How to achieve micro-precision tolerances with precision injection molding machines?
2025/07/02 By Topstar
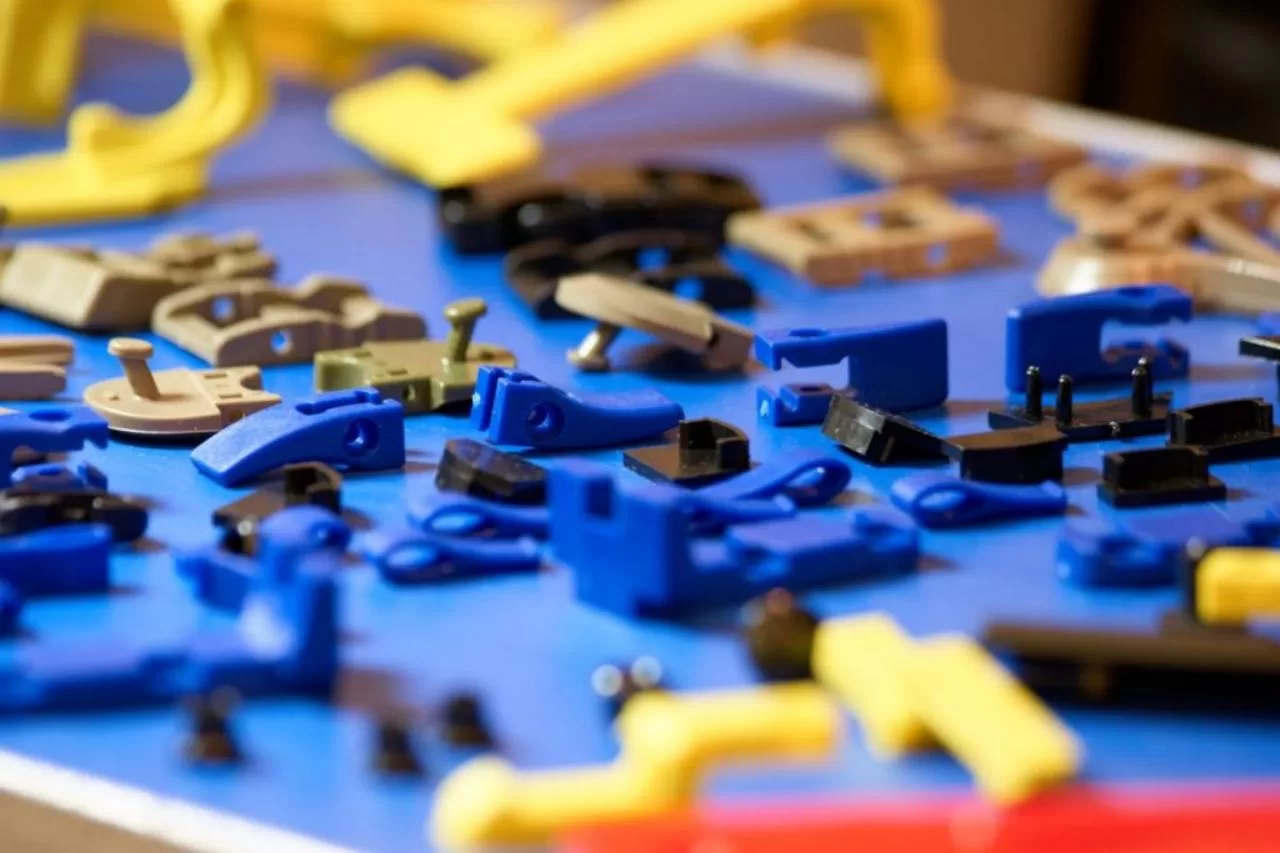
Precision injection molding machines are capable of producing parts with micro-tolerances. This micro-precision tolerance (usually ±0.01 mm or less) is crucial for the production of products such as medical devices, micro-optical devices, and precision connectors. Such precision injection molding machines utilise electric drives to achieve ultra-precision motion, employ low-damping injection units to provide sensitive pressure feedback, and design high-rigidity, low-friction mechanical structures, making them more suitable for precision molding. Servo motors replace hydraulic pumps in precision injection molding, providing consistent, programmable speed and pressure. At the same time, the role of linear guides and low-damping injection units in capturing subtle pressure changes enables high-precision pressure control, ensuring uniform filling and achieving more precise injection molding.
