What are the components and characteristics of a giant injection molding machine?
2024/01/17 By Topstar
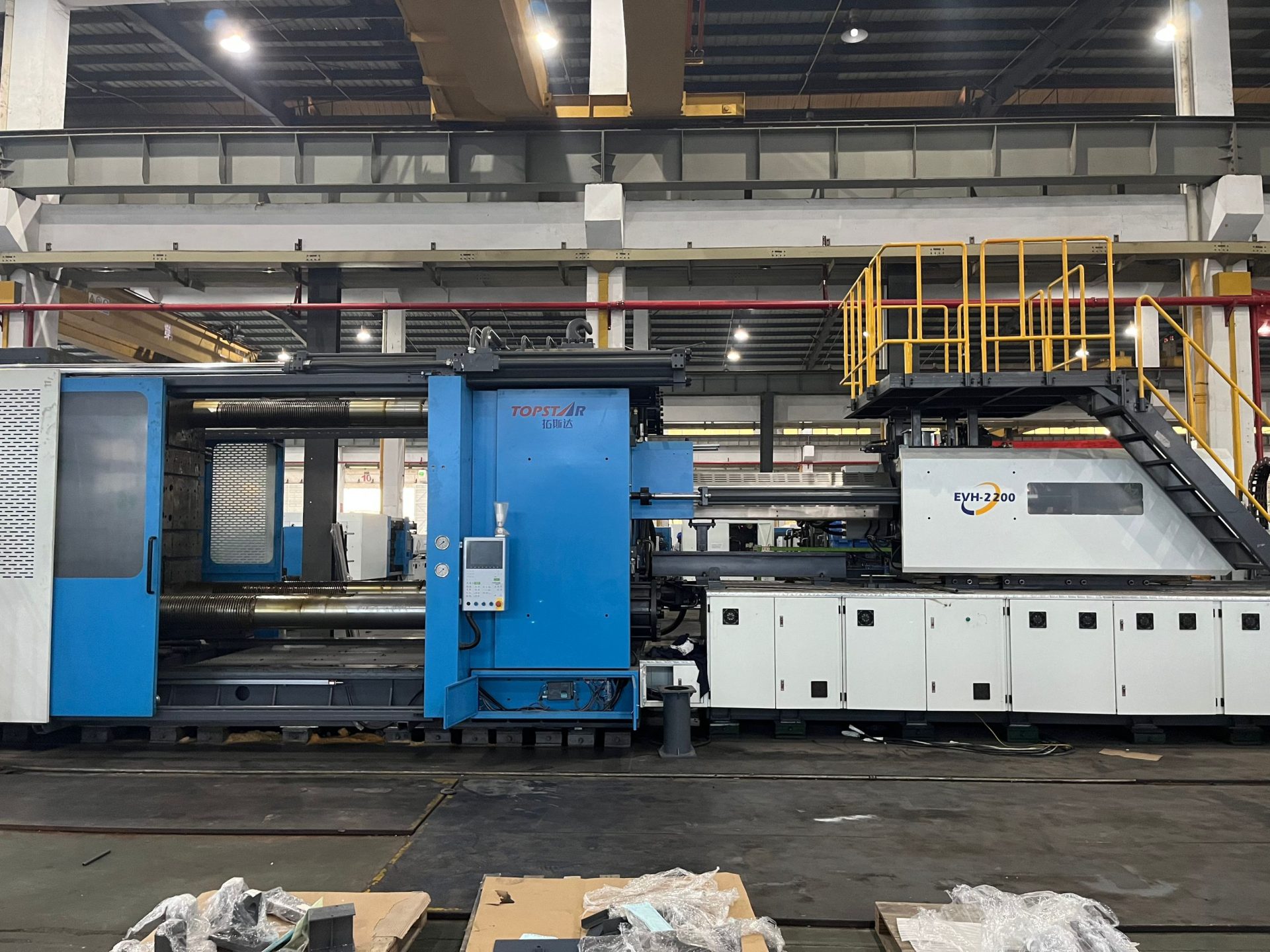
Among Topstar’s injection molding machine series, the giant injection molding machine is one of the leading injection molding equipment for mass production. Among them, the TH series injection molding machine is a giant injection molding machine. This guide will tell operators the differences between their components and their characteristics.
