Why are swing arm robot the most accurate in injection molding?
2024/03/01 By Topstar
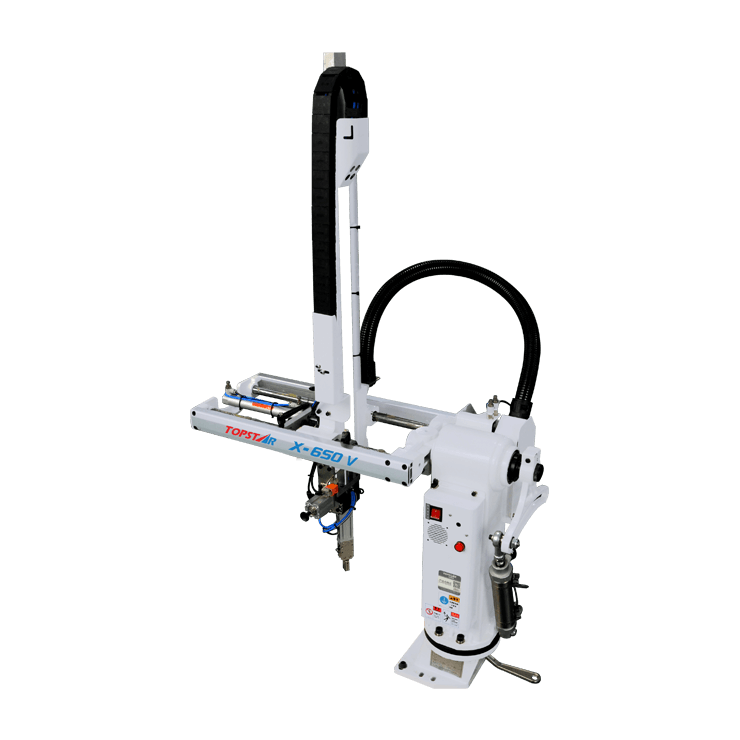
In injection molding, if the accuracy of the swing arm robot in grabbing plastic raw materials is not accurate enough, it will lead to position deviation and uncoordinated pickup time, leading to problems such as failure to take out and equipment alarm shutdown. And swing-arm robots’ take-out accuracy is the best in injection molding. This product guide will examine why swing-arm robots are considered the most accurate in injection molding.
Structure and design of swing arm robot
The main reason for the precision and robustness of swing arm robots is their mechanical structure. Their robots usually use high-strength, high-tension aluminum alloys and precision linear guides, which have durability, rigidity, and resistance to external impacts. This mechanical structure allows them to withstand high loads, vibrations, and repetitive movements without affecting their performance or reliability. The segmented structure of swing-arm robots enables them to perform joint activities and maneuvers in multiple degrees of freedom, mimicking the flexibility and range of motion of the human arm and wrist, and can rotate products 90°. Each part has powerful motors, actuators, and sensors to precisely control and coordinate movement, ensuring smooth and accurate operation during complex tasks.
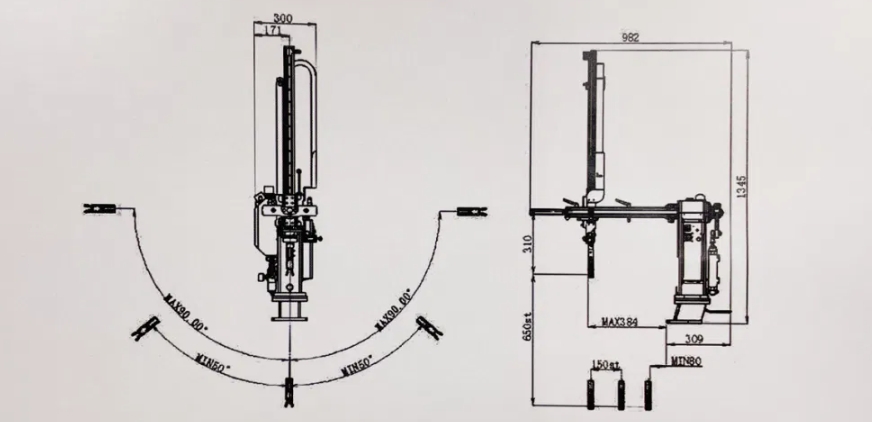
Flexibility of swing arm robot arms
The flexibility of the swing arm robot’s arms lies in their ability to rotate and move. Each joint in the arm of the swing-arm robot provides rotation or linear motion. The fixture is installed on the front part of the arm, which can rotate 90°. It also has an adsorption fixture on the fixture. We installed a sensing device. It facilitates easy mold changes and has a hydraulic shock absorber to ensure stable and smooth front and rear strokes.
