Machine Injection Molding at Home: 8 Best Features
2022/01/13 By Topstar
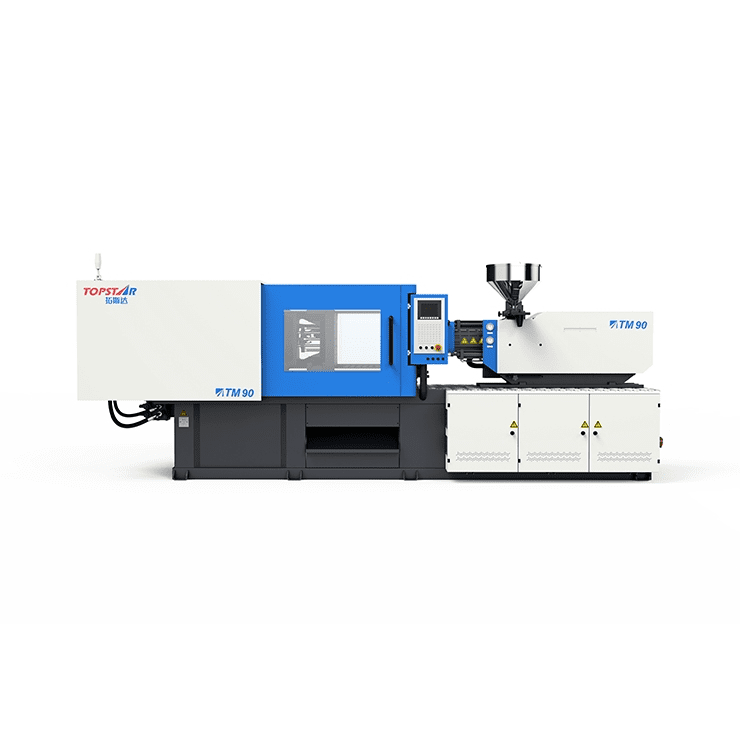
Plastic injection molding equipment
Plastic products play one of the main roles in human life. Moreover, this material is irreplaceable both in production and in everyday life. The manufacturing method is of interest to many people; in private houses, equipment for machine injection molding is increasingly appearing.
This material is the most profitable of many production options. Furthermore, it is common to perform various products that are in demand in the household.
As for natural materials, which are very expensive and rather difficult to manufacture, plastic parts replace over time? In addition, this is because people do not think about how to produce products that are familiar and easy to use.
CONTENT
- Types of plastics and raw materials
- Manufacturing technique
- Equipment for the manufacture of plastic items
- Special equipment
- Plastic molding at home
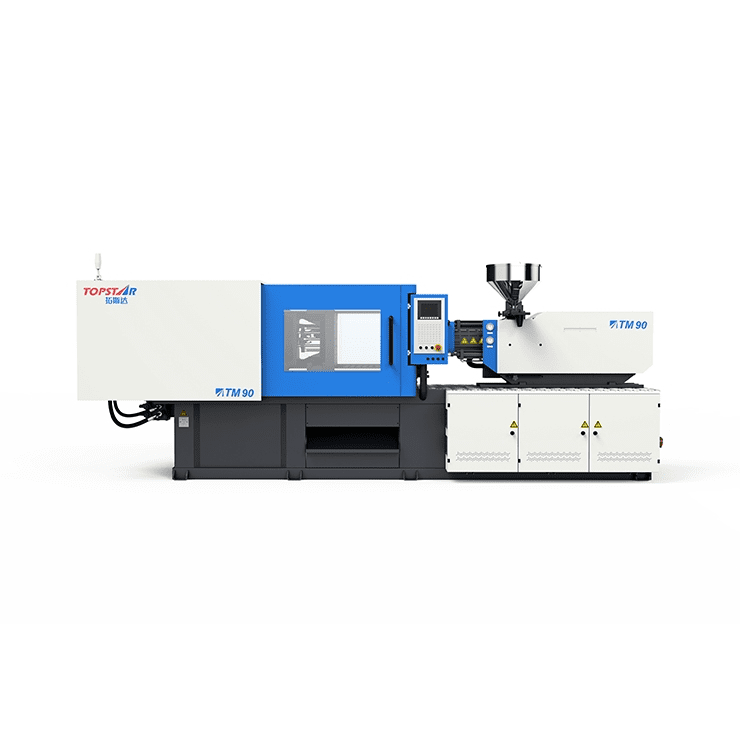
Raw materials of machine injection molding
For the production of polymer products, the following types of plastics are common:
- polyethylene;
- Similarly, polystyrene;
- Moreover, polyethylene terephthalate;
- Furthermore, polyvinyl chloride;
- In addition, high and low pressure polyethylene;
- polypropylene;
Generally, the quality of plastic manufacturing is the choice of raw materials. Even the best machine injection molding needs to be reconfigured when the starting material manufacturer changes.