Using electric drives to drive precision injection molding machines
To achieve micro-precision tolerances, we first use electric drives on precision injection molding machines. Electric drive control can achieve position control accuracy within ±0.1 mm, eliminating fluctuations in hydraulic valve cores and making it an all electric injection molding machine. In addition, closed-loop feedback ensures the repeatability of screw positioning and clamp movement in each cycle. The servo drive receives molding process data and independently generates operating curves, enabling real-time servo motor control. This results in improved accuracy of position, speed, and pressure control, as well as smooth acceleration and precise switching. It ensures that there is no overshoot or fluctuation when filling the micro cavity. The transformation of the injection molding machine from hydraulic to intelligent electric drive reduces maintenance, improves energy efficiency by up to 30%, and lays a stable operating foundation for micro-precision molding on every all electric injection molding machine.
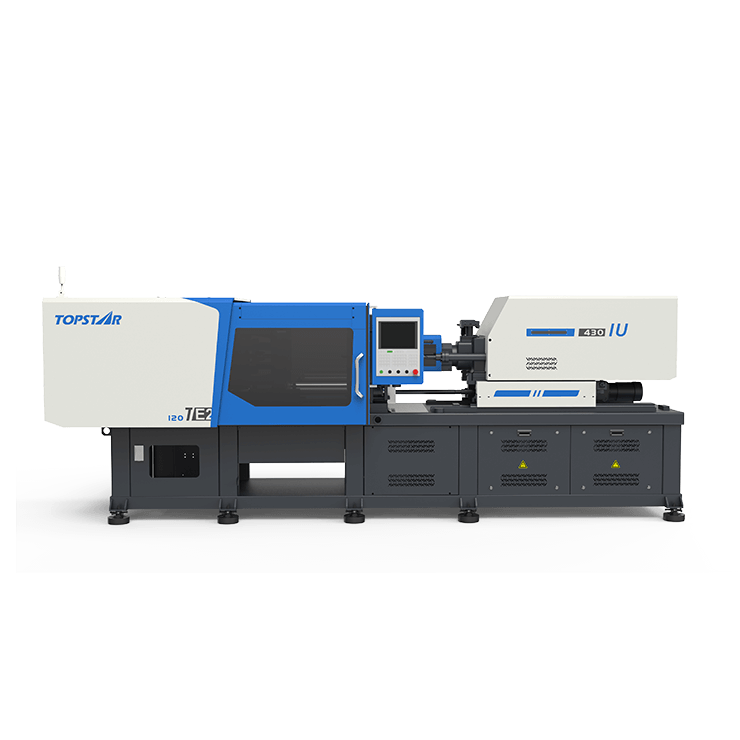
Low-damping injection unit and linear guide
To reduce pressure fluctuations in micro-precision molding, we utilise a combination of low-damping injection units and precision linear guides on these precision injection molding machines. First, we will assemble low-viscosity fluids and high-rigidity components into the injection unit to minimize energy losses. Then, technicians mount the screw and barrel assembly on a preloaded linear guide to maintain constant friction throughout the process. At the same time, I will calibrate the pressure sensor directly on the guide frame, allowing for the detection of pressure changes as low as 0.1 bar in real time. This sensitive feedback loop enables the electric servo controller to instantly adjust the injection curve, preventing flow-induced deviations and weld lines. Topstar’s all-electric injection moulding machines feature low-damping mechanical structures, high-precision linear guides, and fast feedback, ensuring dimensional stability and repeatable micro-tolerance performance over thousands of cycles.
