How does an all electric injection molding machine address Short-Shot Defects in Medical bottle Caps?
- all electric injection molding machine
- all electric injection molding machines
- medical grade injection molding machines
- medical injection molding machines
2025/05/09 By Topstar
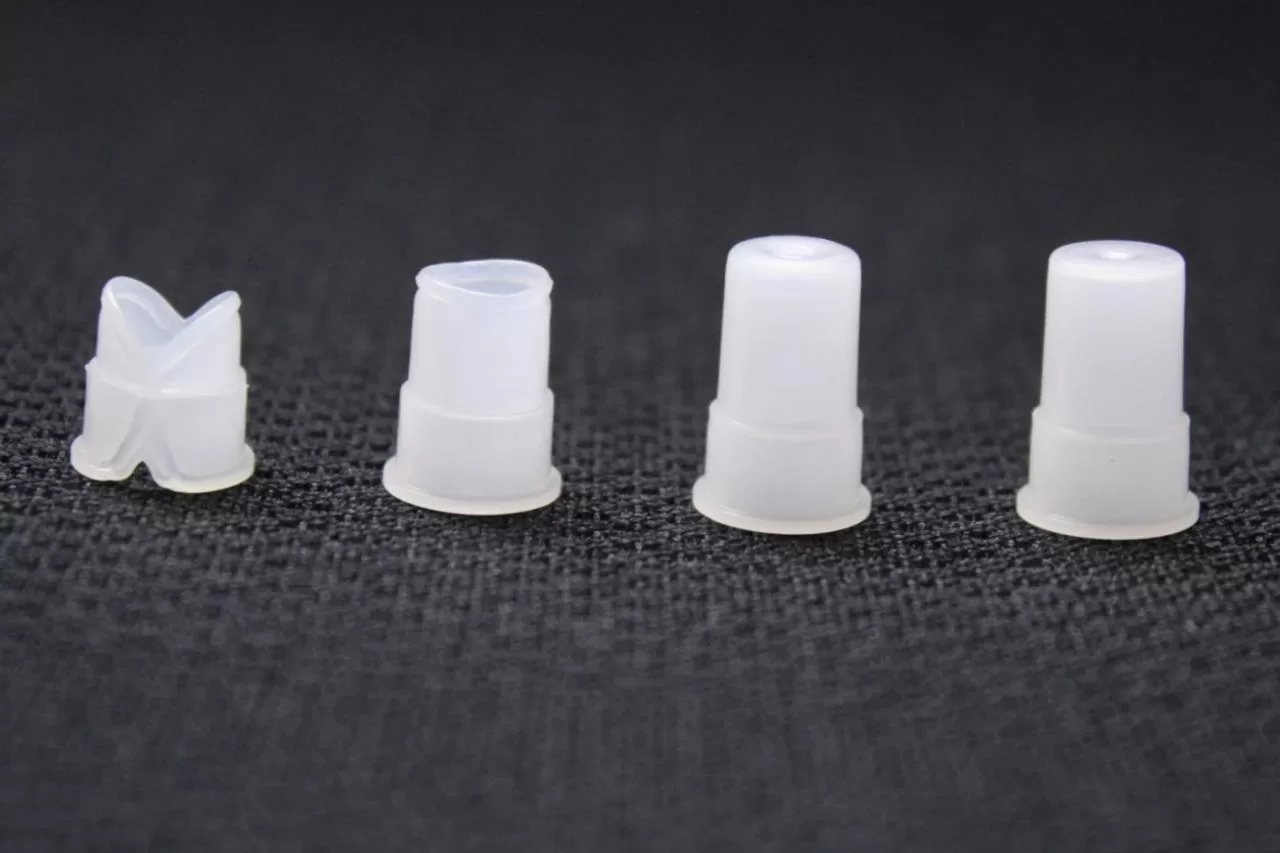
When using an electric injection molding machine to produce pharmaceutical bottle caps, a common quality problem is insufficient injection, where the molten polymer fails to fill the entire mold cavity, resulting in incomplete bottle caps, which affects the seal integrity and sterility. Inconsistent melt pressure, temperature fluctuations, or insufficient injection speed can cause insufficient injection. These defects are not allowed in medical applications because regulatory agencies like the FDA have strict dimensional tolerances and sealing requirements for medical products. To address this defect and the strict requirements of medical manufacturing, Topstar provides centrally controlled, precision-moulded medical grade injection molding machines to eliminate insufficient injection and ensure reliable, high-volume production of consistent medical bottle caps.
