How to choose the mold temperature controller correctly?
2024/03/16 By Topstar
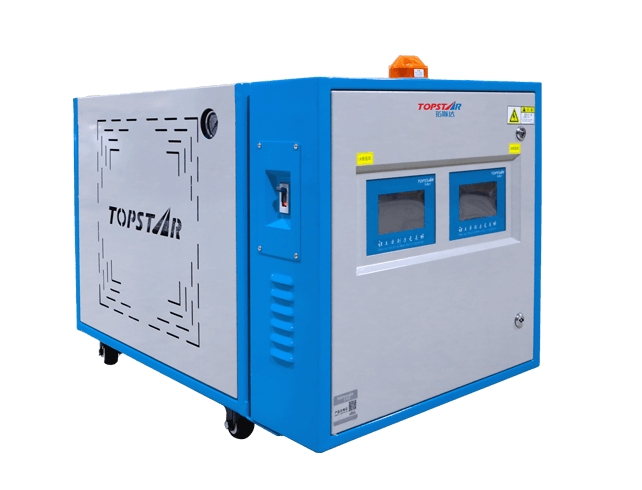
A mold temperature controller is a kind of auxiliary equipment and plays a vital role in the injection molding process. Choosing a suitable temperature controller can significantly improve production efficiency, shorten cycle times, and achieve product quality. In this comprehensive guide, we’ll explore the key factors to consider when purchasing a mold temperature controller.
Understand your application needs for mold temperature controllers
First, the type of molding material significantly affects temperature control requirements. Different materials have specific temperature requirements for proper flow, solidification, and final product quality. Therefore, knowing the precise temperature required to process the material before selecting it is essential. Second, the size and complexity of the mold play a key role in determining the capacity and capabilities required of the temperature controller. Large molds or molds with complex designs may require a more powerful temperature control system with higher heating and cooling capabilities to ensure uniform temperature distribution throughout the mold cavity.
Types of mold temperature controllers
The water-type mold temperature controller uses water as the heat transfer medium to achieve heat exchange by direct (low-temperature type) or indirect cooling (high-temperature type). It regulates the temperature of plastic-forming molds and extrusion-forming rollers. It controls the temperatures of the molds and rollers with high precision through heating and cooling devices. Water-based mold temperature controllers are generally more cost-effective and environmentally friendly than oil-based systems. They have rapid heating and cooling functions and are suitable for plastic processing industries, PVC sheet extrusion, etc. Topstar’s water-type mold temperature controller electrical control box is isolated from the fuselage, has a good heat insulation effect, and has a long service life. It is equipped with a dedicated touchscreen controller, which makes temperature control more reasonable and allows the power saving rate to reach more than 35%.
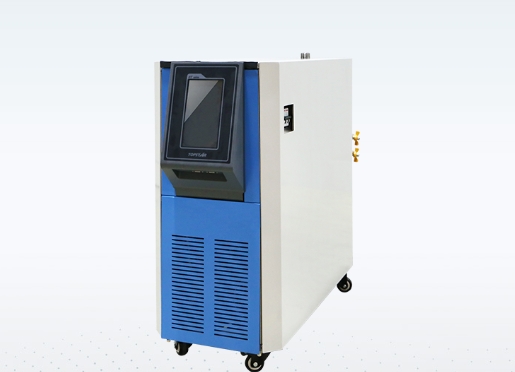
The oil-type mold temperature controller uses oil as the heat transfer medium to achieve heat exchange through indirect cooling. These controllers circulate oil through the mold’s cooling channels to control temperature. Oil-based systems are famous for their high precision and stability in temperature control. They use high-pressure, large-flow water pumps, which can provide significant flow rates to small parts of the mold water channels and control the mold temperature evenly. Topstar’s oil-type mold temperature controllers adopt a unique heating design, which is suitable for use in different temperature control places and has apparent energy-saving effects. At the same time, they have automatic exhaust functions and air-blowing and oil return functions.
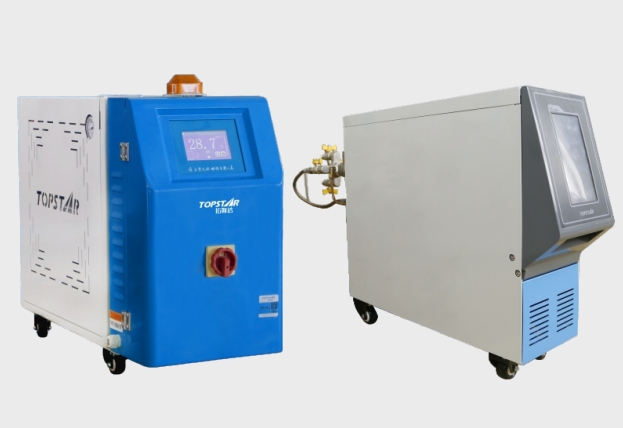
Consider size and compatibility
The temperature controller must be sized to match the molding operation’s scale and the mold being used. If you use larger molds or produce high volumes, you need a temperature controller with excellent heating and cooling capabilities. Conversely, smaller molds or low-volume production may require a more compact temperature controller.
