mold temperature controller can be connected to Topstar’s injection molding machines through a dedicated control system, and there is no communication problem between the devices.
Impact of using a water type mold temperature controller with injection molding machines
When integrated with a plastic injection molding machine, a water type mold temperature controller provides fast ramping speeds at moderate temperatures, making it the first choice for thermoplastics such as PP, PE, and ABS. Their high specific heat capacity and low fluid viscosity ensure uniform temperature distribution across the mold surface, minimizing thermal gradients that can cause warpage, sink marks, or residual stresses in the final part. At the same time, water-type temperature controllers are compatible with the control systems of Topstar injection molding machines, and the PID control of water-type temperature controllers ensures temperature stability of ±0.1°C, which is critical for delicate parts such as optical or medical housings.
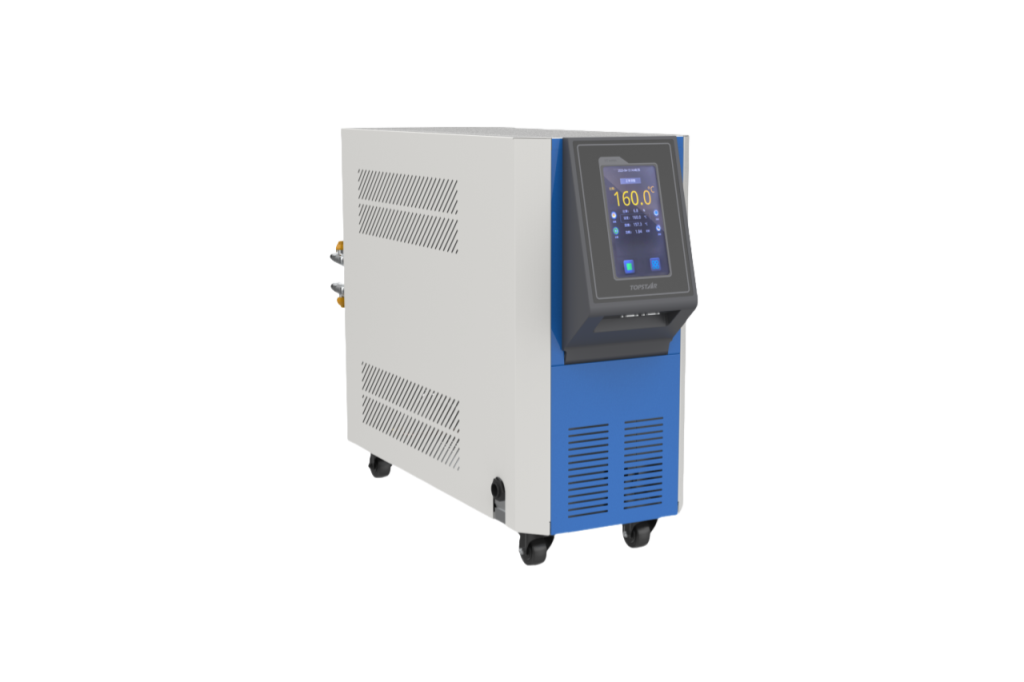
High-precision filters can simplify maintenance and regularly replace water treatment chemicals to prevent corrosion and biological growth, for operations focusing on medium and low temperature molds, such as consumer goods, toys, and automotive interior parts, water-type temperature controllers combined with plastic injection molding machines provide reliable and cost-effective performance.
Impact of using oil type temperature controllers with injection molding machines
Oil type temperature controllers are more suitable when using injection molding machines to produce PC, LCP, PEEK, and die casting processes. They can maintain mold temperatures between 200°C and 320°C, ensuring smooth melt flow, well-developed crystal structure, and excellent surface finish. At the same time, it can bring precise temperature control, rapid heating, and cooling. In addition, to ensure safe use, the oil type mold temperature controller adopts an electrical box separation design to isolate the high temperature conduction in the chassis and effectively protect the electrical components.