Stable control system of an electric injection molding machine
At the heart of Topstar’s all electric injection molding machines is a highly stable, self-developed control system that coordinates every stage of the molding cycle. Unlike traditional hydraulic injection molding machines, the electric platform provides precise timing and repeatable motion curves with millisecond accuracy. At the same time, proprietary control algorithms continuously monitor injection speed, screw position, and barrel temperature, automatically correcting deviations that may cause material shortages. Maintaining injection speed within ±0.5% and mould temperature within ±0.3°C prevents viscosity peaks and ensures smooth flow of molten resin into every detail of the cap mold. In addition, the control system provides real-time communication, compatibility, and data acquisition awareness to ensure compliance with production regulations for Class I and Class II medical parts, thereby enhancing traceability and quality assurance.
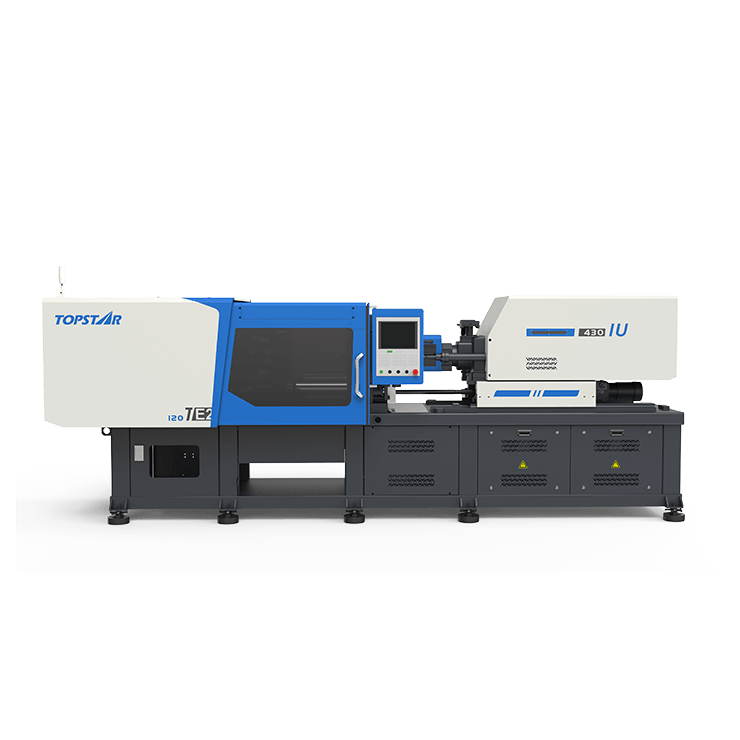
Low-damping injection seat for accurate metering
Achieving accurate shot volume To avoid underfilling, Topstar’s all electric injection molding machines use low-damping injection seats and electroplated screws. This configuration minimizes mechanical backlash and energy loss during the metering and injection stages. The low-damping seat ensures that the axial force applied to the screw is directly converted into positive plasticization and melt accumulation, keeping the weight difference of each shot within ±0.1%. For medical caps, which often require injection volumes of less than 5 grams for small-diameter caps, this metering accuracy ensures that each cap receives the exact required injection volume. In addition, this stability allows manufacturers to use a variety of medical-grade resins, including polypropylene and polyethylene, without constant recalibration or compromising part integrity.
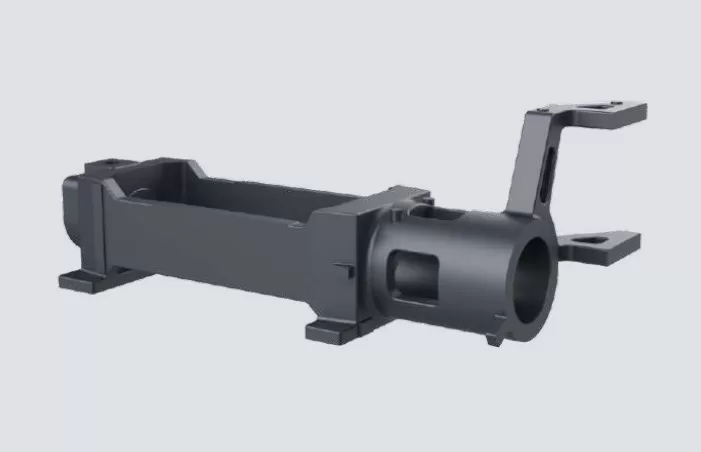
Discrete intelligent drive of all electric injection molding machine for stable pressure control
Filling complex bottle cap cavities under high shear conditions requires continuous stability of injection pressure. Discrete intelligent drive technology is integrated in medical-grade all electric injection molding machines, a servo drive architecture that decouples the control loop of each actuator. This enables the injection unit to maintain constant pressure for real-time adjustment, even if the load or material rheology changes suddenly. When injecting the narrow threads and undercut parts of medical bottle caps at high speed, the drive can adjust within microseconds to maintain peak pressure and ensure complete cavity filling. In addition, the intelligent drive system supports advanced diagnostic functions to help technicians monitor energy consumption, torque feedback, and injection curve stability, all of which can achieve a zero-defect manufacturing environment in the medical industry.
