What auxiliary equipment does a large injection molding machine need?
2025/07/07 By Topstar
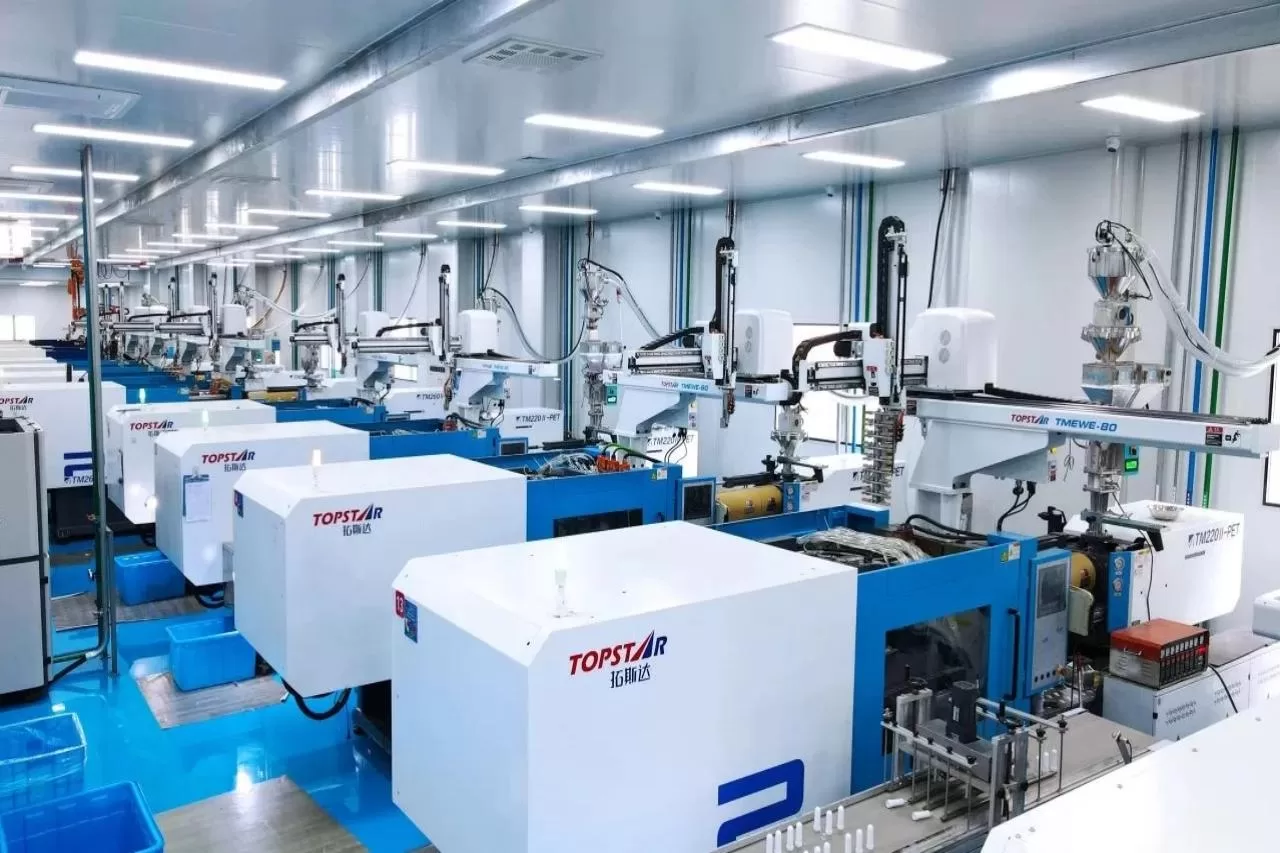
A standalone injection molding machine cannot operate optimally without a complete set of auxiliary equipment to handle material conditioning, temperature control, and waste management, which are critical to a stable and productive molding cycle. Generally speaking, seven key auxiliary equipment are required for each large injection molding machine installation, including mold temperature controllers, chillers, material dryers, feed conveying and metering systems, and pelletizers. These auxiliary equipment pieces each manage precise thermal management, using efficient material handling to prevent contamination and downtime, etc., to build a complete injection molding production line.
