Troubleshooting Common Issues with Injection Molding Robot
2023/10/20 By Topstar
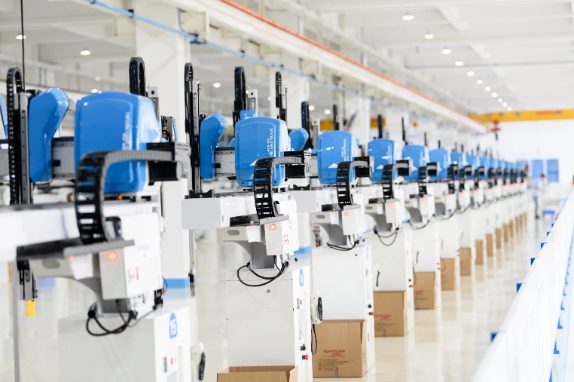
Injection molding robots have revolutionized manufacturing, significantly improving efficiency and precision. However, like any complex system, they can face technical glitches. In this comprehensive guide, we’ll explore common problems that can arise when using injection molding robot and provide practical solutions. Understanding these challenges and how to solve them is critical to ensuring the manufacturing process runs smoothly and maximizing the benefits of automation.
1. Injection molding robot calibration and accuracy challenges
Injection molding requires high precision, and even minor alignment issues can cause defects in the final product. Problems can occur due to incorrect positioning, tool wear, or mechanical misalignment. These issues can result in poor-quality parts.
Solution: Regular calibration and maintenance are crucial to solving this problem. Implement a thorough calibration procedure, check for mechanical wear, and ensure the robot is accurately aligned with the mold and injection unit. Or consider investing in an automated calibration system, which reduces human error and provides the highest accuracy in the calibration process. This not only improves product quality but also optimizes robot performance.
2. Injection molding robot communication error
In an automated environment, communication is crucial. Communication errors between robots and injection molding machines can cause production delays and mistakes. These errors can be frustrating, whether it’s a programming language, data transfer, or compatibility issue.
Solution: Check the injection molding robot‘s programming and communication protocols. Ensure compatibility with your injection molding machine. Software is regularly updated to address known bugs, and operators are trained to resolve minor communications glitches. Implement redundant communication systems to minimize the risk of errors. This dual-channel approach ensures that even if one communication path encounters a problem, the backup system can seamlessly take over, reducing downtime.
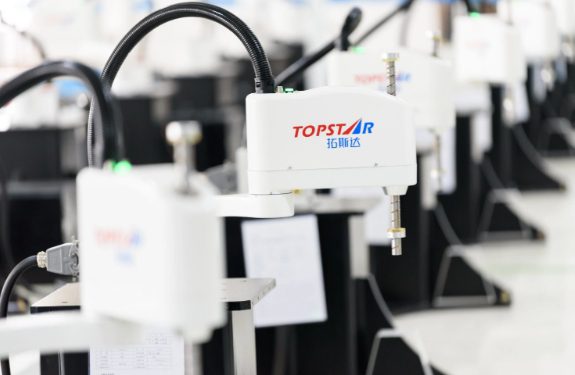
3. Injection molding robot overheating and motor failure
Overheating and motor failure can lead to costly downtime. An overworked or damaged motor can overheat, potentially causing safety issues and affecting the robot’s performance.
Solution: Implement a regular maintenance schedule to inspect and replace worn parts. Ensure the cooling system functions correctly and the injection molding robot operates within the specified temperature range. Monitoring motion performance is critical to identifying early signs of failure. A real-time monitoring system is also installed to evaluate motor temperature and performance continuously. If overheating is detected, these systems can automatically shut down the robot, preventing damage and ensuring safety.
4. Payload Limitation
Exceeding the payload limit of an injection molding robot is a common problem, especially when handling heavy molds or complex tooling setups. This can lead to shortened robot life, reduced accuracy, and potential accidents.
Solution: Carefully evaluate your robot’s payload capacity and stay within its limitations. Invest in a suitable robot model for your application. Consider using lightweight tools to reduce stress on the robot. Implement a load monitoring system that provides real-time data on the weight being processed. These systems can automatically stop an injection molding robot if it approaches or exceeds its payload limit, preventing overloading and maintaining the integrity of the robot.