Otherwise, the quality of the products produced will be completely different.
Manufacturing technique
Algorithm for the implementation of any type of plastic products:
- the formation of an unambiguous chemical composition;
- Moreover, gas comes into the polymer environment;
- Subsequently, the resulting mass is given the desired casting;
- Hence, setting the final shape.
Several Ways of Making Plastic Products
At the initial level, different components are mixed in order to obtain a plastic substance. After that, a gas adds to the polymer in a specific way: either the introduction of rapidly boiling substances or mechanical foaming.
Basically, they disappear when comes under gas pressure. The manufacturing method of machine injection molding depends on the type of polymer and products. Furthermore, there are several ways of making plastic products:
- The presence of castings – the plastic mass turns into a liquid and pours into various forms similar to the finished product. As a result, quite a lot of objects form: dishes, stationery;
- thermoforming;
- compression molding – during the manufacturing process, the required amount of material comes in the mold, the halves are connected, and then the finished part forms;
- encapsulation;
- vacuum forming – Moreover, the required shapes obtain from plastic sheets under different pressures;
- laminating;
- Blowing out – the heated mass pours into the mold. Similarly, the mold closes and fills with air. In addition, the polymer spreads over the entire inner surface in equal amounts;
- extrusion – there is a softening of the mass and its suppression through the matrix, which forms the required shape;
- press molding – the work piece compresses inside the mold; excess material exits through the slots.
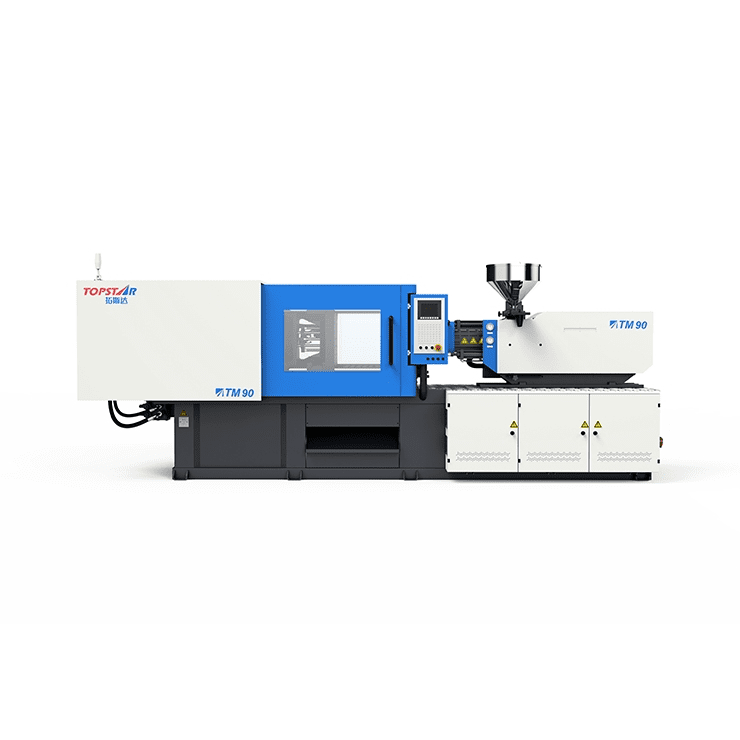
Equipment for the manufacture of plastic items
To produce plastic products, you will need a finished production line or machine injection molding. Hence, any master can build it at home.
Extruders are a huge range of machines that facilitate the production of foam and window profiles, pipes and plastic slate, tubular and sheet films, polymer sheets. Simultaneously, the main structure of the machine is the excluder.
The extrusion line is made up of a set of additional mechanisms. Manufacturing works in automatic mode, it regulates by a specific program.
An injection molding machine is a plastic injection molding machine. The pre-cooked mass shapes into molds and cooled. As a result, a finished piece forms.
Injection molding of plastics is a technological process of manufacturing products by processing thermoplastic polymers heated to a liquid state. Injection molding machines for the manufacture of plastics allow you to fully automate the production process, and create serial products of any size and configuration.
Features of machine injection molding
The principle of operation of injection molding machines for the production of plastics is to melt a granular polymer material to a liquid state and feed it under high pressure into a closed injection mold. Moreover, the product takes on the exact shape of the inner cavity of the mold.
Injection molding allows you to create products with the thinnest walls. They are easy to reinforced or empty inside, multi-colored and foamed. In addition, it combines various polymers. Various types of raw materials can be common in production: polyethylene, polystyrene, polyethylene terephthalates, polyvinyl chloride, and polypropylene.
