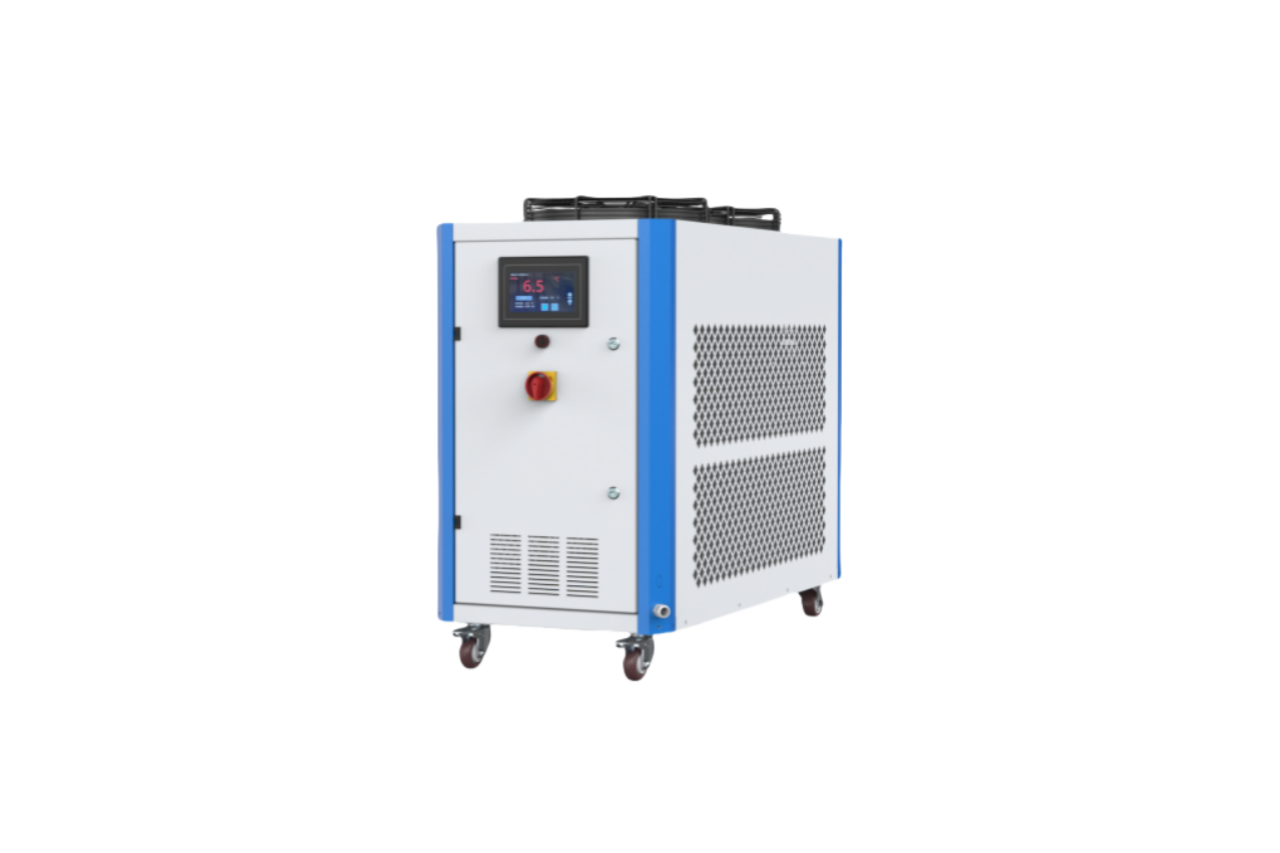
Water chillers that operate with injection molding machines must maintain a stable temperature and avoid unnecessary short cycling of the compressors to ensure optimal performance. Short cycling (i.e., frequent on and off of the compressor) shortens compressor life, increases energy consumption, and can cause system failures. We will examine how water chiller design can address short cycling issues through the use of fully computerized thermostats, precise temperature differentials, optimized cycle timers, and intelligent monitoring. And explain what short cycling is and why it happens.