In addition, manufacturers can choose the number and type of joints and the length and shape of each section to optimize robot arms for a specific task or workspace. This modular approach allows them to adapt to a variety of environments and perform a variety of functions. By adapting to the contours of the mold and the working environment, swing-arm robots can achieve unrivaled precision when handling delicate plastic materials.
Advanced control system for swing arm robots
Topstar independently developed the control system of the swing arm robot. This system uses high-performance servo motors, actuators, and drive mechanisms to accurately control the movement of each joint in the robot arm. By adjusting the motor’s speed, acceleration, and position, the control system can execute a smooth and accurate motion trajectory, allowing the robotic arm to reach the desired position and direction accurately. The overall energy efficiency increases by 20%. Additionally, we equip it with a handheld controller, making the operation more convenient for the operator. The control system combines sensor feedback to monitor and adjust the robot’s movement in real-time. Encoders, resolvers, and other position sensors can provide accurate feedback on each joint’s position, speed, and acceleration, allowing the control system to compensate for errors and interference and maintain Precise motion control, reducing downtime.
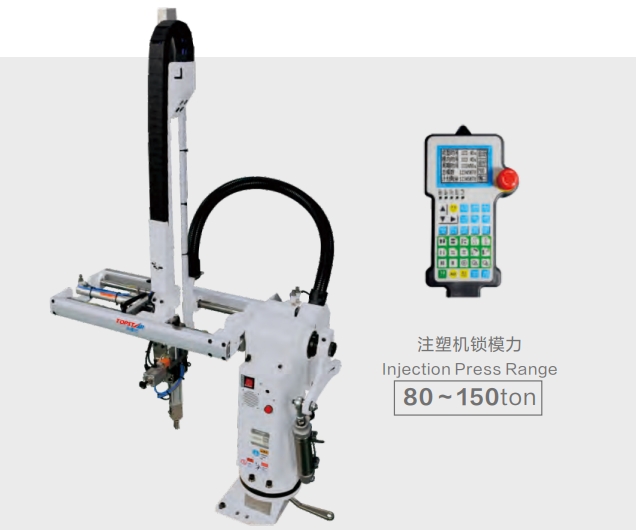
Customized end-of-arm tools
Customized end-of-arm tools (EOAT) enable swing arm robots to perform specific tasks accurately and reliably. Through unique design and customization, they can be applied to horizontal injection molding machines of 50T~250T and quickly remove the runner from the injection molding machine mold. We put the runner and finished product into the granulator next to the machine for immediate recycling. Therefore, manufacturers can design EOATs with specialized grippers, fingers, suction cups, or magnetic attachments to address different plastics’ specific properties and characteristics. This customization ensures objects’ safe and stable gripping, reducing the risk of slipping, damage, or misalignment during operation.
Maintain accuracy during high-speed operation
One of the key factors that enable a swing arm robot to maintain accuracy during high-speed operation is its advanced motion control system. These systems utilize complex algorithms and feedback mechanisms to precisely adjust the speed, acceleration, and deceleration of the robot’s swing arm joints. By precisely controlling the movement trajectory of the robotic arm, the control system minimizes errors and deviations, ensuring that the end effector accurately follows the desired trajectory.