In addition, the problem of natural wear and leakage of the shaft seal is solved by a magnetic drive pump, and an over-temperature protection switch is standard in the motor coil to prevent the motor from overheating and burning, reduce the failure rate, and reduce the risk of accidental contact by personnel. They are usually widely used in fields requiring strict tolerances and excellent mechanical properties.
Impact on cycle time and production efficiency
The right mold temperature controller directly affects the cycle time efficiency of the injection molding machine. Water type controllers have the characteristics of rapid heat exchange, which can shorten the preheating and cooling stages of low-temperature molds by up to 20%, thereby significantly increasing the output of injection molding machines. However, due to the boiling point of water and system pressure limitations, their performance will decrease above 180°C. In contrast, oil-type controllers maintain consistent high-temperature control, prevent overcooling of critical thin-walled parts, and eliminate rework related to incomplete filling or cold materials.

Despite slower cooling rates than water type temperature controllers, the advanced cooling circuits and heat exchangers integrated into Topstar’s temperature controllers mitigate these effects, providing balanced cycle times under various processing conditions. Actual case studies have shown that high-volume manufacturers who switch to optimized temperature controllers can reduce overall cycle times by 5-10%, directly translating into increased daily output and revenue.
Energy Consumption and Cost Considerations
Of course, energy efficiency is an area of concern for any injection molding manufacturer. Water type mold temperature controllers typically consume less power when used with all electric injection molding machines, up to 15% less, because water’s higher specific heat capacity requires less energy to maintain target temperatures between 120°C and 180°C.
In contrast, oil type temperature controllers require more energy to heat and circulate the viscous oil, especially at temperatures above 250°C. However, the total cost of ownership must also consider the increased machine uptime and reduced scrap rates that oil type systems can provide in producing high-performance polymers. We advise our customers to conduct a comprehensive cost analysis and find that water type temperature controllers can achieve a quick return on investment when used with all electric injection molding machines for standard commodity plastic production. In contrast, oil type temperature controllers can maximize production and part performance for special applications, offsetting higher operating costs.
Maintenance, Safety, and Reliability
The synergy between mold temperature controllers and injection molding machines extends to strict maintenance and safety procedures. Water type mold temperature controllers require regular filter changes, coolant quality checks, and monitoring of corrosion inhibitors to prevent scale buildup and microbial growth. Oil type cooling requires regular oil sampling, particle contamination analysis, and filter changes to remove oxidation byproducts and ensure thermal stability. Topstar injection molding machines have an integrated alarm system connected to the controller sensors to automatically shut down during coolant loss, overpressure, or temperature exceedance. Our recommended maintenance intervals are once a quarter for water type mold temperature controllers and once every two years for oil type mold temperature controllers to ensure operational reliability, protect hydraulic seals, and prevent unexpected downtime.
Choose based on machine type and material.
The choice of water and oil type temperature controllers can significantly affect the performance of the injection molding machine. Water-based systems excel at low to medium temperatures (120°C to 180°C), enabling fast cycle times, reduced energy consumption, and simplified maintenance. Oil type temperature controllers provide stable high temperature control (200°C – 320°C), which is suitable for injection molding engineering polymers requiring thermal uniformity and die casting processes. We recommend that you choose based on the injection molding machine you already have, material properties, production volume, cycle time goals, and total cost of ownership goals.
