Troubleshooting Material Hang-Ups in Feeding and Conveying System
2023/11/13 By Topstar
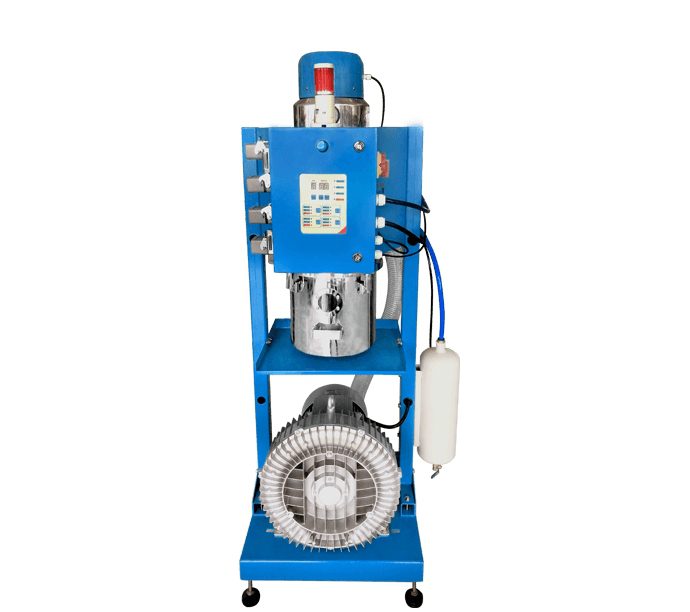
In complex injection molding processes, the smooth operation of feed and conveyor systems ensures a seamless production process. However, material hang-ups can impact gears, causing delays, increased downtime, and potential defects in the final product. Below, we look closely at common challenges associated with material hang-ups and explore effective troubleshooting strategies to keep your Feeding and Conveying System running like well-oiled machines.
Understand material issues in Feeding and Conveying System
Material stagnation occurs when obstructions or blockages in the feeding and conveying system disrupt the continuous flow of material. These disruptions can stem from various factors, such as irregular material shapes, inconsistent dimensions, and environmental conditions. The first step is to recognize the root causes and effectively address them. A thorough analysis of the system’s component and material properties is also essential for a targeted troubleshooting approach.
Troubleshooting begins with understanding the complexities of material behavior within the system. How the material interacts with various components such as hoppers, chutes, and conveyor belts is critical. Environmental factors such as temperature and humidity are essential in diagnosing and preventing potential hangs. This expanded understanding helps solve problems and provides the basis for taking proactive steps to avoid future disruptions.
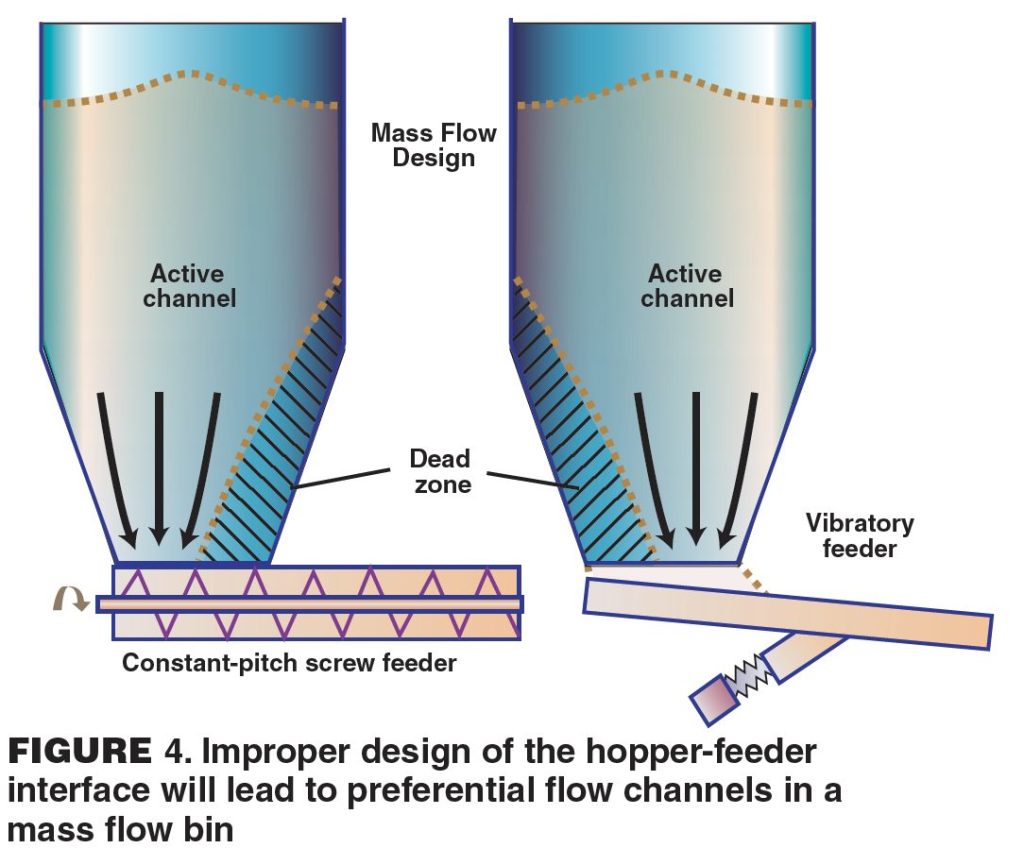
Identify common causes of material hang-ups
The common reasons behind these outages must be identified to resolve material issues successfully. Improper system design, incorrect hopper angles, or improper conveyor belt tension often cause irregular material flow. Factors such as moisture content, material degradation, and foreign particles can also cause hangups. Systematically examining each potential cause, you can tailor your troubleshooting strategy to address the issues plaguing your feed and conveyor systems.
