Analyzing the Impact of Cooling System Design on Injection Molding Process Stability
2023/11/15 By Topstar
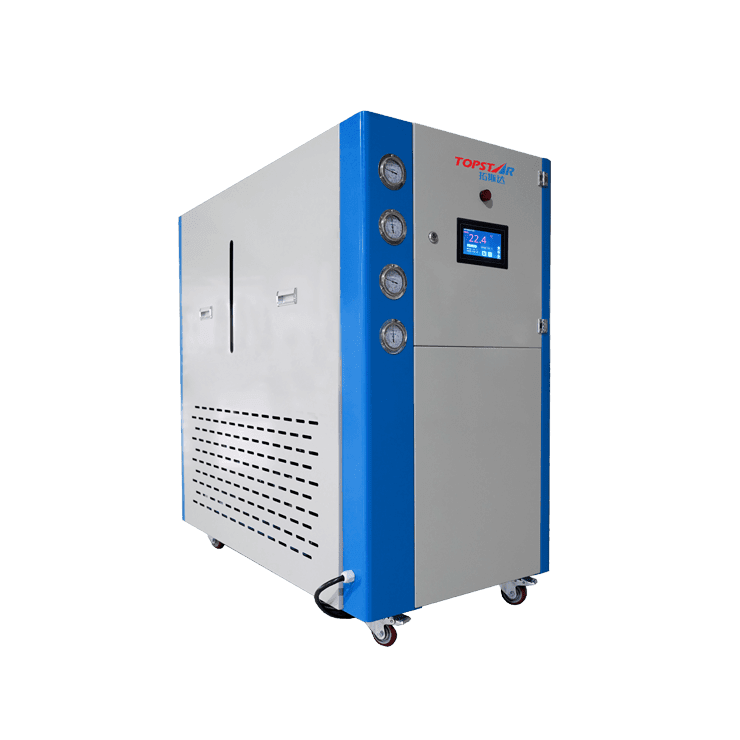
In injection molding, achieving stability is synonymous with precision, and one of the cores of this precision lies in the design of the cooling system. Today, we will talk about the cooling system alone and the direct impact of cooling system design on the stability of the entire injection molding process. Many plastics manufacturers recognize that their complexities extend beyond the circulation of cooling media. It involves a detailed understanding of material properties, part geometry, and the thermal dynamics in the injection molding process.
Direct impact of cooling system design on stability
Effective cooling system design is more than just a technical consideration; it directly affects the stability of injection molding. The layout of the cooling channels within the mold is crucial. Our thoughtful design ensures even cooling, minimizing variations in part quality. Engineers carefully plan these channels’ location, size, and configuration, laying the foundation for a stable and consistent injection molding process. In addition to channel geometries, their advancements involve integrating simulation tools that allow virtual prototyping. This sophisticated approach helps predict and optimize the thermal behavior of the mold, providing unprecedented control over the stability of the injection molding process.
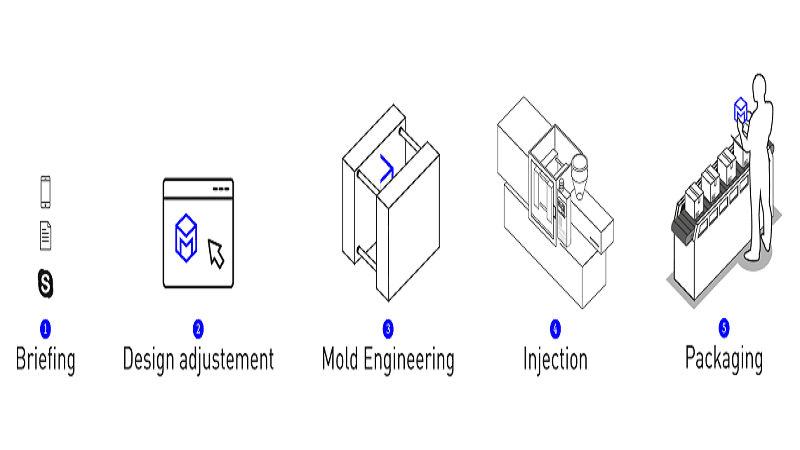
Cooling system efficiency
Their efficiency is an essential requirement for consistency. The system’s ability to evenly dissipate heat from the mold affects solidification speed, preventing warpage and ensuring consistent part dimensions. Innovations such as conformal cooling maximize efficiency, reduce cycle times, and contribute to the stability of the injection molding process. In addition, the integration of advanced cooling technology enables real-time monitoring of temperature changes. This level of precision ensures efficient heat dissipation and immediate corrective action, further reinforcing the role of the cooling system in maintaining stability.
Maintain equilibrium temperature
Balancing temperatures is tricky in injection molding, and cooling systems are vital to maintaining this balance. Changes in mold temperature can cause inconsistent material flow, shrinkage, and compromised part quality. A cooling system with a precise temperature control unit plays a vital role in stabilizing the injection molding process by ensuring the temperature is controlled and uniform throughout the mold. Integrating advanced temperature control units and sophisticated feedback mechanisms allows dynamic adjustments during molding. This real-time adaptability helps improve stability and adapts to the nuances of different materials, ensuring optimal performance in various molding applications.