Giant injection molding machine clamping units
The core component of the giant injection molding machine is the mold clamping part, and the clamping force can reach 550T-2800T. It adopts a central four-cylinder mold clamping, and the clamping force is evenly distributed in the center of the template, resulting in high product molding accuracy and greatly extending the life of the machine and mold. In addition, we adopt a powerful hydraulic system that utilizes pistons and cylinders to exert great force to clamp and loosen the mold. This capability is critical to meeting the enormous pressure and temperature requirements of producing large, complex plastic parts. These parts are firmly connected by high-strength elements such as gears and guide pins, ensuring precise alignment and stability of the mold during the injection molding process.
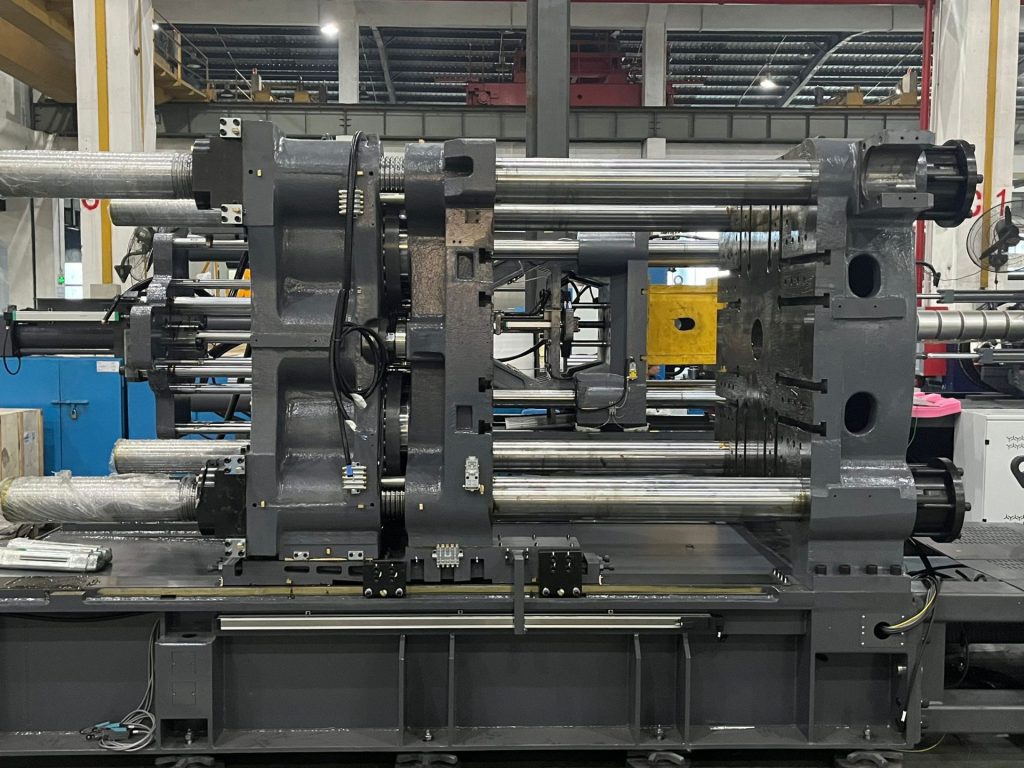
Giant injection molding machine injection units
The injection unit of the giant injection molding machine is different from other machines in that it uses high-performance chrome-plated screws to meet the needs of highly mixed-color products and specially customized plasticizing components for different product machines, such as PC, PA, etc. A durable and efficient screw plasticizes the molten material and injects it into the mold. Ensures a consistent and controlled flow of molten plastic, promoting uniformity in the final product. In addition, we use a two-way synchronous injection cylinder structure to prevent damage to the screw and linear rail due to unbalanced load. An advanced control system, which precisely adjusts injection speed, pressure, and temperature according to the specific requirements of each molding cycle, controls the process. This precision helps produce high-quality, defect-free plastic products.