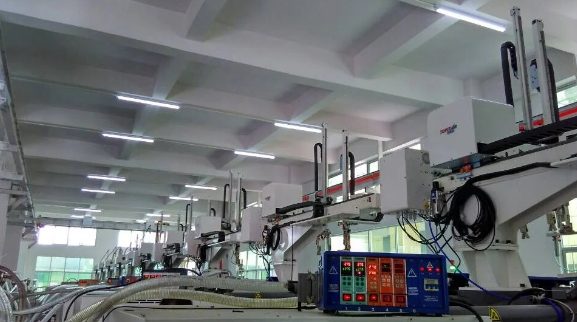
5. Sensor and vision system failure
Many injection molding robots rely on sensors and vision systems for precise placement and quality control. Sensor or vision system failure can result in incorrect part placement, increasing scrap rates.
Solution: Maintain sensors and vision systems regularly. Keep them clean and ensure they are calibrated correctly. Having spare sensors and vision components on hand can help reduce downtime during a failure. I can also use advanced sensor diagnostics to detect faults and predict potential problems. This proactive approach allows for preventive maintenance, reducing unplanned downtime and increasing efficiency.
Final summary
Solving everyday problems with injection molding robots is integral to ensuring a smooth and efficient manufacturing process. By addressing calibration challenges, communication errors, overheating and motor failures, payload limitations, sensor and vision system issues, software and programming glitches, and safety issues, manufacturers can unlock the full potential of these automated systems. If you still have other problems with your injection molding robot, you are always welcome to consult our official website!
TRENDING POSTS
- What factors can cause delays in the injection molding process of plastic molding machine? 2023/10/20
- Exhibition Review| Topstar participates in InterPlas Thailand 2024 2023/10/20
- Star Case | Topstar helps Santong upgrade its intelligent plant 2023/10/20
- Topstar Special | National Science and Technology Workers Day 2023/10/20
HOT TOPIC
- .ervo motor-driven linear robots
- 3 axis robot
- 3 axis robots
- 3 in 1 Compact Dehumidifying Dryer
- 3-axis robot
- 3-axis robots
- 5-axis CNC machine
- accuracy
- Air Chillers
- all electric injection molding machine
- all electric injection molding machines
- All-electric injection molding machines
- and overall production quality. Therefore
- AP-RubberPlas
- automated injection molding machine
- Automation changed engineering
- automation of injection molding robots
- auxiliary machine
- Bench Injection Molding Machine
- Cabinet dryer manufacturers
- Cabinet dryers
- chiller
- CNC Drilling Machine
- CNC Drilling Machines
- cnc engraving machine manufacturer
- cnc laser cutting machine manufacturer
- CNC machine
- CNC Machine Center
- CNC Machine for Sale
- CNC Machine Manufacturing
- CNC Machine Tool
- CNC machine tool product
- CNC Machining Center
- CNC wood carving machine
- Cooling system
- Cross-Walking Single Axis Servo Cylinder Robot
- Cross-Walking Single-Axis Servo Cylinder Robot
- Cross-Walking Three-Axis/Five-Axis Servo Driven Robot
- cross-walking three-axis/five-axis servo-driven robot
- Dehumidifier Dryer
- Dehumidifying Dryer
- delta parallel robot
- Desktop Injection Molding Machine
- Desktop injection molding machines
- Desktop Molding Machine
- desktop plastic injection machine
- Desktop Plastic Injection Molding Machine
- direct clamp injection molding machine
- Direct clamp injection molding machines
- Dosing & mixing system
- Drilling Centers
- Drying and dehumidification system
- drying and dehumidifying equipment
- Drying and Dehumidifying System
- drying system
- effective and efficient. Cabinet dryers are also used in other industries where large quantities of material need to be dried
- efficient injection molding machine
- elbow hydraulic injection molding machines
- electric injection molding machine
- electric injection molding machines
- energy-efficient injection molding robot
- energy-saving injection molding machine
- etc. Among injection molding robots
- exhibition
- features of CNC machine
- Feeding And Conveying System
- Five Axis Machine Center
- Fully automatic injection molding machine
- Gathering Topstar
- giant injection molding machine
- GMU-600 5-Axis Machining Center
- Granulating & Recycling System
- Heavy duty injection molding machine
- High-precision electric molding machines
- high-precision plastic molding machines
- high-speed all electric injection molding machine
- Honeycomb rotor dehumidifier
- horizontal injection molding machine
- Horizontal Injection Molding Machines
- Horizontal Injection Moulding Machine
- Horizontal Mixer manufacturer
- How The CNC Machine Works
- hybrid injection molding machine
- hydraulic injection molding machine
- Hydraulic Injection Molding Machines
- in this article
- Industrial robot
- Industrial Robot Chinese brand
- industrial robot parts
- industrial robot supplier
- Industrial robots
- Industry Chain
- Injection Manipulator
- injection manipulator robot
- injection mold machines
- Injection molding
- Injection molding automation
- Injection Molding Automation Solution
