The Future of Plastic Molding machine: Trends to Watch
2023/10/25 By Topstar
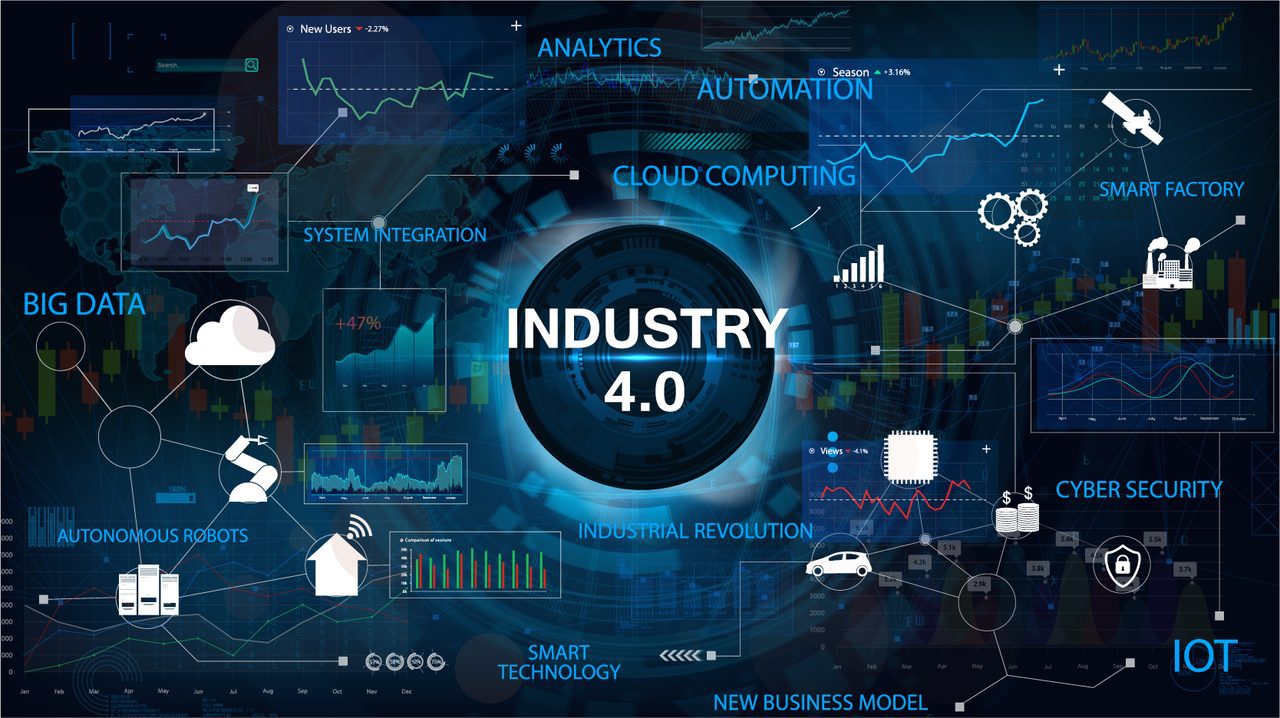
Throughout the booming plastic molding industry, being aware of the latest trends and innovations is vital to stay ahead of the curve. This article looks closer at the plastic molding machine future and the industry’s trends. From advanced materials to intelligent automation, these developments are more than just buzzwords; they represent significant changes that will impact how plastic products are manufactured.
Intelligent plastic molding machine enter the Internet era!
The emergence of intelligent plastic molding machines represents a significant leap forward for the industry. These machines are becoming increasingly connected, leveraging the Internet of Things (IoT) power to communicate in real-time with various components and operators. This connectivity opens the door to numerous advantages. Real-time data analysis allows for more precise monitoring of the molding process. Any irregularities or deviations from the desired output can be promptly identified and resolved. Predictive maintenance is another aspect of this trend, allowing manufacturers to schedule maintenance activities precisely when needed, thereby reducing downtime and preventing unexpected failures. Additionally, operators can even monitor multiple machines simultaneously from remote locations. This not only improves operational efficiency but also saves time and resources.
Integration of Industry 4.0 and plastic molding machine!
The integration of Industry 4.0 technologies is reshaping the landscape of plastic molding. This industrial revolution introduced automation, artificial intelligence, and robotics into manufacturing. In the case of plastic molding machines, this means that the devices can operate with a higher degree of autonomy. They can make real-time adjustments based on data analysis, predict potential problems, and even initiate maintenance activities without human intervention. Industry 4.0 turns the concept of the “smart factory” into reality. In real-time, operators can monitor and control the production line and respond immediately to changes in production demand. This not only optimizes operational efficiency but also improves the quality and consistency of the final product.
