Why is the preheating function of the mould temperature controller so important?
2025/05/14 By Topstar
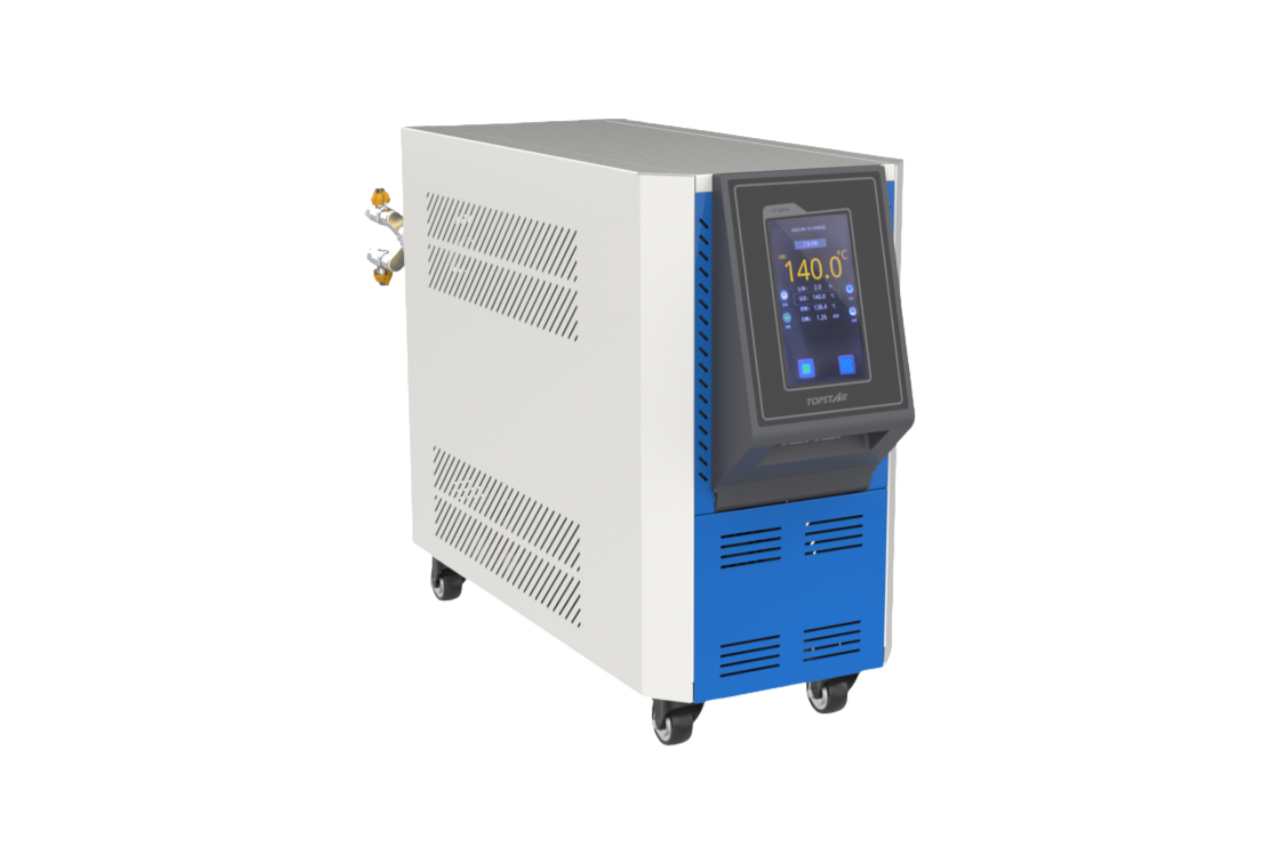
When changing moulds, operators must wait for the new mould to preheat to operating temperature and the old mould to cool completely before removing it. This waiting time is often more than 30-60 minutes, leading to lost production time. A mould temperature controller with preheating function can automatically start heating one hour before the expected mould change, thus bridging this gap and ensuring that the next mould is at the optimal temperature when installed. As a result, mould changes are faster and downtime is reduced, allowing manufacturers to meet the needs of high-mix, high-volume production in areas such as automotive or consumer electronics packaging. And by integrating the preheating function into the workflow of the mould temperature controller, production efficiency will be significantly improved.
Shorten mould change downtime through forced cooling of the mould temperature controller.
