What are Machining Parameters of The Manipulator?
2022/04/28 By Topstar
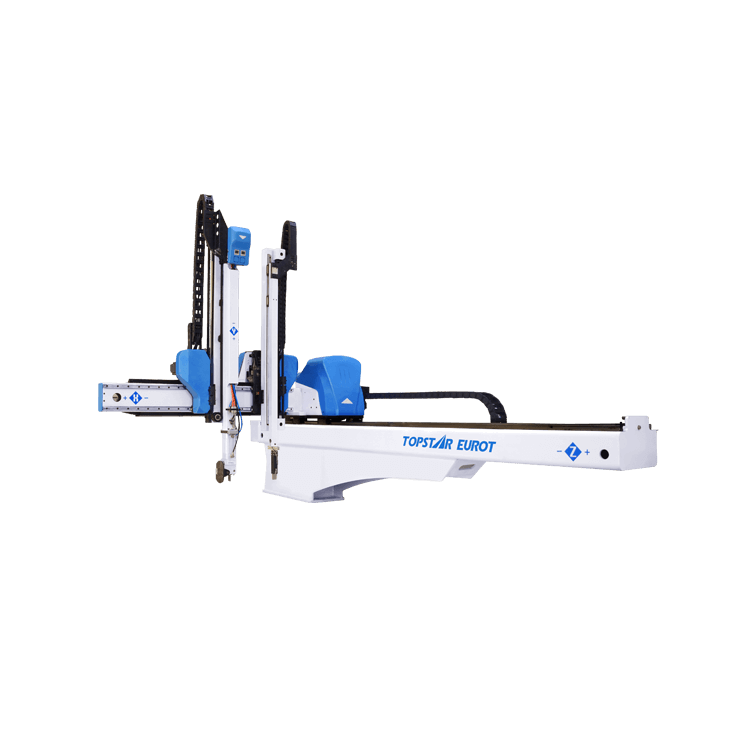
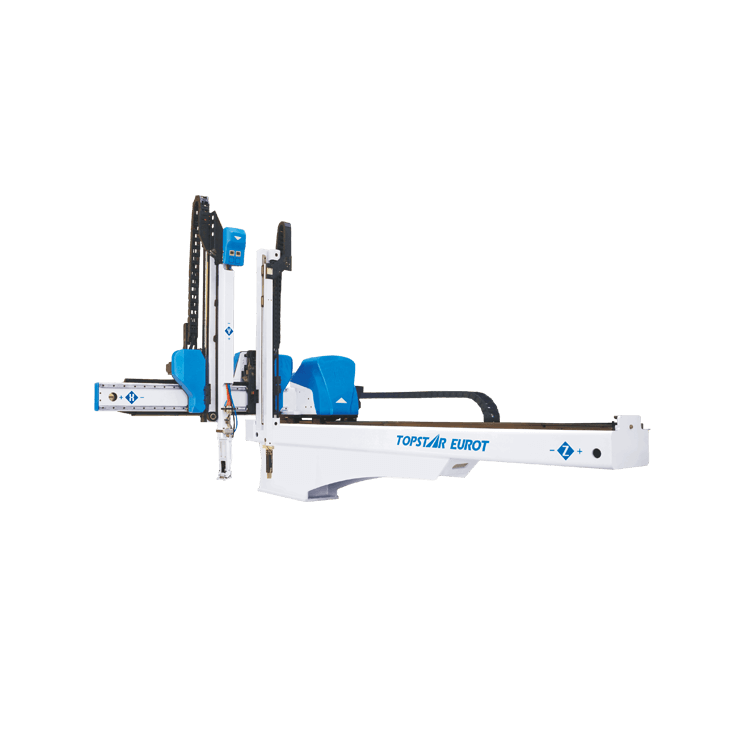
The clamping system of the manipulator has the primary function of opening and closing the mold and creating a clamp to hold the mold during the cooling process. Moreover, at the same time, this system also has another task of pushing the product out of the mold after the end of the pressing cycle.
The main structure of a clamping system includes:
- Push unit of manipulator
- Pliers assembly
- movable plate
- Fixed plate
- Connection bar
Mold system of injection molding manipulator
The plastic injection molding manipulator‘s injection mold is known to be an essential part of the plastic product processing process. Moreover, the manipulator must ensure high accuracy with a minimal design tolerance ratio.
After the plasticization process, the molten plastic is injected into the mold. At this time, the mold pressure must be large enough to close the mold until the plastic cools and hardens.
