Requirements for injection molding machines when injecting PET Preform injection molding
2024/03/02 By Topstar
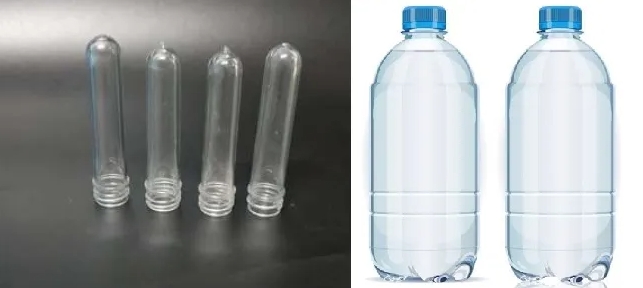
PET preform injection molding is a specialized injection molding process used to produce PET bottles, containers, and other plastic items. To ensure the high-quality and efficient production of PET bottle preforms, an injection molding machine must be installed that meets the specific requirements for PET Preform injection molding. Therefore, this guide will clarify the basic requirements for an injection molding machine when manufacturing PET bottle preforms.
Optimal heating and cooling systems for PET preform injection molding
In the PET bottle preform injection molding process, the design of the heating and cooling system of the injection molding machine injection system is essential. PET bottle preforms are formed by heating PET resin to a molten state and then injecting it into a mold for molding. Therefore, the heating system of the injection molding machine needs to ensure that the resin can be heated evenly to the appropriate temperature to ensure the quality and stability of the molded product. At the same time, the design of the cooling system is also crucial. After injection molding, we must cool the PET bottle and preform it quickly to solidify its shape. A sound injection molding machine cooling system should reduce mold temperature effectively to ensure rapid product cooling and avoid deformation or defects.
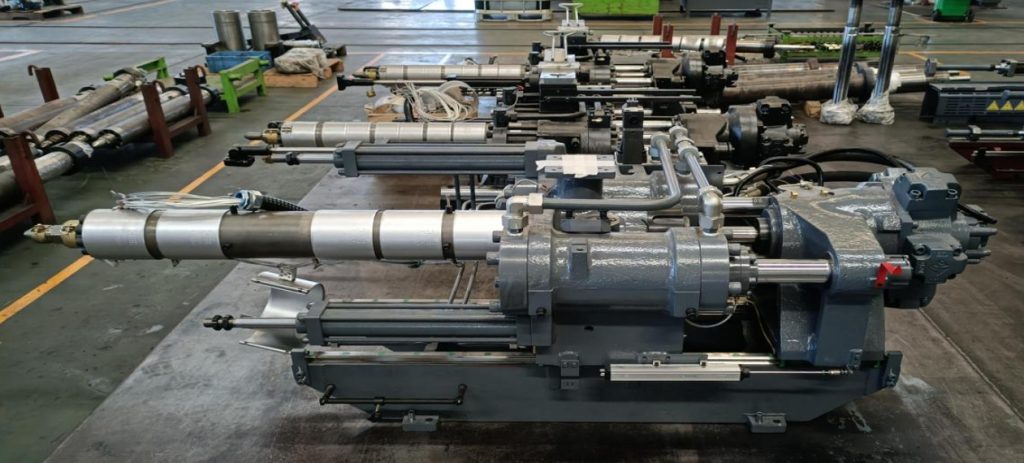
PET preform injection molding requires high injection pressure and speed capabilities
PET preform injection molding also places specific requirements on the high-pressure and high-speed capabilities of the injection molding machine. This is a thermoplastic polymer that exhibits high viscosity when melted. Therefore, during the injection molding process, we need to inject the material into the mold cavity with sufficient force and speed to ensure correct filling and pressure-holding of the mold. Injection molding machines with high injection pressure can melt the viscosity of PET resin well and force it accurately into complex mold cavities. High injection pressure also helps achieve an even distribution of material throughout the mold, preventing defects such as voids, sink marks, or uneven thickness in the preform.
The high injection speeds of injection molding machines also drastically reduce cycle times and ensure rapid mold filling before the material cools and solidifies. Therefore, we often equip injection molding machines used for PET preform molding with robust hydraulic systems capable of generating high pressures and rapid injection devices capable of delivering material at high speeds.