Mold temperature controllers enable precise thermal management of a large injection molding machine
Large injection molding machines require precise mold temperature control to achieve consistent part dimensions, prevent warping, and ensure the best surface finish. High-precision mold temperature controllers (typically water or oil-based) regulate temperatures with PID adjustment, maintaining ±0.1°C stability during extended operation. These units heat molds to exact set points during injection, preventing inconsistent polymer cooling. In addition, fast dynamic heating through servo-driven pumps can reduce preheating time by 25%. When the mold contains core and cavity circuits with different thermal requirements, I integrate a dual-zone controller and fine-tune each circuit separately. Real-time temperature logging enables predictive maintenance and alerts me before channel blockage or pump wear affects the molding cycle. This auxiliary function ensures that the injection molding machine provides uniform molding in each cycle.
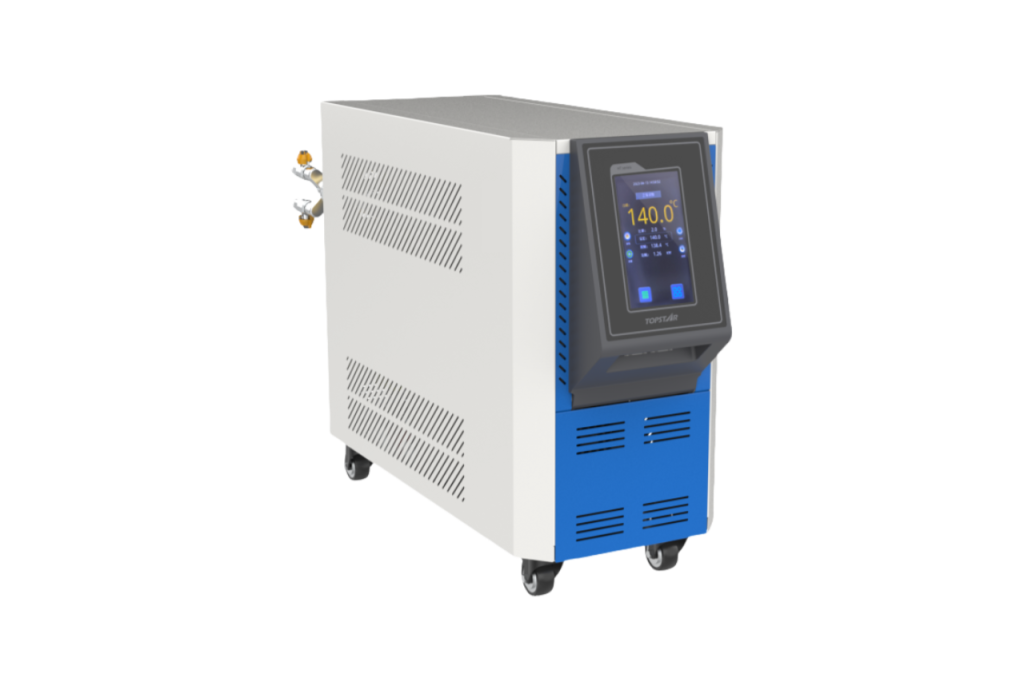
Basic efficient cooling water chiller
For large injection molding machines, effective cooling of molds and hydraulic systems is also required, so we need to integrate a water chiller. 7-12°C chilled water circulates in the mold cooling line to achieve rapid solidification, thereby reducing the cooling stage by up to 20%. In addition, a separate hydraulic oil circuit prevents thermal degradation of seals and valves and extends the service life of the machine. The water chiller series also includes air-cooled chillers, water-cooled chillers, and models with variable-speed compressors and coil evaporators.