Moreover, the structure of a mold system will include:
- Two fixed cutting boards and one movable cutting board to open the mold
- Parallel cylindrical 4-axis guide shaft
- Mold lock cylinder: Create force to open and close the mold
- Hydraulic cylinder for extruding products
- Die thickness adjuster: electric or hydraulic motor drive.
- Safety door front door and back door
The manipulator: central control system
The control system will help the manipulator operator monitor and adjust the machining parameters, temperature, pressure, and injection speed. This control process can directly affect product quality and economic efficiency. A central control system will include two main components: a computer screen and a control panel.
Structure of injection molding manipulator
Machining parameters of injection molding manipulator
Moreover, to design a complete injection molding manipulator equipment, the machining parameters are one of the critical factors for the manufacturer to manufacture the manipulator. Typically, an injection molding manipulator will include four main parameters:
Injection volume: The manipulator will have a casting volume of 230,000cm3. In addition, many businesses also use a manipulator with a spray volume of 6,125,500cm3.
Injection speed: With an injection molding manipulator, speed will directly affect the product shape. Moreover, if the rate is not up to the standard, your plastic product will not have a glossy stretch, uniform in all positions.
Injection pressure: The adjustment will depend on the mold structure, the type of plastic material, and the processing temperature. In addition, the injection time is also a factor affecting the pressure of the injection molding manipulator.
Pressed area: This machining parameter will be determined by the basic parameters of the manipulator. In addition, the pressing area of the injection molding manipulator will directly affect the mold clamping. Mold size and some other parameters.
Mold design: creating a set of 3D molds
It is the process of creating a set of 3D molds on a computer based on the characteristics and specifications of a product. This process can apply to new products or those that must be recreated in real life.
Moreover, you can use the following software to simplify the mold design process: AutoCAD, Catia, etc. The manipulator will allow you to build all the necessary mold details. At the same time, you can accurately represent the mold plates’ dimensions, spirals, etc..
In addition, with molds with complex structures requiring high sophistication, engineers must show every tiny detail clearly because the machining process will be challenging to cover all the details. Therefore, small pieces will easily be overlooked. This will directly affect the quality of both the mold design and product forming processes.
The manipulator: mold design classification
The mold classification will contribute to simplifying the mold design process. Because then, casting engineers can more easily shape their mold design to suit the customer’s use. Currently, molds are divided into seven different classifications:
What is Plastic injection mold?
Plastic injection mold is also known as KEN for short. This set of tools is used to shape products based on customer drawings. Besides, the plastic injection mold will include many parts put together. Next, all liquefied plastic will be sprayed into the mold cavity and then cooled to shape the product. The manipulator engineers will need extensive experience in mold cavity processing.
Moreover, one of the other designs of the die is the punching die. This is a tool that uses impact force to conduct shaping and shaping plastic products.
This type of mold is commonly used to make details for thin metal and alloy plates in a cold state under pressure. In terms of structure, the design of the stamping die will include the punch and the die.
Hot stamping mold uses a die-making process.
Hot stamping dies design is a commonly used die-making process for metal working by pressure in a desirable state. Moreover, the raw material must be heated to a high temperature when processing with the manipulator.
After this process, you must wait a while for the workpiece to return to room temperature. You will receive a product similar to the design at the end of the process.
Cold stamping mold
A cold stamping die is a set of molds that use pressure to shape a workpiece in an unconscious state. Therefore, the design of a cold stamping die will require high precision and a careful calculation of the materials used to make the mold. Moreover, the high pressure will cause the mold to deviate from its position during punching if you do not choose a suitable hammer material.
The manipulator: standard plastic mold design processes
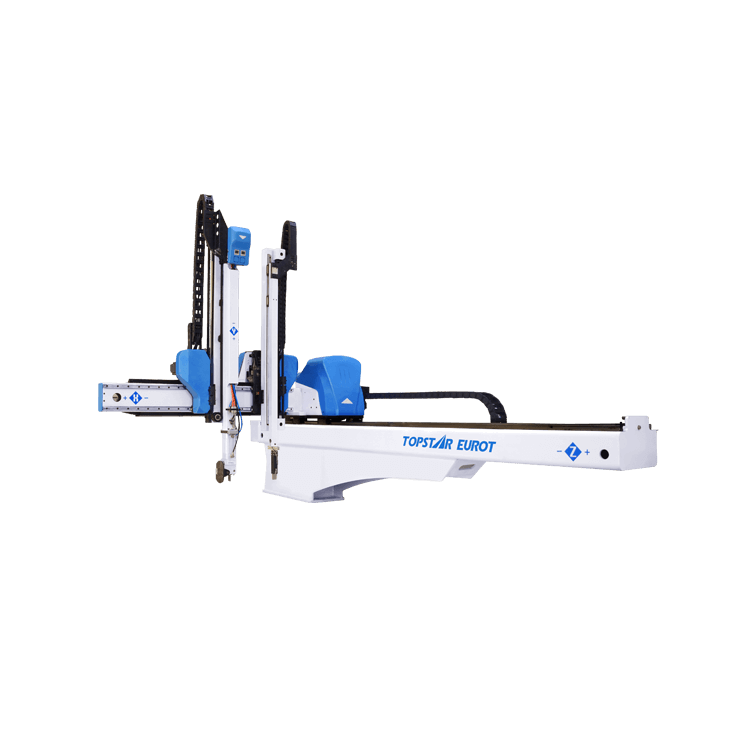
The entire stamping die design process will go through 4 steps:
Step 1: Calculate the exact cutting force of the product. After receiving samples from partners, design engineers will need to determine the stamping force used for the product. Moreover, the difference in the magnitude of the stamping force will depend on the size and shape of the product.