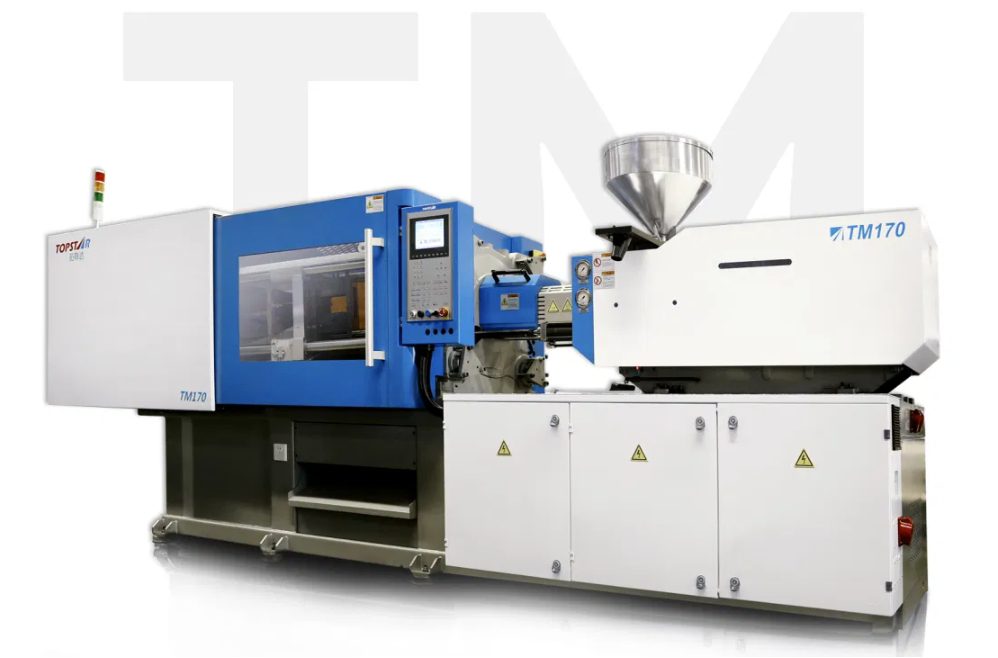
Sustainable practices and environmentally friendly materials
Sustainability is the future direction of plastic molding. As the world becomes more aware of the environmental impact of plastics, the industry is shifting towards more environmentally friendly practices and materials. One of the main trends is the adoption of bioplastics. The materials are derived from renewable resources and are biodegradable, making them more sustainable than traditional plastics.
Additionally, waste reduction is an integral part of the sustainability trend. Innovations to recycle and reuse plastic waste are becoming increasingly common. Some plastic molding machines are now equipped to use recycled materials, reducing the industry’s environmental impact. It’s also a strategic choice for plastic molding companies looking to stay competitive.
Advanced materials and complex geometries
The plastic molding industry is experiencing a shift toward more advanced materials and complex geometries. Traditional plastics are being supplemented and, in some cases, replaced by high-performance polymers, composites, and thermoset resins. These materials offer enhanced mechanical properties, temperature, and chemical resistance, making them suitable for broader applications.
Additionally, mold design and 3D printing technology advances have made it possible to create complex product geometries. Previously, specific procedures were difficult to achieve using traditional molding techniques. However, the integration of 3D printing and advanced mold design software is expanding the possibilities. Manufacturers can now create highly detailed and customized components, from intricate internal structures to complex surface textures.
