Which injection molding machine is the most productive?
2024/04/12 By Topstar
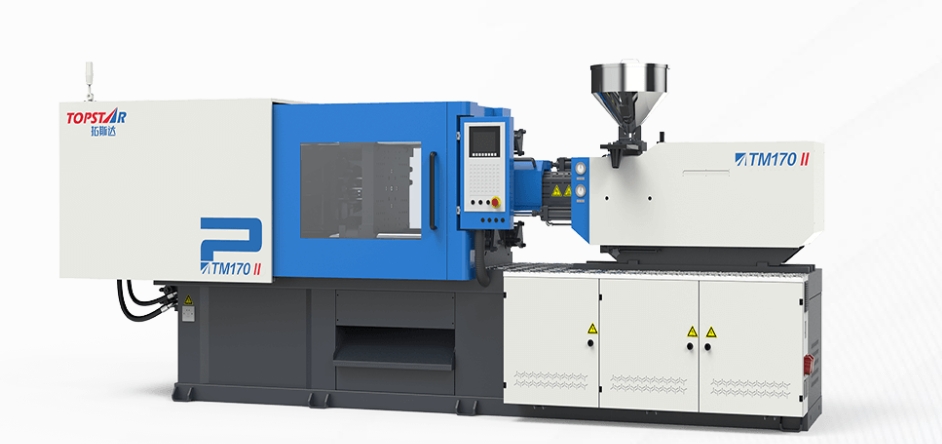
Every manufacturing boss will pay attention to the production capacity of his workshop every day or even every quarter, which is directly related to profit income. In injection molding, the core equipment is the injection molding machine, which is the key to determining productivity and capacity. There are different configurations in various injection molding machines, so there will be differences in production capacity.
What factors are related to production capacity in injection molding?
The production capacity in injection molding is related to different factors. The first is the selection of raw materials. Different material types and qualities will directly affect molding, cycle time, and part quality. Next, mold design and structure will also have a certain impact on production capacity. The most important thing is the injection molding machine and its process parameters. Each type of injection molding machine affects cycle time and overall production efficiency in terms of injection accuracy, repeatability, and speed. It is also necessary to combine the settings of their process parameters including temperature, pressure, and injection speed to obtain higher productivity.
The relationship between production capacity and raw materials
The type of raw material selected will affect the production capacity of the injection molding machine. Different materials have different flow characteristics, viscosity, and melt temperature, directly affecting the injection molding process. For example, high-viscosity materials may require higher injection pressures and longer fill times, impacting the machine’s throughput and overall capacity. Their physical properties, such as melt flow index, shrinkage, and thermal conductivity, also affect the throughput of the injection molding machine. Using materials with a high melt flow index makes flowing through the injection device easier, resulting in faster fill times and higher throughput.
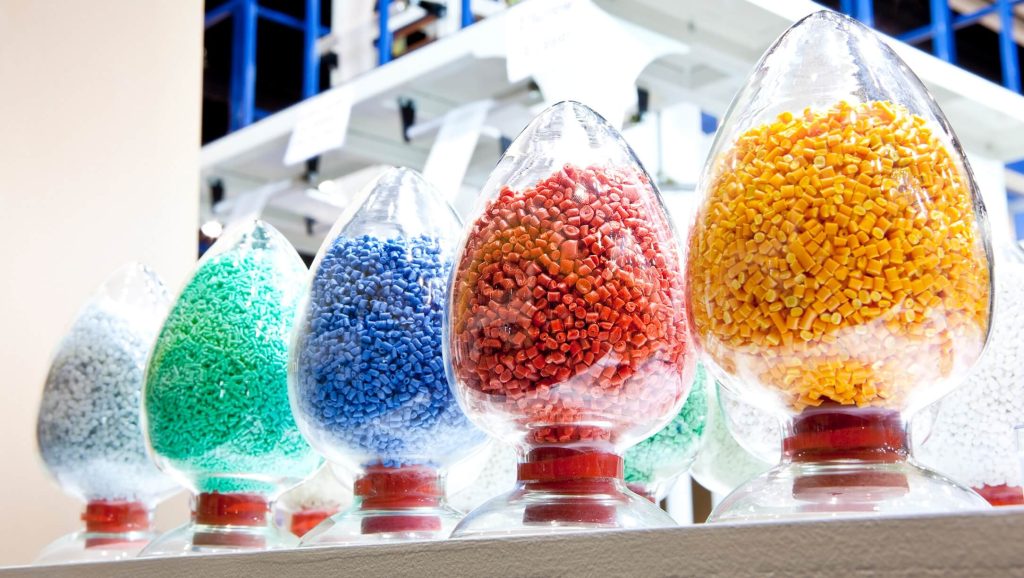
The relationship between production capacity and mold design and structure
Different mold designs can affect part cycle times and thus productivity. While the mold’s structural integrity maintains consistent part quality, a rugged mold design can withstand the stresses and pressures of the injection molding process, reducing the likelihood of mold damage. If the mold you use is simple, it will help simplify the production process, increase productivity, and increase tenderness. Different clamping forces and injection pressures will also affect the final production capacity. The clamping force range that Topstar can provide is 90t-2200t, which can meet the production of different plastic products and the corresponding production capacity.