The machines are adjusted for certain parameters:
- consistency;
- Moreover, the degree of viscosity;
- Similarly, melting parameters.
The strength, quality and accuracy of the parameters of the products depend on the temperature and the value of the pressure indicators, which should be in the range from 80 to 200 MPa.
It is important to maintain the necessary balance, as low pressure can lead to the formation of cavities or under filling, and too high – to the formation of flash.
Varieties of machine injection molding methods
The determining factor in the choice of equipment is the methods of melting, which are injection or intrusive.
Machine injection molding is suitable for creating parts of complex configuration with walls of various thicknesses: from very thin to thick-walled. It is a popular method, comes by minimal shrinkage, the ability to use multi-cavity molds for molding plastics, working with any polymers.
The intrusive method is suitable for creating three-dimensional parts with thick walls. By rotating the worm screw, the molten mass feeds into the injection mold and fills it. Then a small amount of solution injects under pressure, filling all the cavities of the casting mold and compensating for the shrinkage of the cooling melt.
Features of the process machine injection molding
Creation of plastic products in injection molding machines takes place in several stages:
- Generally, polymer raw materials load into the receiving hopper of the injection molding machine.
- Under the influence of their own weight, the granules enter the screw zone, where they melt under the influence of high temperatures.
- Under high pressure, through the die of the plasticization module, the molten mass injects into the mold.
- In the process of cooling in the molds, the pressure gradually decreases, the products pull out.
Conclusion
The whole casting process takes from a few seconds to 10 minutes. In addition, it depends on the starting material, wall thickness, dimensions and configuration of the parts.
Machine injection molding create plastic car parts, various containers, stationery, toys, household items, components for electronics, medical equipment and other products.
TRENDING POSTS
- What factors can cause delays in the injection molding process of plastic molding machine? 2022/01/13
- Exhibition Review| Topstar participates in InterPlas Thailand 2024 2022/01/13
- Star Case | Topstar helps Santong upgrade its intelligent plant 2022/01/13
- Topstar Special | National Science and Technology Workers Day 2022/01/13
HOT TOPIC
- .ervo motor-driven linear robots
- 3 axis robot
- 3 axis robots
- 3 in 1 Compact Dehumidifying Dryer
- 3-axis robot
- 3-axis robots
- 5-axis CNC machine
- accuracy
- Air Chillers
- all electric injection molding machine
- all electric injection molding machines
- All-electric injection molding machines
- and overall production quality. Therefore
- AP-RubberPlas
- automated injection molding machine
- Automation changed engineering
- automation of injection molding robots
- auxiliary machine
- Bench Injection Molding Machine
- Cabinet dryer manufacturers
- Cabinet dryers
- chiller
- CNC Drilling Machine
- CNC Drilling Machines
- cnc engraving machine manufacturer
- cnc laser cutting machine manufacturer
- CNC machine
- CNC Machine Center
- CNC Machine for Sale
- CNC Machine Manufacturing
- CNC Machine Tool
- CNC machine tool product
- CNC Machining Center
- CNC wood carving machine
- Cooling system
- Cross-Walking Single Axis Servo Cylinder Robot
- Cross-Walking Single-Axis Servo Cylinder Robot
- Cross-Walking Three-Axis/Five-Axis Servo Driven Robot
- cross-walking three-axis/five-axis servo-driven robot
- Dehumidifier Dryer
- Dehumidifying Dryer
- delta parallel robot
- Desktop Injection Molding Machine
- Desktop injection molding machines
- Desktop Molding Machine
- desktop plastic injection machine
- Desktop Plastic Injection Molding Machine
- direct clamp injection molding machine
- Direct clamp injection molding machines
- Dosing & mixing system
- Drilling Centers
- Drying and dehumidification system
- drying and dehumidifying equipment
- Drying and Dehumidifying System
- drying system
- effective and efficient. Cabinet dryers are also used in other industries where large quantities of material need to be dried
- efficient injection molding machine
- elbow hydraulic injection molding machines
- electric injection molding machine
- electric injection molding machines
- energy-efficient injection molding robot
- energy-saving injection molding machine
- etc. Among injection molding robots
- exhibition
- features of CNC machine
- Feeding And Conveying System
- Five Axis Machine Center
- Fully automatic injection molding machine
- Gathering Topstar
- giant injection molding machine
- GMU-600 5-Axis Machining Center
- Granulating & Recycling System
- Heavy duty injection molding machine
- High-precision electric molding machines
- high-precision plastic molding machines
- high-speed all electric injection molding machine
- Honeycomb rotor dehumidifier
- horizontal injection molding machine
- Horizontal Injection Molding Machines
- Horizontal Injection Moulding Machine
