What key efficiency improvements can Injection Robots achieve?
2024/11/27 By Topstar
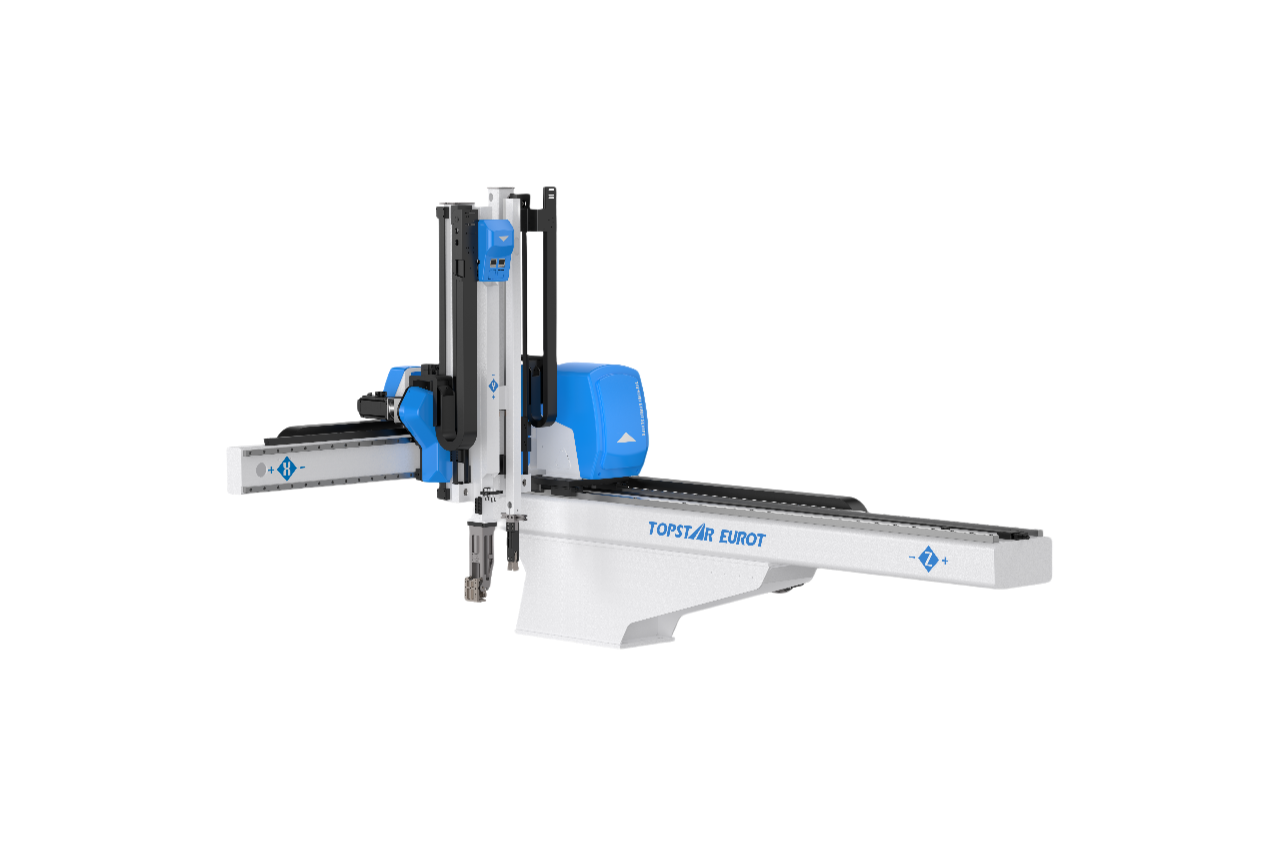
Injection robots automatically place and grab plastic parts instead of performing manual tasks. Doing so helps simplify injection molding production lines, shorten cycle times, minimize human errors, and increase production. They improve the precision and consistency of molded parts, save more energy, and improve workplace safety. As one of Topstar’s self-developed and self-produced products, the injection robot has come to the fifth generation, the five-in-one servo injection robot. So, in this article, we will introduce you to the critical efficiency improvements they can achieve.