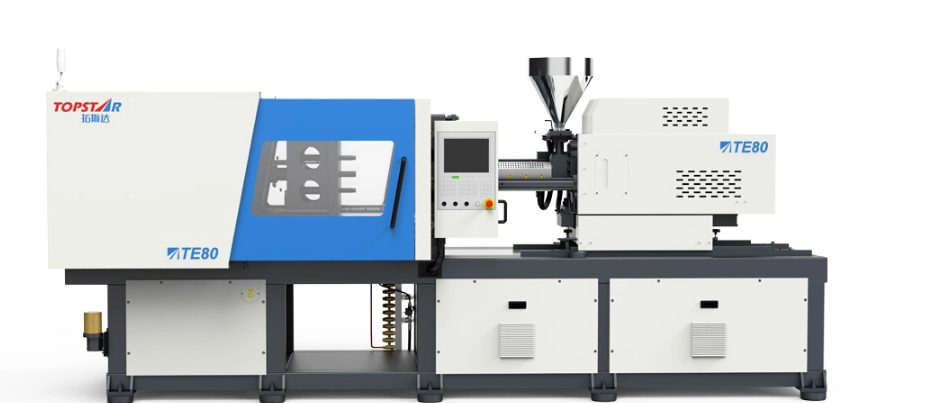
Digital twin for plastic molding process simulation
Using digital twins in plastic molding revolutionizes how manufacturers approach their production processes. A digital twin is a virtual representation of a physical system or method. This means creating virtual replicas of molding machines, molds, and the entire production process in plastic molding. This technology has many advantages. By creating a digital twin, engineers can simulate and optimize the molding process before physical production begins. This allows for a thorough analysis of the entire process, identifying potential problems or inefficiencies. In addition, manufacturers can precisely control the production process with digital twins, optimizing every step to improve efficiency and quality.
In the future
Plastic molding machines will be marked by a dynamic shift towards intelligent technology, sustainability, advanced materials, digital twins, customization, and skill enhancement. Manufacturers that embrace these trends will be well-positioned to thrive in a rapidly evolving industry. We at Topstar will keep abreast of the situation and adapt to the changing situation to meet the unique needs of consumers and the industry.
TRENDING POSTS
- What factors can cause delays in the injection molding process of plastic molding machine? 2023/10/25
- Exhibition Review| Topstar participates in InterPlas Thailand 2024 2023/10/25
- Star Case | Topstar helps Santong upgrade its intelligent plant 2023/10/25
- Topstar Special | National Science and Technology Workers Day 2023/10/25
HOT TOPIC
- .ervo motor-driven linear robots
- 3 axis robot
- 3 axis robots
- 3 in 1 Compact Dehumidifying Dryer
- 3-axis robot
- 3-axis robots
- 5-axis CNC machine
- accuracy
- Air Chillers
- all electric injection molding machine
- all electric injection molding machines
- All-electric injection molding machines
- and overall production quality. Therefore
- AP-RubberPlas
- automated injection molding machine
- Automation changed engineering
- automation of injection molding robots
- auxiliary machine
- Bench Injection Molding Machine
- Cabinet dryer manufacturers
- Cabinet dryers
- chiller
- CNC Drilling Machine
- CNC Drilling Machines
- cnc engraving machine manufacturer
- cnc laser cutting machine manufacturer
- CNC machine
- CNC Machine Center
- CNC Machine for Sale
- CNC Machine Manufacturing
- CNC Machine Tool
- CNC machine tool product
- CNC Machining Center
- CNC wood carving machine
- Cooling system
- Cross-Walking Single Axis Servo Cylinder Robot
- Cross-Walking Single-Axis Servo Cylinder Robot
- Cross-Walking Three-Axis/Five-Axis Servo Driven Robot
- cross-walking three-axis/five-axis servo-driven robot
- Dehumidifier Dryer
- Dehumidifying Dryer
- delta parallel robot
- Desktop Injection Molding Machine
- Desktop injection molding machines
- Desktop Molding Machine
- desktop plastic injection machine
- Desktop Plastic Injection Molding Machine
- direct clamp injection molding machine
- Direct clamp injection molding machines
- Dosing & mixing system
- Drilling Centers
- Drying and dehumidification system
- drying and dehumidifying equipment
- Drying and Dehumidifying System
- drying system
- effective and efficient. Cabinet dryers are also used in other industries where large quantities of material need to be dried
- efficient injection molding machine
- elbow hydraulic injection molding machines
- electric injection molding machine
- electric injection molding machines
- energy-efficient injection molding robot
- energy-saving injection molding machine
- etc. Among injection molding robots
- exhibition
- features of CNC machine
- Feeding And Conveying System
- Five Axis Machine Center
- Fully automatic injection molding machine
- Gathering Topstar
- giant injection molding machine
- GMU-600 5-Axis Machining Center
- Granulating & Recycling System
- Heavy duty injection molding machine
- High-precision electric molding machines
- high-precision plastic molding machines
- high-speed all electric injection molding machine
- Honeycomb rotor dehumidifier
- horizontal injection molding machine
- Horizontal Injection Molding Machines
- Horizontal Injection Moulding Machine
- Horizontal Mixer manufacturer
- How The CNC Machine Works
- hybrid injection molding machine
- hydraulic injection molding machine
- Hydraulic Injection Molding Machines
- in this article
- Industrial robot
- Industrial Robot Chinese brand
- industrial robot parts
- industrial robot supplier
- Industrial robots
- Industry Chain
- Injection Manipulator
- injection manipulator robot
- injection mold machines
- Injection molding
- Injection molding automation