Water chiller with fully computerized thermostat control
To prevent short cycling, Topstar equips the water chiller with a fully computerized thermostat that provides intuitive control and advanced algorithm protection. First, the operator sets the target water temperature, typically ranging from 5°C to 35°C, using a straightforward touch interface. Then, the controller maintains a precise temperature differential range (typically ±1°C) to avoid rapid on/off commands. Additionally, our engineers have set minimum on and off times in the thermostat to ensure that the compressor runs for at least three minutes per cycle and turns off only when necessary. At the same time, built-in alarms alert users in the event of sensor failure or drastic temperature fluctuations, making the injection molding chiller user-friendly and stable against short cycles even in complex process environments.
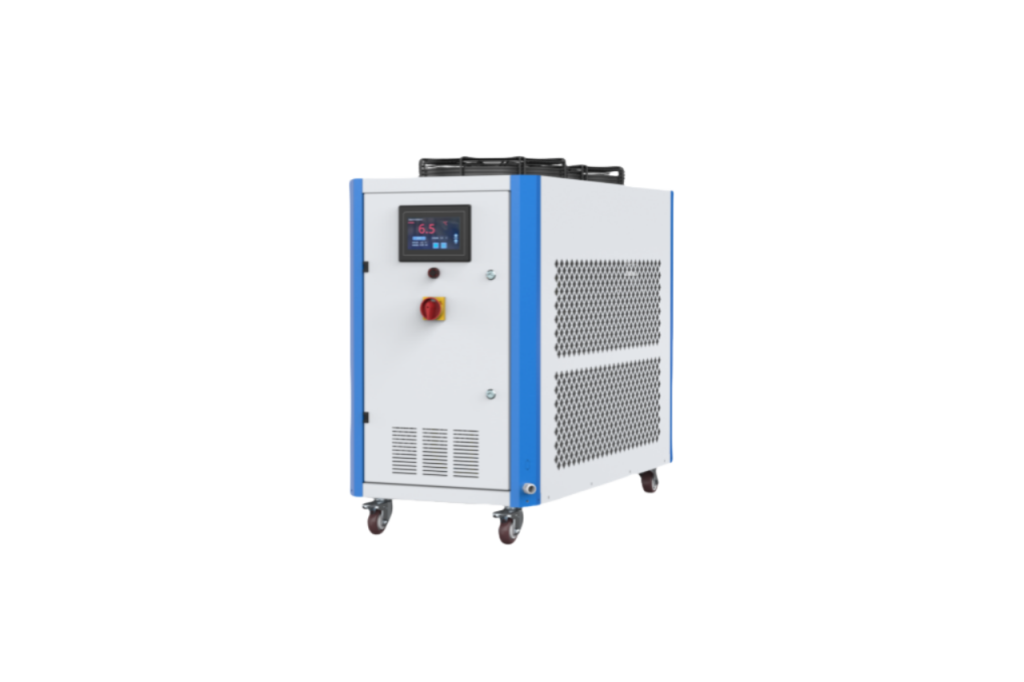
Accurate temperature range and differential settings
In any water chiller application, the start/stop threshold needs to be managed. For specific specialized applications, a low-temperature chiller must be used in conjunction with an injection molding machine. The low-temperature type is capable of delivering 3°C ice water, and the temperature difference will never exceed 2°C. For example, setting the water chiller to 10°C and establishing a hysteresis of 2°C means that the compressor will only stop when the water temperature reaches 12°C and restart only at 8 °C, thus avoiding rapid switching. Additionally, you can adjust these parameters in the integration to match process needs, mold cycle, times, and seasonal changes. This fine-tuning eliminates false trips caused by minor thermal fluctuations, ensuring that the compressor only cycles when system demand changes.
Optimize water flow and cycle time of the water chiller.