Relationship with injection molding machine type
Hydraulic injection molding machines are one of the more traditional types. They can provide strong clamping force and large injection capacity while being able to handle a variety of materials and applications, allowing the production of large plastic parts and high-volume production. However, they typically have longer cycle times than electric injection molding machines, thus affecting overall throughput and productivity and ultimately throughput.
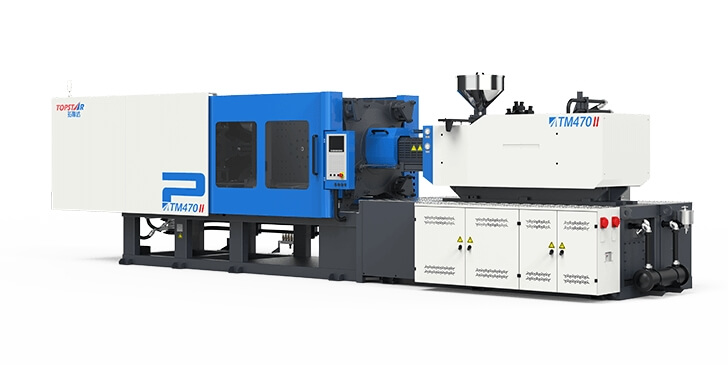
On the other hand, electric injection molding machines can precisely control the injection process, resulting in shorter cycle times and improved repeatability. Gain more throughput by utilizing electric servo motors for all machine functions including clamping, injection, and ejection for fast cycle times.
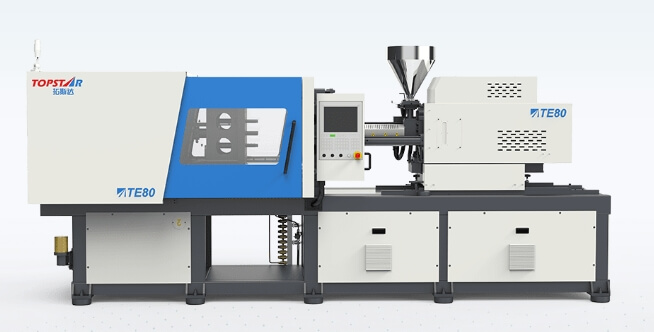
Hybrid injection molding machines combine the best features of the two previous machines, achieving a balance between power, precision, and energy efficiency. Boasting the flexibility and performance of an electric motor with the robustness and power of a hydraulic system, it increases productivity while saving energy.
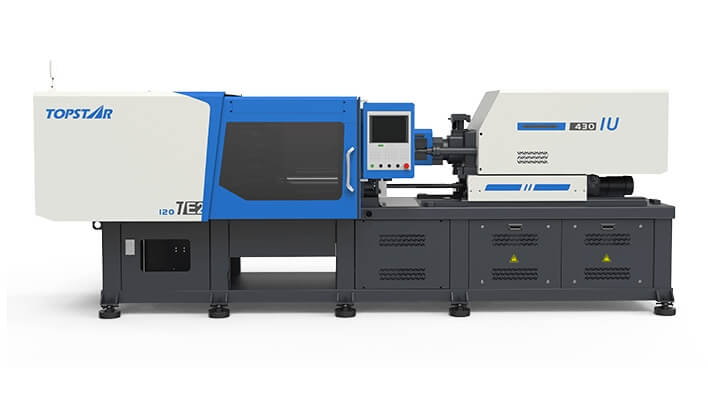
Optimize injection molding machine process parameters to increase production capacity
During the entire injection molding process, parameters such as temperature, pressure, and injection speed can be adjusted in a targeted manner to increase output. Differences in temperature during injection molding will directly affect material flow and melt quality. Properly adjusted settings for barrel and mold temperatures ensure proper material viscosity and mold filling, resulting in faster cycle times and increased throughput. In addition, you can carefully adjust injection pressure and speed based on material properties and part requirements, allowing for optimal fill times while avoiding issues like burrs, sink marks, or warping. High injection speeds are beneficial for filling molds quickly, shortening molding cycle times, and increasing throughput if the material flow remains uniform and controlled.
