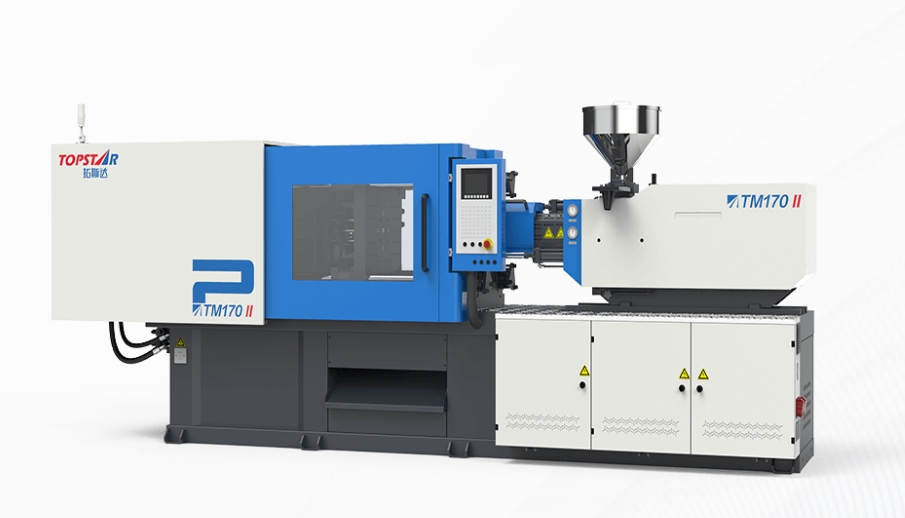
A suitable injection molding machine can ensure the manufacturing business’s success and production efficiency. There are various choices in the market. Choosing an injection molding machine is a critical and essential task. In this blog post, we will share with you what you need to pay attention to and what factors to consider when choosing an injection molding machine to help you make an informed decision that meets your production needs and budget requirements.
Determine your injection molding manufacturing needs
First, you must understand your production needs before choosing, considering factors such as part size, geometry, material properties, and throughput requirements. This will help you determine your injection molding machine’s required clamping force and shot volume capacity to meet your production needs effectively. Usually, the clamping force of the injection molding machine is about 90T-2200T, which needs to be determined according to the products you produce. Next, their material compatibility and processing capabilities are evaluated. The type of thermoplastic or thermoset material required to ensure the machine can process the part must also consider factors such as melt temperature, viscosity, and flow characteristics.
Understand the types of injection molding machines
Injection molding machines are mainly divided into three types. Different types work according to specific production requirements and process changes.
Hydraulic injection molding machine:
Hydraulic molding machines use a hydraulic system to generate the clamping force and injection pressure required for the molding process. They are known for their ruggedness, reliability, and ability to handle high clamping force applications. Hydraulic presses can precisely control injection speed and pressure, making them suitable for various thermoplastic and thermoset materials. It is the most common type, represented by Topstar’s TS Series Toggle Hydraulic Injection Molding Machine.
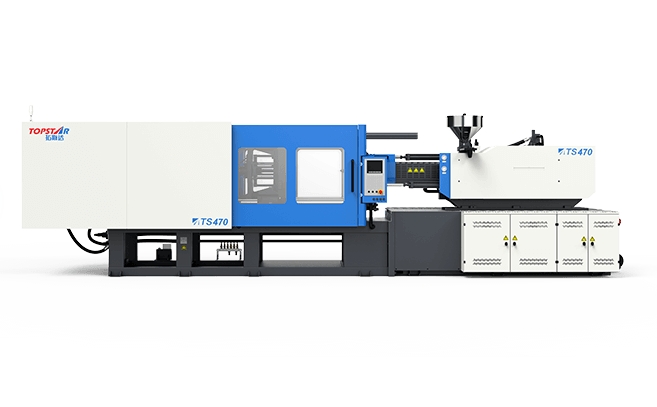
Electric injection molding machine:
Electric injection molding machines use electric servo motors to drive the movement of injection devices, mold clamping mechanisms, and other machine functions. They offer higher accuracy, repeatability, and energy efficiency than hydraulic presses. In addition, the motor is also the first choice for clean room environments and applications requiring high-speed, high-precision molding, such as the medical and food industries. Among Topstar, the TE series electric injection molding machine is representative.