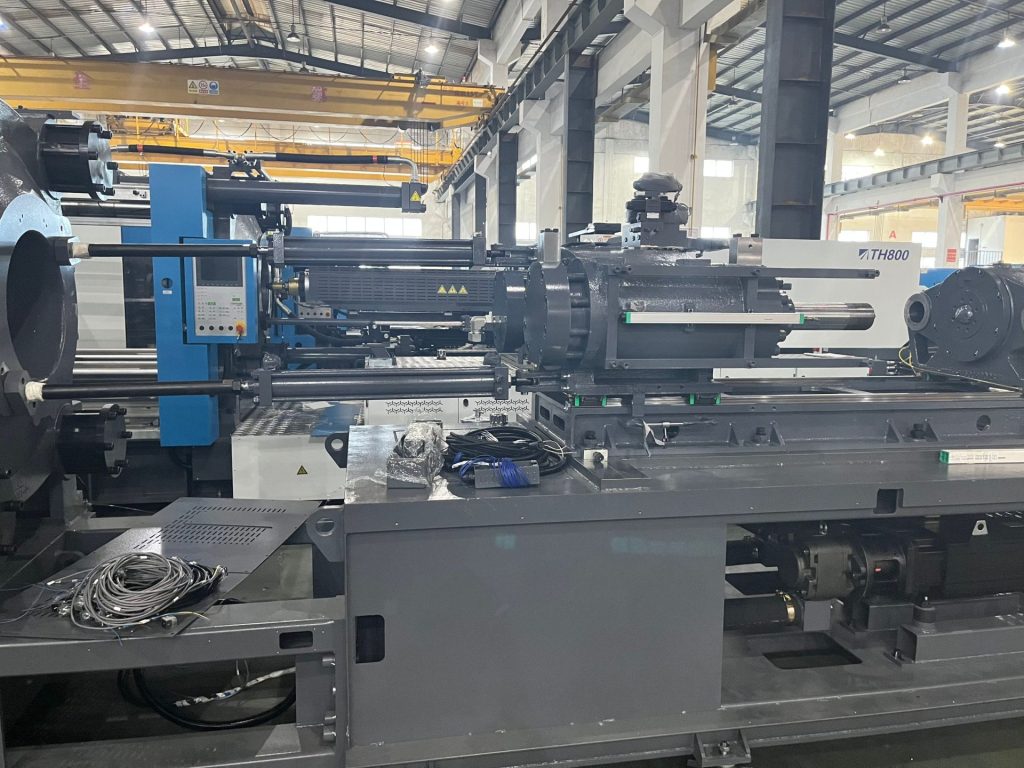
Advanced control system
The control system of the giant injection molding machine adopts an advanced oil circuit design. It is matched with European professional controllers, enhancing machine movement stability, increasing the yield rate, and accelerating the response speed. The control system is also one of our company’s three core technologies. Our independently developed programming language supports multiple industrial bus communication protocols such as EtherCAT, RTEX, MECHATROLINK, and CAN. The controller platform can realize integrated control with the Topstar injection molding machine controller, integrate a rich injection molding industry process package, and effectively improve the collaborative efficiency of giant injection molding machines and robots. In addition, many giant injection molding machines can achieve real-time monitoring, data collection, and analysis, meeting the conditions of Industry 4.0.
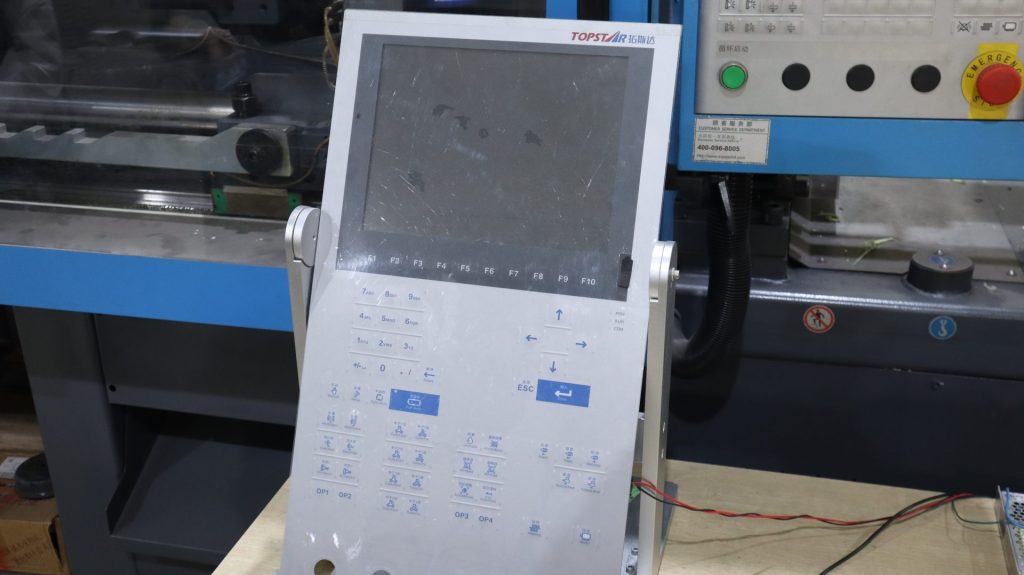
Hydraulic system of giant injection molding machine
The hydraulic system of giant injection molding machines uses an accumulator system to store hydraulic energy. This enables fast and powerful movements, such as rapid mold closing and high-speed injection, helping to shorten cycle times and increase production efficiency. Constructed with heavy-duty cylinders, reinforced hoses, and patented seals to ensure reliability and longevity even in high-pressure and high-temperature environments. Some giant injection molded bodies have regenerative hydraulic systems to improve energy efficiency. These systems recover and reuse energy during deceleration, reducing overall energy consumption.