The size and design of these water chillers can meet high flow requirements to handle large cavity molds. In environments with higher ambient temperatures, you can also add glycol-based antifreeze to prevent ice formation and incorporate redundant pumps for fail-safe operation. A properly integrated chiller not only optimizes cycle efficiency but also protects hydraulic components and ensures consistent molding conditions throughout production.
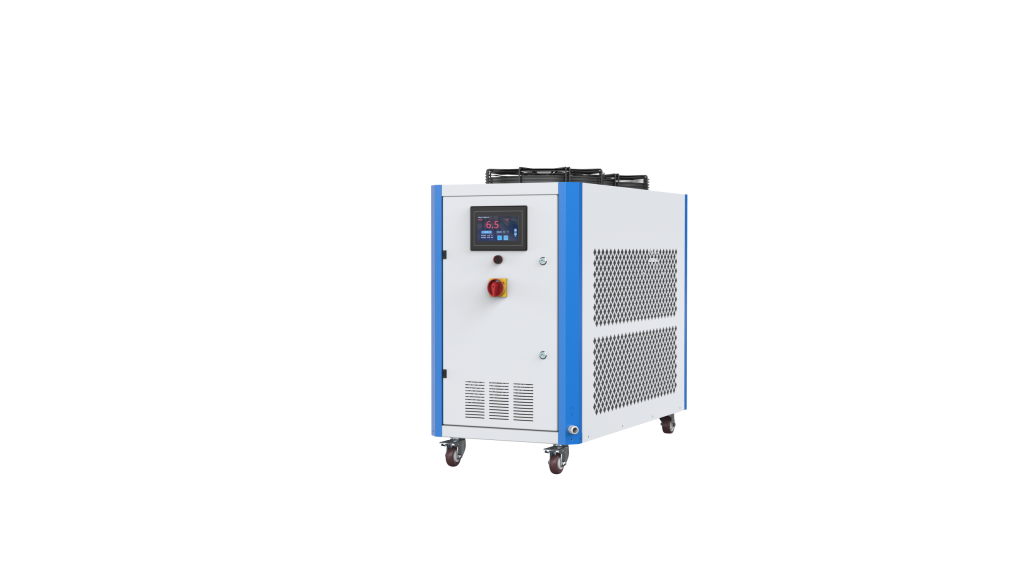
Material hopper dryers for moisture-free resin feed
Before using any injection molding machines for production, operators must dry the feed material, especially hygroscopic resins like nylon, PET, or ABS. Therefore, they install dehumidifying dryers that maintain a -40°C dew point. For example, these dehumidifying dryers can dry PET at 80°C for four hours to eliminate residual moisture, which would otherwise cause speckle defects. In addition, dryers prevent brittle or weak spots in the final product. We integrate dryers directly into the injection molding machine hopper using insulated, heated hoses and automatic level sensors to provide continuous material supply during material changes. Topstar machines feature touchscreen controllers that allow operators to set multiple drying zones and monitor humidity levels remotely. This ensures that each machine processes optimally dried resin, resulting in lower scrap rates and faster start-up cycles.
Feed conveying and metering systems for precise material handling of large injection molding machine
Powerful feed conveying systems and gravimetric metering mixers achieve precise resin and additive measurements on large injection molding machines. Vacuum conveyors convey particles from ground silos to multiple machine hoppers, eliminating manual handling and contamination, and then gravimetric metering mixers are able to maintain the precise ratio of virgin resin, recycled materials and colorants, which is essential for maintaining consistent mechanical and appearance properties. Topstar’s metering and mixing system can automatically calculate the required speed through the conditions set by the microcomputer control system, with accurate metering and an error value of ±1%. It also has a conveying circuit with a differential pressure sensor to detect blockages early and calibrate the mixer scale to an accuracy of ±0.5% to ensure uniform mixing. By integrating these systems, each injection molding machine can obtain dust-free, perfectly mixed feed, reducing cycle-to-cycle differences.