- Injection Molding Automation Solution
- injection molding dryer
- Injection molding equipment
- injection molding hopper dryer
- Injection molding machine
- injection molding machine brand
- Injection Molding Machine Factory
- Injection Molding Machine Manufacture
- Injection molding machine manufacturer
- injection molding machine manufacturers
- Injection molding machine procurement
- injection molding machine robotic arm
- injection molding machine with a robot
- Injection molding machines
- injection molding material dehumidifying
- injection molding plant
- Injection Molding Robot
- injection molding robot arm
- Injection molding robot automation
- Injection molding robotic arm
- injection molding robots
- Injection moulding machine
- Injection Moulding Robots
- Injection Robot
- Injection robot arm
- Injection robot manufacturer
- Injection robot wholesale
- injection robots
- intelligent injection molding machines
- Introducing Injection Robot
- It is the best choice for drying large quantities of material at once. Cabinetmakers use these machines because they are fast
- large injection molding machine
- Learn what industrial automation and robotics is
- linear robot
- linear robots
- low speed sound-proof granulator
- machine plastic molding
- make sure to add some! Improvements (2) Keyphrase in introduction: Your keyphrase or its synonyms appear in the first paragraph of the copy
- manipulator machine
- manufacturing
- medical grade injection molding machines
- medical injection molding machine
- medical injection molding machines
- micro injection molding machine
- middle speed granulator
- Mini CNC machine manufacturers.
- Mold Temperature Control System
- mold temperature controller
- mold temperature controllers
- molding material Dehumidifying System
- mould temperature control system
- mould temperature controller
- mould temperature controllers
- New electric injection molding machine
- nitrogen dryer manufacturer
- nitrogen dryer system manufacturer
- Oil type mold temperature controller
- Oil type mold temperature controllers
- open day
- Outbound links: No outbound links appear in this page. Add some! Images: No images appear on this page. Add some! Internal links: No internal links appear in this page
- PET Preform injection molding
- phone case maker machine
- phone case making machine
- plastic bottle making machine
- plastic bottle manufacturing
- plastic bucket making machine
- plastic bucket manufacturing
- Plastic chair making machine
- plastic forming equipment
- plastic hopper dryer
- plastic injection machine
- plastic injection machines
- plastic injection molding
- Plastic injection molding equipment
- Plastic injection molding machine
- Plastic Injection Molding Machines
- plastic injection moulding machine
- plastic injection robot
- Plastic Molding machine
- Plastic Molding Machines
- plastic molding press
- plastic moulding machine
- plastic phone case making machine
- plastic-molding machine
- powerful granulator
- Powerful Type Sound-Proof Granulator
- precision injection molding
- precision injection molding machines
- production of plastic seats
- pure water mould temperature controller
- Robot injection molding
- robot injection molding machine
- robot manufacturing companies
- Robotic arm for injection molding machine
- robotic injection molding machines
- robotics in injection molding
- SCARA robot
- SCARA robots
- Service-oriented manufacturing
- Servo Cylinder Robot
- servo driven robot
- Servo Driven Robots
- servo injection robots
- servo motor-driven linear robots
- servo-driven 3-axis robot
- Servo-Driven Robot
- Setup of injection machine
- Silicone Injection Molding Machine
- six-axis industrial robot
- Stainless Hopper Dryer
- Stainless Hopper Dryers
- star club
- swing arm robot
- take-out robots
- the choice between servo-driven robots and hydraulic robots will have a certain impact on efficiency
- the most popular injection molding machine
- the type of injection molding robot
- toggle clamp injection molding machine
- Toggle Hydraulic Injection Molding Machines
- toggle injection molding machine
- Top 10 brands of injection robots
- Topstar
- Topstar Engineering
- Topstar Industrial Robots
- Topstar injection molding intelligent
- Topstar Scara Robots
- Useful Injection molding machine
- Vertical machining centers
- volumetric type blender
- water chiller
- water chillers
- water distributor
- water type mold temperature controller
- Water Type MoldTemperature Controller
- Water-Type Mould Temperature Controllers
- We often face choices when performing injection molding. We will choose the type of injection molding machine
- wholesale of injection molding machines
- x carve CNC