Transforming manufacturing with injection molding automation solutions
2024/01/15 By Topstar
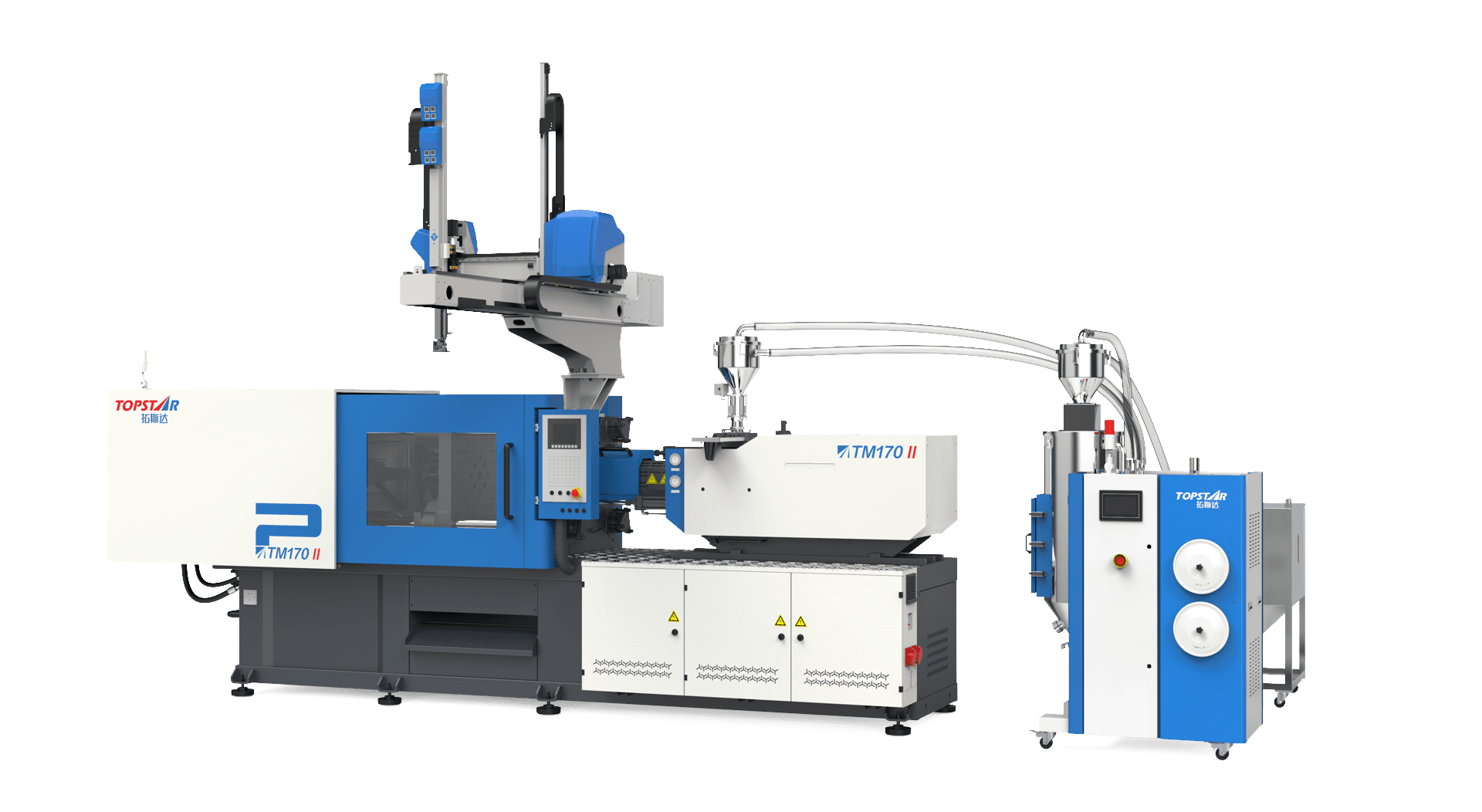
In the past, the traditional injection molding manufacturing industry relied on manual labor and injection molding machines to perform injection molding work, which was unreliable for the entire injection molding cycle time and personnel safety. In today’s manufacturing industry, with the advent of Industry 4.0, traditional injection molding methods are gradually being eliminated, and their replacement is injection molding automation. The following will introduce you to Topstar’s injection molding automation solution, which allows traditional injection molding manufacturing to operate.
