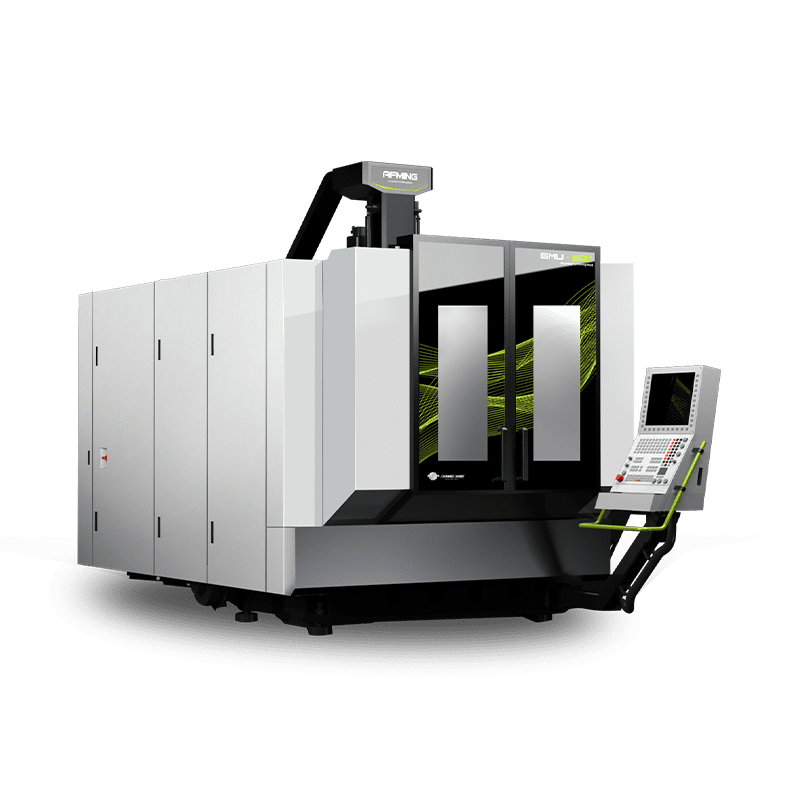
The CNC Machine Center is a cutting-edge production tool that can carry out several machining operations with excellent quality, surface finish, and precision.
Manufacturing prismatic parts for the industry, like gearboxes, partitions, frames, and covers, necessitates various machining processes, including milling, boring, drilling, tapping, and many more.
In the past, there were many working stages in this production process, and it took a lot of time and money to provide the finished product due to the operation of several machine tools. To solve this problem. One machine may handle various machining needs by performing milling, lathing, and drilling operations.
Here are the few types of CNC Machine Centre:
CNC Machine Center for Horizontal Machining
The tool is fitted on the horizontal spindle of the CNC machine, which is classically a sole spindle machine with a programmed tool changer in its machining center.
APC (an automatic pallet changer) can load and unload quickly. The APC has six, eight, or more pallets, each of which can hold a workpiece while the machine is programmed to finish the pallet before it. A new tray is changed after working.
CNC Machine Center for Vertical Machining
This kind of equipment allows for the completion of numerous tasks simultaneously. Most vertical machining centers have three axes, while some can also act as spindle heads with one or two axes of rotation.
The VMC (Vertical Machining Center) is appropriate for the molding process. The three elementary categories of VMC include Multi Spindles, Columns, and Gantry Structures.
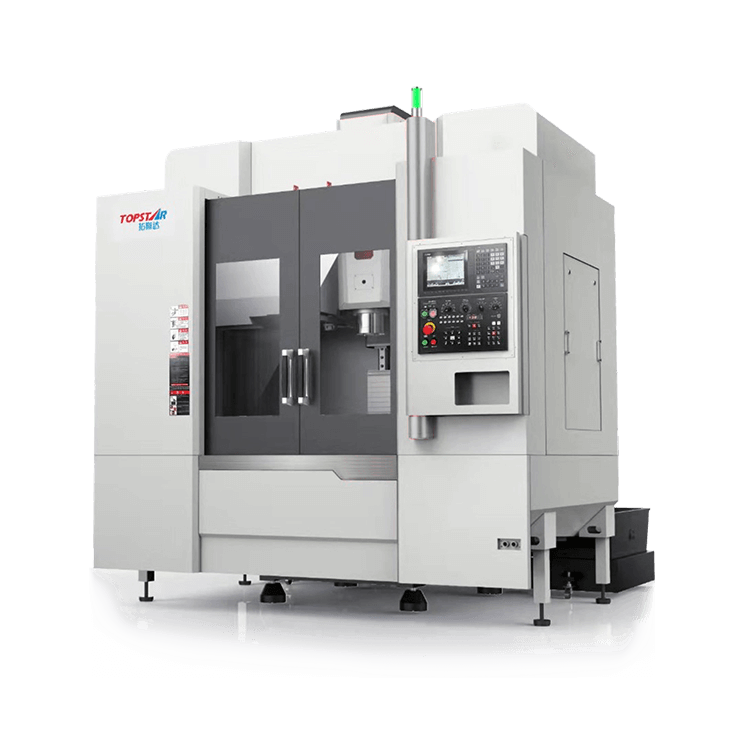
CNC Machine Center for Universal Machining
The universal Machining Centre is comparable to a horizontal one. It has a computerized control tilting feature. The top surface of the workpiece usually uses a universal machine center, which has five or more axes. It allows machining the work piece’s various sides as a single unit.