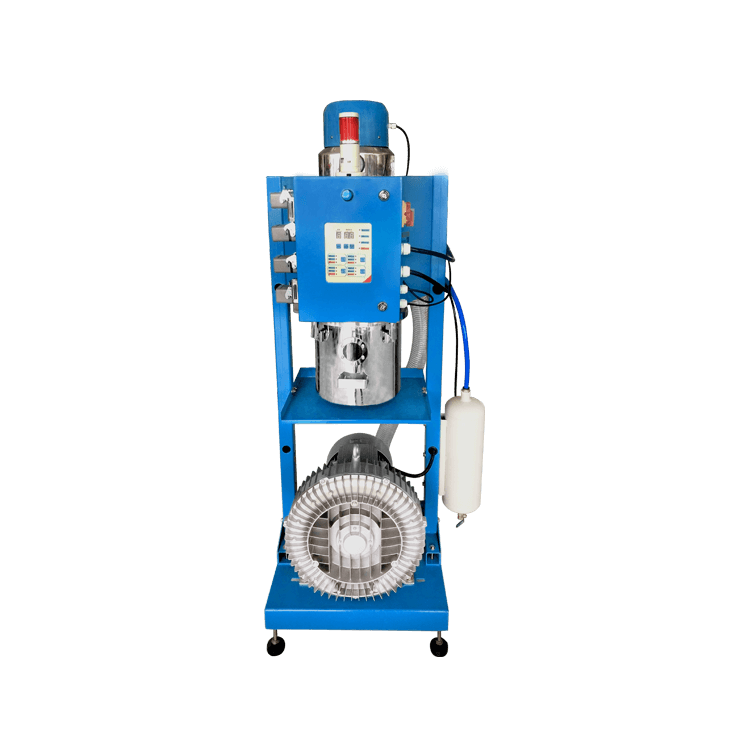
Integrated granulator for waste reduction
To minimize waste and maintain sustainability, we equip each large injection molding machine with an online granulator. This system primarily crushes nozzle materials at the machine side, efficiently recycling hard and brittle plastics like PC, nylon, and ABS. The granulator then dries the recovered particles and feeds them back into the system in precise proportions. At the same time, you can also choose a pulverizer with different speeds and silence, through the high-torque granulator shaft and variable speed motor, to handle brittle and ductile waste without producing too much fine powder. The design eliminates screens, produces uniformly crushed particles, and minimizes dust content.
The double-layer soundproof design is adopted in the feed hopper; the inner layer is made of stainless steel, and there is a visual material window. This on-site recycling cycle can reduce raw material costs by up to 10% and reduce landfill, which helps achieve environmentally friendly production, improve your corporate sustainability indicators, and ensure a continuous supply of raw materials.
Achieve complete injection molding
Large injection molding machines can only perform molding work completely if they are equipped with a complete set of auxiliary equipment, which requires mold temperature controllers, high-efficiency ice water machines, humidity control dryers, precise feed conveying and metering systems, and on-site granulators integrated around them. We integrate and fine-tune each auxiliary equipment to ensure regular operation to meet production needs, seamless material flow, stable processing temperature, and continuous waste recovery.