Precision molding of complex bottle cap geometries
Medical bottle caps often have tamper-proof bands, flip-top hinges, and internal sealing ribs, requiring precise mold filling. The all-electric injection molding machine provided by Topstar has high repeatability and position accuracy of up to ±0.01 mm, which can accurately replicate complex features. Each cap design recipe stores variable injection speed profiles to control the melt front speed and prevent premature freezing of thin-walled parts. The injection molding machine responds quickly and achieves full injection acceleration within 20 milliseconds, ensuring it fills complex cap molds before the polymer cools. In addition, this precision helps reduce material waste and shorten cycle times, thereby supporting the sustainability and cost-effectiveness of large-scale medical production lines. At the same time, electric injection molding machines can save at least 50% of electricity and up to 60% compared to hydraulic presses, with better energy-saving effects.
Centralized control of medical production lines
Large-scale production of medical caps requires close integration of medical injection molding machines with molding, conveying, inspection, and packaging. The Topstar all electric injection molding machine has a centralized control platform that can communicate seamlessly with auxiliary equipment such as dehumidification dryers, mold temperature controllers, and downstream automatic cap sorting machines. The central control system uses a single communication protocol to coordinate pre-drying cycles, injection plans, and online leak testing. If the system detects a lack of material in the cap, it automatically pauses the production line and adjusts the molding parameters in real time. In addition, the centralized interface enables the quality assurance team to generate real-time reports, conduct statistical process control, and track all production batches, fully complying with ISO 13485 and GMP requirements.
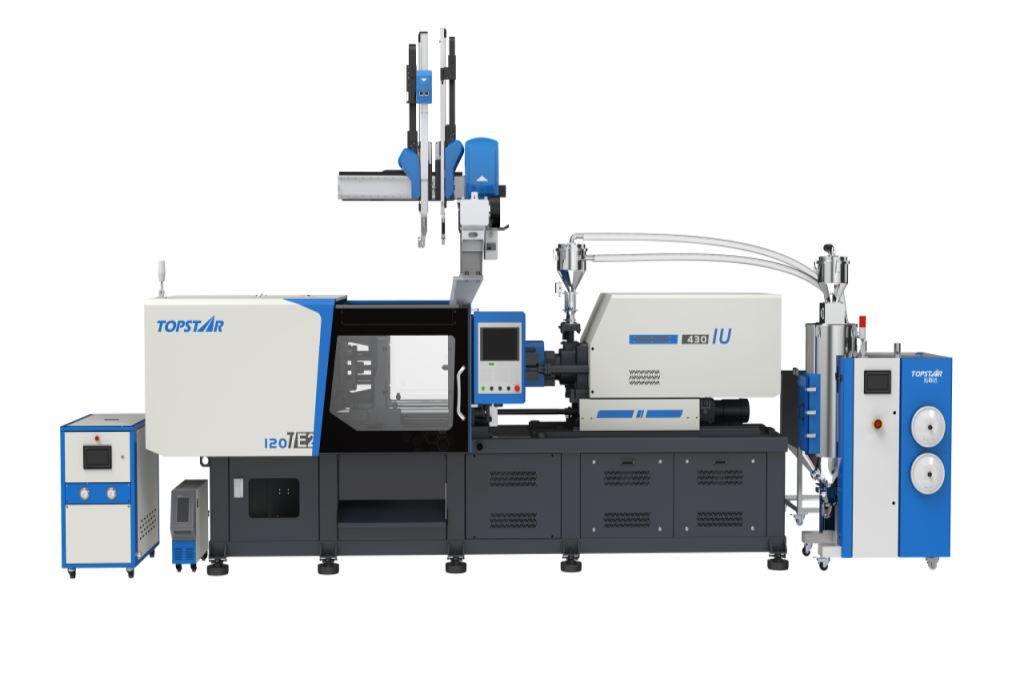
Bringing medical caps without production defects
With a stable control system, low-damping injection seat, discrete intelligent drive, centralized production management, and precision molding capabilities, Topstar’s all electric injection molding machine solves the problem of missing material defects in manufacturing medical bottle caps. It becomes a precise and stable medical injection molding machine. Precise and stable motion control, real-time monitoring, and seamless integration with a wider production system ensure the consistency of bottle cap quality.