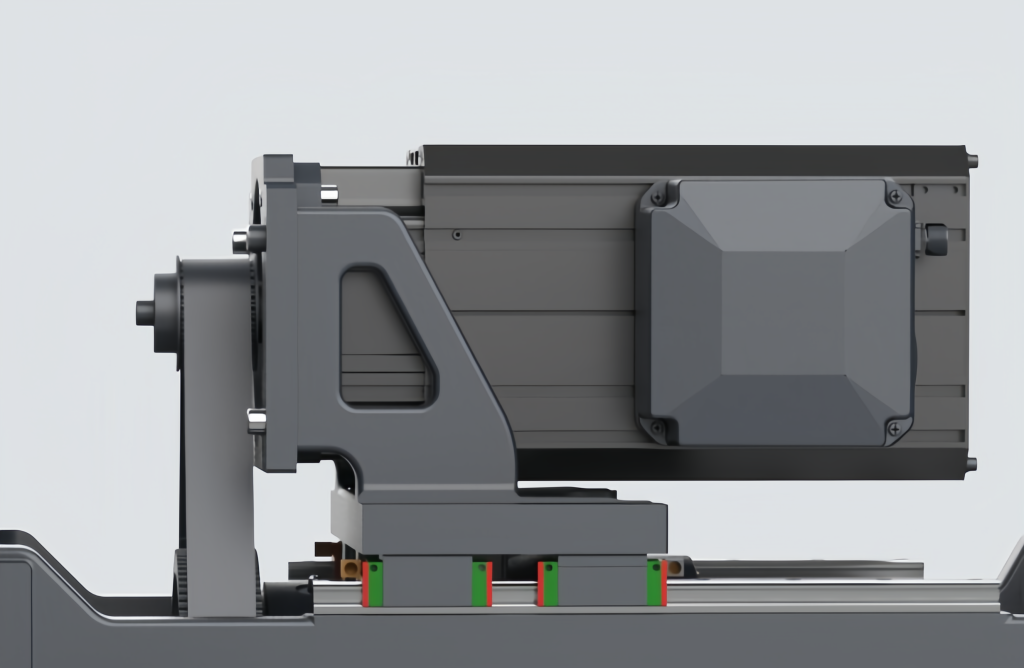
Precision injection molding machines with high-precision pressure control
Achieving micro-precision molding also demands a high-precision pressure control system on the injection molding machine, powered by electric servo valves and multi-zone pressure regulation technology. By dividing the injection pressure into programmable zones (filling, holding, and holding), you can fine-tune the melt flow to match the cavity geometry. As a result, over-holding is eliminated and stress gradients that cause dimensional warpage are reduced. At the same time, you can set the pressure control loop to achieve a control bandwidth sufficient to correct deviations within 5 milliseconds. Additionally, we have implemented a pressure overshoot prevention algorithm to ensure a smooth transition from filling to holding. This rapid correction capability ensures uniform cavity pressure, which can consistently translate into parts within micro-precision tolerances, even for the most complex mould designs.