An in-depth analysis of the design of feed and conveyor systems shows that considerations of material properties and adaptability play an essential role in preventing hang-ups. Additionally, exploring the advanced tensioning mechanisms of conveyor belts and the impact of material degradation on system functionality enhances the reader’s understanding.
Optimize feeding and conveying system design
Prevention is the best prerequisite, and the same is true for material blockage in feeding and conveying systems. From selecting the right hopper design to ensuring the right chute angle, optimizing system design is a proactive measure that can pay dividends in terms of efficiency and reliability.
The hopper is a crucial component to prevent materials from hanging up. Customized hopper design based on your material characteristics. Consider factors such as funnel angle, outlet size, and wall friction to ensure consistent material flow without the risk of blockages or irregularities. Materials with different particle sizes or densities may cause segregation during transportation. Optimize system design to minimize material separation. This may involve incorporating features such as anti-separation chutes to ensure that all components receive an even distribution of material. These optimization efforts are about feeding and conveying systems that allow companies to adapt to changing material needs.
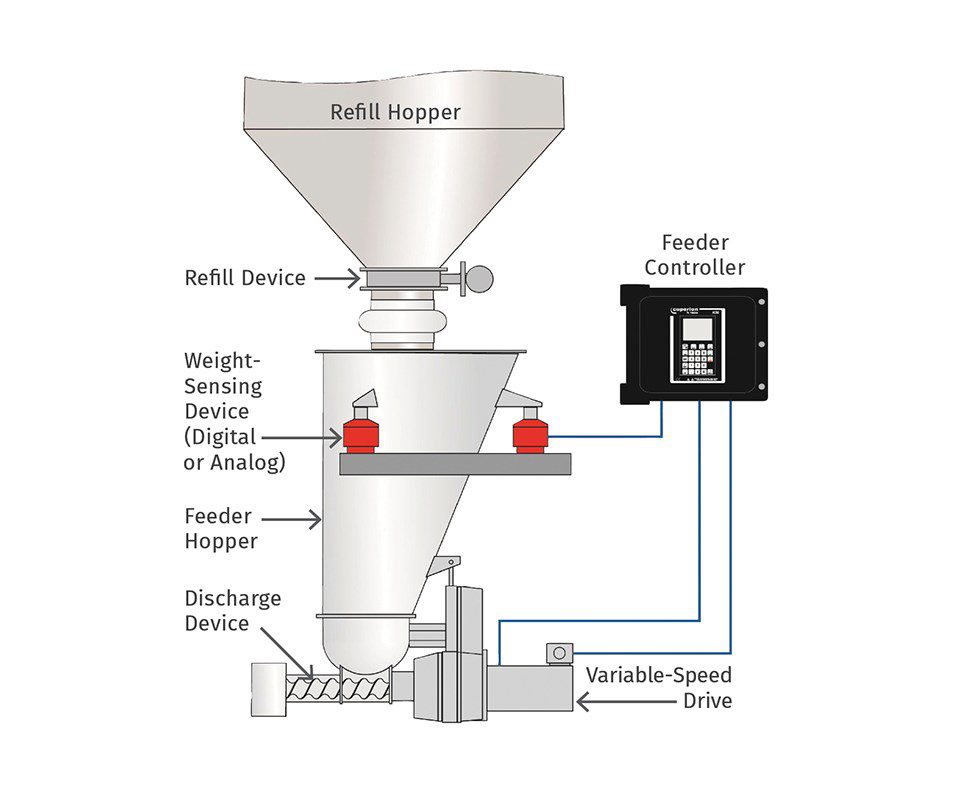
Implement a regular maintenance protocol for system health
Just as regular inspections are critical to maintaining good health, routine maintenance is essential to the longevity and optimal performance of your feeding and conveying systems. This includes checking components for wear, removing accumulated residue, and lubricating moving parts. Having a proactive maintenance plan will not only prevent material stagnation but also extend the life of your equipment, thereby reducing overall operating costs. We add a layer of complexity to maintenance protocols by exploring the integration of condition-monitoring systems and using predictive analytics to foresee potential issues.