Understand the essence of injection molding automation
Injection molding automation is an automated workflow that combines injection molding machines, robots, and auxiliary equipment. In the past, we used manual labor to grab and transport materials. This method is not only time-consuming but also inefficient. Injection molding automation is adding a manipulator above the injection molding machine to automatically grab materials and add auxiliary equipment at the rear for material transportation and drying. Through our standard KEBA computer and our self-developed control program, we can control the parameter setting of the entire machine on an interface to achieve flexible human-computer interaction.
Injection molding machines in injection molding automation
Topstar’s injection molding machines are divided into TM ll series hinged injection molding machines, TE ll series electric injection molding machines, TH series direct pressure injection molding machines, and TS series injection molding machines. They are suitable for different application scenarios according to their advantages. They are all equipped with KEBA computers and use our independently developed control program to make production control more precise. The entire series of injection molding machines can integrated with auxiliary systems highly, making operation more convenient and efficient.
The TM II series can accurately grasp the mold opening position with the robot, having an automatic compensation function. TS series uses advanced oil circuit design and control for stable machine action, higher yield, and faster response. The TE ll series has all-electric and hybrid models on the same platform. High-stability template in the clamping unit, high-rigidity structure in the injection unit, and user-friendly TUI interactive page.
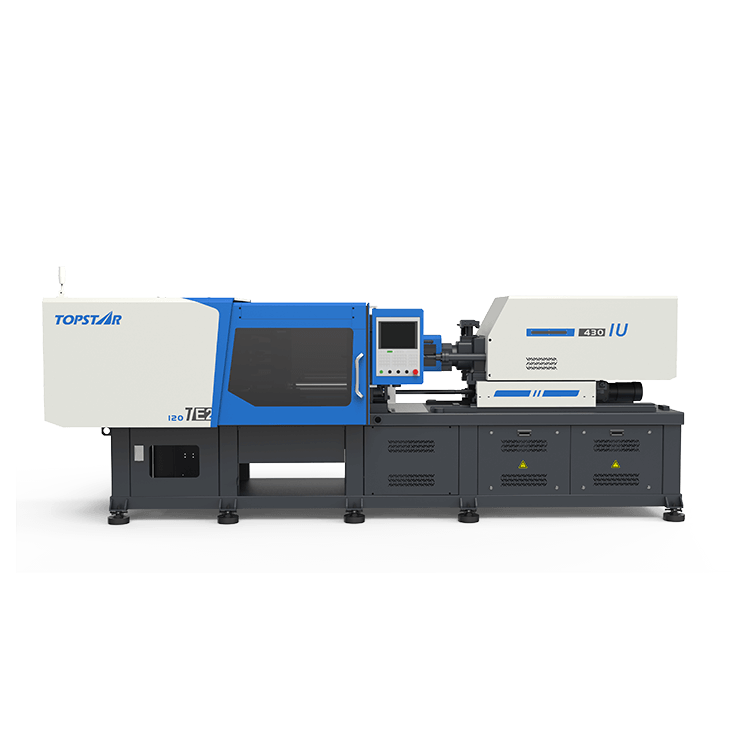
Injection robots in injection molding automation
Topstar’s manipulators include the AD-80s, MD-120s series, EUW-80, and others. The MD series manipulator suits various horizontal injection molding machines ranging from 75 to 1,300 tons, extracting finished products and nozzles that demand high appearance and precision. The EUW-80 series is the company’s newly developed linear manipulator for complete servo injection molding. It can perform remote monitoring, equipment operation, data statistics, analysis, and life management. A cylinder drives the AD series, enabling it to meet various simple embedding actions, reduce the cost of servo motors, and remain affordable. Through the robot’s high precision, high speed, and high performance, we can replace manual work, making our production more efficient and personnel safer.