TRENDING POSTS
- What factors can cause delays in the injection molding process of plastic molding machine? 2025/05/16
- Exhibition Review| Topstar participates in InterPlas Thailand 2024 2025/05/16
- Star Case | Topstar helps Santong upgrade its intelligent plant 2025/05/16
- Topstar Special | National Science and Technology Workers Day 2025/05/16
HOT TOPIC
- .ervo motor-driven linear robots
- 1.0 guangdong topstar technology co. ltd
- 1.0 topstar china
- 1.0 topstar robot
- 11
- 2
- 21
- 23
- 3 axis robot
- 3 axis robots
- 3 in 1 Compact Dehumidifying Dryer
- 3-axis robot
- 3-axis robots
- 39
- 41
- 5-axis CNC machine
- 62
- accuracy
- Air Chillers
- all electric injection molding machine
- all electric injection molding machines
- All-electric injection molding machines
- and overall production quality. Therefore
- AP-RubberPlas
- automated injection molding machine
- Automation changed engineering
- automation of injection molding robots
- auxiliary machine
- Bench Injection Molding Machine
- Cabinet dryer manufacturers
- Cabinet dryers
- chiller
- CNC Drilling Machine
- CNC Drilling Machines
- cnc engraving machine manufacturer
- cnc laser cutting machine manufacturer
- CNC machine
- CNC Machine Center
- CNC Machine for Sale
- CNC Machine Manufacturing
- CNC Machine Tool
- CNC machine tool product
- CNC Machining Center
- CNC wood carving machine
- Cooling system
- Cross-Walking Single Axis Servo Cylinder Robot
- Cross-Walking Single-Axis Servo Cylinder Robot
- Cross-Walking Three-Axis/Five-Axis Servo Driven Robot
- cross-walking three-axis/five-axis servo-driven robot
- Dehumidifier Dryer
- Dehumidifying Dryer
- delta parallel robot
- Desktop Injection Molding Machine
- Desktop injection molding machines
- Desktop Molding Machine
- desktop plastic injection machine
- Desktop Plastic Injection Molding Machine
- direct clamp injection molding machine
- Direct clamp injection molding machines
- Dosing & mixing system
- Drilling Centers
- Drying and dehumidification system
- drying and dehumidifying equipment
- Drying and Dehumidifying System
- drying system
- effective and efficient. Cabinet dryers are also used in other industries where large quantities of material need to be dried
- efficient injection molding machine
- elbow hydraulic injection molding machines
- electric injection molding machine
- electric injection molding machines
- energy-efficient injection molding robot
- energy-efficient water chiller
- energy-efficient water chillers
- energy-saving injection molding machine
- etc. Among injection molding robots
- exhibition
- features of CNC machine
- Feeding And Conveying System
- Five Axis Machine Center
- Fully automatic injection molding machine
- Gathering Topstar
- giant injection molding machine
- GMU-600 5-Axis Machining Center
- Granulating & Recycling System
- Heavy duty injection molding machine
- High-precision electric molding machines
- high-precision plastic molding machines
- high-speed all electric injection molding machine
- high-speed electric injection molding machine
- High-Speed Packaging Injection Molding
- Honeycomb rotor dehumidifier
- horizontal injection molding machine
- Horizontal Injection Molding Machines
- Horizontal Injection Moulding Machine
- Horizontal Mixer manufacturer
- How The CNC Machine Works
- hybrid injection molding machine
- hydraulic injection molding machine
- Hydraulic Injection Molding Machines
- in this article
- Industrial robot
- Industrial Robot Chinese brand
- industrial robot parts
- industrial robot supplier
- Industrial robots
- Industry Chain
- Injection Manipulator
- injection manipulator robot
- injection mold machines
- Injection molding
- Injection molding automation
- Injection Molding Automation Solution
- injection molding dryer
- Injection molding equipment
- injection molding hopper dryer
- Injection molding machine
- injection molding machine brand
- Injection Molding Machine Factory
- Injection Molding Machine Manufacture
- Injection molding machine manufacturer
- injection molding machine manufacturers
- Injection molding machine procurement
- injection molding machine robotic arm
- injection molding machine with a robot
- Injection molding machines
- injection molding material dehumidifying
- injection molding plant
- injection molding process
- Injection Molding Robot
- injection molding robot arm
- Injection molding robot automation
- Injection molding robotic arm
- injection molding robots
- Injection moulding machine
- injection moulding machines
- Injection Moulding Robots
- Injection Robot
- Injection robot arm
- Injection robot manufacturer
- Injection robot wholesale
- injection robots
- intelligent injection molding machines
- Intelligent mould temperature controller
- Introducing Injection Robot
- It is the best choice for drying large quantities of material at once. Cabinetmakers use these machines because they are fast
- Large flow water type mold temperature controller
- large injection molding machine
- large injection molding machines
- Learn what industrial automation and robotics is
- linear robot
- linear robots
- low speed sound-proof granulator
- machine plastic molding
- make sure to add some! Improvements (2) Keyphrase in introduction: Your keyphrase or its synonyms appear in the first paragraph of the copy
- manipulator machine
- manufacturing
- medical grade injection molding machines
- medical injection molding machine
- medical injection molding machines
- micro injection molding machine
- middle speed granulator
- Mini CNC machine manufacturers.
