What is manipulator? An Incredibly Useful Machine
2022/04/14 By Topstar
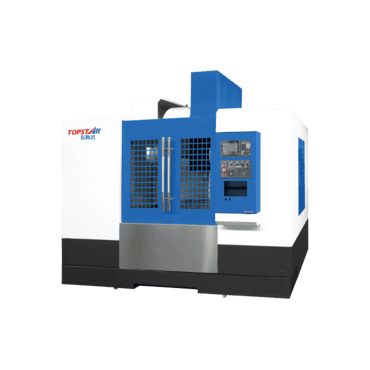
Firstly, a thread-cutting manipulator is industrial equipment designed for threading with taps and dies and drilling in soft materials.
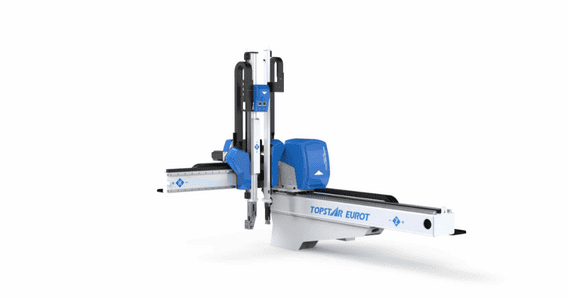
Depending on the drive type, threading manipulators are classified into the following types.
Pneumatic threading manipulator
Secondly, it is suitable for threading M2-M27 mm. Such manipulators are very popular because. c cut the main threads. Small dimensions and weight make it easy to place the tool even in a small workplace. Manipulators are easy to connect in a workshop equipped with a compressed air system.
The ability to significantly reduce the cost of operating technological equipment because “slow” operations for cutting threads of large diameters from stationary machines with a high price of machine hours are moving to “faster” and more productive thread-cutting manipulators;
Thread-cutting electric manipulator
As well as, the manipulator is suitable for workshops with no compressed air and a need for large-diameter threading up to M60. Also, the advantages include fully programmable threading parameters, including forward and reverse rotation speed, thread pitch, and depth, which are comparable in quality and functionality to CNC threading machines.
Hydraulic threading machine manipulator
Their power is higher than that of manipulators with pneumatic drives. Thread diameter – 3-60 mm. It also reduces the duration of the processing period of one part; reduces breakages of taps; the ability to cut threads strictly at the required angle; parallelism of threaded holes to the working plane.
Furthermore, the manipulator is an effective pantograph system of the parallelogram arm during movement, ensuring that the desired position of the drive axis is maintained; high-quality cutting of most sizes and types of threads when using one model of a manipulator with quick-change adapters; the versatility of the manipulator: it can also be used for countersinking,
Main advantages of the robot manipulator
The main advantages of the robot manipulator are operational readiness, which is close to 100%, high repeatability of movements, and accuracy when moving workpieces. Manipulator robots are reliable and automatically make production more economical.
The workpiece loading process’s reliability is ensured by a robotic system that turns any CNC machine into a highly efficient machining center, helping to create an optimally organized production site at a woodworking plant or furniture factory.
Manipulator Advantages
- Moving preparations in various conditions, at the different organization of places of storage, with alignment and turn
- Additional functions are possible, such as determining the position of the workpieces or cleaning them.
- Work with different materials.
- Manipulator has a high-speed operation.
- Reduction of physical loads of operators
- High operational readiness reduces the number and downtime and improves product quality.
Technical features
- Robot with 5 or 6 axes as the central element of the manipulator machining section
- Simple and intuitive control thanks to the integration of the robot manipulator in the control system of the production site and the visualization of processes in CNC machining centers
- Production of new products does not require complex adjustment as the movements of the robot manipulator adapt to the sizes of preparations automatically.
- It is possible to use a barcode scanner.
- Efficiency due to the use of electricity only directly at the time of movement of the workpieces
INDUSTRIAL ROBOT MANIPULATOR
Furthermore, modern processing equipment divides into three main classes. The first, most numerous, and representative class is CNC machines. The second, – the production complex based on programmable logic controllers (PLC).