The mould change process requires sufficient cooling of the hot mould to ensure safe operation. The mould temperature controller with forced cooling function solves the problem of long cooling time by continuously opening the cooling solenoid valve after production to allow the maximum coolant flow to flow through the mould channel. In a mould temperature control system, forced cooling can reduce the mould temperature from 200°C to below 50°C in about 10 minutes. The timed cooling function of the mould temperature controller precisely manages this rapid cooling, minimizing non-productive intervals. The timed on-off feature further enhances this benefit by enabling a seamless transition to the preheating phase. Combining rapid forced cooling with intelligent preheat scheduling eliminates traditional temperature cycle delays, allowing for faster mould changes.
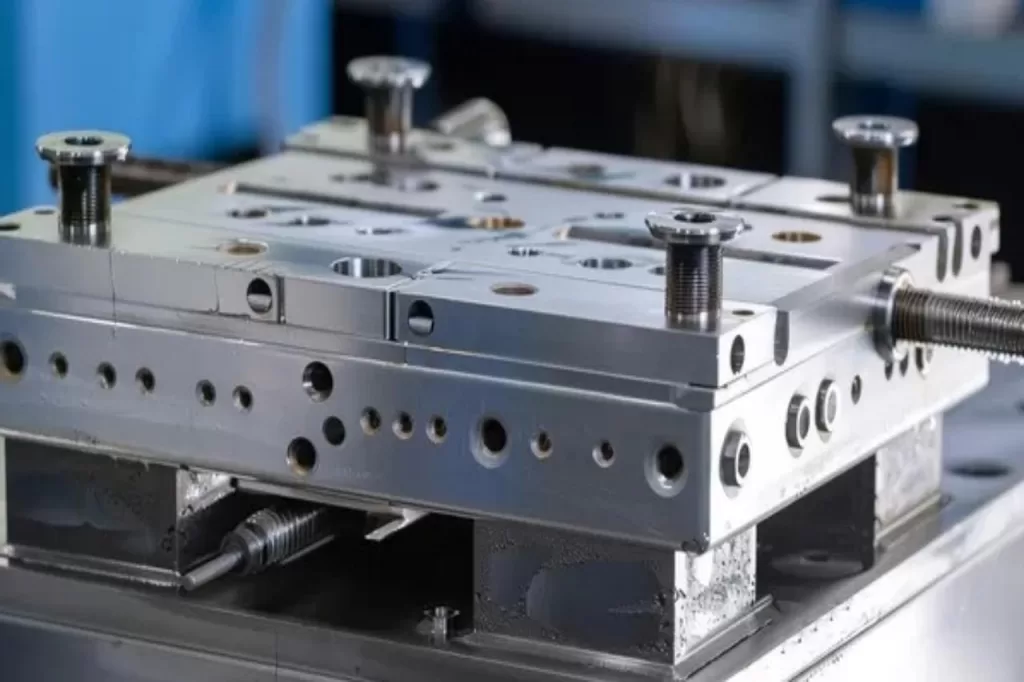
Timed On/Off Functionality and Preheat Scheduling for Mould Temperature Controller
The heart of the advanced preheating capabilities in Topstar’s mould temperature controllers lies in their programmable timers. Users enter the estimated mould change time into the controller interface, and the system automatically powers the heater cartridges at predetermined intervals to reach the set temperature when the mould arrives. Mould temperature controllers with timed on-off functionality replace manual intervention and guesswork by automatically achieving optimal temperature conditions without requiring operator supervision. Combined with an intelligent PID control loop, the mould temperature controller balances heater output and coolant flow during preheating to avoid overshoot and maintain uniform mould temperature. This precise timing reduces energy waste by heating when needed and ensures that production resumes immediately after mould installation.