Optimize cycle time
Cycle time optimization is not just a matter of speed but is closely related to the cooling system’s efficiency. Faster, more even heat dissipation means shorter cycle times, resulting in increased productivity. Manufacturers can balance speed and stability in the injection molding process by analyzing the direct impact of cooling system design on cycle times. Advanced cooling system design incorporates predictive modeling to determine optimal cycle times for specific molds and materials. This data-driven approach minimizes trial and error, promoting a more efficient and stable production process.
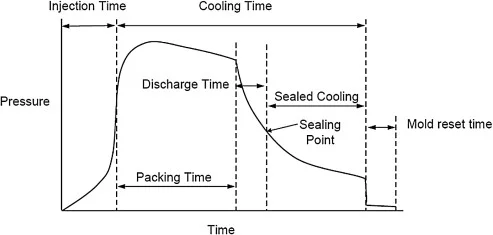
Mitigating part defects
They are the frontline defense against part defects that could destabilize the injection molding process. Effective cooling ensures controlled and uniform solidification, helping to reduce imperfections such as warpages and sink marks. Analyzing the direct impact of cooling system design on defect prevention reveals strategies to improve part quality and overall process stability. In-depth materials analysis is the cornerstone of this strategy, understanding how different materials respond to cooling and designing systems that accommodate these nuances. Case studies of defect mitigation through custom cooling solutions provide valuable insights for manufacturers aiming to optimize stability.
Make good use of your cooling system
Cooling systems are a strategic asset for manufacturers aiming for stability, minimal defects, and optimal efficiency in their injection molding processes. Looking at cooling systems from this perspective allows for continuous improvement and innovation. This commitment to advanced cooling system design ensures a stable and efficient production process that maintains the highest quality and precision standards in injection molding.
TRENDING POSTS
- What factors can cause delays in the injection molding process of plastic molding machine? 2023/11/15
- Exhibition Review| Topstar participates in InterPlas Thailand 2024 2023/11/15
- Star Case | Topstar helps Santong upgrade its intelligent plant 2023/11/15
- Topstar Special | National Science and Technology Workers Day 2023/11/15
HOT TOPIC
- .ervo motor-driven linear robots
- 1.0 guangdong topstar technology co. ltd
- 1.0 topstar china
- 1.0 topstar robot
- 11
- 2
- 21
- 23
- 3 axis robot
- 3 axis robots
- 3 in 1 Compact Dehumidifying Dryer
- 3-axis robot
- 3-axis robots
- 39
- 41
- 5-axis CNC machine
- 62
- accuracy
- Air Chillers
- all electric injection molding machine
- all electric injection molding machines
- All-electric injection molding machines
- and overall production quality. Therefore
- AP-RubberPlas
- automated injection molding machine
- Automation changed engineering
- automation of injection molding robots
- auxiliary machine
- Bench Injection Molding Machine
- Cabinet dryer manufacturers
- Cabinet dryers
- chiller
- CNC Drilling Machine
- CNC Drilling Machines
- cnc engraving machine manufacturer
- cnc laser cutting machine manufacturer
- CNC machine
- CNC Machine Center
- CNC Machine for Sale
- CNC Machine Manufacturing
- CNC Machine Tool
- CNC machine tool product
- CNC Machining Center
- CNC wood carving machine
- Cooling system
- Cross-Walking Single Axis Servo Cylinder Robot
- Cross-Walking Single-Axis Servo Cylinder Robot
- Cross-Walking Three-Axis/Five-Axis Servo Driven Robot
- cross-walking three-axis/five-axis servo-driven robot
- Dehumidifier Dryer
- Dehumidifying Dryer
- delta parallel robot
- Desktop Injection Molding Machine
- Desktop injection molding machines
- Desktop Molding Machine
- desktop plastic injection machine
- Desktop Plastic Injection Molding Machine
- direct clamp injection molding machine
- Direct clamp injection molding machines
- Dosing & mixing system
- Drilling Centers
- Drying and dehumidification system
- drying and dehumidifying equipment
- Drying and Dehumidifying System
- drying system
- effective and efficient. Cabinet dryers are also used in other industries where large quantities of material need to be dried
- efficient injection molding machine
- elbow hydraulic injection molding machines
- electric injection molding machine
- electric injection molding machines
- energy-efficient injection molding robot
- energy-saving injection molding machine
- etc. Among injection molding robots
- exhibition
- features of CNC machine
- Feeding And Conveying System
- Five Axis Machine Center
- Fully automatic injection molding machine
- Gathering Topstar
- giant injection molding machine
- GMU-600 5-Axis Machining Center
- Granulating & Recycling System
- Heavy duty injection molding machine
- High-precision electric molding machines
- high-precision plastic molding machines
- high-speed all electric injection molding machine
- Honeycomb rotor dehumidifier
- horizontal injection molding machine
- Horizontal Injection Molding Machines
- Horizontal Injection Moulding Machine
- Horizontal Mixer manufacturer
- How The CNC Machine Works
- hybrid injection molding machine
- hydraulic injection molding machine
- Hydraulic Injection Molding Machines