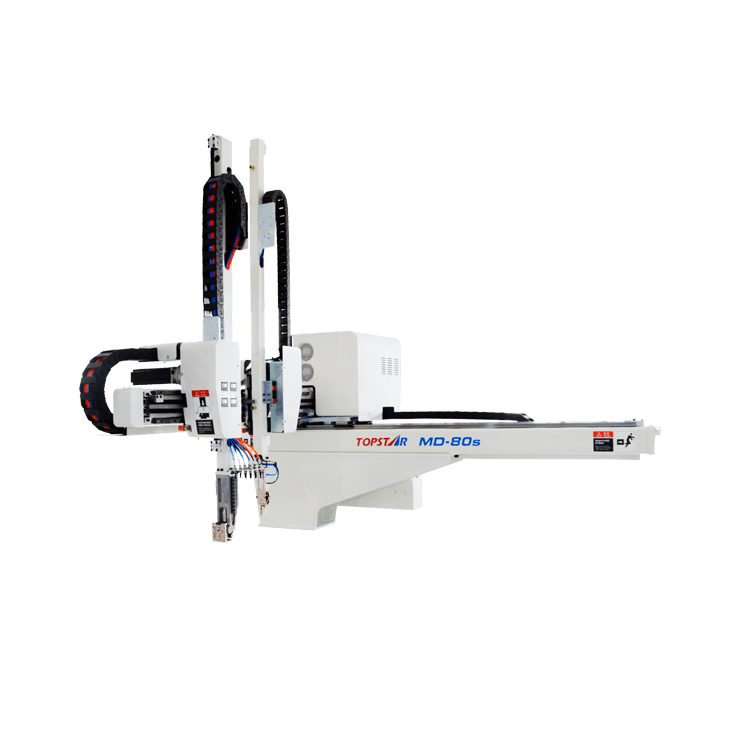
Auxiliary equipment
Auxiliary products can support all aspects of the production of injection molding machines. The TDB series (3 in 1 Compact) dehumidifying dryer is the most common. It integrates three dehumidification functions, drying and feeding into one machine, with an optional three-stage feeding function. The 3-in-1 design is space-efficient and ideal for automated and compact spaces. At the same time, they have a honeycomb runner, which ensures good stability while obtaining low dew point dry air. The machine adopts microcomputer control, which has lower energy consumption and a drying air volume of 50-300m³/hr. We have also designed optical-grade three-in-one dehumidifiers for optical-grade products to meet the needs of different customers.
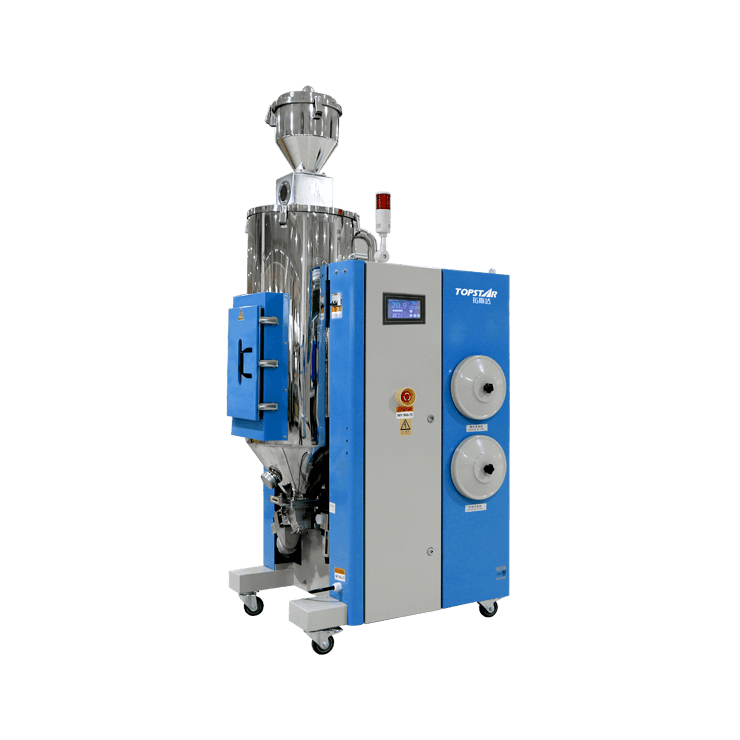
What can automation bring?