Step 2: Select the manipulator with a capacity suitable for the design. Currently, many businesses have used multi-purpose stamping manipulators. Therefore, they can flexibly adjust the ability to match the processing needs of the product.
Step 3: Calculate the height and size of the detailed mold. Moreover, engineers will need to detail each size on the design so that the technical staff can process the product most efficiently.
Step 4: Use design software to create shapes for products. Depending on the model, engineers will choose 2D or 3D software. Currently, there are several design software used by many casting engineers: AutoCAD, Catia, etc. Using the software, the die design will show the parameters of each part.
TRENDING POSTS
- What factors can cause delays in the injection molding process of plastic molding machine? 2022/04/28
- Exhibition Review| Topstar participates in InterPlas Thailand 2024 2022/04/28
- Star Case | Topstar helps Santong upgrade its intelligent plant 2022/04/28
- Topstar Special | National Science and Technology Workers Day 2022/04/28
HOT TOPIC
- .ervo motor-driven linear robots
- 3 axis robot
- 3 axis robots
- 3 in 1 Compact Dehumidifying Dryer
- 3-axis robot
- 3-axis robots
- 5-axis CNC machine
- accuracy
- Air Chillers
- all electric injection molding machine
- all electric injection molding machines
- All-electric injection molding machines
- and overall production quality. Therefore
- AP-RubberPlas
- automated injection molding machine
- Automation changed engineering
- automation of injection molding robots
- auxiliary machine
- Bench Injection Molding Machine
- Cabinet dryer manufacturers
- Cabinet dryers
- chiller
- CNC Drilling Machine
- CNC Drilling Machines
- cnc engraving machine manufacturer
- cnc laser cutting machine manufacturer
- CNC machine
- CNC Machine Center
- CNC Machine for Sale
- CNC Machine Manufacturing
- CNC Machine Tool
- CNC machine tool product
- CNC Machining Center
- CNC wood carving machine
- Cooling system
- Cross-Walking Single Axis Servo Cylinder Robot
- Cross-Walking Single-Axis Servo Cylinder Robot
- Cross-Walking Three-Axis/Five-Axis Servo Driven Robot
- cross-walking three-axis/five-axis servo-driven robot
- Dehumidifier Dryer
- Dehumidifying Dryer
- delta parallel robot
- Desktop Injection Molding Machine
- Desktop injection molding machines
- Desktop Molding Machine
- desktop plastic injection machine
- Desktop Plastic Injection Molding Machine
- direct clamp injection molding machine
- Direct clamp injection molding machines
- Dosing & mixing system
- Drilling Centers
- Drying and dehumidification system
- drying and dehumidifying equipment
- Drying and Dehumidifying System
- drying system
- effective and efficient. Cabinet dryers are also used in other industries where large quantities of material need to be dried
- efficient injection molding machine
- elbow hydraulic injection molding machines
- electric injection molding machine
- electric injection molding machines
- energy-efficient injection molding robot
- energy-saving injection molding machine
- etc. Among injection molding robots
- exhibition
- features of CNC machine
- Feeding And Conveying System
- Five Axis Machine Center
- Fully automatic injection molding machine
- Gathering Topstar
- giant injection molding machine
- GMU-600 5-Axis Machining Center
- Granulating & Recycling System
- Heavy duty injection molding machine
- High-precision electric molding machines
- high-precision plastic molding machines
- high-speed all electric injection molding machine
- Honeycomb rotor dehumidifier
- horizontal injection molding machine
- Horizontal Injection Molding Machines
- Horizontal Injection Moulding Machine
- Horizontal Mixer manufacturer
- How The CNC Machine Works
- hybrid injection molding machine
- hydraulic injection molding machine
- Hydraulic Injection Molding Machines
- in this article
- Industrial robot
- Industrial Robot Chinese brand
- industrial robot parts
- industrial robot supplier
- Industrial robots
- Industry Chain
- Injection Manipulator
- injection manipulator robot
- injection mold machines
- Injection molding
- Injection molding automation
- Injection Molding Automation Solution
- injection molding dryer
- Injection molding equipment
- injection molding hopper dryer
- Injection molding machine
- injection molding machine brand
- Injection Molding Machine Factory
- Injection Molding Machine Manufacture
- Injection molding machine manufacturer