Leverage advanced technology for real-time monitoring
In the age of Industry 4.0, integrating advanced technologies into your feed and conveyor systems can provide real-time insights and proactive solutions. Intelligent sensors, IoT devices, and data analytics can comprehensively view system performance. By detecting potential issues before they escalate, you can take corrective action quickly, minimize downtime, and maintain consistent material flow.
Efficient production through effective troubleshooting
In summary, troubleshooting material problems in feeding and conveying systems is a multifaceted task that requires a holistic approach and patience. By investing time and resources in resolving material issues, you ensure the efficiency of your system and contribute to the overall success and quality of your injection molding operation. Remember, well-maintained and optimized feeding and conveying systems are the backbone of a thriving production environment. We at Topstar always provide you with good services and products
TRENDING POSTS
- What factors can cause delays in the injection molding process of plastic molding machine? 2023/11/13
- Exhibition Review| Topstar participates in InterPlas Thailand 2024 2023/11/13
- Star Case | Topstar helps Santong upgrade its intelligent plant 2023/11/13
- Topstar Special | National Science and Technology Workers Day 2023/11/13
HOT TOPIC
- .ervo motor-driven linear robots
- 1.0 guangdong topstar technology co. ltd
- 1.0 topstar china
- 1.0 topstar robot
- 11
- 2
- 21
- 23
- 3 axis robot
- 3 axis robots
- 3 in 1 Compact Dehumidifying Dryer
- 3-axis robot
- 3-axis robots
- 39
- 41
- 5-axis CNC machine
- 62
- accuracy
- Air Chillers
- all electric injection molding machine
- all electric injection molding machines
- All-electric injection molding machines
- and overall production quality. Therefore
- AP-RubberPlas
- automated injection molding machine
- Automation changed engineering
- automation of injection molding robots
- auxiliary machine
- Bench Injection Molding Machine
- Cabinet dryer manufacturers
- Cabinet dryers
- chiller
- CNC Drilling Machine
- CNC Drilling Machines
- cnc engraving machine manufacturer
- cnc laser cutting machine manufacturer
- CNC machine
- CNC Machine Center
- CNC Machine for Sale
- CNC Machine Manufacturing
- CNC Machine Tool
- CNC machine tool product
- CNC Machining Center
- CNC wood carving machine
- Cooling system
- Cross-Walking Single Axis Servo Cylinder Robot
- Cross-Walking Single-Axis Servo Cylinder Robot
- Cross-Walking Three-Axis/Five-Axis Servo Driven Robot
- cross-walking three-axis/five-axis servo-driven robot
- Dehumidifier Dryer
- Dehumidifying Dryer
- delta parallel robot
- Desktop Injection Molding Machine
- Desktop injection molding machines
- Desktop Molding Machine
- desktop plastic injection machine
- Desktop Plastic Injection Molding Machine
- direct clamp injection molding machine
- Direct clamp injection molding machines
- Dosing & mixing system
- Drilling Centers
- Drying and dehumidification system
- drying and dehumidifying equipment
- Drying and Dehumidifying System
- drying system
- effective and efficient. Cabinet dryers are also used in other industries where large quantities of material need to be dried
- efficient injection molding machine
- elbow hydraulic injection molding machines
- electric injection molding machine
- electric injection molding machines
- energy-efficient injection molding robot
- energy-saving injection molding machine
- etc. Among injection molding robots
- exhibition
- features of CNC machine
- Feeding And Conveying System
- Five Axis Machine Center
- Fully automatic injection molding machine
- Gathering Topstar
- giant injection molding machine
- GMU-600 5-Axis Machining Center
- Granulating & Recycling System
- Heavy duty injection molding machine
- High-precision electric molding machines
- high-precision plastic molding machines
- high-speed all electric injection molding machine
- Honeycomb rotor dehumidifier
- horizontal injection molding machine
- Horizontal Injection Molding Machines
- Horizontal Injection Moulding Machine
- Horizontal Mixer manufacturer
- How The CNC Machine Works
- hybrid injection molding machine
- hydraulic injection molding machine
- Hydraulic Injection Molding Machines
- in this article
- Industrial robot
- Industrial Robot Chinese brand
- industrial robot parts
- industrial robot supplier
- Industrial robots
- Industry Chain
- Injection Manipulator
- injection manipulator robot
- injection mold machines
- Injection molding
- Injection molding automation
- Injection Molding Automation Solution
- injection molding dryer
- Injection molding equipment
- injection molding hopper dryer