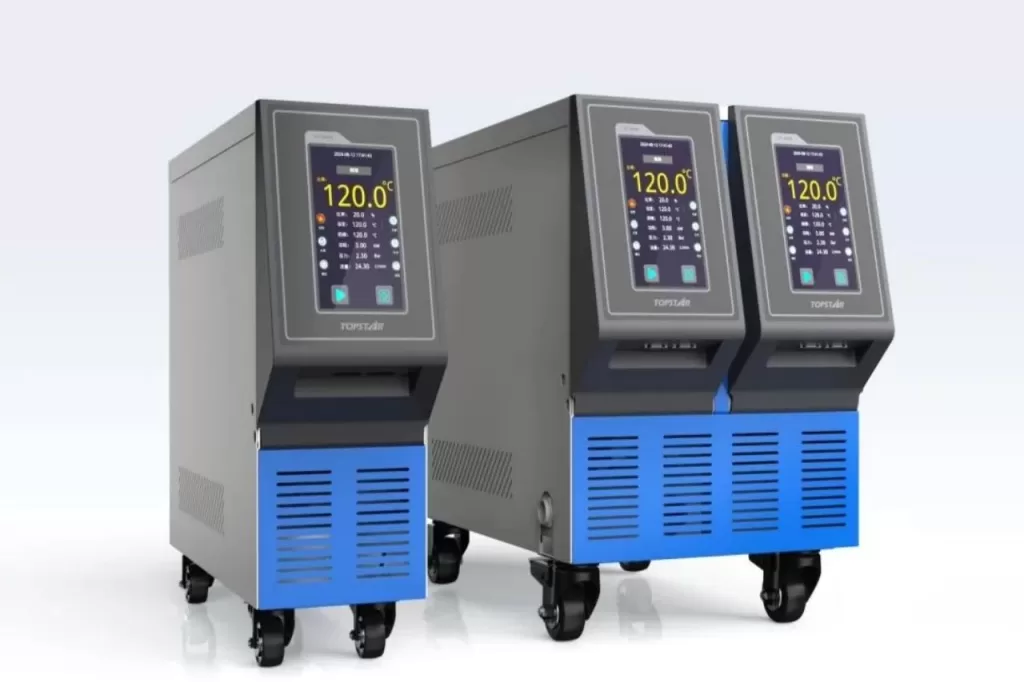
Improved Productivity and Cycle Time
Implementing the preheating feature in advance can bring significant productivity improvements to any injection moulding plant. By shortening the mould change window by approximately 10%, an 8-hour shift can accommodate additional mould changes, equating to tens of thousands of additional parts per year in high-speed packaging applications. Mould temperature controllers equipped with preheat and forced cooling can significantly reduce the average downtime per mould change from 45 minutes to less than 20 minutes, freeing up machine production cycles. For industries that require frequent mould changes, such as medical device or consumer electronics manufacturers, this feature ensures maximum mould temperature controller utilisation, reduces labor costs for manual preheat monitoring, and shortens lead times.
Improve part quality through thermal consistency
In addition to increasing production, the mould temperature controller’s preheat function directly impacts part quality. Stable mould temperatures minimise thermal gradients that cause weld lines, sink marks, or dimensional deformation. The mould temperature controller ensures that the molten polymer fills the cavity under uniform conditions from the first shot by preheating the mould to the precise process temperature before production begins. This uniformity results in a better surface finish and reduced scrap rates. Topstar’s mould temperature controller with preheating schedule provides this consistency, allowing manufacturers to adhere to strict quality standards while maintaining fast mould changes.
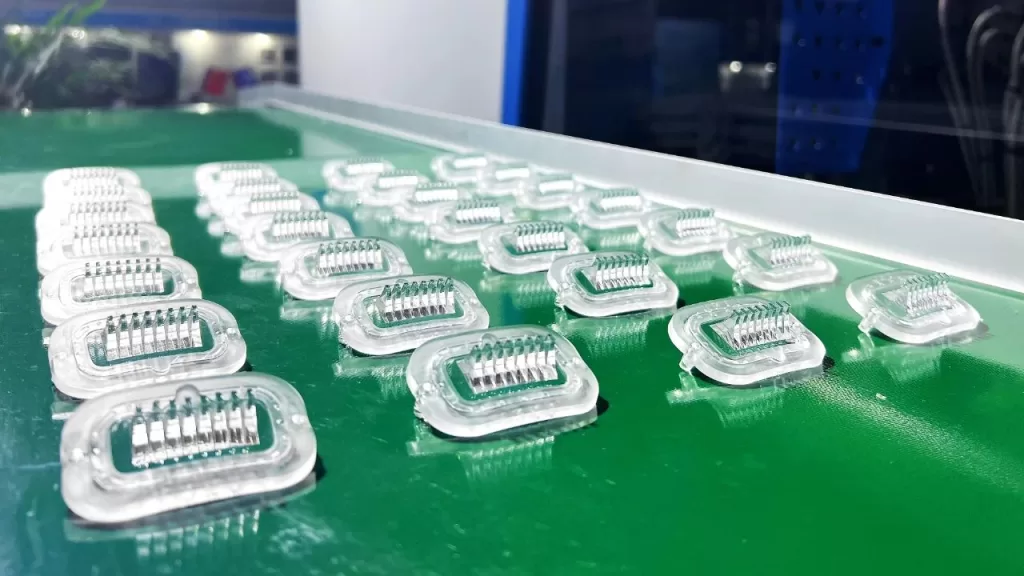
Remote operation and intelligent integration
Topstar integrates its mould temperature controller with injection moulding machines through a unified communication language under its self-developed control system, and also connects it with MES. Engineers can schedule preheating cycles, adjust setpoints, and monitor real-time mould temperatures of multiple machines from a central control room or even a mobile device. This mould temperature controller connection function helps predictive scheduling, ensuring that moulds receive accurate preheating commands when needed, or during non-working hours or shift changes. At the same time, automatic alarms notify operators of temperature deviations or maintenance needs, reducing unplanned downtime. Manufacturers can optimise their thermal management processes and overall production workflows by embedding advanced preheating functions into a broader industrial intelligence framework.