The third – the least numerous but the most dynamically developing class – robotic technological complexes (RTC), made based on industrial robotic manipulators. At the same time, the technical characteristics of modern industrial robots have reached such values.
They already allow them to be used in such technological operations that were previously performed exclusively using CNC machines. Using these capabilities, Cook Robotics was the first manufacturer of industrial robots to develop its concept of using industrial robots in applications traditionally considered the preserve of manipulator machine tools.
Industries where robot-based machining centers are currently being successfully used:
Foundry: sprue and riser cutting, milling, debarring.
Woodworking: drilling, milling, sawing, edging, polishing.
Stone processing: milling, sawing, grinding, polishing.
Modeling: milling, drilling.
Metalworking: cutting, milling, drilling, sawing.
The robot control system understands the CNC codes
An essential distinguishing feature of such RTKs is that it is not necessary to know the programming language of robots to develop control programs (in the case of Top star, this is the KRL language.
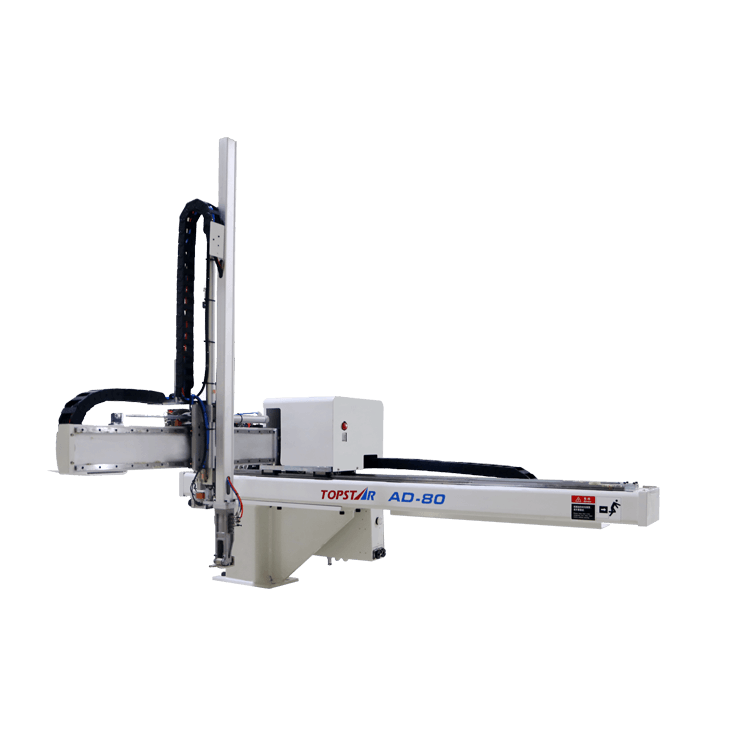
Due to the prevalence of manipulator systems, a huge technological experience has been gained in using 5-axis machines in the above applications. There are a significant number of software packages for various technical applications.
However, the ability of Top star manipulator robots to work with these programs dramatically facilitates the development of new RTK capabilities for operators and technologists, turning the robot, from the point of view of an operator or a programmer-technologist, in fact, into a CNC machine.
Industrial robotic arms provide an additional number of advantages
- The robot replaces the machine: a complete set of commands; standard functions G, M, S, T, L; other functions and powers; a combination of CNC with robot sensors.
- Large working area: cheaper compared to most machines; high degree of freedom; installation flexibility; requires little space for placement.
- Ease of use: direct interface with CAD/CAM systems; execution of G-codes, no need to train CNC operators; copying programs.
- High accuracy: the controller reads many points ahead, spline interpolation, and various compensation modules.
CNC machines based on coordinate tables
Most often, these are portal machines with 2 or 3 degrees of freedom, less often 5, and designed for various types of cutting, such as laser, plasma, water jet, or gas. And even here, robots are already finding use in sheet metal work, providing their owners with several apparent advantages.
Eventually, several research and production companies in Russia began to develop and offer manipulator machines for sheet processing based on robots that “understand” conventional CNC programs.
Compared to traditionally used 5-axis systems based on coordinate tables, installations made using robotic manipulators, at comparable, and sometimes lower prices, have more opportunities.