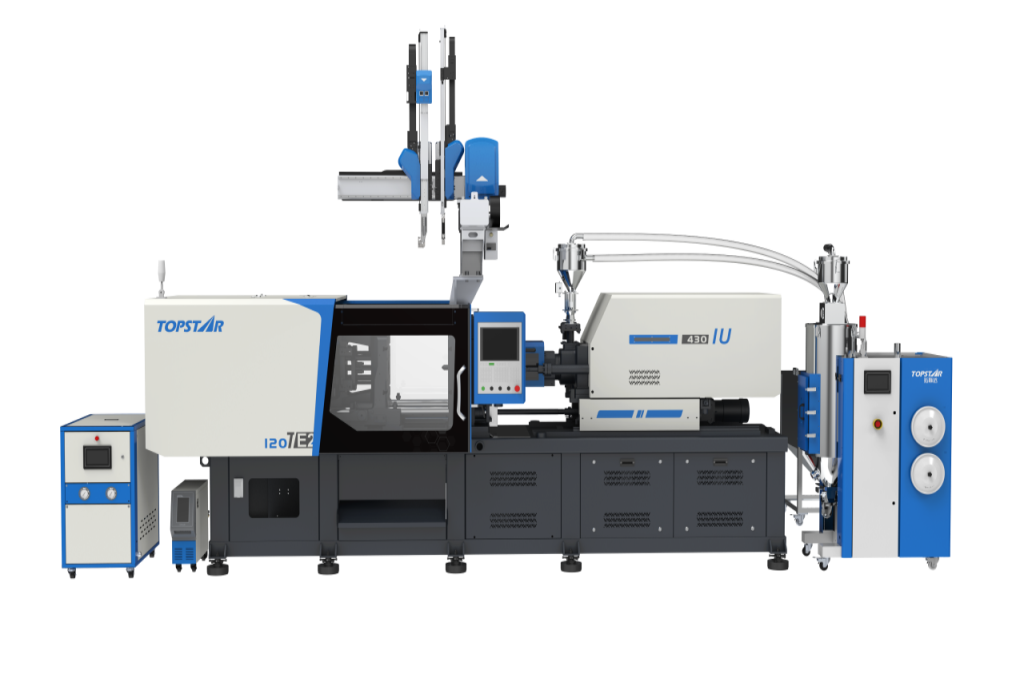
High rigidity and low-friction structural design
The mechanical structure of the injection molding machine also directly affects the dimensional accuracy of the product during production. We used stress analysis to optimise the frame stiffness, minimising deflection under full clamping force. We also adopted a high-rigidity, structurally stable one-piece injection seat and a low-damping linear guide to reduce friction and wear. In actual production, manufacturers process the core components to achieve flatness below 10 μm and alignment tolerance within ±0.01 mm, guaranteeing that the injection axis and template stay parallel under all loads. We also use a rolled ball screw with high preload to eliminate backlash in the axial drive of the injection unit. This high-rigidity, low-friction structure serves as the physical backbone for achieving micro-tolerance moulding, resisting thermal and mechanical drift even at high injection rates.
Monitoring the production process for adaptive control
Throughout the precision injection molding machine, we integrate various pressure sensors and infrared pyrometers into the mold to track real-time part molding in progress. Therefore, we can dynamically adjust the injection speed, pressure, and cooling parameters through the HMI interface of the injection molding machine. At the same time, you can write machine learning modules in the control software to analyze cycle-to-cycle variation data and automatically adjust setpoints to compensate for material batch variations or ambient temperature changes. In addition, the system records process data for each injection during production, enabling predictive maintenance and process optimization. This closed-loop adaptive control maintains final part micro-tolerances and eliminates impacts from external fluctuations or material variations.
Achieving micro-precision molding production
Micro-precision tolerances for plastic parts can be achieved in injection molding through the use of an electric drive, low-damping injection unit, high-precision pressure control, rigid structural design, and adaptive process monitoring on precision injection molding machines. For operators, servo motion profiles can be adjusted, pressure loops fine-tuned, and mechanical stiffness verified. Real-time feedback can also be used to ensure consistent accuracy of less than 0.01 mm.