Precise injection control and injection volume adjustment
Injection molding machines with precise injection control can regulate the flow of molten PET resin into the mold cavity. This control ensures the material fills the cavity evenly and avoids defects such as short shots or overflows. Their injection machine systems should equip advanced control systems such as proportional valves and servo motors to accurately adjust injection parameters such as pressure, speed, and volume. Additionally, in PET Preform injection molding, the ability to adapt shot volume to accommodate changes in preform design, weight, and wall thickness is critical. Therefore, an injection molding machine must be required to accurately adjust the injection amount or volume of molten resin injected into the mold cavity to ensure that each bottle meets the specified requirements.
Robust and reliable clamping mechanism
PET Preform injection molding requires the injection molding machine to have a robust and reliable clamping mechanism to ensure an efficient and stable production process. In PET preform molding, the clamping mechanism of the injection molding machine must withstand the high pressure generated during the injection process and the mechanical stress caused by material expansion and cooling of the preform. Because PET resin will exert considerable pressure on the mold wall when melted, the mold clamping device of the injection molding machine must have a solid and uniform clamping force to prevent mold deformation or dislocation. We usually design PET bottle preform molds with multiple cavities to improve production efficiency. We must ensure that the mold clamping structure distributes the clamping force evenly on all cavities. This provides consistent shaping of multiple preforms in each cycle.
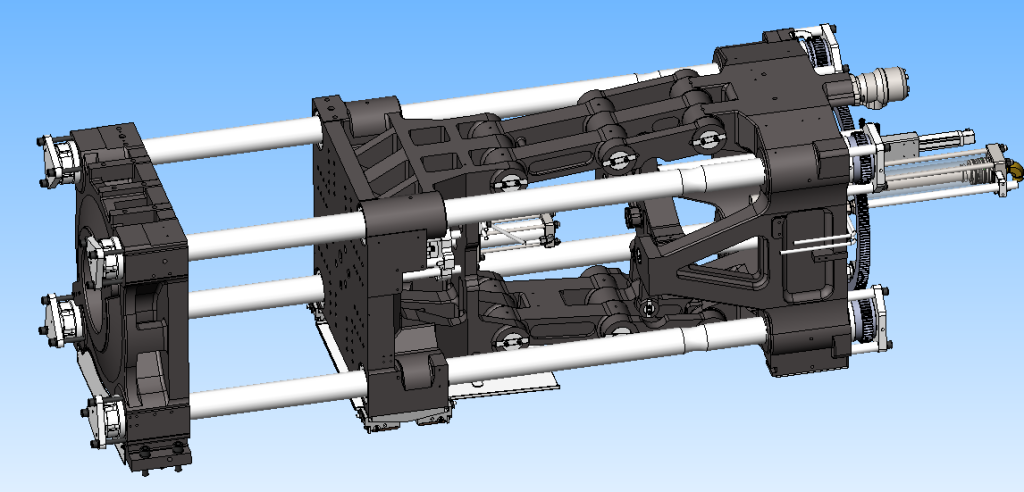
Advanced control systems and process monitoring capabilities
They require injection molding machines with advanced control systems, and process monitoring functions to ensure the production process’s efficiency and product quality stability. The advanced control system can accurately control injection molding parameters such as temperature, pressure, speed, and injection volume to meet the processing needs of PET resin. We monitor and adjust various real-time parameters during the injection molding through sensors and feedback devices to ensure we achieve the expected standards for each performance’s size, weight, and quality. Using real-time data and feedback, operators can adjust production parameters promptly. For this process, advanced process monitoring functions include real-time monitoring of injection molding machine operating status, production cycle, material consumption, product quality, and other vital indicators.