Additionally, we optimize their mechanical design to minimize backlash, inertia, and vibration, which can affect accuracy during high-speed operation. The joints of swing-arm robots are designed with precision components such as bearings, gears, and drive systems to reduce friction and clearance and ensure smooth and accurate motion transmission. Their aluminum alloy allows them to reduce inertia and improve dynamic response, making the whole body lighter and consuming less power.
ultimately
Swing arm robots have high precision in injection molding because of their sturdy structure, arm flexibility, and the integration of advanced control systems, which can play a crucial role in ensuring the quality, consistency, and efficiency of the injection molding process. Role.
TRENDING POSTS
- What factors can cause delays in the injection molding process of plastic molding machine? 2024/03/01
- Exhibition Review| Topstar participates in InterPlas Thailand 2024 2024/03/01
- Star Case | Topstar helps Santong upgrade its intelligent plant 2024/03/01
- Topstar Special | National Science and Technology Workers Day 2024/03/01
HOT TOPIC
- .ervo motor-driven linear robots
- 3 axis robot
- 3 axis robots
- 3 in 1 Compact Dehumidifying Dryer
- 3-axis robot
- 3-axis robots
- 5-axis CNC machine
- accuracy
- Air Chillers
- all electric injection molding machine
- all electric injection molding machines
- All-electric injection molding machines
- and overall production quality. Therefore
- AP-RubberPlas
- automated injection molding machine
- Automation changed engineering
- automation of injection molding robots
- auxiliary machine
- Bench Injection Molding Machine
- Cabinet dryer manufacturers
- Cabinet dryers
- chiller
- CNC Drilling Machine
- CNC Drilling Machines
- cnc engraving machine manufacturer
- cnc laser cutting machine manufacturer
- CNC machine
- CNC Machine Center
- CNC Machine for Sale
- CNC Machine Manufacturing
- CNC Machine Tool
- CNC machine tool product
- CNC Machining Center
- CNC wood carving machine
- Cooling system
- Cross-Walking Single Axis Servo Cylinder Robot
- Cross-Walking Single-Axis Servo Cylinder Robot
- Cross-Walking Three-Axis/Five-Axis Servo Driven Robot
- cross-walking three-axis/five-axis servo-driven robot
- Dehumidifier Dryer
- Dehumidifying Dryer
- delta parallel robot
- Desktop Injection Molding Machine
- Desktop injection molding machines
- Desktop Molding Machine
- desktop plastic injection machine
- Desktop Plastic Injection Molding Machine
- direct clamp injection molding machine
- Direct clamp injection molding machines
- Dosing & mixing system
- Drilling Centers
- Drying and dehumidification system
- drying and dehumidifying equipment
- Drying and Dehumidifying System
- drying system
- effective and efficient. Cabinet dryers are also used in other industries where large quantities of material need to be dried
- efficient injection molding machine
- elbow hydraulic injection molding machines
- electric injection molding machine
- electric injection molding machines
- energy-efficient injection molding robot
- energy-saving injection molding machine
- etc. Among injection molding robots
- exhibition
- features of CNC machine
- Feeding And Conveying System
- Five Axis Machine Center
- Fully automatic injection molding machine
- Gathering Topstar
- giant injection molding machine
- GMU-600 5-Axis Machining Center
- Granulating & Recycling System
- Heavy duty injection molding machine
- High-precision electric molding machines
- high-precision plastic molding machines
- high-speed all electric injection molding machine
- Honeycomb rotor dehumidifier
- horizontal injection molding machine
- Horizontal Injection Molding Machines
- Horizontal Injection Moulding Machine
- Horizontal Mixer manufacturer
- How The CNC Machine Works
- hybrid injection molding machine
- hydraulic injection molding machine
- Hydraulic Injection Molding Machines
- in this article
- Industrial robot
- Industrial Robot Chinese brand
- industrial robot parts
- industrial robot supplier
- Industrial robots
- Industry Chain
- Injection Manipulator
- injection manipulator robot
- injection mold machines
- Injection molding
- Injection molding automation
- Injection Molding Automation Solution
- injection molding dryer
- Injection molding equipment
- injection molding hopper dryer
- Injection molding machine
- injection molding machine brand
- Injection Molding Machine Factory
- Injection Molding Machine Manufacture