Maximise production efficiency through preheating.
Especially in multi-variety, high-volume production industries, the preheating function of mould temperature controllers can greatly improve production efficiency. Combined with forced cooling, precisely timed power control and networked scheduling, non-productive downtime is significantly reduced, mould change efficiency is increased by up to 10%, and ensuring part quality through stable thermal conditions.
TRENDING POSTS
- What factors can cause delays in the injection molding process of plastic molding machine? 2025/05/14
- Exhibition Review| Topstar participates in InterPlas Thailand 2024 2025/05/14
- Star Case | Topstar helps Santong upgrade its intelligent plant 2025/05/14
- Topstar Special | National Science and Technology Workers Day 2025/05/14
HOT TOPIC
- .ervo motor-driven linear robots
- 1.0 guangdong topstar technology co. ltd
- 1.0 topstar china
- 1.0 topstar robot
- 11
- 2
- 21
- 23
- 3 axis robot
- 3 axis robots
- 3 in 1 Compact Dehumidifying Dryer
- 3-axis robot
- 3-axis robots
- 39
- 41
- 5-axis CNC machine
- 62
- accuracy
- Air Chillers
- all electric injection molding machine
- all electric injection molding machines
- All-electric injection molding machines
- and overall production quality. Therefore
- AP-RubberPlas
- automated injection molding machine
- Automation changed engineering
- automation of injection molding robots
- auxiliary machine
- Bench Injection Molding Machine
- Cabinet dryer manufacturers
- Cabinet dryers
- chiller
- CNC Drilling Machine
- CNC Drilling Machines
- cnc engraving machine manufacturer
- cnc laser cutting machine manufacturer
- CNC machine
- CNC Machine Center
- CNC Machine for Sale
- CNC Machine Manufacturing
- CNC Machine Tool
- CNC machine tool product
- CNC Machining Center
- CNC wood carving machine
- Cooling system
- Cross-Walking Single Axis Servo Cylinder Robot
- Cross-Walking Single-Axis Servo Cylinder Robot
- Cross-Walking Three-Axis/Five-Axis Servo Driven Robot
- cross-walking three-axis/five-axis servo-driven robot
- Dehumidifier Dryer
- Dehumidifying Dryer
- delta parallel robot
- Desktop Injection Molding Machine
- Desktop injection molding machines
- Desktop Molding Machine
- desktop plastic injection machine
- Desktop Plastic Injection Molding Machine
- direct clamp injection molding machine
- Direct clamp injection molding machines
- Dosing & mixing system
- Drilling Centers
- Drying and dehumidification system
- drying and dehumidifying equipment
- Drying and Dehumidifying System
- drying system
- effective and efficient. Cabinet dryers are also used in other industries where large quantities of material need to be dried
- efficient injection molding machine
- elbow hydraulic injection molding machines
- electric injection molding machine
- electric injection molding machines
- energy-efficient injection molding robot
- energy-efficient water chiller
- energy-efficient water chillers
- energy-saving injection molding machine
- etc. Among injection molding robots
- exhibition
- features of CNC machine
- Feeding And Conveying System
- Five Axis Machine Center
- Fully automatic injection molding machine
- Gathering Topstar
- giant injection molding machine
- GMU-600 5-Axis Machining Center
- Granulating & Recycling System
- Heavy duty injection molding machine
- High-precision electric molding machines
- high-precision plastic molding machines
- high-speed all electric injection molding machine
- high-speed electric injection molding machine
- High-Speed Packaging Injection Molding
- Honeycomb rotor dehumidifier
- horizontal injection molding machine
- Horizontal Injection Molding Machines
- Horizontal Injection Moulding Machine
- Horizontal Mixer manufacturer
- How The CNC Machine Works
- hybrid injection molding machine
- hydraulic injection molding machine
- Hydraulic Injection Molding Machines
- in this article
- Industrial robot
- Industrial Robot Chinese brand
- industrial robot parts
- industrial robot supplier
- Industrial robots
- Industry Chain
- Injection Manipulator
- injection manipulator robot
- injection mold machines
- Injection molding
- Injection molding automation
- Injection Molding Automation Solution
- injection molding dryer
- Injection molding equipment
- injection molding hopper dryer
- Injection molding machine
- injection molding machine brand
- Injection Molding Machine Factory
- Injection Molding Machine Manufacture
- Injection molding machine manufacturer
- injection molding machine manufacturers
- Injection molding machine procurement
- injection molding machine robotic arm
- injection molding machine with a robot