The energy efficiency of the injection robots has increased by 20%
Every stop and collision of the machine will incur high costs, significantly reducing the energy efficiency of production. Therefore, Topstar has achieved a more precise, energy-saving, and intelligent “five-in-one” servo drive based on upgrading the underlying technical architecture of software and hardware. “Five-in-one servo drive” enables one servo drive to control 5 servo motors directly, and the removal control is more precise. Only 3 CPU chips are used to achieve a five-axis-in-one design. Each CPU chip controls two axes, and the maximum power of each axis is 750W. This provides mighty power for the injection robot. At the same time, the multi-axis standard busbar design scheme improves energy efficiency by 20%.
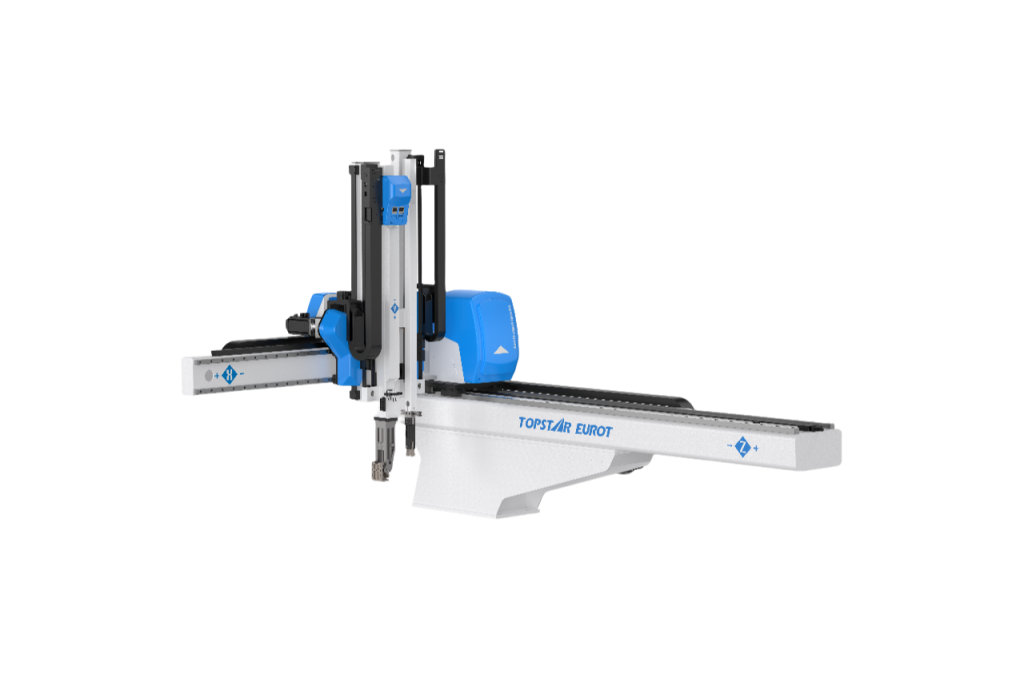
Increase production efficiency by 5% for each injection molding unit.
Traditional injection robot management aims to achieve cross-system interconnection through network protocols, which have signal delay, poor compatibility, and low stability. Topstar uses the open architecture of the underlying control system to enable injection molding peripheral auxiliary machines and injection molding machines to have a native language for system integration, making equipment interconnection an extension of the system. This can enable the injection robot to support the host to call signals, realize integrated operation, and allow the control system to automatically optimize the removal process, thereby improving the injection molding efficiency of the production line. It solves the problems of removal failure and equipment alarm shutdown caused by ejection position deviation and uncoordinated suction time. The injection robot and the mold opening process are synchronized, which increases the production efficiency of each intelligent injection molding unit by about 5%.