Applications
Milling is a treatment process. It gives professional artisans a superior method for expertly cutting, milling, drilling, tapping, and shaping steel for various applications and purposes. CNC controllers are only one example of how technology advancements have sped up and simplified manufacturing.
You know the value of high-quality, adaptable equipment if you operate in a machine shop. Due to the need to cut and remove material manually, vertical machining centers have advanced significantly.
Features & Advantages
CNC machines are crucial for automating mechanical parts manufacturing to boost throughput and keep quality constant. An efficient machine type depends heavily on its CNC Machine Center.
Speed
Speed is a significant factor that drives efficiency. High-speed CNC Machine centers shorten the cycle time of CNC machine activities. One illustration is moving the spindle home to change tools and correctly placing the cutting tool before cutting.
Cutting feeds can go over 300 ppm, a rough estimate for face-milling aluminum, depending on several variables (material, path, depth of cut, and part). Additionally, every operation is completed within a few thousandths of a millimeter, including the machine’s repeated location of every feature.
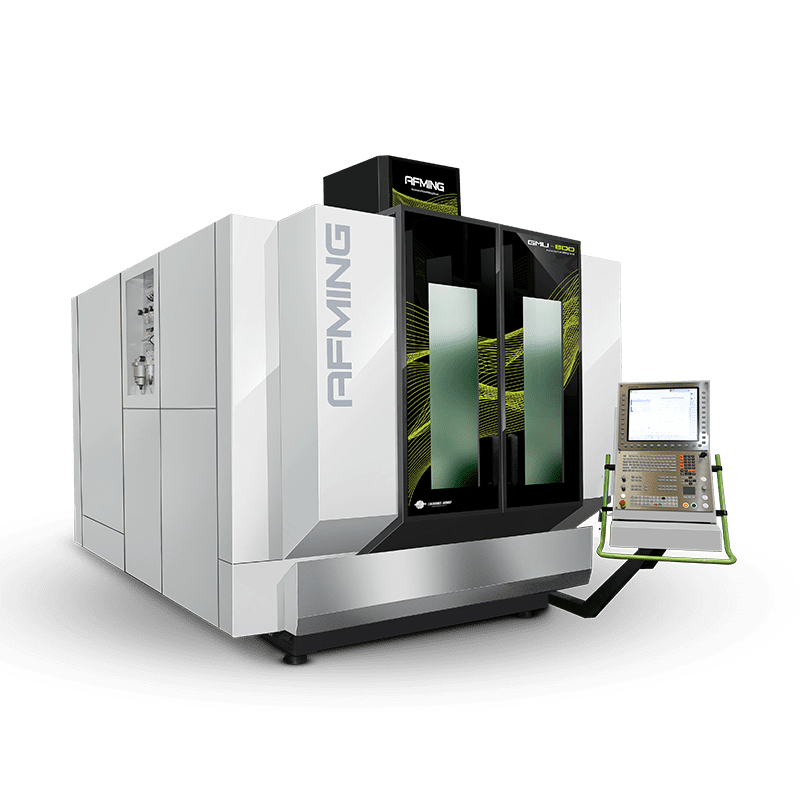
Precision
Precision machining is frequently the solution when strict tolerance requirements for a workpiece must be met. Due to its design and construction, CNC machines can cut with an accuracy 0.001″. That is a blatant case of dividing hairs. In addition, it is completed at astonishing speeds.
Repeatability
A CNC machine consistently repeats all steps while operating from a computer program that always and precisely manages the machining procedure. In routine operations, repeatability problems often include the rigidity of a part and work staying, or the tooling is wearing out rather than the machine’s functionality.