TRENDING POSTS
- What factors can cause delays in the injection molding process of plastic molding machine? 2025/07/02
- Exhibition Review| Topstar participates in InterPlas Thailand 2024 2025/07/02
- Star Case | Topstar helps Santong upgrade its intelligent plant 2025/07/02
- Topstar Special | National Science and Technology Workers Day 2025/07/02
HOT TOPIC
- .ervo motor-driven linear robots
- 1.0 guangdong topstar technology co. ltd
- 1.0 topstar china
- 1.0 topstar robot
- 11
- 2
- 21
- 23
- 3 axis robot
- 3 axis robots
- 3 in 1 Compact Dehumidifying Dryer
- 3-axis robot
- 3-axis robots
- 39
- 41
- 5-axis CNC machine
- 62
- accuracy
- Air Chillers
- all electric injection molding machine
- all electric injection molding machines
- All-electric injection molding machines
- and overall production quality. Therefore
- AP-RubberPlas
- automated injection molding machine
- Automation changed engineering
- automation of injection molding robots
- auxiliary machine
- Bench Injection Molding Machine
- Cabinet dryer manufacturers
- Cabinet dryers
- chiller
- CNC Drilling Machine
- CNC Drilling Machines
- cnc engraving machine manufacturer
- cnc laser cutting machine manufacturer
- CNC machine
- CNC Machine Center
- CNC Machine for Sale
- CNC Machine Manufacturing
- CNC Machine Tool
- CNC machine tool product
- CNC Machining Center
- CNC wood carving machine
- Cooling system
- Cross-Walking Single Axis Servo Cylinder Robot
- Cross-Walking Single-Axis Servo Cylinder Robot
- Cross-Walking Three-Axis/Five-Axis Servo Driven Robot
- cross-walking three-axis/five-axis servo-driven robot
- Dehumidifier Dryer
- Dehumidifying Dryer
- delta parallel robot
- Desktop Injection Molding Machine
- Desktop injection molding machines
- Desktop Molding Machine
- desktop plastic injection machine
- Desktop Plastic Injection Molding Machine
- direct clamp injection molding machine
- Direct clamp injection molding machines
- Dosing & mixing system
- Drilling Centers
- Drying and dehumidification system
- drying and dehumidifying equipment
- Drying and Dehumidifying System
- drying system
- effective and efficient. Cabinet dryers are also used in other industries where large quantities of material need to be dried
- efficient injection molding machine
- elbow hydraulic injection molding machines
- electric injection molding machine
- electric injection molding machines
- energy-efficient injection molding robot
- energy-efficient water chiller
- energy-efficient water chillers
- energy-saving injection molding machine
- etc. Among injection molding robots
- exhibition
- features of CNC machine
- Feeding And Conveying System
- Five Axis Machine Center
- Fully automatic injection molding machine
- Gathering Topstar
- giant injection molding machine
- GMU-600 5-Axis Machining Center
- Granulating & Recycling System
- Heavy duty injection molding machine
- High-precision electric molding machines
- high-precision plastic molding machines
- high-speed all electric injection molding machine
- high-speed electric injection molding machine
- High-Speed Packaging Injection Molding
- Honeycomb rotor dehumidifier
- horizontal injection molding machine
- Horizontal Injection Molding Machines
- Horizontal Injection Moulding Machine
- Horizontal Mixer manufacturer
- How The CNC Machine Works
- hybrid injection molding machine
- hydraulic injection molding machine
- Hydraulic Injection Molding Machines
- in this article
- Industrial robot
- Industrial Robot Chinese brand
- industrial robot parts
- industrial robot supplier
- Industrial robots
- Industry Chain
- Injection Manipulator
- injection manipulator robot
- injection mold machines
- Injection molding
- Injection molding automation
- Injection Molding Automation Solution
- injection molding dryer
- Injection molding equipment
- injection molding hopper dryer
- Injection molding machine
- injection molding machine brand
- Injection Molding Machine Factory
- Injection Molding Machine Manufacture
- Injection molding machine manufacturer
- injection molding machine manufacturers
- Injection molding machine procurement
- injection molding machine robotic arm
- injection molding machine with a robot
- Injection molding machines
- injection molding material dehumidifying
- injection molding plant
- injection molding process
- Injection Molding Robot
- injection molding robot arm
- Injection molding robot automation
- Injection molding robotic arm
- injection molding robots
- Injection moulding machine
- injection moulding machines
- Injection Moulding Robots
- Injection Robot
- Injection robot arm
- Injection robot manufacturer
- Injection robot wholesale
- injection robots
- intelligent injection molding machines
- Intelligent mould temperature controller
- Introducing Injection Robot
- It is the best choice for drying large quantities of material at once. Cabinetmakers use these machines because they are fast
- Large flow water type mold temperature controller
- large injection molding machine
- large injection molding machines
- Learn what industrial automation and robotics is
- linear robot
- linear robots
- low speed sound-proof granulator
- machine plastic molding
- make sure to add some! Improvements (2) Keyphrase in introduction: Your keyphrase or its synonyms appear in the first paragraph of the copy
- manipulator machine
- manufacturing
- medical grade injection molding machines
- medical injection molding machine
- medical injection molding machines
- micro injection molding machine
- middle speed granulator
- Mini CNC machine manufacturers.