Conclusion
Finally, a wide range of industrial manipulator robots allows you to select the optimal configuration of the water jet, laser, and plasma cutting systems in terms of the specific technical requirements of the customer and minimize the cost.
The presence of a wide range of proven device models – positioners coordinated working with robots, can significantly expand the scope of robotic cutting systems, including spatial cutting of pipelines.
TRENDING POSTS
- What factors can cause delays in the injection molding process of plastic molding machine? 2022/04/14
- Exhibition Review| Topstar participates in InterPlas Thailand 2024 2022/04/14
- Star Case | Topstar helps Santong upgrade its intelligent plant 2022/04/14
- Topstar Special | National Science and Technology Workers Day 2022/04/14
HOT TOPIC
- .ervo motor-driven linear robots
- 1.0 guangdong topstar technology co. ltd
- 1.0 topstar china
- 1.0 topstar robot
- 11
- 2
- 21
- 23
- 3 axis robot
- 3 axis robots
- 3 in 1 Compact Dehumidifying Dryer
- 3-axis robot
- 3-axis robots
- 39
- 41
- 5-axis CNC machine
- 62
- accuracy
- Air Chillers
- all electric injection molding machine
- all electric injection molding machines
- All-electric injection molding machines
- and overall production quality. Therefore
- AP-RubberPlas
- automated injection molding machine
- Automation changed engineering
- automation of injection molding robots
- auxiliary machine
- Bench Injection Molding Machine
- Cabinet dryer manufacturers
- Cabinet dryers
- chiller
- CNC Drilling Machine
- CNC Drilling Machines
- cnc engraving machine manufacturer
- cnc laser cutting machine manufacturer
- CNC machine
- CNC Machine Center
- CNC Machine for Sale
- CNC Machine Manufacturing
- CNC Machine Tool
- CNC machine tool product
- CNC Machining Center
- CNC wood carving machine
- Cooling system
- Cross-Walking Single Axis Servo Cylinder Robot
- Cross-Walking Single-Axis Servo Cylinder Robot
- Cross-Walking Three-Axis/Five-Axis Servo Driven Robot
- cross-walking three-axis/five-axis servo-driven robot
- Dehumidifier Dryer
- Dehumidifying Dryer
- delta parallel robot
- Desktop Injection Molding Machine
- Desktop injection molding machines
- Desktop Molding Machine
- desktop plastic injection machine
- Desktop Plastic Injection Molding Machine
- direct clamp injection molding machine
- Direct clamp injection molding machines
- Dosing & mixing system
- Drilling Centers
- Drying and dehumidification system
- drying and dehumidifying equipment
- Drying and Dehumidifying System
- drying system
- effective and efficient. Cabinet dryers are also used in other industries where large quantities of material need to be dried
- efficient injection molding machine
- elbow hydraulic injection molding machines
- electric injection molding machine
- electric injection molding machines
- energy-efficient injection molding robot
- energy-saving injection molding machine
- etc. Among injection molding robots
- exhibition
- features of CNC machine
- Feeding And Conveying System
- Five Axis Machine Center
- Fully automatic injection molding machine
- Gathering Topstar
- giant injection molding machine
- GMU-600 5-Axis Machining Center
- Granulating & Recycling System
- Heavy duty injection molding machine
- High-precision electric molding machines
- high-precision plastic molding machines
- high-speed all electric injection molding machine
- Honeycomb rotor dehumidifier
- horizontal injection molding machine
- Horizontal Injection Molding Machines
- Horizontal Injection Moulding Machine
- Horizontal Mixer manufacturer
- How The CNC Machine Works
- hybrid injection molding machine
- hydraulic injection molding machine
- Hydraulic Injection Molding Machines
- in this article
- Industrial robot
- Industrial Robot Chinese brand
- industrial robot parts
- industrial robot supplier
- Industrial robots
- Industry Chain
- Injection Manipulator
- injection manipulator robot
- injection mold machines
- Injection molding
- Injection molding automation
- Injection Molding Automation Solution
- injection molding dryer
- Injection molding equipment
- injection molding hopper dryer
- Injection molding machine
- injection molding machine brand
- Injection Molding Machine Factory
- Injection Molding Machine Manufacture
- Injection molding machine manufacturer
- injection molding machine manufacturers
- Injection molding machine procurement
- injection molding machine robotic arm