TRENDING POSTS
- What factors can cause delays in the injection molding process of plastic molding machine? 2025/07/07
- Exhibition Review| Topstar participates in InterPlas Thailand 2024 2025/07/07
- Star Case | Topstar helps Santong upgrade its intelligent plant 2025/07/07
- Topstar Special | National Science and Technology Workers Day 2025/07/07
HOT TOPIC
- .ervo motor-driven linear robots
- 1.0 guangdong topstar technology co. ltd
- 1.0 topstar china
- 1.0 topstar robot
- 11
- 2
- 21
- 23
- 3 axis robot
- 3 axis robots
- 3 in 1 Compact Dehumidifying Dryer
- 3-axis robot
- 3-axis robots
- 39
- 41
- 5-axis CNC machine
- 62
- accuracy
- Air Chillers
- all electric injection molding machine
- all electric injection molding machines
- All-electric injection molding machines
- and overall production quality. Therefore
- AP-RubberPlas
- automated injection molding machine
- Automation changed engineering
- automation of injection molding robots
- auxiliary machine
- Bench Injection Molding Machine
- Cabinet dryer manufacturers
- Cabinet dryers
- chiller
- CNC Drilling Machine
- CNC Drilling Machines
- cnc engraving machine manufacturer
- cnc laser cutting machine manufacturer
- CNC machine
- CNC Machine Center
- CNC Machine for Sale
- CNC Machine Manufacturing
- CNC Machine Tool
- CNC machine tool product
- CNC Machining Center
- CNC wood carving machine
- Cooling system
- Cross-Walking Single Axis Servo Cylinder Robot
- Cross-Walking Single-Axis Servo Cylinder Robot
- Cross-Walking Three-Axis/Five-Axis Servo Driven Robot
- cross-walking three-axis/five-axis servo-driven robot
- Dehumidifier Dryer
- Dehumidifying Dryer
- delta parallel robot
- Desktop Injection Molding Machine
- Desktop injection molding machines
- Desktop Molding Machine
- desktop plastic injection machine
- Desktop Plastic Injection Molding Machine
- direct clamp injection molding machine
- Direct clamp injection molding machines
- Dosing & mixing system
- Drilling Centers
- Drying and dehumidification system
- drying and dehumidifying equipment
- Drying and Dehumidifying System
- drying system
- effective and efficient. Cabinet dryers are also used in other industries where large quantities of material need to be dried
- efficient injection molding machine
- elbow hydraulic injection molding machines
- electric injection molding machine
- electric injection molding machines
- energy-efficient injection molding robot
- energy-efficient water chiller
- energy-efficient water chillers
- energy-saving injection molding machine
- etc. Among injection molding robots
- exhibition
- features of CNC machine
- Feeding And Conveying System
- Five Axis Machine Center
- Fully automatic injection molding machine
- Gathering Topstar
- giant injection molding machine
- GMU-600 5-Axis Machining Center
- Granulating & Recycling System
- Heavy duty injection molding machine
- High-precision electric molding machines
- high-precision plastic molding machines
- high-speed all electric injection molding machine
- high-speed electric injection molding machine
- High-Speed Packaging Injection Molding
- Honeycomb rotor dehumidifier
- horizontal injection molding machine
- Horizontal Injection Molding Machines
- Horizontal Injection Moulding Machine
- Horizontal Mixer manufacturer
- How The CNC Machine Works
- hybrid injection molding machine
- hydraulic injection molding machine
- Hydraulic Injection Molding Machines
- in this article
- Industrial robot
- Industrial Robot Chinese brand
- industrial robot parts
- industrial robot supplier
- Industrial robots
- Industry Chain
- Injection Manipulator
- injection manipulator robot
- injection mold machines
- Injection molding
- Injection molding automation
- Injection Molding Automation Solution
- injection molding dryer
- Injection molding equipment
- injection molding hopper dryer
- Injection molding machine
- injection molding machine brand
- Injection Molding Machine Factory
- Injection Molding Machine Manufacture
- Injection molding machine manufacturer
- injection molding machine manufacturers
- Injection molding machine procurement
- injection molding machine robotic arm
- injection molding machine with a robot
- Injection molding machines
- injection molding material dehumidifying
- injection molding plant
- injection molding process
- Injection Molding Robot
- injection molding robot arm
- Injection molding robot automation
- Injection molding robotic arm
- injection molding robots
- Injection moulding machine
- injection moulding machines
- Injection Moulding Robots
- Injection Robot
- Injection robot arm
- Injection robot manufacturer
- Injection robot wholesale
- injection robots
- intelligent injection molding machines
- intelligent mold temperature
- intelligent mold temperature controller
- Intelligent mould temperature controller
- Introducing Injection Robot
- It is the best choice for drying large quantities of material at once. Cabinetmakers use these machines because they are fast
- Large flow water type mold temperature controller
- large injection molding machine
- large injection molding machines
- Learn what industrial automation and robotics is
- linear robot
- linear robots
- low speed sound-proof granulator
- machine plastic molding
- make sure to add some! Improvements (2) Keyphrase in introduction: Your keyphrase or its synonyms appear in the first paragraph of the copy
- manipulator machine
- manufacturing
- medical grade injection molding machines
- medical injection molding machine
- medical injection molding machines
- micro injection molding machine
- middle speed granulator
- Mini CNC machine manufacturers.