To prevent short cycles of the water chiller, proper control of water flow and temperature is also necessary. During the development of the chiller, I installed a variable-speed pump with a calibrated cycle speed of 10-20 L/min, depending on the mold size and heat load. Additionally, it is possible to monitor the flow sensor and set a minimum flow threshold, ensuring the compressor only operates when sufficient coolant flows through the heat exchanger. During the development and production process, a cycle timer is also configured to pause the compressor start if the flow rate falls below the set value, thereby reducing stress on the components and ensuring that our injection molding chiller operates only under optimal hydraulic conditions. This coordination between flow dynamics and cycle time significantly extends the compressor’s life and improves overall system stability.
Leveraging the efficiency of shell and tube condensers
To further stabilize the operation of the compressor, the Topstar chiller utilizes a shell and tube condenser, renowned for its rapid heat conduction and excellent heat dissipation performance. This sturdy tube bundle transfers heat efficiently even in warm ambient conditions, thereby maintaining low head pressure and stable compressor exhaust volume. I designed the condenser size 20% higher than the rated capacity of the water chiller to prevent pressure peaks that often trigger premature compressor shutdown or safety lockout. This efficient heat dissipation enables longer, smoother compressor cycles, reducing the risk of short cycling in demanding injection molding applications, especially on hot days.
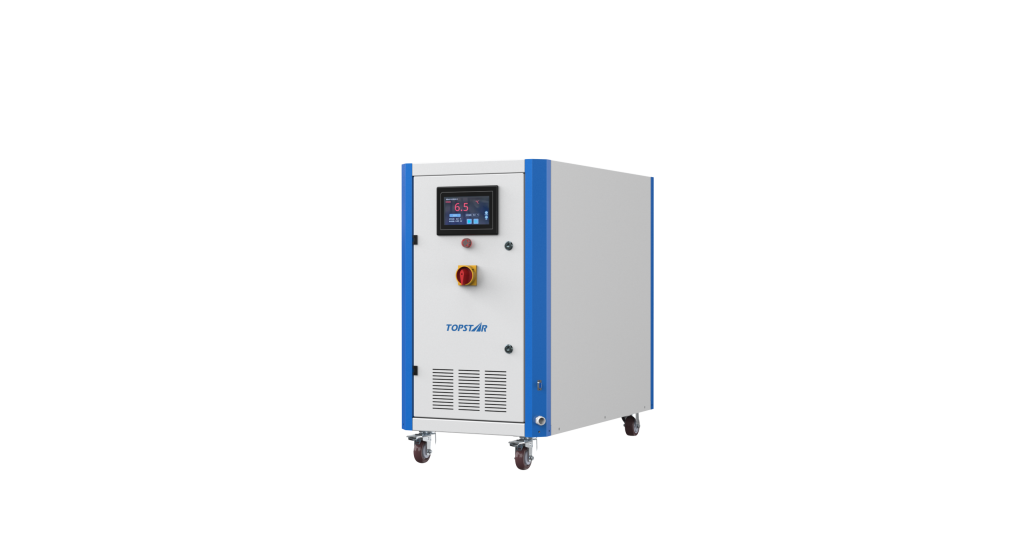
Implementing Anti-Short Cycle Timers and Safeguards
In addition to hardware improvements, I integrated anti-short-cycle timers and software safeguards into the water chiller’s control logic. For example, the system prohibits the compressor from restarting for at least two minutes after shutdown, thereby preventing rapid cycling due to minor temperature fluctuations. I also set a maximum cycle limit per hour (usually no more than six) to avoid excessive on/off events. Additionally, these controllers log every start and stop event, allowing the maintenance team to analyze cycling patterns. These programmable safeguards ensure that our injection molding chillers maintain predictable operation even when workloads fluctuate and protect their compressors from excessive wear.
Delivering Reliable, Stable Operation
Preventing chiller compressor short cycling requires a holistic approach, combining computer-controlled thermostats with precise temperature differential settings, optimized water flow control, efficient shell-and-tube condensers, and powerful anti-short-cycle timers and diagnostics. We take these factors into account in every water chiller we design to ensure stable compressor operation, improve energy efficiency, and extend equipment life.