- injection molding machine manufacturers
- Injection molding machine procurement
- injection molding machine robotic arm
- injection molding machine with a robot
- Injection molding machines
- injection molding material dehumidifying
- injection molding plant
- Injection Molding Robot
- injection molding robot arm
- Injection molding robot automation
- Injection molding robotic arm
- injection molding robots
- Injection moulding machine
- Injection Moulding Robots
- Injection Robot
- Injection robot arm
- Injection robot manufacturer
- Injection robot wholesale
- injection robots
- intelligent injection molding machines
- Introducing Injection Robot
- It is the best choice for drying large quantities of material at once. Cabinetmakers use these machines because they are fast
- large injection molding machine
- large injection molding machines
- Learn what industrial automation and robotics is
- linear robot
- linear robots
- low speed sound-proof granulator
- machine plastic molding
- make sure to add some! Improvements (2) Keyphrase in introduction: Your keyphrase or its synonyms appear in the first paragraph of the copy
- manipulator machine
- manufacturing
- medical grade injection molding machines
- medical injection molding machine
- medical injection molding machines
- micro injection molding machine
- middle speed granulator
- Mini CNC machine manufacturers.
- Mold Temperature Control System
- mold temperature controller
- mold temperature controllers
- molding material Dehumidifying System
- mould temperature control system
- mould temperature controller
- mould temperature controllers
- New electric injection molding machine
- nitrogen dryer manufacturer
- nitrogen dryer system manufacturer
- Oil type mold temperature controller
- Oil type mold temperature controllers
- open day
- Outbound links: No outbound links appear in this page. Add some! Images: No images appear on this page. Add some! Internal links: No internal links appear in this page
- PET Preform injection molding
- phone case maker machine
- phone case making machine
- plastic bottle making machine
- plastic bottle manufacturing
- plastic bucket making machine
- plastic bucket manufacturing
- Plastic chair making machine
- plastic forming equipment
- plastic hopper dryer
- plastic injection machine
- plastic injection machines
- plastic injection molding
- Plastic injection molding equipment
- Plastic injection molding machine
- Plastic Injection Molding Machines
- plastic injection moulding machine
- plastic injection robot
- Plastic Molding machine
- Plastic Molding Machines
- plastic molding press
- plastic moulding machine
- plastic phone case making machine
- plastic-molding machine
- powerful granulator
- Powerful Type Sound-Proof Granulator
- precision injection molding
- precision injection molding machines
- production of plastic seats
- pure water mould temperature controller
- Robot injection molding
- robot injection molding machine
- robot manufacturing companies
- Robotic arm for injection molding machine
- robotic injection molding machines
- robotics in injection molding
- SCARA robot
- SCARA robots
- Service-oriented manufacturing
- Servo Cylinder Robot
- servo driven robot
- Servo Driven Robots
- servo injection robots
- servo motor-driven linear robots
- servo-driven 3-axis robot
- Servo-Driven Robot
- Setup of injection machine
- Silicone Injection Molding Machine
- six-axis industrial robot
- Stainless Hopper Dryer
- Stainless Hopper Dryers
- star club
- swing arm robot
- take-out robots
- the choice between servo-driven robots and hydraulic robots will have a certain impact on efficiency
- the most popular injection molding machine
- the type of injection molding robot
- toggle clamp injection molding machine
- Toggle Hydraulic Injection Molding Machines
- toggle injection molding machine
- Top 10 brands of injection robots
- Topstar
- Topstar Engineering
- Topstar Industrial Robots
- Topstar injection molding intelligent
- Topstar Scara Robots
- Useful Injection molding machine
- Vertical machining centers
- volumetric type blender
- water chiller
- water chillers
- water distributor
- water type mold temperature controller
- Water Type MoldTemperature Controller
- Water-Type Mould Temperature Controllers
- We often face choices when performing injection molding. We will choose the type of injection molding machine
- wholesale of injection molding machines
- x carve CNC