TRENDING POSTS
- What factors can cause delays in the injection molding process of plastic molding machine? 2025/05/09
- Exhibition Review| Topstar participates in InterPlas Thailand 2024 2025/05/09
- Star Case | Topstar helps Santong upgrade its intelligent plant 2025/05/09
- Topstar Special | National Science and Technology Workers Day 2025/05/09
HOT TOPIC
- .ervo motor-driven linear robots
- 1.0 guangdong topstar technology co. ltd
- 1.0 topstar china
- 1.0 topstar robot
- 11
- 2
- 21
- 23
- 3 axis robot
- 3 axis robots
- 3 in 1 Compact Dehumidifying Dryer
- 3-axis robot
- 3-axis robots
- 39
- 41
- 5-axis CNC machine
- 62
- accuracy
- Air Chillers
- all electric injection molding machine
- all electric injection molding machines
- All-electric injection molding machines
- and overall production quality. Therefore
- AP-RubberPlas
- automated injection molding machine
- Automation changed engineering
- automation of injection molding robots
- auxiliary machine
- Bench Injection Molding Machine
- Cabinet dryer manufacturers
- Cabinet dryers
- chiller
- CNC Drilling Machine
- CNC Drilling Machines
- cnc engraving machine manufacturer
- cnc laser cutting machine manufacturer
- CNC machine
- CNC Machine Center
- CNC Machine for Sale
- CNC Machine Manufacturing
- CNC Machine Tool
- CNC machine tool product
- CNC Machining Center
- CNC wood carving machine
- Cooling system
- Cross-Walking Single Axis Servo Cylinder Robot
- Cross-Walking Single-Axis Servo Cylinder Robot
- Cross-Walking Three-Axis/Five-Axis Servo Driven Robot
- cross-walking three-axis/five-axis servo-driven robot
- Dehumidifier Dryer
- Dehumidifying Dryer
- delta parallel robot
- Desktop Injection Molding Machine
- Desktop injection molding machines
- Desktop Molding Machine
- desktop plastic injection machine
- Desktop Plastic Injection Molding Machine
- direct clamp injection molding machine
- Direct clamp injection molding machines
- Dosing & mixing system
- Drilling Centers
- Drying and dehumidification system
- drying and dehumidifying equipment
- Drying and Dehumidifying System
- drying system
- effective and efficient. Cabinet dryers are also used in other industries where large quantities of material need to be dried
- efficient injection molding machine
- elbow hydraulic injection molding machines
- electric injection molding machine
- electric injection molding machines
- energy-efficient injection molding robot
- energy-efficient water chiller
- energy-efficient water chillers
- energy-saving injection molding machine
- etc. Among injection molding robots
- exhibition
- features of CNC machine
- Feeding And Conveying System
- Five Axis Machine Center
- Fully automatic injection molding machine
- Gathering Topstar
- giant injection molding machine
- GMU-600 5-Axis Machining Center
- Granulating & Recycling System
- Heavy duty injection molding machine
- High-precision electric molding machines
- high-precision plastic molding machines
- high-speed all electric injection molding machine
- high-speed electric injection molding machine
- High-Speed Packaging Injection Molding
- Honeycomb rotor dehumidifier
- horizontal injection molding machine
- Horizontal Injection Molding Machines
- Horizontal Injection Moulding Machine
- Horizontal Mixer manufacturer
- How The CNC Machine Works
- hybrid injection molding machine
- hydraulic injection molding machine
- Hydraulic Injection Molding Machines
- in this article
- Industrial robot
- Industrial Robot Chinese brand
- industrial robot parts
- industrial robot supplier
- Industrial robots
- Industry Chain
- Injection Manipulator
- injection manipulator robot
- injection mold machines
- Injection molding
- Injection molding automation
- Injection Molding Automation Solution
- injection molding dryer
- Injection molding equipment
- injection molding hopper dryer
- Injection molding machine
- injection molding machine brand
- Injection Molding Machine Factory
- Injection Molding Machine Manufacture
- Injection molding machine manufacturer
- injection molding machine manufacturers
- Injection molding machine procurement
- injection molding machine robotic arm
- injection molding machine with a robot
- Injection molding machines
- injection molding material dehumidifying
- injection molding plant
- injection molding process
- Injection Molding Robot
- injection molding robot arm
- Injection molding robot automation