The injection molding automated production method combines Topstar’s latest technology to simplify our work and production processes and reshape how we manufacture plastic parts. Automation minimizes manual intervention, resulting in increased revenue from shorter cycle times. Ensure accuracy and repeatability throughout the entire injection molding automation process. We can carefully manage variables such as temperature, pressure, and cycle time with our in-house developed control system to produce consistently high-quality parts. Injection molding automation is also a representative of Industry 4.0. Intelligent sensors, connectivity, and data analytics enable real-time monitoring and data-driven decision-making, enabling a more agile and responsive manufacturing ecosystem. Many regions have implemented fully automated, unmanned production.
Automate your workshop
We have always been committed to enabling the global manufacturing industry to realize automated and intelligent manufacturing. Through our injection molding automation, your production workshop can reduce cycle time, gain more profits, and produce products with consistent quality, higher precision, and more stability.
TRENDING POSTS
- What factors can cause delays in the injection molding process of plastic molding machine? 2024/01/15
- Exhibition Review| Topstar participates in InterPlas Thailand 2024 2024/01/15
- Star Case | Topstar helps Santong upgrade its intelligent plant 2024/01/15
- Topstar Special | National Science and Technology Workers Day 2024/01/15
HOT TOPIC
- .ervo motor-driven linear robots
- 1.0 guangdong topstar technology co. ltd
- 1.0 topstar china
- 1.0 topstar robot
- 11
- 2
- 21
- 23
- 3 axis robot
- 3 axis robots
- 3 in 1 Compact Dehumidifying Dryer
- 3-axis robot
- 3-axis robots
- 39
- 41
- 5-axis CNC machine
- 62
- accuracy
- Air Chillers
- all electric injection molding machine
- all electric injection molding machines
- All-electric injection molding machines
- and overall production quality. Therefore
- AP-RubberPlas
- automated injection molding machine
- Automation changed engineering
- automation of injection molding robots
- auxiliary machine
- Bench Injection Molding Machine
- Cabinet dryer manufacturers
- Cabinet dryers
- chiller
- CNC Drilling Machine
- CNC Drilling Machines
- cnc engraving machine manufacturer
- cnc laser cutting machine manufacturer
- CNC machine
- CNC Machine Center
- CNC Machine for Sale
- CNC Machine Manufacturing
- CNC Machine Tool
- CNC machine tool product
- CNC Machining Center
- CNC wood carving machine
- Cooling system
- Cross-Walking Single Axis Servo Cylinder Robot
- Cross-Walking Single-Axis Servo Cylinder Robot
- Cross-Walking Three-Axis/Five-Axis Servo Driven Robot
- cross-walking three-axis/five-axis servo-driven robot
- Dehumidifier Dryer
- Dehumidifying Dryer
- delta parallel robot
- Desktop Injection Molding Machine
- Desktop injection molding machines
- Desktop Molding Machine
- desktop plastic injection machine
- Desktop Plastic Injection Molding Machine
- direct clamp injection molding machine
- Direct clamp injection molding machines
- Dosing & mixing system
- Drilling Centers
- Drying and dehumidification system
- drying and dehumidifying equipment
- Drying and Dehumidifying System
- drying system
- effective and efficient. Cabinet dryers are also used in other industries where large quantities of material need to be dried
- efficient injection molding machine
- elbow hydraulic injection molding machines
- electric injection molding machine
- electric injection molding machines
- energy-efficient injection molding robot
- energy-saving injection molding machine
- etc. Among injection molding robots
- exhibition
- features of CNC machine
- Feeding And Conveying System
- Five Axis Machine Center
- Fully automatic injection molding machine
- Gathering Topstar
- giant injection molding machine
- GMU-600 5-Axis Machining Center
- Granulating & Recycling System
- Heavy duty injection molding machine
- High-precision electric molding machines
- high-precision plastic molding machines
- high-speed all electric injection molding machine
- Honeycomb rotor dehumidifier
- horizontal injection molding machine
- Horizontal Injection Molding Machines
- Horizontal Injection Moulding Machine
- Horizontal Mixer manufacturer
- How The CNC Machine Works
- hybrid injection molding machine
- hydraulic injection molding machine
- Hydraulic Injection Molding Machines
- in this article
- Industrial robot
- Industrial Robot Chinese brand
- industrial robot parts
- industrial robot supplier
- Industrial robots
- Industry Chain
- Injection Manipulator
- injection manipulator robot
- injection mold machines
- Injection molding
- Injection molding automation