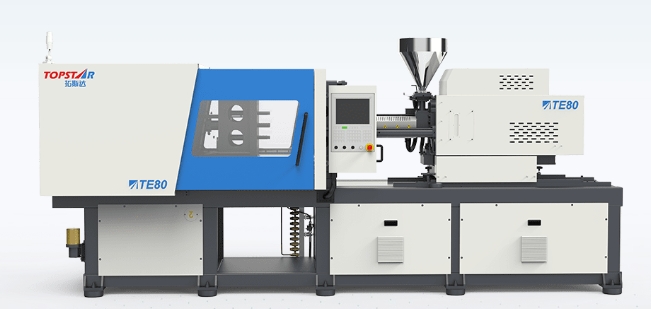
Hybrid injection molding machine:
Hybrid machines combine hydraulic and electric drive systems by taking advantage of the advantages of both technologies. This enables them to use electric servo motors for injection and clamping movements, while hydraulic systems provide auxiliary functions such as ejection operation and core pulling. Hybrid machines improve energy efficiency, shorten cycle times, and reduce noise levels compared to purely hydraulic machines. For example, Topstar’s TEII Series All Electric Injection Molding Machine.
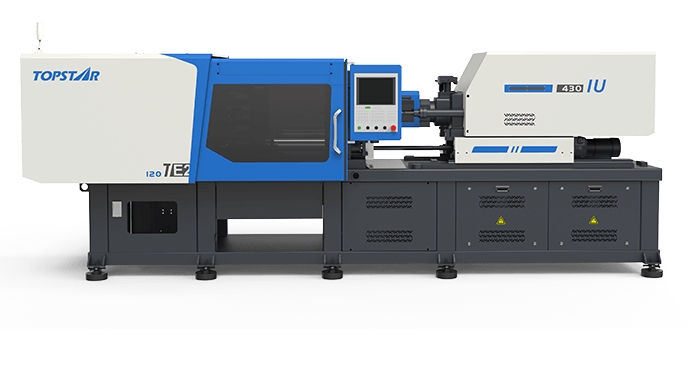
Calculate the clamping force of the injection molding machine
The clamping force ensures that the machine keeps the mold fully closed during the injection and cooling phases of the molding process. The size and complexity of the molded part directly affect the required clamping force. More significant parts with greater surface area require higher clamping troops to withstand the pressure exerted by the injected material and prevent mold deflection or flash formation. Likewise, parts with complex geometries, thin walls, or complex features may require higher clamping forces to maintain mold integrity and dimensional accuracy. Such clamping force is generally around 2200T.
The type and characteristics of the molding material also affect the required clamping force, with materials with higher viscosity or stiffness requiring more force to fill the mold cavity and achieve uniform part quality. Additionally, some materials may exert high internal pressures or stresses during molding, requiring higher clamping forces to counteract these forces and prevent mold from deforming or cracking. Injection pressure and injection rate also affect the force exerted on the mold walls and, thus, the required clamping force. We can determine if they have sufficient clamping force capability using empirical formulas or software simulations to calculate the force needed for a specific application.

Consider automation and integration options for your injection molding machine
When choosing, you should also consider the automation and integration options of the injection molding machine. Most of the current injection molding machines can meet the needs of injection molding integration. Integrating them with injection molding robots and auxiliary equipment can achieve automated part handling, reducing manual labor and increasing production efficiency. Automated conveyor systems optimize workflow efficiency, reduce material handling errors, and promote continuous production processes. Injection molding machines with integrated vision systems, sensors, and measurement equipment can monitor key process parameters, detect defects, and verify part dimensions, surface finish, and material properties. Enable real-time feedback and process adjustments to improve product consistency and customer satisfaction.