- Injection molding robotic arm
- injection molding robots
- Injection moulding machine
- injection moulding machines
- Injection Moulding Robots
- Injection Robot
- Injection robot arm
- Injection robot manufacturer
- Injection robot wholesale
- injection robots
- intelligent injection molding machines
- Intelligent mould temperature controller
- Introducing Injection Robot
- It is the best choice for drying large quantities of material at once. Cabinetmakers use these machines because they are fast
- Large flow water type mold temperature controller
- large injection molding machine
- large injection molding machines
- Learn what industrial automation and robotics is
- linear robot
- linear robots
- low speed sound-proof granulator
- machine plastic molding
- make sure to add some! Improvements (2) Keyphrase in introduction: Your keyphrase or its synonyms appear in the first paragraph of the copy
- manipulator machine
- manufacturing
- medical grade injection molding machines
- medical injection molding machine
- medical injection molding machines
- micro injection molding machine
- middle speed granulator
- Mini CNC machine manufacturers.
- Mold Temperature Control System
- mold temperature controller
- mold temperature controllers
- molding material Dehumidifying System
- mould temperature control system
- mould temperature controller
- mould temperature controllers
- New electric injection molding machine
- nitrogen dryer manufacturer
- nitrogen dryer system manufacturer
- Oil type mold temperature controller
- Oil type mold temperature controllers
- open day
- Outbound links: No outbound links appear in this page. Add some! Images: No images appear on this page. Add some! Internal links: No internal links appear in this page
- PET Preform injection molding
- phone case maker machine
- phone case making machine
- phone cover making machine
- plastic bottle making machine
- plastic bottle manufacturing
- plastic bucket making machine
- plastic bucket manufacturing
- Plastic chair making machine
- plastic forming equipment
- plastic hopper dryer
- plastic injection machine
- plastic injection machines
- plastic injection molding
- Plastic injection molding equipment
- Plastic injection molding machine
- Plastic Injection Molding Machines
- plastic injection moulding machine
- plastic injection moulding machines
- plastic injection robot
- plastic molding
- Plastic Molding machine
- Plastic Molding Machines
- plastic molding press
- plastic moulding machine
- plastic phone case making machine
- plastic-molding machine
- powerful granulator
- Powerful Type Sound-Proof Granulator
- precision injection molding
- precision injection molding machines
- production of plastic seats
- pure water mould temperature controller
- Robot injection molding
- robot injection molding machine
- robot manufacturing companies
- Robotic arm for injection molding machine
- robotic injection molding machines
- robotics in injection molding
- SCARA robot
- SCARA robots
- Service-oriented manufacturing
- Servo Cylinder Robot
- servo driven robot
- Servo Driven Robots
- servo injection molding machine
- servo injection robots
- servo motor-driven linear robots
- servo-driven 3-axis robot
- Servo-Driven Robot
- Setup of injection machine
- Silicone Injection Molding Machine
- six-axis industrial robot
- Stainless Hopper Dryer
- Stainless Hopper Dryers
- star club
- swing arm robot
- take-out robot
- take-out robots
- the choice between servo-driven robots and hydraulic robots will have a certain impact on efficiency
- the most popular injection molding machine
- the type of injection molding robot
- TMII injection molding machine
- toggle clamp injection molding machine
- Toggle Hydraulic Injection Molding Machines
- toggle injection molding machine
- Top 10 brands of injection robots
- Topstar
- Topstar Engineering
- Topstar Industrial Robots
- Topstar injection molding intelligent
- Topstar Scara Robots
- Useful Injection molding machine
- Vertical machining centers
- volumetric type blender
- water chiller
- water chillers
- water distributor
- water type mold temperature controller
- Water Type MoldTemperature Controller
- Water-Type Mould Temperature Controllers
- We often face choices when performing injection molding. We will choose the type of injection molding machine
- wholesale of injection molding machines
- x carve CNC
- 热门查询 点击次数 展示 排名 topstar