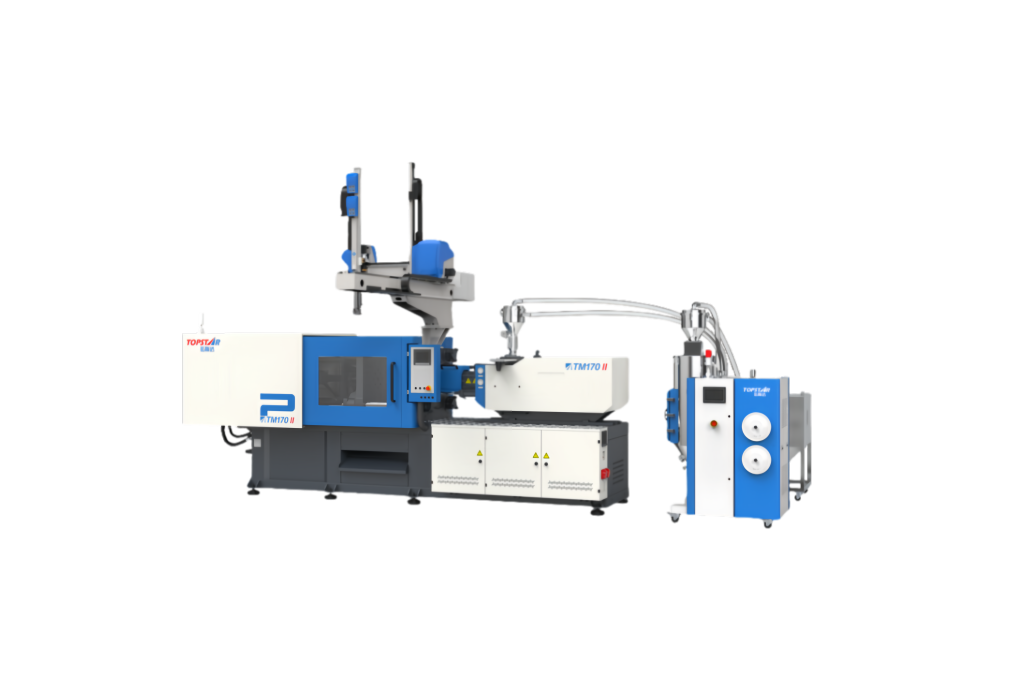
Enhanced the expansion and flexibility of the injection robots
Under the five-in-one servo drive system, the injection robot has more robust functional scalability and can add back-end automation processes according to customer needs. The robot’s back end can customize according to specific production requirements, whether it integrates quality inspection, classification, packaging, or additional material handling. This scalability ensures manufacturers can adapt to changing market demands without purchasing new robot systems.
At the same time, advanced manipulator motion control technology ensures smooth and precise movement according to predetermined contours when executing complex trajectories or paths. This flexibility’s efficiency improvement means a shorter production cycle, which shortens the turnaround time and increases the output, greatly improving the workshop’s production quality and efficiency.
Lighter weight and faster speed
The injection robot uses an arm of lightweight and high-strength A6061 material, reducing 20 structural components and weight by 20%. This makes the robot more flexible without affecting strength. Therefore, it is lighter and more capable of handling heavy tasks. The high-strength aluminum material ensures that the robot can withstand the pressure of rapid acceleration and deceleration without the risk of deformation or wear, thereby extending its service life. Weight reduction is also a great help in improving performance, especially speed and efficiency. Their maximum speed has increased by 10%, allowing the system to complete tasks faster without sacrificing accuracy. In addition, the time required for acceleration and deceleration has also been reduced by 20%, enabling faster start and stop of its actions.
Safer operation
The injection robot protection technology (soft floating joints) dramatically improves the robot’s ability to handle unexpected situations. This technology detects when the robot experiences excessive torque or strain, allowing the system to respond automatically by softening the movement or adjusting the torque level. This significantly improves the protection capability when facing torques exceeding the set torque, effectively reducing potential damage to customer molds, injection molding machine ejectors, and products and further improving production efficiency and equipment stability.
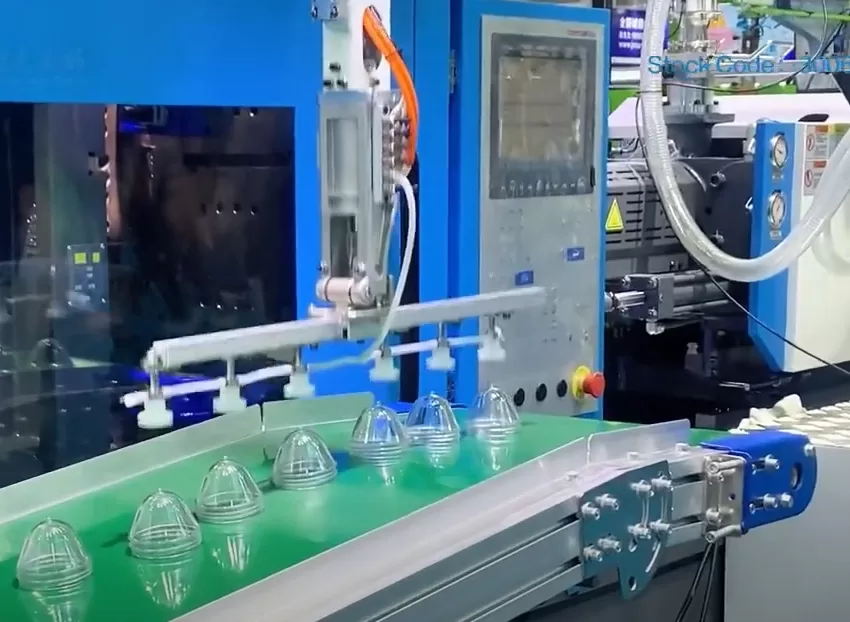
At the same time, the optional “personnel protection configuration” reduces the risk of accidental injury due to unintentional contact with the running machine. This configuration provides additional safety protection for workers. It includes built-in sensors and safety barriers that detect whether there are human operators near the robot’s operating area. If the operator is too close to the robot, the system will immediately stop the robot’s movement to reduce the risk of accidental injury.