- in this article
- Industrial robot
- Industrial Robot Chinese brand
- industrial robot parts
- industrial robot supplier
- Industrial robots
- Industry Chain
- Injection Manipulator
- injection manipulator robot
- injection mold machines
- Injection molding
- Injection molding automation
- Injection Molding Automation Solution
- injection molding dryer
- Injection molding equipment
- injection molding hopper dryer
- Injection molding machine
- injection molding machine brand
- Injection Molding Machine Factory
- Injection Molding Machine Manufacture
- Injection molding machine manufacturer
- injection molding machine manufacturers
- Injection molding machine procurement
- injection molding machine robotic arm
- injection molding machine with a robot
- Injection molding machines
- injection molding material dehumidifying
- injection molding plant
- Injection Molding Robot
- injection molding robot arm
- Injection molding robot automation
- Injection molding robotic arm
- injection molding robots
- Injection moulding machine
- injection moulding machines
- Injection Moulding Robots
- Injection Robot
- Injection robot arm
- Injection robot manufacturer
- Injection robot wholesale
- injection robots
- intelligent injection molding machines
- Introducing Injection Robot
- It is the best choice for drying large quantities of material at once. Cabinetmakers use these machines because they are fast
- large injection molding machine
- large injection molding machines
- Learn what industrial automation and robotics is
- linear robot
- linear robots
- low speed sound-proof granulator
- machine plastic molding
- make sure to add some! Improvements (2) Keyphrase in introduction: Your keyphrase or its synonyms appear in the first paragraph of the copy
- manipulator machine
- manufacturing
- medical grade injection molding machines
- medical injection molding machine
- medical injection molding machines
- micro injection molding machine
- middle speed granulator
- Mini CNC machine manufacturers.
- Mold Temperature Control System
- mold temperature controller
- mold temperature controllers
- molding material Dehumidifying System
- mould temperature control system
- mould temperature controller
- mould temperature controllers
- New electric injection molding machine
- nitrogen dryer manufacturer
- nitrogen dryer system manufacturer
- Oil type mold temperature controller
- Oil type mold temperature controllers
- open day
- Outbound links: No outbound links appear in this page. Add some! Images: No images appear on this page. Add some! Internal links: No internal links appear in this page
- PET Preform injection molding
- phone case maker machine
- phone case making machine
- plastic bottle making machine
- plastic bottle manufacturing
- plastic bucket making machine
- plastic bucket manufacturing
- Plastic chair making machine
- plastic forming equipment
- plastic hopper dryer
- plastic injection machine
- plastic injection machines
- plastic injection molding
- Plastic injection molding equipment
- Plastic injection molding machine
- Plastic Injection Molding Machines
- plastic injection moulding machine
- plastic injection moulding machines
- plastic injection robot
- Plastic Molding machine
- Plastic Molding Machines
- plastic molding press
- plastic moulding machine
- plastic phone case making machine
- plastic-molding machine
- powerful granulator
- Powerful Type Sound-Proof Granulator
- precision injection molding
- precision injection molding machines
- production of plastic seats
- pure water mould temperature controller
- Robot injection molding
- robot injection molding machine
- robot manufacturing companies
- Robotic arm for injection molding machine
- robotic injection molding machines
- robotics in injection molding
- SCARA robot
- SCARA robots
- Service-oriented manufacturing
- Servo Cylinder Robot
- servo driven robot
- Servo Driven Robots
- servo injection robots
- servo motor-driven linear robots
- servo-driven 3-axis robot
- Servo-Driven Robot
- Setup of injection machine
- Silicone Injection Molding Machine
- six-axis industrial robot
- Stainless Hopper Dryer
- Stainless Hopper Dryers
- star club
- swing arm robot
- take-out robots
- the choice between servo-driven robots and hydraulic robots will have a certain impact on efficiency
- the most popular injection molding machine
- the type of injection molding robot
- toggle clamp injection molding machine
- Toggle Hydraulic Injection Molding Machines
- toggle injection molding machine
- Top 10 brands of injection robots
- Topstar
- Topstar Engineering
- Topstar Industrial Robots
- Topstar injection molding intelligent
- Topstar Scara Robots
- Useful Injection molding machine
- Vertical machining centers
- volumetric type blender
- water chiller
- water chillers
- water distributor
- water type mold temperature controller
- Water Type MoldTemperature Controller
- Water-Type Mould Temperature Controllers
- We often face choices when performing injection molding. We will choose the type of injection molding machine
- wholesale of injection molding machines
- x carve CNC
- 热门查询 点击次数 展示 排名 topstar