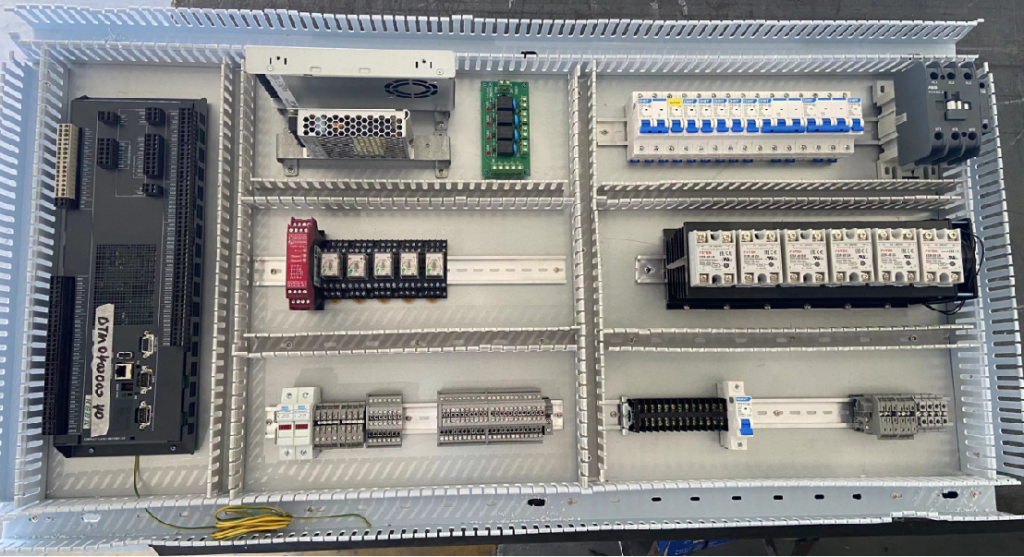
Use a suitable injection molding machine
Through this guide, you can know that an injection molding machine that meets the needs of PET bottle preform molding needs optimal heating and cooling systems, high injection pressure and speed capabilities, etc. Each of these aspects can affect the quality of the PET bottle preforms produced, so we must choose a suitable injection molding machine for PET bottle preforms.
TRENDING POSTS
- What factors can cause delays in the injection molding process of plastic molding machine? 2024/03/02
- Exhibition Review| Topstar participates in InterPlas Thailand 2024 2024/03/02
- Star Case | Topstar helps Santong upgrade its intelligent plant 2024/03/02
- Topstar Special | National Science and Technology Workers Day 2024/03/02
HOT TOPIC
- .ervo motor-driven linear robots
- 3 axis robot
- 3 axis robots
- 3 in 1 Compact Dehumidifying Dryer
- 3-axis robot
- 3-axis robots
- 5-axis CNC machine
- accuracy
- Air Chillers
- all electric injection molding machine
- all electric injection molding machines
- All-electric injection molding machines
- and overall production quality. Therefore
- AP-RubberPlas
- automated injection molding machine
- Automation changed engineering
- automation of injection molding robots
- auxiliary machine
- Bench Injection Molding Machine
- Cabinet dryer manufacturers
- Cabinet dryers
- chiller
- CNC Drilling Machine
- CNC Drilling Machines
- cnc engraving machine manufacturer
- cnc laser cutting machine manufacturer
- CNC machine
- CNC Machine Center
- CNC Machine for Sale
- CNC Machine Manufacturing
- CNC Machine Tool
- CNC machine tool product
- CNC Machining Center
- CNC wood carving machine
- Cooling system
- Cross-Walking Single Axis Servo Cylinder Robot
- Cross-Walking Single-Axis Servo Cylinder Robot
- Cross-Walking Three-Axis/Five-Axis Servo Driven Robot
- cross-walking three-axis/five-axis servo-driven robot
- Dehumidifier Dryer
- Dehumidifying Dryer
- delta parallel robot
- Desktop Injection Molding Machine
- Desktop injection molding machines
- Desktop Molding Machine
- desktop plastic injection machine
- Desktop Plastic Injection Molding Machine
- direct clamp injection molding machine
- Direct clamp injection molding machines
- Dosing & mixing system
- Drilling Centers
- Drying and dehumidification system
- drying and dehumidifying equipment
- Drying and Dehumidifying System
- drying system
- effective and efficient. Cabinet dryers are also used in other industries where large quantities of material need to be dried
- efficient injection molding machine
- elbow hydraulic injection molding machines
- electric injection molding machine
- electric injection molding machines
- energy-efficient injection molding robot
- energy-saving injection molding machine
- etc. Among injection molding robots
- exhibition
- features of CNC machine
- Feeding And Conveying System
- Five Axis Machine Center
- Fully automatic injection molding machine
- Gathering Topstar
- giant injection molding machine
- GMU-600 5-Axis Machining Center
- Granulating & Recycling System
- Heavy duty injection molding machine
- High-precision electric molding machines
- high-precision plastic molding machines
- high-speed all electric injection molding machine
- Honeycomb rotor dehumidifier
- horizontal injection molding machine
- Horizontal Injection Molding Machines
- Horizontal Injection Moulding Machine
- Horizontal Mixer manufacturer
- How The CNC Machine Works
- hybrid injection molding machine
- hydraulic injection molding machine
- Hydraulic Injection Molding Machines
- in this article
- Industrial robot
- Industrial Robot Chinese brand
- industrial robot parts
- industrial robot supplier
- Industrial robots
- Industry Chain
- Injection Manipulator
- injection manipulator robot
- injection mold machines
- Injection molding
- Injection molding automation
- Injection Molding Automation Solution
- injection molding dryer
- Injection molding equipment
- injection molding hopper dryer
- Injection molding machine
- injection molding machine brand
- Injection Molding Machine Factory
- Injection Molding Machine Manufacture
- Injection molding machine manufacturer
- injection molding machine manufacturers
- Injection molding machine procurement
- injection molding machine robotic arm