- Mold Temperature Control System
- mold temperature controller
- mold temperature controllers
- molding material Dehumidifying System
- mould temperature control system
- mould temperature controller
- mould temperature controllers
- New electric injection molding machine
- nitrogen dryer manufacturer
- nitrogen dryer system manufacturer
- Oil type mold temperature controller
- Oil type mold temperature controllers
- open day
- Outbound links: No outbound links appear in this page. Add some! Images: No images appear on this page. Add some! Internal links: No internal links appear in this page
- PET Preform injection molding
- phone case maker machine
- phone case making machine
- phone cover making machine
- plastic bottle making machine
- plastic bottle manufacturing
- plastic bucket making machine
- plastic bucket manufacturing
- Plastic chair making machine
- plastic forming equipment
- plastic hopper dryer
- plastic injection machine
- plastic injection machines
- plastic injection molding
- Plastic injection molding equipment
- Plastic injection molding machine
- Plastic Injection Molding Machines
- plastic injection moulding machine
- plastic injection moulding machines
- plastic injection robot
- plastic molding
- Plastic Molding machine
- plastic molding machine 1
- Plastic Molding Machines
- plastic molding press
- plastic moulding machine
- plastic phone case making machine
- plastic-molding machine
- powerful granulator
- Powerful Type Sound-Proof Granulator
- precision injection molding
- precision injection molding machines
- production of plastic seats
- pure water mould temperature controller
- Robot injection molding
- robot injection molding machine
- robot manufacturing companies
- Robotic arm for injection molding machine
- robotic injection molding machines
- robotics in injection molding
- SCARA robot
- SCARA robots
- Service-oriented manufacturing
- Servo Cylinder Robot
- servo driven robot
- Servo Driven Robots
- servo injection molding machine
- servo injection robots
- servo motor-driven linear robots
- servo-driven 3-axis robot
- Servo-Driven Robot
- Setup of injection machine
- Silicone Injection Molding Machine
- six-axis industrial robot
- Stainless Hopper Dryer
- Stainless Hopper Dryers
- star club
- swing arm robot
- take-out robot
- take-out robots
- the choice between servo-driven robots and hydraulic robots will have a certain impact on efficiency
- the most popular injection molding machine
- the type of injection molding robot
- TMII injection molding machine
- toggle clamp injection molding machine
- Toggle Hydraulic Injection Molding Machines
- toggle injection molding machine
- Top 10 brands of injection robots
- Topstar
- Topstar Engineering
- Topstar Industrial Robots
- Topstar injection molding intelligent
- Topstar Scara Robots
- Useful Injection molding machine
- Vertical machining centers
- volumetric type blender
- water chiller
- water chillers
- water distributor
- water type mold temperature controller
- Water Type MoldTemperature Controller
- Water-Type Mould Temperature Controllers
- We often face choices when performing injection molding. We will choose the type of injection molding machine
- wholesale of injection molding machines
- x carve CNC
- 热门查询 点击次数 展示 排名 topstar