- Injection molding machine manufacturer
- injection molding machine manufacturers
- Injection molding machine procurement
- injection molding machine robotic arm
- injection molding machine with a robot
- Injection molding machines
- injection molding material dehumidifying
- injection molding plant
- Injection Molding Robot
- injection molding robot arm
- Injection molding robot automation
- Injection molding robotic arm
- injection molding robots
- Injection moulding machine
- Injection Moulding Robots
- Injection Robot
- Injection robot arm
- Injection robot manufacturer
- Injection robot wholesale
- injection robots
- intelligent injection molding machines
- Introducing Injection Robot
- It is the best choice for drying large quantities of material at once. Cabinetmakers use these machines because they are fast
- large injection molding machine
- large injection molding machines
- Learn what industrial automation and robotics is
- linear robot
- linear robots
- low speed sound-proof granulator
- machine plastic molding
- make sure to add some! Improvements (2) Keyphrase in introduction: Your keyphrase or its synonyms appear in the first paragraph of the copy
- manipulator machine
- manufacturing
- medical grade injection molding machines
- medical injection molding machine
- medical injection molding machines
- micro injection molding machine
- middle speed granulator
- Mini CNC machine manufacturers.
- Mold Temperature Control System
- mold temperature controller
- mold temperature controllers
- molding material Dehumidifying System
- mould temperature control system
- mould temperature controller
- mould temperature controllers
- New electric injection molding machine
- nitrogen dryer manufacturer
- nitrogen dryer system manufacturer
- Oil type mold temperature controller
- Oil type mold temperature controllers
- open day
- Outbound links: No outbound links appear in this page. Add some! Images: No images appear on this page. Add some! Internal links: No internal links appear in this page
- PET Preform injection molding
- phone case maker machine
- phone case making machine
- plastic bottle making machine
- plastic bottle manufacturing
- plastic bucket making machine
- plastic bucket manufacturing
- Plastic chair making machine
- plastic forming equipment
- plastic hopper dryer
- plastic injection machine
- plastic injection machines
- plastic injection molding
- Plastic injection molding equipment
- Plastic injection molding machine
- Plastic Injection Molding Machines
- plastic injection moulding machine
- plastic injection robot
- Plastic Molding machine
- Plastic Molding Machines
- plastic molding press
- plastic moulding machine
- plastic phone case making machine
- plastic-molding machine
- powerful granulator
- Powerful Type Sound-Proof Granulator
- precision injection molding
- precision injection molding machines
- production of plastic seats
- pure water mould temperature controller
- Robot injection molding
- robot injection molding machine
- robot manufacturing companies
- Robotic arm for injection molding machine
- robotic injection molding machines
- robotics in injection molding
- SCARA robot
- SCARA robots
- Service-oriented manufacturing
- Servo Cylinder Robot
- servo driven robot
- Servo Driven Robots
- servo injection robots
- servo motor-driven linear robots
- servo-driven 3-axis robot
- Servo-Driven Robot
- Setup of injection machine
- Silicone Injection Molding Machine
- six-axis industrial robot
- Stainless Hopper Dryer
- Stainless Hopper Dryers
- star club
- swing arm robot
- take-out robots
- the choice between servo-driven robots and hydraulic robots will have a certain impact on efficiency
- the most popular injection molding machine
- the type of injection molding robot
- toggle clamp injection molding machine
- Toggle Hydraulic Injection Molding Machines
- toggle injection molding machine
- Top 10 brands of injection robots
- Topstar
- Topstar Engineering
- Topstar Industrial Robots
- Topstar injection molding intelligent
- Topstar Scara Robots
- Useful Injection molding machine
- Vertical machining centers
- volumetric type blender
- water chiller
- water chillers
- water distributor
- water type mold temperature controller
- Water Type MoldTemperature Controller
- Water-Type Mould Temperature Controllers
- We often face choices when performing injection molding. We will choose the type of injection molding machine
- wholesale of injection molding machines
- x carve CNC