- injection molding machine with a robot
- Injection molding machines
- injection molding material dehumidifying
- injection molding plant
- Injection Molding Robot
- injection molding robot arm
- Injection molding robot automation
- Injection molding robotic arm
- injection molding robots
- Injection moulding machine
- Injection Moulding Robots
- Injection Robot
- Injection robot arm
- Injection robot manufacturer
- Injection robot wholesale
- injection robots
- intelligent injection molding machines
- Introducing Injection Robot
- It is the best choice for drying large quantities of material at once. Cabinetmakers use these machines because they are fast
- large injection molding machine
- Learn what industrial automation and robotics is
- linear robot
- linear robots
- low speed sound-proof granulator
- machine plastic molding
- make sure to add some! Improvements (2) Keyphrase in introduction: Your keyphrase or its synonyms appear in the first paragraph of the copy
- manipulator machine
- manufacturing
- medical grade injection molding machines
- medical injection molding machine
- medical injection molding machines
- micro injection molding machine
- middle speed granulator
- Mini CNC machine manufacturers.
- Mold Temperature Control System
- mold temperature controller
- mold temperature controllers
- molding material Dehumidifying System
- mould temperature control system
- mould temperature controller
- mould temperature controllers
- New electric injection molding machine
- nitrogen dryer manufacturer
- nitrogen dryer system manufacturer
- Oil type mold temperature controller
- Oil type mold temperature controllers
- open day
- Outbound links: No outbound links appear in this page. Add some! Images: No images appear on this page. Add some! Internal links: No internal links appear in this page
- PET Preform injection molding
- phone case maker machine
- phone case making machine
- plastic bottle making machine
- plastic bottle manufacturing
- plastic bucket making machine
- plastic bucket manufacturing
- Plastic chair making machine
- plastic forming equipment
- plastic hopper dryer
- plastic injection machine
- plastic injection machines
- plastic injection molding
- Plastic injection molding equipment
- Plastic injection molding machine
- Plastic Injection Molding Machines
- plastic injection moulding machine
- plastic injection robot
- Plastic Molding machine
- Plastic Molding Machines
- plastic molding press
- plastic moulding machine
- plastic phone case making machine
- plastic-molding machine
- powerful granulator
- Powerful Type Sound-Proof Granulator
- precision injection molding
- precision injection molding machines
- production of plastic seats
- pure water mould temperature controller
- Robot injection molding
- robot injection molding machine
- robot manufacturing companies
- Robotic arm for injection molding machine
- robotic injection molding machines
- robotics in injection molding
- SCARA robot
- SCARA robots
- Service-oriented manufacturing
- Servo Cylinder Robot
- servo driven robot
- Servo Driven Robots
- servo injection robots
- servo motor-driven linear robots
- servo-driven 3-axis robot
- Servo-Driven Robot
- Setup of injection machine
- Silicone Injection Molding Machine
- six-axis industrial robot
- Stainless Hopper Dryer
- Stainless Hopper Dryers
- star club
- swing arm robot
- take-out robots
- the choice between servo-driven robots and hydraulic robots will have a certain impact on efficiency
- the most popular injection molding machine
- the type of injection molding robot
- toggle clamp injection molding machine
- Toggle Hydraulic Injection Molding Machines
- toggle injection molding machine
- Top 10 brands of injection robots
- Topstar
- Topstar Engineering
- Topstar Industrial Robots
- Topstar injection molding intelligent
- Topstar Scara Robots
- Useful Injection molding machine
- Vertical machining centers
- volumetric type blender
- water chiller
- water chillers
- water distributor
- water type mold temperature controller
- Water Type MoldTemperature Controller
- Water-Type Mould Temperature Controllers
- We often face choices when performing injection molding. We will choose the type of injection molding machine
- wholesale of injection molding machines
- x carve CNC