- injection molding machine with a robot
- Injection molding machines
- injection molding material dehumidifying
- injection molding plant
- Injection Molding Robot
- injection molding robot arm
- Injection molding robot automation
- Injection molding robotic arm
- injection molding robots
- Injection moulding machine
- injection moulding machines
- Injection Moulding Robots
- Injection Robot
- Injection robot arm
- Injection robot manufacturer
- Injection robot wholesale
- injection robots
- intelligent injection molding machines
- Introducing Injection Robot
- It is the best choice for drying large quantities of material at once. Cabinetmakers use these machines because they are fast
- large injection molding machine
- large injection molding machines
- Learn what industrial automation and robotics is
- linear robot
- linear robots
- low speed sound-proof granulator
- machine plastic molding
- make sure to add some! Improvements (2) Keyphrase in introduction: Your keyphrase or its synonyms appear in the first paragraph of the copy
- manipulator machine
- manufacturing
- medical grade injection molding machines
- medical injection molding machine
- medical injection molding machines
- micro injection molding machine
- middle speed granulator
- Mini CNC machine manufacturers.
- Mold Temperature Control System
- mold temperature controller
- mold temperature controllers
- molding material Dehumidifying System
- mould temperature control system
- mould temperature controller
- mould temperature controllers
- New electric injection molding machine
- nitrogen dryer manufacturer
- nitrogen dryer system manufacturer
- Oil type mold temperature controller
- Oil type mold temperature controllers
- open day
- Outbound links: No outbound links appear in this page. Add some! Images: No images appear on this page. Add some! Internal links: No internal links appear in this page
- PET Preform injection molding
- phone case maker machine
- phone case making machine
- plastic bottle making machine
- plastic bottle manufacturing
- plastic bucket making machine
- plastic bucket manufacturing
- Plastic chair making machine
- plastic forming equipment
- plastic hopper dryer
- plastic injection machine
- plastic injection machines
- plastic injection molding
- Plastic injection molding equipment
- Plastic injection molding machine
- Plastic Injection Molding Machines
- plastic injection moulding machine
- plastic injection moulding machines
- plastic injection robot
- Plastic Molding machine
- Plastic Molding Machines
- plastic molding press
- plastic moulding machine
- plastic phone case making machine
- plastic-molding machine
- powerful granulator
- Powerful Type Sound-Proof Granulator
- precision injection molding
- precision injection molding machines
- production of plastic seats
- pure water mould temperature controller
- Robot injection molding
- robot injection molding machine
- robot manufacturing companies
- Robotic arm for injection molding machine
- robotic injection molding machines
- robotics in injection molding
- SCARA robot
- SCARA robots
- Service-oriented manufacturing
- Servo Cylinder Robot
- servo driven robot
- Servo Driven Robots
- servo injection robots
- servo motor-driven linear robots
- servo-driven 3-axis robot
- Servo-Driven Robot
- Setup of injection machine
- Silicone Injection Molding Machine
- six-axis industrial robot
- Stainless Hopper Dryer
- Stainless Hopper Dryers
- star club
- swing arm robot
- take-out robots
- the choice between servo-driven robots and hydraulic robots will have a certain impact on efficiency
- the most popular injection molding machine
- the type of injection molding robot
- toggle clamp injection molding machine
- Toggle Hydraulic Injection Molding Machines
- toggle injection molding machine
- Top 10 brands of injection robots
- Topstar
- Topstar Engineering
- Topstar Industrial Robots
- Topstar injection molding intelligent
- Topstar Scara Robots
- Useful Injection molding machine
- Vertical machining centers
- volumetric type blender
- water chiller
- water chillers
- water distributor
- water type mold temperature controller
- Water Type MoldTemperature Controller
- Water-Type Mould Temperature Controllers
- We often face choices when performing injection molding. We will choose the type of injection molding machine
- wholesale of injection molding machines
- x carve CNC
- 热门查询 点击次数 展示 排名 topstar