TRENDING POSTS
- What factors can cause delays in the injection molding process of plastic molding machine? 2025/07/09
- Exhibition Review| Topstar participates in InterPlas Thailand 2024 2025/07/09
- Star Case | Topstar helps Santong upgrade its intelligent plant 2025/07/09
- Topstar Special | National Science and Technology Workers Day 2025/07/09
HOT TOPIC
- .ervo motor-driven linear robots
- 1.0 guangdong topstar technology co. ltd
- 1.0 topstar china
- 1.0 topstar robot
- 11
- 2
- 21
- 23
- 3 axis robot
- 3 axis robots
- 3 in 1 Compact Dehumidifying Dryer
- 3-axis robot
- 3-axis robots
- 39
- 41
- 5-axis CNC machine
- 62
- accuracy
- Air Chillers
- all electric injection molding machine
- all electric injection molding machines
- All-electric injection molding machines
- and overall production quality. Therefore
- AP-RubberPlas
- automated injection molding machine
- Automation changed engineering
- automation of injection molding robots
- auxiliary machine
- Bench Injection Molding Machine
- Cabinet dryer manufacturers
- Cabinet dryers
- chiller
- CNC Drilling Machine
- CNC Drilling Machines
- cnc engraving machine manufacturer
- cnc laser cutting machine manufacturer
- CNC machine
- CNC Machine Center
- CNC Machine for Sale
- CNC Machine Manufacturing
- CNC Machine Tool
- CNC machine tool product
- CNC Machining Center
- CNC wood carving machine
- Cooling system
- Cross-Walking Single Axis Servo Cylinder Robot
- Cross-Walking Single-Axis Servo Cylinder Robot
- Cross-Walking Three-Axis/Five-Axis Servo Driven Robot
- cross-walking three-axis/five-axis servo-driven robot
- Dehumidifier Dryer
- Dehumidifying Dryer
- delta parallel robot
- Desktop Injection Molding Machine
- Desktop injection molding machines
- Desktop Molding Machine
- desktop plastic injection machine
- Desktop Plastic Injection Molding Machine
- direct clamp injection molding machine
- Direct clamp injection molding machines
- Dosing & mixing system
- Drilling Centers
- Drying and dehumidification system
- drying and dehumidifying equipment
- Drying and Dehumidifying System
- drying system
- effective and efficient. Cabinet dryers are also used in other industries where large quantities of material need to be dried
- efficient injection molding machine
- elbow hydraulic injection molding machines
- electric injection molding machine
- electric injection molding machines
- energy-efficient injection molding robot
- energy-efficient water chiller
- energy-efficient water chillers
- energy-saving injection molding machine
- etc. Among injection molding robots
- exhibition
- features of CNC machine
- Feeding And Conveying System
- Five Axis Machine Center
- Fully automatic injection molding machine
- Gathering Topstar
- giant injection molding machine
- GMU-600 5-Axis Machining Center
- Granulating & Recycling System
- Heavy duty injection molding machine
- High-precision electric molding machines
- high-precision plastic molding machines
- high-speed all electric injection molding machine
- high-speed electric injection molding machine
- High-Speed Packaging Injection Molding
- Honeycomb rotor dehumidifier
- horizontal injection molding machine
- Horizontal Injection Molding Machines
- Horizontal Injection Moulding Machine
- Horizontal Mixer manufacturer
- How The CNC Machine Works
- hybrid injection molding machine
- hydraulic injection molding machine
- Hydraulic Injection Molding Machines
- in this article
- Industrial robot
- Industrial Robot Chinese brand
- industrial robot parts
- industrial robot supplier
- Industrial robots
- Industry Chain
- Injection Manipulator
- injection manipulator robot
- injection mold machines
- Injection molding
- Injection molding automation
- Injection Molding Automation Solution
- injection molding dryer
- Injection molding equipment
- injection molding hopper dryer
- Injection molding machine
- injection molding machine brand
- Injection Molding Machine Factory
- Injection Molding Machine Manufacture
- Injection molding machine manufacturer
- injection molding machine manufacturers
- Injection molding machine procurement
- injection molding machine robotic arm
- injection molding machine with a robot
- Injection molding machines
- injection molding material dehumidifying
- injection molding plant
- injection molding process
- Injection Molding Robot
- injection molding robot arm
- Injection molding robot automation
- Injection molding robotic arm
- injection molding robots
- Injection moulding machine
- injection moulding machines
- Injection Moulding Robots
- Injection Robot
- Injection robot arm
- Injection robot manufacturer
- Injection robot wholesale
- injection robots
- intelligent injection molding machines
- intelligent mold temperature
- intelligent mold temperature controller
- Intelligent mould temperature controller
- Introducing Injection Robot
- It is the best choice for drying large quantities of material at once. Cabinetmakers use these machines because they are fast
- Large flow water type mold temperature controller
- large injection molding machine
- large injection molding machines
- Learn what industrial automation and robotics is
- linear robot
- linear robots
- low speed sound-proof granulator
- machine plastic molding
- make sure to add some! Improvements (2) Keyphrase in introduction: Your keyphrase or its synonyms appear in the first paragraph of the copy
- manipulator machine
- manufacturing
- medical grade injection molding machines
- medical injection molding machine
- medical injection molding machines
- micro injection molding machine
- middle speed granulator
- Mini CNC machine manufacturers.