Comprehensively improve the efficiency of injection molding production.
Based on the “five-in-one” servo drive, the injection molding robot’s energy efficiency, production efficiency, expansion, and flexibility have been greatly improved. By automating key processes, these injection robots can improve productivity and promote safer and more sustainable operations.
TRENDING POSTS
- What factors can cause delays in the injection molding process of plastic molding machine? 2024/11/27
- Exhibition Review| Topstar participates in InterPlas Thailand 2024 2024/11/27
- Star Case | Topstar helps Santong upgrade its intelligent plant 2024/11/27
- Topstar Special | National Science and Technology Workers Day 2024/11/27
HOT TOPIC
- .ervo motor-driven linear robots
- 1.0 guangdong topstar technology co. ltd
- 1.0 topstar china
- 1.0 topstar robot
- 11
- 2
- 21
- 23
- 3 axis robot
- 3 axis robots
- 3 in 1 Compact Dehumidifying Dryer
- 3-axis robot
- 3-axis robots
- 39
- 41
- 5-axis CNC machine
- 62
- accuracy
- Air Chillers
- all electric injection molding machine
- all electric injection molding machines
- All-electric injection molding machines
- and overall production quality. Therefore
- AP-RubberPlas
- automated injection molding machine
- Automation changed engineering
- automation of injection molding robots
- auxiliary machine
- Bench Injection Molding Machine
- Cabinet dryer manufacturers
- Cabinet dryers
- chiller
- CNC Drilling Machine
- CNC Drilling Machines
- cnc engraving machine manufacturer
- cnc laser cutting machine manufacturer
- CNC machine
- CNC Machine Center
- CNC Machine for Sale
- CNC Machine Manufacturing
- CNC Machine Tool
- CNC machine tool product
- CNC Machining Center
- CNC wood carving machine
- Cooling system
- Cross-Walking Single Axis Servo Cylinder Robot
- Cross-Walking Single-Axis Servo Cylinder Robot
- Cross-Walking Three-Axis/Five-Axis Servo Driven Robot
- cross-walking three-axis/five-axis servo-driven robot
- Dehumidifier Dryer
- Dehumidifying Dryer
- delta parallel robot
- Desktop Injection Molding Machine
- Desktop injection molding machines
- Desktop Molding Machine
- desktop plastic injection machine
- Desktop Plastic Injection Molding Machine
- direct clamp injection molding machine
- Direct clamp injection molding machines
- Dosing & mixing system
- Drilling Centers
- Drying and dehumidification system
- drying and dehumidifying equipment
- Drying and Dehumidifying System
- drying system
- effective and efficient. Cabinet dryers are also used in other industries where large quantities of material need to be dried
- efficient injection molding machine
- elbow hydraulic injection molding machines
- electric injection molding machine
- electric injection molding machines
- energy-efficient injection molding robot
- energy-saving injection molding machine
- etc. Among injection molding robots
- exhibition
- features of CNC machine
- Feeding And Conveying System
- Five Axis Machine Center
- Fully automatic injection molding machine
- Gathering Topstar
- giant injection molding machine
- GMU-600 5-Axis Machining Center
- Granulating & Recycling System
- Heavy duty injection molding machine
- High-precision electric molding machines
- high-precision plastic molding machines
- high-speed all electric injection molding machine
- Honeycomb rotor dehumidifier
- horizontal injection molding machine
- Horizontal Injection Molding Machines
- Horizontal Injection Moulding Machine
- Horizontal Mixer manufacturer
- How The CNC Machine Works
- hybrid injection molding machine
- hydraulic injection molding machine
- Hydraulic Injection Molding Machines
- in this article
- Industrial robot
- Industrial Robot Chinese brand
- industrial robot parts
- industrial robot supplier
- Industrial robots
- Industry Chain
- Injection Manipulator
- injection manipulator robot
- injection mold machines
- Injection molding
- Injection molding automation
- Injection Molding Automation Solution
- injection molding dryer
- Injection molding equipment
- injection molding hopper dryer
- Injection molding machine
- injection molding machine brand
- Injection Molding Machine Factory
- Injection Molding Machine Manufacture
- Injection molding machine manufacturer
- injection molding machine manufacturers
- Injection molding machine procurement
- injection molding machine robotic arm