Programmable
The fundamental principle of CNC machining is straightforward: Use machine programming to meet the requirements of setting up multiple tool processing parts. Engineers frequently employ a visible 3D software application that generates G-code For CNC machine tools. Engineers or the production crew do remote download and upload of programs to and from a CNC machine.
Adaptable
The setup procedure is setting up a CNC machine to operate a new part. Each part has a unique design, and interchangeable fixtures hold the details in the machine for processing.
Therefore, the system will change the programming when a new operation starts to make CNC machines adaptable to produce different parts, tools, and fixtures. Having devices of the same type, each capable of running a specific amount increases flexibility.
Automatic Coin Changers
A CNC machine uses an automatic tool changer to change tools (ATC). The system starts the cutting features with a face mill and switches to another device, similar to a portable drill; when this one is finished, the program manages tooling and operations.
Switching two trays with many CNC machines using APC (Automatic Tray Changer). While one pallet is in the cutting area, the other is accessible to the operator for loading, unloading, processing, etc.
Hydraulic Devices
Hydraulic systems support, clamp, and unclamp the part. Clamp the components according to the same pressure and sequence by pressing a button. In production machining, repeatability and accuracy significantly improve loading efficiency.
Conclusion
CNC Machine Center is considered a highly effective tool. CNC machine tools are equipped with additional hardware to automate part processing better. Topstar is regarded as a trustworthy enterprise for buying CNC Machines. This enterprise is famous for providing cost-effective, reliable, and highly advanced version products. For further queries, you can visit their website 24/7.
TRENDING POSTS
- What factors can cause delays in the injection molding process of plastic molding machine? 2022/08/13
- Exhibition Review| Topstar participates in InterPlas Thailand 2024 2022/08/13
- Star Case | Topstar helps Santong upgrade its intelligent plant 2022/08/13
- Topstar Special | National Science and Technology Workers Day 2022/08/13
HOT TOPIC
- .ervo motor-driven linear robots
- 3 axis robot
- 3 axis robots
- 3 in 1 Compact Dehumidifying Dryer
- 3-axis robot
- 3-axis robots
- 5-axis CNC machine
- accuracy
- Air Chillers
- all electric injection molding machine
- all electric injection molding machines
- All-electric injection molding machines
- and overall production quality. Therefore
- AP-RubberPlas
- automated injection molding machine
- Automation changed engineering
- automation of injection molding robots
- auxiliary machine
- Bench Injection Molding Machine
- Cabinet dryer manufacturers
- Cabinet dryers
- chiller
- CNC Drilling Machine
- CNC Drilling Machines
- cnc engraving machine manufacturer
- cnc laser cutting machine manufacturer
- CNC machine
- CNC Machine Center
- CNC Machine for Sale
- CNC Machine Manufacturing
- CNC Machine Tool
- CNC machine tool product
- CNC Machining Center
- CNC wood carving machine
- Cooling system
- Cross-Walking Single Axis Servo Cylinder Robot
- Cross-Walking Single-Axis Servo Cylinder Robot
- Cross-Walking Three-Axis/Five-Axis Servo Driven Robot
- cross-walking three-axis/five-axis servo-driven robot
- Dehumidifier Dryer
- Dehumidifying Dryer
- delta parallel robot
- Desktop Injection Molding Machine
- Desktop injection molding machines
- Desktop Molding Machine
- desktop plastic injection machine
- Desktop Plastic Injection Molding Machine
- direct clamp injection molding machine
- Direct clamp injection molding machines
- Dosing & mixing system
- Drilling Centers
- Drying and dehumidification system
- drying and dehumidifying equipment
- Drying and Dehumidifying System
- drying system
- effective and efficient. Cabinet dryers are also used in other industries where large quantities of material need to be dried
- efficient injection molding machine
- elbow hydraulic injection molding machines
- electric injection molding machine
- electric injection molding machines
- energy-efficient injection molding robot
- energy-saving injection molding machine
- etc. Among injection molding robots
- exhibition
- features of CNC machine
- Feeding And Conveying System
- Five Axis Machine Center
- Fully automatic injection molding machine
- Gathering Topstar
- giant injection molding machine
- GMU-600 5-Axis Machining Center
- Granulating & Recycling System
- Heavy duty injection molding machine
- High-precision electric molding machines
- high-precision plastic molding machines
- high-speed all electric injection molding machine
- Honeycomb rotor dehumidifier
- horizontal injection molding machine
- Horizontal Injection Molding Machines
- Horizontal Injection Moulding Machine
- Horizontal Mixer manufacturer
- How The CNC Machine Works
- hybrid injection molding machine
- hydraulic injection molding machine