Acquire production capacity based on circumstances
According to the description in the article, the production capacity of an injection molding machine is related to the type of machine used, clamping force, injection pressure, and raw materials used. Therefore, we cannot directly give a standard answer, but in the daily injection molding process, relevant injection molding parameters must be optimized to improve the overall production capacity further.
TRENDING POSTS
- What factors can cause delays in the injection molding process of plastic molding machine? 2024/04/12
- Exhibition Review| Topstar participates in InterPlas Thailand 2024 2024/04/12
- Star Case | Topstar helps Santong upgrade its intelligent plant 2024/04/12
- Topstar Special | National Science and Technology Workers Day 2024/04/12
HOT TOPIC
- .ervo motor-driven linear robots
- 3 axis robot
- 3 axis robots
- 3 in 1 Compact Dehumidifying Dryer
- 3-axis robot
- 3-axis robots
- 5-axis CNC machine
- accuracy
- Air Chillers
- all electric injection molding machine
- all electric injection molding machines
- All-electric injection molding machines
- and overall production quality. Therefore
- AP-RubberPlas
- automated injection molding machine
- Automation changed engineering
- automation of injection molding robots
- auxiliary machine
- Bench Injection Molding Machine
- Cabinet dryer manufacturers
- Cabinet dryers
- chiller
- CNC Drilling Machine
- CNC Drilling Machines
- cnc engraving machine manufacturer
- cnc laser cutting machine manufacturer
- CNC machine
- CNC Machine Center
- CNC Machine for Sale
- CNC Machine Manufacturing
- CNC Machine Tool
- CNC machine tool product
- CNC Machining Center
- CNC wood carving machine
- Cooling system
- Cross-Walking Single Axis Servo Cylinder Robot
- Cross-Walking Single-Axis Servo Cylinder Robot
- Cross-Walking Three-Axis/Five-Axis Servo Driven Robot
- cross-walking three-axis/five-axis servo-driven robot
- Dehumidifier Dryer
- Dehumidifying Dryer
- delta parallel robot
- Desktop Injection Molding Machine
- Desktop injection molding machines
- Desktop Molding Machine
- desktop plastic injection machine
- Desktop Plastic Injection Molding Machine
- direct clamp injection molding machine
- Direct clamp injection molding machines
- Dosing & mixing system
- Drilling Centers
- Drying and dehumidification system
- drying and dehumidifying equipment
- Drying and Dehumidifying System
- drying system
- effective and efficient. Cabinet dryers are also used in other industries where large quantities of material need to be dried
- efficient injection molding machine
- elbow hydraulic injection molding machines
- electric injection molding machine
- electric injection molding machines
- energy-efficient injection molding robot
- energy-saving injection molding machine
- etc. Among injection molding robots
- exhibition
- features of CNC machine
- Feeding And Conveying System
- Five Axis Machine Center
- Fully automatic injection molding machine
- Gathering Topstar
- giant injection molding machine
- GMU-600 5-Axis Machining Center
- Granulating & Recycling System
- Heavy duty injection molding machine
- High-precision electric molding machines
- high-precision plastic molding machines
- high-speed all electric injection molding machine
- Honeycomb rotor dehumidifier
- horizontal injection molding machine
- Horizontal Injection Molding Machines
- Horizontal Injection Moulding Machine
- Horizontal Mixer manufacturer
- How The CNC Machine Works
- hybrid injection molding machine
- hydraulic injection molding machine
- Hydraulic Injection Molding Machines
- in this article
- Industrial robot
- Industrial Robot Chinese brand
- industrial robot parts
- industrial robot supplier
- Industrial robots
- Industry Chain
- Injection Manipulator
- injection manipulator robot
- injection mold machines
- Injection molding
- Injection molding automation
- Injection Molding Automation Solution
- injection molding dryer
- Injection molding equipment
- injection molding hopper dryer
- Injection molding machine
- injection molding machine brand
- Injection Molding Machine Factory
- Injection Molding Machine Manufacture
- Injection molding machine manufacturer
- injection molding machine manufacturers
- Injection molding machine procurement
- injection molding machine robotic arm