- injection molding machine with a robot
- Injection molding machines
- injection molding material dehumidifying
- injection molding plant
- Injection Molding Robot
- injection molding robot arm
- Injection molding robot automation
- Injection molding robotic arm
- injection molding robots
- Injection moulding machine
- Injection Moulding Robots
- Injection Robot
- Injection robot arm
- Injection robot manufacturer
- Injection robot wholesale
- injection robots
- intelligent injection molding machines
- Introducing Injection Robot
- It is the best choice for drying large quantities of material at once. Cabinetmakers use these machines because they are fast
- large injection molding machine
- large injection molding machines
- Learn what industrial automation and robotics is
- linear robot
- linear robots
- low speed sound-proof granulator
- machine plastic molding
- make sure to add some! Improvements (2) Keyphrase in introduction: Your keyphrase or its synonyms appear in the first paragraph of the copy
- manipulator machine
- manufacturing
- medical grade injection molding machines
- medical injection molding machine
- medical injection molding machines
- micro injection molding machine
- middle speed granulator
- Mini CNC machine manufacturers.
- Mold Temperature Control System
- mold temperature controller
- mold temperature controllers
- molding material Dehumidifying System
- mould temperature control system
- mould temperature controller
- mould temperature controllers
- New electric injection molding machine
- nitrogen dryer manufacturer
- nitrogen dryer system manufacturer
- Oil type mold temperature controller
- Oil type mold temperature controllers
- open day
- Outbound links: No outbound links appear in this page. Add some! Images: No images appear on this page. Add some! Internal links: No internal links appear in this page
- PET Preform injection molding
- phone case maker machine
- phone case making machine
- plastic bottle making machine
- plastic bottle manufacturing
- plastic bucket making machine
- plastic bucket manufacturing
- Plastic chair making machine
- plastic forming equipment
- plastic hopper dryer
- plastic injection machine
- plastic injection machines
- plastic injection molding
- Plastic injection molding equipment
- Plastic injection molding machine
- Plastic Injection Molding Machines
- plastic injection moulding machine
- plastic injection robot
- Plastic Molding machine
- Plastic Molding Machines
- plastic molding press
- plastic moulding machine
- plastic phone case making machine
- plastic-molding machine
- powerful granulator
- Powerful Type Sound-Proof Granulator
- precision injection molding
- precision injection molding machines
- production of plastic seats
- pure water mould temperature controller
- Robot injection molding
- robot injection molding machine
- robot manufacturing companies
- Robotic arm for injection molding machine
- robotic injection molding machines
- robotics in injection molding
- SCARA robot
- SCARA robots
- Service-oriented manufacturing
- Servo Cylinder Robot
- servo driven robot
- Servo Driven Robots
- servo injection robots
- servo motor-driven linear robots
- servo-driven 3-axis robot
- Servo-Driven Robot
- Setup of injection machine
- Silicone Injection Molding Machine
- six-axis industrial robot
- Stainless Hopper Dryer
- Stainless Hopper Dryers
- star club
- swing arm robot
- take-out robots
- the choice between servo-driven robots and hydraulic robots will have a certain impact on efficiency
- the most popular injection molding machine
- the type of injection molding robot
- toggle clamp injection molding machine
- Toggle Hydraulic Injection Molding Machines
- toggle injection molding machine
- Top 10 brands of injection robots
- Topstar
- Topstar Engineering
- Topstar Industrial Robots
- Topstar injection molding intelligent
- Topstar Scara Robots
- Useful Injection molding machine
- Vertical machining centers
- volumetric type blender
- water chiller
- water chillers
- water distributor
- water type mold temperature controller
- Water Type MoldTemperature Controller
- Water-Type Mould Temperature Controllers
- We often face choices when performing injection molding. We will choose the type of injection molding machine
- wholesale of injection molding machines
- x carve CNC
- 热门查询 点击次数 展示 排名 topstar