- Injection molding machines
- injection molding material dehumidifying
- injection molding plant
- injection molding process
- Injection Molding Robot
- injection molding robot arm
- Injection molding robot automation
- Injection molding robotic arm
- injection molding robots
- Injection moulding machine
- injection moulding machines
- Injection Moulding Robots
- Injection Robot
- Injection robot arm
- Injection robot manufacturer
- Injection robot wholesale
- injection robots
- intelligent injection molding machines
- Intelligent mould temperature controller
- Introducing Injection Robot
- It is the best choice for drying large quantities of material at once. Cabinetmakers use these machines because they are fast
- Large flow water type mold temperature controller
- large injection molding machine
- large injection molding machines
- Learn what industrial automation and robotics is
- linear robot
- linear robots
- low speed sound-proof granulator
- machine plastic molding
- make sure to add some! Improvements (2) Keyphrase in introduction: Your keyphrase or its synonyms appear in the first paragraph of the copy
- manipulator machine
- manufacturing
- medical grade injection molding machines
- medical injection molding machine
- medical injection molding machines
- micro injection molding machine
- middle speed granulator
- Mini CNC machine manufacturers.
- Mold Temperature Control System
- mold temperature controller
- mold temperature controllers
- molding material Dehumidifying System
- mould temperature control system
- mould temperature controller
- mould temperature controllers
- New electric injection molding machine
- nitrogen dryer manufacturer
- nitrogen dryer system manufacturer
- Oil type mold temperature controller
- Oil type mold temperature controllers
- open day
- Outbound links: No outbound links appear in this page. Add some! Images: No images appear on this page. Add some! Internal links: No internal links appear in this page
- PET Preform injection molding
- phone case maker machine
- phone case making machine
- phone cover making machine
- plastic bottle making machine
- plastic bottle manufacturing
- plastic bucket making machine
- plastic bucket manufacturing
- Plastic chair making machine
- plastic forming equipment
- plastic hopper dryer
- plastic injection machine
- plastic injection machines
- plastic injection molding
- Plastic injection molding equipment
- Plastic injection molding machine
- Plastic Injection Molding Machines
- plastic injection moulding machine
- plastic injection moulding machines
- plastic injection robot
- plastic molding
- Plastic Molding machine
- plastic molding machine 1
- Plastic Molding Machines
- plastic molding press
- plastic moulding machine
- plastic phone case making machine
- plastic-molding machine
- powerful granulator
- Powerful Type Sound-Proof Granulator
- precision injection molding
- precision injection molding machines
- production of plastic seats
- pure water mould temperature controller
- Robot injection molding
- robot injection molding machine
- robot manufacturing companies
- Robotic arm for injection molding machine
- robotic injection molding machines
- robotics in injection molding
- SCARA robot
- SCARA robots
- Service-oriented manufacturing
- Servo Cylinder Robot
- servo driven robot
- Servo Driven Robots
- servo injection molding machine
- servo injection robots
- servo motor-driven linear robots
- servo-driven 3-axis robot
- Servo-Driven Robot
- Setup of injection machine
- Silicone Injection Molding Machine
- six-axis industrial robot
- Stainless Hopper Dryer
- Stainless Hopper Dryers
- star club
- swing arm robot
- take-out robot
- take-out robots
- the choice between servo-driven robots and hydraulic robots will have a certain impact on efficiency
- the most popular injection molding machine
- the type of injection molding robot
- TMII injection molding machine
- toggle clamp injection molding machine
- Toggle Hydraulic Injection Molding Machines
- toggle injection molding machine
- Top 10 brands of injection robots
- Topstar
- Topstar Engineering
- Topstar Industrial Robots
- Topstar injection molding intelligent
- Topstar Scara Robots
- Useful Injection molding machine
- Vertical machining centers
- volumetric type blender
- water chiller
- water chillers
- water distributor
- water type mold temperature controller
- Water Type MoldTemperature Controller
- Water-Type Mould Temperature Controllers
- We often face choices when performing injection molding. We will choose the type of injection molding machine
- wholesale of injection molding machines
- x carve CNC
- 热门查询 点击次数 展示 排名 topstar