The physical size of the temperature controller should be compatible with the available space in your facility and the layout of your production line. Maintenance access, ventilation clearances, and distance from other equipment must be considered to optimize installation and operation. When selecting, compatibility with existing injection molding equipment and infrastructure is critical. Ensuring the controller is compatible with the types of molds, injection molding machines, and ancillary equipment used in your facility also includes communication protocols, control interfaces, and software integration for seamless operation and data exchange.
Temperature Controller Advanced Features and Functions
Modern mold temperature controllers often have advanced features and functions to increase performance and productivity, such as precision temperature control, advanced temperature controllers to provide precise temperature regulation with minimal deviation from the set point, sophisticated algorithms, and sensor technology to maintain temperatures within tight tolerances and ensure consistent product quality and process repeatability. A dedicated touchscreen controller for the mold temperature controller allows operators to monitor process parameters, adjust settings, and diagnose problems from a centralized location.
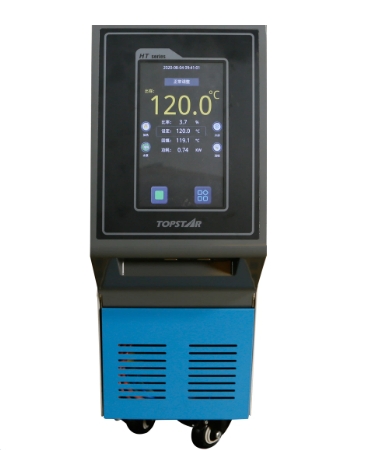
Evaluate manufacturer’s after-sales support
When purchasing a mold temperature controller, you must also determine whether the manufacturer has warranty coverage and after-sales support services. A comprehensive warranty protects against defects and malfunctions, while responsive after-sales support ensures timely problem resolution and technical assistance when needed. Another is to determine the availability of the manufacturer’s service and maintenance options to ensure they can provide timely help when needed.
Ultimately
When purchasing a mold temperature controller, we carefully evaluate your application needs and consider temperature control accuracy and different types to select the best machine. If you want to learn more about them, please visit our official website.
TRENDING POSTS
- What factors can cause delays in the injection molding process of plastic molding machine? 2024/03/16
- Exhibition Review| Topstar participates in InterPlas Thailand 2024 2024/03/16
- Star Case | Topstar helps Santong upgrade its intelligent plant 2024/03/16
- Topstar Special | National Science and Technology Workers Day 2024/03/16
HOT TOPIC
- .ervo motor-driven linear robots
- 3 axis robot
- 3 axis robots
- 3 in 1 Compact Dehumidifying Dryer
- 3-axis robot
- 3-axis robots
- 5-axis CNC machine
- accuracy
- Air Chillers
- all electric injection molding machine
- all electric injection molding machines
- All-electric injection molding machines
- and overall production quality. Therefore
- AP-RubberPlas
- automated injection molding machine
- Automation changed engineering
- automation of injection molding robots
- auxiliary machine
- Bench Injection Molding Machine
- Cabinet dryer manufacturers
- Cabinet dryers
- chiller
- CNC Drilling Machine
- CNC Drilling Machines
- cnc engraving machine manufacturer
- cnc laser cutting machine manufacturer
- CNC machine
- CNC Machine Center
- CNC Machine for Sale
- CNC Machine Manufacturing
- CNC Machine Tool
- CNC machine tool product
- CNC Machining Center
- CNC wood carving machine
- Cooling system
- Cross-Walking Single Axis Servo Cylinder Robot
- Cross-Walking Single-Axis Servo Cylinder Robot
- Cross-Walking Three-Axis/Five-Axis Servo Driven Robot
- cross-walking three-axis/five-axis servo-driven robot
- Dehumidifier Dryer
- Dehumidifying Dryer
- delta parallel robot
- Desktop Injection Molding Machine
- Desktop injection molding machines
- Desktop Molding Machine
- desktop plastic injection machine
- Desktop Plastic Injection Molding Machine
- direct clamp injection molding machine
- Direct clamp injection molding machines
- Dosing & mixing system
- Drilling Centers
- Drying and dehumidification system
- drying and dehumidifying equipment
- Drying and Dehumidifying System
- drying system
- effective and efficient. Cabinet dryers are also used in other industries where large quantities of material need to be dried
- efficient injection molding machine
- elbow hydraulic injection molding machines
- electric injection molding machine
- electric injection molding machines
- energy-efficient injection molding robot
- energy-saving injection molding machine
- etc. Among injection molding robots
- exhibition
- features of CNC machine
- Feeding And Conveying System
- Five Axis Machine Center
- Fully automatic injection molding machine
- Gathering Topstar
- giant injection molding machine
- GMU-600 5-Axis Machining Center
- Granulating & Recycling System
- Heavy duty injection molding machine
- High-precision electric molding machines
- high-precision plastic molding machines
- high-speed all electric injection molding machine
- Honeycomb rotor dehumidifier
- horizontal injection molding machine
- Horizontal Injection Molding Machines
- Horizontal Injection Moulding Machine
- Horizontal Mixer manufacturer