- Horizontal Mixer manufacturer
- How The CNC Machine Works
- hybrid injection molding machine
- hydraulic injection molding machine
- Hydraulic Injection Molding Machines
- in this article
- Industrial robot
- Industrial Robot Chinese brand
- industrial robot parts
- industrial robot supplier
- Industrial robots
- Industry Chain
- Injection Manipulator
- injection manipulator robot
- injection mold machines
- Injection molding
- Injection molding automation
- Injection Molding Automation Solution
- injection molding dryer
- Injection molding equipment
- injection molding hopper dryer
- Injection molding machine
- injection molding machine brand
- Injection Molding Machine Factory
- Injection Molding Machine Manufacture
- Injection molding machine manufacturer
- injection molding machine manufacturers
- Injection molding machine procurement
- injection molding machine robotic arm
- injection molding machine with a robot
- Injection molding machines
- injection molding material dehumidifying
- injection molding plant
- Injection Molding Robot
- injection molding robot arm
- Injection molding robot automation
- Injection molding robotic arm
- injection molding robots
- Injection moulding machine
- Injection Moulding Robots
- Injection Robot
- Injection robot arm
- Injection robot manufacturer
- Injection robot wholesale
- injection robots
- intelligent injection molding machines
- Introducing Injection Robot
- It is the best choice for drying large quantities of material at once. Cabinetmakers use these machines because they are fast
- large injection molding machine
- Learn what industrial automation and robotics is
- linear robot
- linear robots
- low speed sound-proof granulator
- machine plastic molding
- make sure to add some! Improvements (2) Keyphrase in introduction: Your keyphrase or its synonyms appear in the first paragraph of the copy
- manipulator machine
- manufacturing
- medical grade injection molding machines
- medical injection molding machine
- medical injection molding machines
- micro injection molding machine
- middle speed granulator
- Mini CNC machine manufacturers.
- Mold Temperature Control System
- mold temperature controller
- mold temperature controllers
- molding material Dehumidifying System
- mould temperature control system
- mould temperature controller
- mould temperature controllers
- New electric injection molding machine
- nitrogen dryer manufacturer
- nitrogen dryer system manufacturer
- Oil type mold temperature controller
- Oil type mold temperature controllers
- open day
- Outbound links: No outbound links appear in this page. Add some! Images: No images appear on this page. Add some! Internal links: No internal links appear in this page
- PET Preform injection molding
- phone case maker machine
- phone case making machine
- plastic bottle making machine
- plastic bottle manufacturing
- plastic bucket making machine
- plastic bucket manufacturing
- Plastic chair making machine
- plastic forming equipment
- plastic hopper dryer
- plastic injection machine
- plastic injection machines
- plastic injection molding
- Plastic injection molding equipment
- Plastic injection molding machine
- Plastic Injection Molding Machines
- plastic injection moulding machine
- plastic injection robot
- Plastic Molding machine
- Plastic Molding Machines
- plastic molding press
- plastic moulding machine
- plastic phone case making machine
- plastic-molding machine
- powerful granulator
- Powerful Type Sound-Proof Granulator
- precision injection molding
- precision injection molding machines
- production of plastic seats
- pure water mould temperature controller
- Robot injection molding
- robot injection molding machine
- robot manufacturing companies
- Robotic arm for injection molding machine
- robotic injection molding machines
- robotics in injection molding
- SCARA robot
- SCARA robots
- Service-oriented manufacturing
- Servo Cylinder Robot
- servo driven robot
- Servo Driven Robots
- servo injection robots
- servo motor-driven linear robots
- servo-driven 3-axis robot
- Servo-Driven Robot
- Setup of injection machine
- Silicone Injection Molding Machine
- six-axis industrial robot
- Stainless Hopper Dryer
- Stainless Hopper Dryers
- star club
- swing arm robot
- take-out robots
- the choice between servo-driven robots and hydraulic robots will have a certain impact on efficiency
- the most popular injection molding machine
- the type of injection molding robot
- toggle clamp injection molding machine
- Toggle Hydraulic Injection Molding Machines
- toggle injection molding machine
- Top 10 brands of injection robots
- Topstar
- Topstar Engineering
- Topstar Industrial Robots
- Topstar injection molding intelligent
- Topstar Scara Robots
- Useful Injection molding machine
- Vertical machining centers
- volumetric type blender
- water chiller
- water chillers
- water distributor
- water type mold temperature controller
- Water Type MoldTemperature Controller
- Water-Type Mould Temperature Controllers
- We often face choices when performing injection molding. We will choose the type of injection molding machine
- wholesale of injection molding machines
- x carve CNC