- Mold Temperature Control System
- mold temperature controller
- mold temperature controllers
- molding material Dehumidifying System
- mould temperature control system
- mould temperature controller
- mould temperature controllers
- New electric injection molding machine
- nitrogen dryer manufacturer
- nitrogen dryer system manufacturer
- Oil type mold temperature controller
- Oil type mold temperature controllers
- open day
- Outbound links: No outbound links appear in this page. Add some! Images: No images appear on this page. Add some! Internal links: No internal links appear in this page
- PET Preform injection molding
- phone case maker machine
- phone case making machine
- phone cover making machine
- plastic bottle making machine
- plastic bottle manufacturing
- plastic bucket making machine
- plastic bucket manufacturing
- Plastic chair making machine
- plastic forming equipment
- plastic hopper dryer
- plastic injection machine
- plastic injection machines
- plastic injection molding
- Plastic injection molding equipment
- Plastic injection molding machine
- Plastic Injection Molding Machines
- plastic injection moulding machine
- plastic injection moulding machines
- plastic injection robot
- plastic molding
- Plastic Molding machine
- plastic molding machine 1
- Plastic Molding Machines
- plastic molding press
- plastic moulding machine
- plastic phone case making machine
- plastic-molding machine
- powerful granulator
- Powerful Type Sound-Proof Granulator
- precision injection molding
- precision injection molding machines
- production of plastic seats
- pure water mould temperature controller
- Robot injection molding
- robot injection molding machine
- robot manufacturing companies
- Robotic arm for injection molding machine
- robotic injection molding machines
- robotics in injection molding
- SCARA robot
- SCARA robots
- Service-oriented manufacturing
- Servo Cylinder Robot
- servo driven robot
- Servo Driven Robots
- servo injection molding machine
- servo injection robots
- servo motor-driven linear robots
- servo-driven 3-axis robot
- Servo-Driven Robot
- Setup of injection machine
- Silicone Injection Molding Machine
- six-axis industrial robot
- Stainless Hopper Dryer
- Stainless Hopper Dryers
- star club
- swing arm robot
- take-out robot
- take-out robots
- the choice between servo-driven robots and hydraulic robots will have a certain impact on efficiency
- the most popular injection molding machine
- the type of injection molding robot
- TMII injection molding machine
- toggle clamp injection molding machine
- Toggle Hydraulic Injection Molding Machines
- toggle injection molding machine
- Top 10 brands of injection robots
- Topstar
- Topstar Engineering
- Topstar Industrial Robots
- Topstar injection molding intelligent
- Topstar Scara Robots
- Useful Injection molding machine
- Vertical machining centers
- volumetric type blender
- water chiller
- water chillers
- water distributor
- water type mold temperature controller
- Water Type MoldTemperature Controller
- Water-Type Mould Temperature Controllers
- We often face choices when performing injection molding. We will choose the type of injection molding machine
- wholesale of injection molding machines
- x carve CNC
- 热门查询 点击次数 展示 排名 topstar