Multi-component molding features
The advanced and precise control system for multi-component molding in the giant injection molding machine is in place. They facilitate precise synchronization of injection units, ensuring precise timing and dosing of each material. This level of control is critical to achieving the desired material distribution and avoiding issues such as color bleeding or material incompatibility. These machines often employ specialized mixing and blending technologies to meet the challenges of multi-material molding. These mechanisms ensure the homogeneity of the final product even when using materials with different properties or colors. Giant injection molding machines used for multi-part molding often incorporate robots to grab product parts, enhancing automation, improving production efficiency, and ensuring consistent product quality through precise placement and combination of different molded parts.
At last
Compared with other injection molding machines, the giant injection molding machine’s mold clamping, injection table, hydraulic pressure, etc., have been fully optimized, and the comprehensive capabilities have been greatly improved. They have unique advantages for producing products with complex shapes and high dimensional accuracy, especially those with thin walls, deep cavities, and multi-cavity requirements.
TRENDING POSTS
- What factors can cause delays in the injection molding process of plastic molding machine? 2024/01/17
- Exhibition Review| Topstar participates in InterPlas Thailand 2024 2024/01/17
- Star Case | Topstar helps Santong upgrade its intelligent plant 2024/01/17
- Topstar Special | National Science and Technology Workers Day 2024/01/17
HOT TOPIC
- .ervo motor-driven linear robots
- 3 axis robot
- 3 axis robots
- 3 in 1 Compact Dehumidifying Dryer
- 3-axis robot
- 3-axis robots
- 5-axis CNC machine
- accuracy
- Air Chillers
- all electric injection molding machine
- all electric injection molding machines
- All-electric injection molding machines
- and overall production quality. Therefore
- AP-RubberPlas
- automated injection molding machine
- Automation changed engineering
- automation of injection molding robots
- auxiliary machine
- Bench Injection Molding Machine
- Cabinet dryer manufacturers
- Cabinet dryers
- chiller
- CNC Drilling Machine
- CNC Drilling Machines
- cnc engraving machine manufacturer
- cnc laser cutting machine manufacturer
- CNC machine
- CNC Machine Center
- CNC Machine for Sale
- CNC Machine Manufacturing
- CNC Machine Tool
- CNC machine tool product
- CNC Machining Center
- CNC wood carving machine
- Cooling system
- Cross-Walking Single Axis Servo Cylinder Robot
- Cross-Walking Single-Axis Servo Cylinder Robot
- Cross-Walking Three-Axis/Five-Axis Servo Driven Robot
- cross-walking three-axis/five-axis servo-driven robot
- Dehumidifier Dryer
- Dehumidifying Dryer
- delta parallel robot
- Desktop Injection Molding Machine
- Desktop injection molding machines
- Desktop Molding Machine
- desktop plastic injection machine
- Desktop Plastic Injection Molding Machine
- direct clamp injection molding machine
- Direct clamp injection molding machines
- Dosing & mixing system
- Drilling Centers
- Drying and dehumidification system
- drying and dehumidifying equipment
- Drying and Dehumidifying System
- drying system
- effective and efficient. Cabinet dryers are also used in other industries where large quantities of material need to be dried
- efficient injection molding machine
- elbow hydraulic injection molding machines
- electric injection molding machine
- electric injection molding machines
- energy-efficient injection molding robot
- energy-saving injection molding machine
- etc. Among injection molding robots
- exhibition
- features of CNC machine
- Feeding And Conveying System
- Five Axis Machine Center
- Fully automatic injection molding machine
- Gathering Topstar
- giant injection molding machine
- GMU-600 5-Axis Machining Center
- Granulating & Recycling System
- Heavy duty injection molding machine
- High-precision electric molding machines
- high-precision plastic molding machines
- high-speed all electric injection molding machine
- Honeycomb rotor dehumidifier
- horizontal injection molding machine
- Horizontal Injection Molding Machines
- Horizontal Injection Moulding Machine
- Horizontal Mixer manufacturer
- How The CNC Machine Works
- hybrid injection molding machine
- hydraulic injection molding machine
- Hydraulic Injection Molding Machines
- in this article
- Industrial robot
- Industrial Robot Chinese brand
- industrial robot parts
- industrial robot supplier
- Industrial robots
- Industry Chain
- Injection Manipulator
- injection manipulator robot
- injection mold machines