- Hydraulic Injection Molding Machines
- in this article
- Industrial robot
- Industrial Robot Chinese brand
- industrial robot parts
- industrial robot supplier
- Industrial robots
- Industry Chain
- Injection Manipulator
- injection manipulator robot
- injection mold machines
- Injection molding
- Injection molding automation
- Injection Molding Automation Solution
- injection molding dryer
- Injection molding equipment
- injection molding hopper dryer
- Injection molding machine
- injection molding machine brand
- Injection Molding Machine Factory
- Injection Molding Machine Manufacture
- Injection molding machine manufacturer
- injection molding machine manufacturers
- Injection molding machine procurement
- injection molding machine robotic arm
- injection molding machine with a robot
- Injection molding machines
- injection molding material dehumidifying
- injection molding plant
- Injection Molding Robot
- injection molding robot arm
- Injection molding robot automation
- Injection molding robotic arm
- injection molding robots
- Injection moulding machine
- Injection Moulding Robots
- Injection Robot
- Injection robot arm
- Injection robot manufacturer
- Injection robot wholesale
- injection robots
- intelligent injection molding machines
- Introducing Injection Robot
- It is the best choice for drying large quantities of material at once. Cabinetmakers use these machines because they are fast
- large injection molding machine
- large injection molding machines
- Learn what industrial automation and robotics is
- linear robot
- linear robots
- low speed sound-proof granulator
- machine plastic molding
- make sure to add some! Improvements (2) Keyphrase in introduction: Your keyphrase or its synonyms appear in the first paragraph of the copy
- manipulator machine
- manufacturing
- medical grade injection molding machines
- medical injection molding machine
- medical injection molding machines
- micro injection molding machine
- middle speed granulator
- Mini CNC machine manufacturers.
- Mold Temperature Control System
- mold temperature controller
- mold temperature controllers
- molding material Dehumidifying System
- mould temperature control system
- mould temperature controller
- mould temperature controllers
- New electric injection molding machine
- nitrogen dryer manufacturer
- nitrogen dryer system manufacturer
- Oil type mold temperature controller
- Oil type mold temperature controllers
- open day
- Outbound links: No outbound links appear in this page. Add some! Images: No images appear on this page. Add some! Internal links: No internal links appear in this page
- PET Preform injection molding
- phone case maker machine
- phone case making machine
- plastic bottle making machine
- plastic bottle manufacturing
- plastic bucket making machine
- plastic bucket manufacturing
- Plastic chair making machine
- plastic forming equipment
- plastic hopper dryer
- plastic injection machine
- plastic injection machines
- plastic injection molding
- Plastic injection molding equipment
- Plastic injection molding machine
- Plastic Injection Molding Machines
- plastic injection moulding machine
- plastic injection robot
- Plastic Molding machine
- Plastic Molding Machines
- plastic molding press
- plastic moulding machine
- plastic phone case making machine
- plastic-molding machine
- powerful granulator
- Powerful Type Sound-Proof Granulator
- precision injection molding
- precision injection molding machines
- production of plastic seats
- pure water mould temperature controller
- Robot injection molding
- robot injection molding machine
- robot manufacturing companies
- Robotic arm for injection molding machine
- robotic injection molding machines
- robotics in injection molding
- SCARA robot
- SCARA robots
- Service-oriented manufacturing
- Servo Cylinder Robot
- servo driven robot
- Servo Driven Robots
- servo injection robots
- servo motor-driven linear robots
- servo-driven 3-axis robot
- Servo-Driven Robot
- Setup of injection machine
- Silicone Injection Molding Machine
- six-axis industrial robot
- Stainless Hopper Dryer
- Stainless Hopper Dryers
- star club
- swing arm robot
- take-out robots
- the choice between servo-driven robots and hydraulic robots will have a certain impact on efficiency
- the most popular injection molding machine
- the type of injection molding robot
- toggle clamp injection molding machine
- Toggle Hydraulic Injection Molding Machines
- toggle injection molding machine
- Top 10 brands of injection robots
- Topstar
- Topstar Engineering
- Topstar Industrial Robots
- Topstar injection molding intelligent
- Topstar Scara Robots
- Useful Injection molding machine
- Vertical machining centers
- volumetric type blender
- water chiller
- water chillers
- water distributor
- water type mold temperature controller
- Water Type MoldTemperature Controller
- Water-Type Mould Temperature Controllers
- We often face choices when performing injection molding. We will choose the type of injection molding machine
- wholesale of injection molding machines
- x carve CNC