- injection molding dryer
- Injection molding equipment
- injection molding hopper dryer
- Injection molding machine
- injection molding machine brand
- Injection Molding Machine Factory
- Injection Molding Machine Manufacture
- Injection molding machine manufacturer
- injection molding machine manufacturers
- Injection molding machine procurement
- injection molding machine robotic arm
- injection molding machine with a robot
- Injection molding machines
- injection molding material dehumidifying
- injection molding plant
- Injection Molding Robot
- injection molding robot arm
- Injection molding robot automation
- Injection molding robotic arm
- injection molding robots
- Injection moulding machine
- Injection Moulding Robots
- Injection Robot
- Injection robot arm
- Injection robot manufacturer
- Injection robot wholesale
- injection robots
- intelligent injection molding machines
- Introducing Injection Robot
- It is the best choice for drying large quantities of material at once. Cabinetmakers use these machines because they are fast
- large injection molding machine
- large injection molding machines
- Learn what industrial automation and robotics is
- linear robot
- linear robots
- low speed sound-proof granulator
- machine plastic molding
- make sure to add some! Improvements (2) Keyphrase in introduction: Your keyphrase or its synonyms appear in the first paragraph of the copy
- manipulator machine
- manufacturing
- medical grade injection molding machines
- medical injection molding machine
- medical injection molding machines
- micro injection molding machine
- middle speed granulator
- Mini CNC machine manufacturers.
- Mold Temperature Control System
- mold temperature controller
- mold temperature controllers
- molding material Dehumidifying System
- mould temperature control system
- mould temperature controller
- mould temperature controllers
- New electric injection molding machine
- nitrogen dryer manufacturer
- nitrogen dryer system manufacturer
- Oil type mold temperature controller
- Oil type mold temperature controllers
- open day
- Outbound links: No outbound links appear in this page. Add some! Images: No images appear on this page. Add some! Internal links: No internal links appear in this page
- PET Preform injection molding
- phone case maker machine
- phone case making machine
- plastic bottle making machine
- plastic bottle manufacturing
- plastic bucket making machine
- plastic bucket manufacturing
- Plastic chair making machine
- plastic forming equipment
- plastic hopper dryer
- plastic injection machine
- plastic injection machines
- plastic injection molding
- Plastic injection molding equipment
- Plastic injection molding machine
- Plastic Injection Molding Machines
- plastic injection moulding machine
- plastic injection robot
- Plastic Molding machine
- Plastic Molding Machines
- plastic molding press
- plastic moulding machine
- plastic phone case making machine
- plastic-molding machine
- powerful granulator
- Powerful Type Sound-Proof Granulator
- precision injection molding
- precision injection molding machines
- production of plastic seats
- pure water mould temperature controller
- Robot injection molding
- robot injection molding machine
- robot manufacturing companies
- Robotic arm for injection molding machine
- robotic injection molding machines
- robotics in injection molding
- SCARA robot
- SCARA robots
- Service-oriented manufacturing
- Servo Cylinder Robot
- servo driven robot
- Servo Driven Robots
- servo injection robots
- servo motor-driven linear robots
- servo-driven 3-axis robot
- Servo-Driven Robot
- Setup of injection machine
- Silicone Injection Molding Machine
- six-axis industrial robot
- Stainless Hopper Dryer
- Stainless Hopper Dryers
- star club
- swing arm robot
- take-out robots
- the choice between servo-driven robots and hydraulic robots will have a certain impact on efficiency
- the most popular injection molding machine
- the type of injection molding robot
- toggle clamp injection molding machine
- Toggle Hydraulic Injection Molding Machines
- toggle injection molding machine
- Top 10 brands of injection robots
- Topstar
- Topstar Engineering
- Topstar Industrial Robots
- Topstar injection molding intelligent
- Topstar Scara Robots
- Useful Injection molding machine
- Vertical machining centers
- volumetric type blender
- water chiller
- water chillers
- water distributor
- water type mold temperature controller
- Water Type MoldTemperature Controller
- Water-Type Mould Temperature Controllers
- We often face choices when performing injection molding. We will choose the type of injection molding machine
- wholesale of injection molding machines
- x carve CNC