- Mold Temperature Control System
- mold temperature controller
- mold temperature controllers
- molding material Dehumidifying System
- mould temperature control system
- mould temperature controller
- mould temperature controllers
- New electric injection molding machine
- nitrogen dryer manufacturer
- nitrogen dryer system manufacturer
- Oil type mold temperature controller
- Oil type mold temperature controllers
- open day
- Outbound links: No outbound links appear in this page. Add some! Images: No images appear on this page. Add some! Internal links: No internal links appear in this page
- PET Preform injection molding
- phone case maker machine
- phone case making machine
- phone cover making machine
- plastic bottle making machine
- plastic bottle manufacturing
- plastic bucket making machine
- plastic bucket manufacturing
- Plastic chair making machine
- plastic forming equipment
- plastic hopper dryer
- plastic injection machine
- plastic injection machines
- plastic injection molding
- Plastic injection molding equipment
- Plastic injection molding machine
- Plastic Injection Molding Machines
- plastic injection moulding machine
- plastic injection moulding machines
- plastic injection robot
- plastic molding
- Plastic Molding machine
- plastic molding machine 1
- Plastic Molding Machines
- plastic molding press
- plastic moulding machine
- plastic phone case making machine
- plastic-molding machine
- powerful granulator
- Powerful Type Sound-Proof Granulator
- precision injection molding
- precision injection molding machines
- production of plastic seats
- pure water mould temperature controller
- Robot injection molding
- robot injection molding machine
- robot manufacturing companies
- Robotic arm for injection molding machine
- robotic injection molding machines
- robotics in injection molding
- SCARA robot
- SCARA robots
- Service-oriented manufacturing
- Servo Cylinder Robot
- servo driven robot
- Servo Driven Robots
- servo injection molding machine
- servo injection robots
- servo motor-driven linear robots
- servo-driven 3-axis robot
- Servo-Driven Robot
- Setup of injection machine
- Silicone Injection Molding Machine
- six-axis industrial robot
- Stainless Hopper Dryer
- Stainless Hopper Dryers
- star club
- swing arm robot
- take-out robot
- take-out robots
- the choice between servo-driven robots and hydraulic robots will have a certain impact on efficiency
- the most popular injection molding machine
- the type of injection molding robot
- TMII injection molding machine
- toggle clamp injection molding machine
- Toggle Hydraulic Injection Molding Machines
- toggle injection molding machine
- Top 10 brands of injection robots
- Topstar
- Topstar Engineering
- Topstar Industrial Robots
- Topstar injection molding intelligent
- Topstar Scara Robots
- Useful Injection molding machine
- Vertical machining centers
- volumetric type blender
- water chiller
- water chillers
- water distributor
- water type mold temperature controller
- Water Type MoldTemperature Controller
- Water-Type Mould Temperature Controllers
- We often face choices when performing injection molding. We will choose the type of injection molding machine
- wholesale of injection molding machines
- x carve CNC
- 热门查询 点击次数 展示 排名 topstar