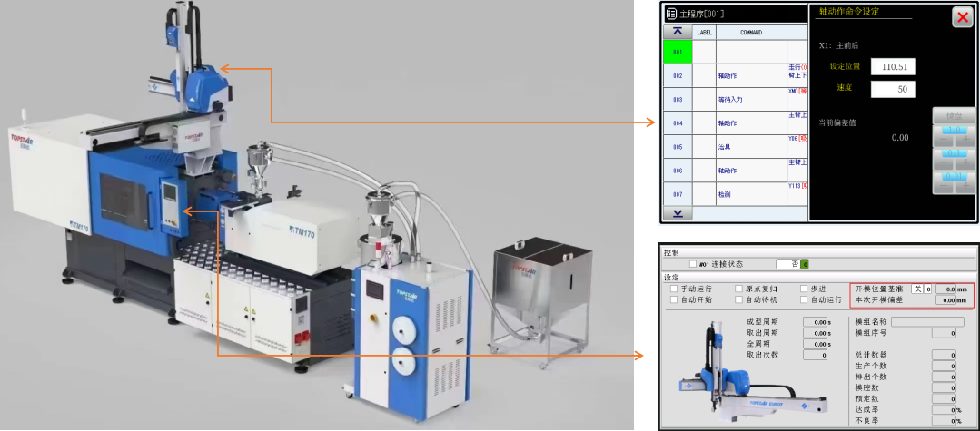
Choose the right manufacturer
In addition to the product itself, we should consider the manufacturer, evaluate the range of models and configurations offered, and look for manufacturers that provide various machine options suitable for different production requirements, part sizes, and materials. Topstar can give machines different clamping forces and injection molding conditions as a top manufacturer. At the same time, it can also provide your factory with integrated injection molding solutions to create your automated factory. Regarding after-sales, we can also offer a dedicated customer support team and technical personnel to assist with installation, maintenance, troubleshooting, and optimization.
Choose the suitable machine for you
Choosing the suitable injection molding machine requires careful consideration of various factors, including manufacturing requirements, machine specifications, performance and automation and integration options, and manufacturer services. By evaluating these factors and conducting in-depth screening, you can select a machine that meets your production needs and increases efficiency and productivity. If you want to know more about product specifications, you can visit our official website.
TRENDING POSTS
- What factors can cause delays in the injection molding process of plastic molding machine? 2024/03/15
- Exhibition Review| Topstar participates in InterPlas Thailand 2024 2024/03/15
- Star Case | Topstar helps Santong upgrade its intelligent plant 2024/03/15
- Topstar Special | National Science and Technology Workers Day 2024/03/15
HOT TOPIC
- .ervo motor-driven linear robots
- 3 axis robot
- 3 axis robots
- 3 in 1 Compact Dehumidifying Dryer
- 3-axis robot
- 3-axis robots
- 5-axis CNC machine
- accuracy
- Air Chillers
- all electric injection molding machine
- all electric injection molding machines
- All-electric injection molding machines
- and overall production quality. Therefore
- AP-RubberPlas
- automated injection molding machine
- Automation changed engineering
- automation of injection molding robots
- auxiliary machine
- Bench Injection Molding Machine
- Cabinet dryer manufacturers
- Cabinet dryers
- chiller
- CNC Drilling Machine
- CNC Drilling Machines
- cnc engraving machine manufacturer
- cnc laser cutting machine manufacturer
- CNC machine
- CNC Machine Center
- CNC Machine for Sale
- CNC Machine Manufacturing
- CNC Machine Tool
- CNC machine tool product
- CNC Machining Center
- CNC wood carving machine
- Cooling system
- Cross-Walking Single Axis Servo Cylinder Robot
- Cross-Walking Single-Axis Servo Cylinder Robot
- Cross-Walking Three-Axis/Five-Axis Servo Driven Robot
- cross-walking three-axis/five-axis servo-driven robot
- Dehumidifier Dryer
- Dehumidifying Dryer
- delta parallel robot
- Desktop Injection Molding Machine
- Desktop injection molding machines
- Desktop Molding Machine
- desktop plastic injection machine
- Desktop Plastic Injection Molding Machine
- direct clamp injection molding machine
- Direct clamp injection molding machines
- Dosing & mixing system
- Drilling Centers
- Drying and dehumidification system
- drying and dehumidifying equipment
- Drying and Dehumidifying System
- drying system
- effective and efficient. Cabinet dryers are also used in other industries where large quantities of material need to be dried
- efficient injection molding machine
- elbow hydraulic injection molding machines
- electric injection molding machine
- electric injection molding machines
- energy-efficient injection molding robot
- energy-saving injection molding machine
- etc. Among injection molding robots
- exhibition
- features of CNC machine
- Feeding And Conveying System
- Five Axis Machine Center
- Fully automatic injection molding machine
- Gathering Topstar
- giant injection molding machine
- GMU-600 5-Axis Machining Center
- Granulating & Recycling System
- Heavy duty injection molding machine
- High-precision electric molding machines
- high-precision plastic molding machines
- high-speed all electric injection molding machine
- Honeycomb rotor dehumidifier
- horizontal injection molding machine
- Horizontal Injection Molding Machines
- Horizontal Injection Moulding Machine
- Horizontal Mixer manufacturer
- How The CNC Machine Works
- hybrid injection molding machine
- hydraulic injection molding machine
- Hydraulic Injection Molding Machines
- in this article
- Industrial robot
- Industrial Robot Chinese brand
- industrial robot parts
- industrial robot supplier
- Industrial robots
- Industry Chain
- Injection Manipulator
- injection manipulator robot
- injection mold machines
- Injection molding
- Injection molding automation