- Injection molding machine
- injection molding machine brand
- Injection Molding Machine Factory
- Injection Molding Machine Manufacture
- Injection molding machine manufacturer
- injection molding machine manufacturers
- Injection molding machine procurement
- injection molding machine robotic arm
- injection molding machine with a robot
- Injection molding machines
- injection molding material dehumidifying
- injection molding plant
- Injection Molding Robot
- injection molding robot arm
- Injection molding robot automation
- Injection molding robotic arm
- injection molding robots
- Injection moulding machine
- injection moulding machines
- Injection Moulding Robots
- Injection Robot
- Injection robot arm
- Injection robot manufacturer
- Injection robot wholesale
- injection robots
- intelligent injection molding machines
- Introducing Injection Robot
- It is the best choice for drying large quantities of material at once. Cabinetmakers use these machines because they are fast
- large injection molding machine
- large injection molding machines
- Learn what industrial automation and robotics is
- linear robot
- linear robots
- low speed sound-proof granulator
- machine plastic molding
- make sure to add some! Improvements (2) Keyphrase in introduction: Your keyphrase or its synonyms appear in the first paragraph of the copy
- manipulator machine
- manufacturing
- medical grade injection molding machines
- medical injection molding machine
- medical injection molding machines
- micro injection molding machine
- middle speed granulator
- Mini CNC machine manufacturers.
- Mold Temperature Control System
- mold temperature controller
- mold temperature controllers
- molding material Dehumidifying System
- mould temperature control system
- mould temperature controller
- mould temperature controllers
- New electric injection molding machine
- nitrogen dryer manufacturer
- nitrogen dryer system manufacturer
- Oil type mold temperature controller
- Oil type mold temperature controllers
- open day
- Outbound links: No outbound links appear in this page. Add some! Images: No images appear on this page. Add some! Internal links: No internal links appear in this page
- PET Preform injection molding
- phone case maker machine
- phone case making machine
- plastic bottle making machine
- plastic bottle manufacturing
- plastic bucket making machine
- plastic bucket manufacturing
- Plastic chair making machine
- plastic forming equipment
- plastic hopper dryer
- plastic injection machine
- plastic injection machines
- plastic injection molding
- Plastic injection molding equipment
- Plastic injection molding machine
- Plastic Injection Molding Machines
- plastic injection moulding machine
- plastic injection moulding machines
- plastic injection robot
- Plastic Molding machine
- Plastic Molding Machines
- plastic molding press
- plastic moulding machine
- plastic phone case making machine
- plastic-molding machine
- powerful granulator
- Powerful Type Sound-Proof Granulator
- precision injection molding
- precision injection molding machines
- production of plastic seats
- pure water mould temperature controller
- Robot injection molding
- robot injection molding machine
- robot manufacturing companies
- Robotic arm for injection molding machine
- robotic injection molding machines
- robotics in injection molding
- SCARA robot
- SCARA robots
- Service-oriented manufacturing
- Servo Cylinder Robot
- servo driven robot
- Servo Driven Robots
- servo injection robots
- servo motor-driven linear robots
- servo-driven 3-axis robot
- Servo-Driven Robot
- Setup of injection machine
- Silicone Injection Molding Machine
- six-axis industrial robot
- Stainless Hopper Dryer
- Stainless Hopper Dryers
- star club
- swing arm robot
- take-out robots
- the choice between servo-driven robots and hydraulic robots will have a certain impact on efficiency
- the most popular injection molding machine
- the type of injection molding robot
- toggle clamp injection molding machine
- Toggle Hydraulic Injection Molding Machines
- toggle injection molding machine
- Top 10 brands of injection robots
- Topstar
- Topstar Engineering
- Topstar Industrial Robots
- Topstar injection molding intelligent
- Topstar Scara Robots
- Useful Injection molding machine
- Vertical machining centers
- volumetric type blender
- water chiller
- water chillers
- water distributor
- water type mold temperature controller
- Water Type MoldTemperature Controller
- Water-Type Mould Temperature Controllers
- We often face choices when performing injection molding. We will choose the type of injection molding machine
- wholesale of injection molding machines
- x carve CNC
- 热门查询 点击次数 展示 排名 topstar