- Injection Molding Automation Solution
- injection molding dryer
- Injection molding equipment
- injection molding hopper dryer
- Injection molding machine
- injection molding machine brand
- Injection Molding Machine Factory
- Injection Molding Machine Manufacture
- Injection molding machine manufacturer
- injection molding machine manufacturers
- Injection molding machine procurement
- injection molding machine robotic arm
- injection molding machine with a robot
- Injection molding machines
- injection molding material dehumidifying
- injection molding plant
- Injection Molding Robot
- injection molding robot arm
- Injection molding robot automation
- Injection molding robotic arm
- injection molding robots
- Injection moulding machine
- Injection Moulding Robots
- Injection Robot
- Injection robot arm
- Injection robot manufacturer
- Injection robot wholesale
- injection robots
- intelligent injection molding machines
- Introducing Injection Robot
- It is the best choice for drying large quantities of material at once. Cabinetmakers use these machines because they are fast
- large injection molding machine
- large injection molding machines
- Learn what industrial automation and robotics is
- linear robot
- linear robots
- low speed sound-proof granulator
- machine plastic molding
- make sure to add some! Improvements (2) Keyphrase in introduction: Your keyphrase or its synonyms appear in the first paragraph of the copy
- manipulator machine
- manufacturing
- medical grade injection molding machines
- medical injection molding machine
- medical injection molding machines
- micro injection molding machine
- middle speed granulator
- Mini CNC machine manufacturers.
- Mold Temperature Control System
- mold temperature controller
- mold temperature controllers
- molding material Dehumidifying System
- mould temperature control system
- mould temperature controller
- mould temperature controllers
- New electric injection molding machine
- nitrogen dryer manufacturer
- nitrogen dryer system manufacturer
- Oil type mold temperature controller
- Oil type mold temperature controllers
- open day
- Outbound links: No outbound links appear in this page. Add some! Images: No images appear on this page. Add some! Internal links: No internal links appear in this page
- PET Preform injection molding
- phone case maker machine
- phone case making machine
- plastic bottle making machine
- plastic bottle manufacturing
- plastic bucket making machine
- plastic bucket manufacturing
- Plastic chair making machine
- plastic forming equipment
- plastic hopper dryer
- plastic injection machine
- plastic injection machines
- plastic injection molding
- Plastic injection molding equipment
- Plastic injection molding machine
- Plastic Injection Molding Machines
- plastic injection moulding machine
- plastic injection robot
- Plastic Molding machine
- Plastic Molding Machines
- plastic molding press
- plastic moulding machine
- plastic phone case making machine
- plastic-molding machine
- powerful granulator
- Powerful Type Sound-Proof Granulator
- precision injection molding
- precision injection molding machines
- production of plastic seats
- pure water mould temperature controller
- Robot injection molding
- robot injection molding machine
- robot manufacturing companies
- Robotic arm for injection molding machine
- robotic injection molding machines
- robotics in injection molding
- SCARA robot
- SCARA robots
- Service-oriented manufacturing
- Servo Cylinder Robot
- servo driven robot
- Servo Driven Robots
- servo injection robots
- servo motor-driven linear robots
- servo-driven 3-axis robot
- Servo-Driven Robot
- Setup of injection machine
- Silicone Injection Molding Machine
- six-axis industrial robot
- Stainless Hopper Dryer
- Stainless Hopper Dryers
- star club
- swing arm robot
- take-out robots
- the choice between servo-driven robots and hydraulic robots will have a certain impact on efficiency
- the most popular injection molding machine
- the type of injection molding robot
- toggle clamp injection molding machine
- Toggle Hydraulic Injection Molding Machines
- toggle injection molding machine
- Top 10 brands of injection robots
- Topstar
- Topstar Engineering
- Topstar Industrial Robots
- Topstar injection molding intelligent
- Topstar Scara Robots
- Useful Injection molding machine
- Vertical machining centers
- volumetric type blender
- water chiller
- water chillers
- water distributor
- water type mold temperature controller
- Water Type MoldTemperature Controller
- Water-Type Mould Temperature Controllers
- We often face choices when performing injection molding. We will choose the type of injection molding machine
- wholesale of injection molding machines
- x carve CNC
- 热门查询 点击次数 展示 排名 topstar