- Injection Molding Automation Solution
- injection molding dryer
- Injection molding equipment
- injection molding hopper dryer
- Injection molding machine
- injection molding machine brand
- Injection Molding Machine Factory
- Injection Molding Machine Manufacture
- Injection molding machine manufacturer
- injection molding machine manufacturers
- Injection molding machine procurement
- injection molding machine robotic arm
- injection molding machine with a robot
- Injection molding machines
- injection molding material dehumidifying
- injection molding plant
- Injection Molding Robot
- injection molding robot arm
- Injection molding robot automation
- Injection molding robotic arm
- injection molding robots
- Injection moulding machine
- Injection Moulding Robots
- Injection Robot
- Injection robot arm
- Injection robot manufacturer
- Injection robot wholesale
- injection robots
- intelligent injection molding machines
- Introducing Injection Robot
- It is the best choice for drying large quantities of material at once. Cabinetmakers use these machines because they are fast
- large injection molding machine
- large injection molding machines
- Learn what industrial automation and robotics is
- linear robot
- linear robots
- low speed sound-proof granulator
- machine plastic molding
- make sure to add some! Improvements (2) Keyphrase in introduction: Your keyphrase or its synonyms appear in the first paragraph of the copy
- manipulator machine
- manufacturing
- medical grade injection molding machines
- medical injection molding machine
- medical injection molding machines
- micro injection molding machine
- middle speed granulator
- Mini CNC machine manufacturers.
- Mold Temperature Control System
- mold temperature controller
- mold temperature controllers
- molding material Dehumidifying System
- mould temperature control system
- mould temperature controller
- mould temperature controllers
- New electric injection molding machine
- nitrogen dryer manufacturer
- nitrogen dryer system manufacturer
- Oil type mold temperature controller
- Oil type mold temperature controllers
- open day
- Outbound links: No outbound links appear in this page. Add some! Images: No images appear on this page. Add some! Internal links: No internal links appear in this page
- PET Preform injection molding
- phone case maker machine
- phone case making machine
- plastic bottle making machine
- plastic bottle manufacturing
- plastic bucket making machine
- plastic bucket manufacturing
- Plastic chair making machine
- plastic forming equipment
- plastic hopper dryer
- plastic injection machine
- plastic injection machines
- plastic injection molding
- Plastic injection molding equipment
- Plastic injection molding machine
- Plastic Injection Molding Machines
- plastic injection moulding machine
- plastic injection robot
- Plastic Molding machine
- Plastic Molding Machines
- plastic molding press
- plastic moulding machine
- plastic phone case making machine
- plastic-molding machine
- powerful granulator
- Powerful Type Sound-Proof Granulator
- precision injection molding
- precision injection molding machines
- production of plastic seats
- pure water mould temperature controller
- Robot injection molding
- robot injection molding machine
- robot manufacturing companies
- Robotic arm for injection molding machine
- robotic injection molding machines
- robotics in injection molding
- SCARA robot
- SCARA robots
- Service-oriented manufacturing
- Servo Cylinder Robot
- servo driven robot
- Servo Driven Robots
- servo injection robots
- servo motor-driven linear robots
- servo-driven 3-axis robot
- Servo-Driven Robot
- Setup of injection machine
- Silicone Injection Molding Machine
- six-axis industrial robot
- Stainless Hopper Dryer
- Stainless Hopper Dryers
- star club
- swing arm robot
- take-out robots
- the choice between servo-driven robots and hydraulic robots will have a certain impact on efficiency
- the most popular injection molding machine
- the type of injection molding robot
- toggle clamp injection molding machine
- Toggle Hydraulic Injection Molding Machines
- toggle injection molding machine
- Top 10 brands of injection robots
- Topstar
- Topstar Engineering
- Topstar Industrial Robots
- Topstar injection molding intelligent
- Topstar Scara Robots
- Useful Injection molding machine
- Vertical machining centers
- volumetric type blender
- water chiller
- water chillers
- water distributor
- water type mold temperature controller
- Water Type MoldTemperature Controller
- Water-Type Mould Temperature Controllers
- We often face choices when performing injection molding. We will choose the type of injection molding machine
- wholesale of injection molding machines
- x carve CNC