- injection molding machine with a robot
- Injection molding machines
- injection molding material dehumidifying
- injection molding plant
- Injection Molding Robot
- injection molding robot arm
- Injection molding robot automation
- Injection molding robotic arm
- injection molding robots
- Injection moulding machine
- Injection Moulding Robots
- Injection Robot
- Injection robot arm
- Injection robot manufacturer
- Injection robot wholesale
- injection robots
- intelligent injection molding machines
- Introducing Injection Robot
- It is the best choice for drying large quantities of material at once. Cabinetmakers use these machines because they are fast
- large injection molding machine
- large injection molding machines
- Learn what industrial automation and robotics is
- linear robot
- linear robots
- low speed sound-proof granulator
- machine plastic molding
- make sure to add some! Improvements (2) Keyphrase in introduction: Your keyphrase or its synonyms appear in the first paragraph of the copy
- manipulator machine
- manufacturing
- medical grade injection molding machines
- medical injection molding machine
- medical injection molding machines
- micro injection molding machine
- middle speed granulator
- Mini CNC machine manufacturers.
- Mold Temperature Control System
- mold temperature controller
- mold temperature controllers
- molding material Dehumidifying System
- mould temperature control system
- mould temperature controller
- mould temperature controllers
- New electric injection molding machine
- nitrogen dryer manufacturer
- nitrogen dryer system manufacturer
- Oil type mold temperature controller
- Oil type mold temperature controllers
- open day
- Outbound links: No outbound links appear in this page. Add some! Images: No images appear on this page. Add some! Internal links: No internal links appear in this page
- PET Preform injection molding
- phone case maker machine
- phone case making machine
- plastic bottle making machine
- plastic bottle manufacturing
- plastic bucket making machine
- plastic bucket manufacturing
- Plastic chair making machine
- plastic forming equipment
- plastic hopper dryer
- plastic injection machine
- plastic injection machines
- plastic injection molding
- Plastic injection molding equipment
- Plastic injection molding machine
- Plastic Injection Molding Machines
- plastic injection moulding machine
- plastic injection robot
- Plastic Molding machine
- Plastic Molding Machines
- plastic molding press
- plastic moulding machine
- plastic phone case making machine
- plastic-molding machine
- powerful granulator
- Powerful Type Sound-Proof Granulator
- precision injection molding
- precision injection molding machines
- production of plastic seats
- pure water mould temperature controller
- Robot injection molding
- robot injection molding machine
- robot manufacturing companies
- Robotic arm for injection molding machine
- robotic injection molding machines
- robotics in injection molding
- SCARA robot
- SCARA robots
- Service-oriented manufacturing
- Servo Cylinder Robot
- servo driven robot
- Servo Driven Robots
- servo injection robots
- servo motor-driven linear robots
- servo-driven 3-axis robot
- Servo-Driven Robot
- Setup of injection machine
- Silicone Injection Molding Machine
- six-axis industrial robot
- Stainless Hopper Dryer
- Stainless Hopper Dryers
- star club
- swing arm robot
- take-out robots
- the choice between servo-driven robots and hydraulic robots will have a certain impact on efficiency
- the most popular injection molding machine
- the type of injection molding robot
- toggle clamp injection molding machine
- Toggle Hydraulic Injection Molding Machines
- toggle injection molding machine
- Top 10 brands of injection robots
- Topstar
- Topstar Engineering
- Topstar Industrial Robots
- Topstar injection molding intelligent
- Topstar Scara Robots
- Useful Injection molding machine
- Vertical machining centers
- volumetric type blender
- water chiller
- water chillers
- water distributor
- water type mold temperature controller
- Water Type MoldTemperature Controller
- Water-Type Mould Temperature Controllers
- We often face choices when performing injection molding. We will choose the type of injection molding machine
- wholesale of injection molding machines
- x carve CNC