- Injection molding
- Injection molding automation
- Injection Molding Automation Solution
- injection molding dryer
- Injection molding equipment
- injection molding hopper dryer
- Injection molding machine
- injection molding machine brand
- Injection Molding Machine Factory
- Injection Molding Machine Manufacture
- Injection molding machine manufacturer
- injection molding machine manufacturers
- Injection molding machine procurement
- injection molding machine robotic arm
- injection molding machine with a robot
- Injection molding machines
- injection molding material dehumidifying
- injection molding plant
- Injection Molding Robot
- injection molding robot arm
- Injection molding robot automation
- Injection molding robotic arm
- injection molding robots
- Injection moulding machine
- Injection Moulding Robots
- Injection Robot
- Injection robot arm
- Injection robot manufacturer
- Injection robot wholesale
- injection robots
- intelligent injection molding machines
- Introducing Injection Robot
- It is the best choice for drying large quantities of material at once. Cabinetmakers use these machines because they are fast
- large injection molding machine
- Learn what industrial automation and robotics is
- linear robot
- linear robots
- low speed sound-proof granulator
- machine plastic molding
- make sure to add some! Improvements (2) Keyphrase in introduction: Your keyphrase or its synonyms appear in the first paragraph of the copy
- manipulator machine
- manufacturing
- medical grade injection molding machines
- medical injection molding machine
- medical injection molding machines
- micro injection molding machine
- middle speed granulator
- Mini CNC machine manufacturers.
- Mold Temperature Control System
- mold temperature controller
- mold temperature controllers
- molding material Dehumidifying System
- mould temperature control system
- mould temperature controller
- mould temperature controllers
- New electric injection molding machine
- nitrogen dryer manufacturer
- nitrogen dryer system manufacturer
- Oil type mold temperature controller
- Oil type mold temperature controllers
- open day
- Outbound links: No outbound links appear in this page. Add some! Images: No images appear on this page. Add some! Internal links: No internal links appear in this page
- PET Preform injection molding
- phone case maker machine
- phone case making machine
- plastic bottle making machine
- plastic bottle manufacturing
- plastic bucket making machine
- plastic bucket manufacturing
- Plastic chair making machine
- plastic forming equipment
- plastic hopper dryer
- plastic injection machine
- plastic injection machines
- plastic injection molding
- Plastic injection molding equipment
- Plastic injection molding machine
- Plastic Injection Molding Machines
- plastic injection moulding machine
- plastic injection robot
- Plastic Molding machine
- Plastic Molding Machines
- plastic molding press
- plastic moulding machine
- plastic phone case making machine
- plastic-molding machine
- powerful granulator
- Powerful Type Sound-Proof Granulator
- precision injection molding
- production of plastic seats
- pure water mould temperature controller
- Robot injection molding
- robot injection molding machine
- robot manufacturing companies
- Robotic arm for injection molding machine
- robotic injection molding machines
- robotics in injection molding
- SCARA robot
- SCARA robots
- Service-oriented manufacturing
- Servo Cylinder Robot
- servo driven robot
- Servo Driven Robots
- servo injection robots
- servo motor-driven linear robots
- servo-driven 3-axis robot
- Servo-Driven Robot
- Setup of injection machine
- Silicone Injection Molding Machine
- six-axis industrial robot
- Stainless Hopper Dryer
- Stainless Hopper Dryers
- star club
- swing arm robot
- take-out robots
- the choice between servo-driven robots and hydraulic robots will have a certain impact on efficiency
- the most popular injection molding machine
- the type of injection molding robot
- toggle clamp injection molding machine
- Toggle Hydraulic Injection Molding Machines
- toggle injection molding machine
- Top 10 brands of injection robots
- Topstar
- Topstar Engineering
- Topstar Industrial Robots
- Topstar injection molding intelligent
- Topstar Scara Robots
- Useful Injection molding machine
- Vertical machining centers
- volumetric type blender
- water chiller
- water chillers
- water distributor
- water type mold temperature controller
- Water Type MoldTemperature Controller
- Water-Type Mould Temperature Controllers
- We often face choices when performing injection molding. We will choose the type of injection molding machine
- wholesale of injection molding machines
- x carve CNC