- How The CNC Machine Works
- hybrid injection molding machine
- hydraulic injection molding machine
- Hydraulic Injection Molding Machines
- in this article
- Industrial robot
- Industrial Robot Chinese brand
- industrial robot parts
- industrial robot supplier
- Industrial robots
- Industry Chain
- Injection Manipulator
- injection manipulator robot
- injection mold machines
- Injection molding
- Injection molding automation
- Injection Molding Automation Solution
- injection molding dryer
- Injection molding equipment
- injection molding hopper dryer
- Injection molding machine
- injection molding machine brand
- Injection Molding Machine Factory
- Injection Molding Machine Manufacture
- Injection molding machine manufacturer
- injection molding machine manufacturers
- Injection molding machine procurement
- injection molding machine robotic arm
- injection molding machine with a robot
- Injection molding machines
- injection molding material dehumidifying
- injection molding plant
- Injection Molding Robot
- injection molding robot arm
- Injection molding robot automation
- Injection molding robotic arm
- injection molding robots
- Injection moulding machine
- Injection Moulding Robots
- Injection Robot
- Injection robot arm
- Injection robot manufacturer
- Injection robot wholesale
- injection robots
- intelligent injection molding machines
- Introducing Injection Robot
- It is the best choice for drying large quantities of material at once. Cabinetmakers use these machines because they are fast
- large injection molding machine
- large injection molding machines
- Learn what industrial automation and robotics is
- linear robot
- linear robots
- low speed sound-proof granulator
- machine plastic molding
- make sure to add some! Improvements (2) Keyphrase in introduction: Your keyphrase or its synonyms appear in the first paragraph of the copy
- manipulator machine
- manufacturing
- medical grade injection molding machines
- medical injection molding machine
- medical injection molding machines
- micro injection molding machine
- middle speed granulator
- Mini CNC machine manufacturers.
- Mold Temperature Control System
- mold temperature controller
- mold temperature controllers
- molding material Dehumidifying System
- mould temperature control system
- mould temperature controller
- mould temperature controllers
- New electric injection molding machine
- nitrogen dryer manufacturer
- nitrogen dryer system manufacturer
- Oil type mold temperature controller
- Oil type mold temperature controllers
- open day
- Outbound links: No outbound links appear in this page. Add some! Images: No images appear on this page. Add some! Internal links: No internal links appear in this page
- PET Preform injection molding
- phone case maker machine
- phone case making machine
- plastic bottle making machine
- plastic bottle manufacturing
- plastic bucket making machine
- plastic bucket manufacturing
- Plastic chair making machine
- plastic forming equipment
- plastic hopper dryer
- plastic injection machine
- plastic injection machines
- plastic injection molding
- Plastic injection molding equipment
- Plastic injection molding machine
- Plastic Injection Molding Machines
- plastic injection moulding machine
- plastic injection robot
- Plastic Molding machine
- Plastic Molding Machines
- plastic molding press
- plastic moulding machine
- plastic phone case making machine
- plastic-molding machine
- powerful granulator
- Powerful Type Sound-Proof Granulator
- precision injection molding
- precision injection molding machines
- production of plastic seats
- pure water mould temperature controller
- Robot injection molding
- robot injection molding machine
- robot manufacturing companies
- Robotic arm for injection molding machine
- robotic injection molding machines
- robotics in injection molding
- SCARA robot
- SCARA robots
- Service-oriented manufacturing
- Servo Cylinder Robot
- servo driven robot
- Servo Driven Robots
- servo injection robots
- servo motor-driven linear robots
- servo-driven 3-axis robot
- Servo-Driven Robot
- Setup of injection machine
- Silicone Injection Molding Machine
- six-axis industrial robot
- Stainless Hopper Dryer
- Stainless Hopper Dryers
- star club
- swing arm robot
- take-out robots
- the choice between servo-driven robots and hydraulic robots will have a certain impact on efficiency
- the most popular injection molding machine
- the type of injection molding robot
- toggle clamp injection molding machine
- Toggle Hydraulic Injection Molding Machines
- toggle injection molding machine
- Top 10 brands of injection robots
- Topstar
- Topstar Engineering
- Topstar Industrial Robots
- Topstar injection molding intelligent
- Topstar Scara Robots
- Useful Injection molding machine
- Vertical machining centers
- volumetric type blender
- water chiller
- water chillers
- water distributor
- water type mold temperature controller
- Water Type MoldTemperature Controller
- Water-Type Mould Temperature Controllers
- We often face choices when performing injection molding. We will choose the type of injection molding machine
- wholesale of injection molding machines
- x carve CNC