- Mold Temperature Control System
- mold temperature controller
- mold temperature controllers
- molding material Dehumidifying System
- mould temperature control system
- mould temperature controller
- mould temperature controllers
- New electric injection molding machine
- nitrogen dryer manufacturer
- nitrogen dryer system manufacturer
- Oil type mold temperature controller
- Oil type mold temperature controllers
- open day
- Outbound links: No outbound links appear in this page. Add some! Images: No images appear on this page. Add some! Internal links: No internal links appear in this page
- PET Preform injection molding
- phone case maker machine
- phone case making machine
- phone cover making machine
- plastic bottle making machine
- plastic bottle manufacturing
- plastic bucket making machine
- plastic bucket manufacturing
- Plastic chair making machine
- plastic forming equipment
- plastic hopper dryer
- plastic injection machine
- plastic injection machines
- plastic injection molding
- Plastic injection molding equipment
- Plastic injection molding machine
- Plastic Injection Molding Machines
- plastic injection moulding machine
- plastic injection moulding machines
- plastic injection robot
- plastic molding
- Plastic Molding machine
- plastic molding machine 1
- Plastic Molding Machines
- plastic molding press
- plastic moulding machine
- plastic phone case making machine
- plastic-molding machine
- powerful granulator
- Powerful Type Sound-Proof Granulator
- precision injection molding
- precision injection molding machines
- production of plastic seats
- pure water mould temperature controller
- Robot injection molding
- robot injection molding machine
- robot manufacturing companies
- Robotic arm for injection molding machine
- robotic injection molding machines
- robotics in injection molding
- SCARA robot
- SCARA robots
- Service-oriented manufacturing
- Servo Cylinder Robot
- servo driven robot
- Servo Driven Robots
- servo injection molding machine
- servo injection robots
- servo motor-driven linear robots
- servo-driven 3-axis robot
- Servo-Driven Robot
- Setup of injection machine
- Silicone Injection Molding Machine
- six-axis industrial robot
- Stainless Hopper Dryer
- Stainless Hopper Dryers
- star club
- swing arm robot
- take-out robot
- take-out robots
- the choice between servo-driven robots and hydraulic robots will have a certain impact on efficiency
- the most popular injection molding machine
- the type of injection molding robot
- TMII injection molding machine
- toggle clamp injection molding machine
- Toggle Hydraulic Injection Molding Machines
- toggle injection molding machine
- Top 10 brands of injection robots
- Topstar
- Topstar Engineering
- Topstar Industrial Robots
- Topstar injection molding intelligent
- Topstar Scara Robots
- Useful Injection molding machine
- Vertical machining centers
- volumetric type blender
- water chiller
- water chillers
- water distributor
- water type mold temperature controller
- Water Type MoldTemperature Controller
- Water-Type Mould Temperature Controllers
- We often face choices when performing injection molding. We will choose the type of injection molding machine
- wholesale of injection molding machines
- x carve CNC
- 热门查询 点击次数 展示 排名 topstar