The Ultimate Deal on Injection Molding Machine 2022
2022/01/31 By Topstar
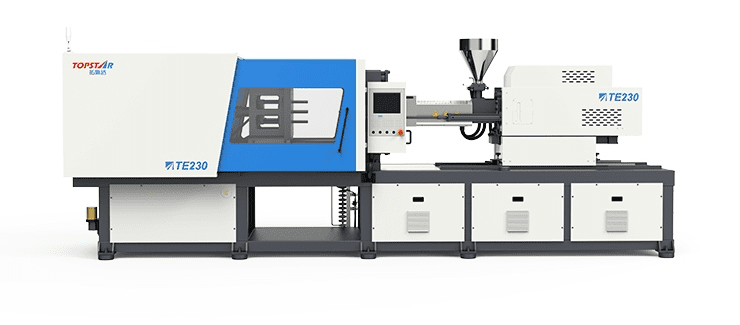
Introduction to plastic injection molding technology
The injection molding machine 2022 is a technology for manufacturing products by injecting molten material into a mold. It can perform on various materials, primarily metals (commonly known as pressure casting), glass, elastomers, blends, and thermoplastics.
This technology is widely shared in manufacturing, from small parts to the entire chassis plate.
Casting details must meticulously design to facilitate the casting process; The casting material, shape, required part characteristics, mold material, and die-forming machine properties must be carefully calculated. This gives the flexibility of injection molding technology.
Introduction to injection molding machine 2022
The injection molding machine was first invented in the United States in 1872 by brothers John Wesley Hyatt and Isaiah. This machine is more primitive than modern equipment; it works like a giant needle; under the action of a piston, the plastic is through the cylinder head and injected into the mold.
German scientists Arthur Eichengrün and Theodore Becker discovered the first soluble forms of cellulose acetate in 1903, which are less flammable than cellulose nitrate and easy to extrude. Arthur Eichengrün developed the first injection molding machine in 1939 and patented the flexible cellulose acetate injection mold.
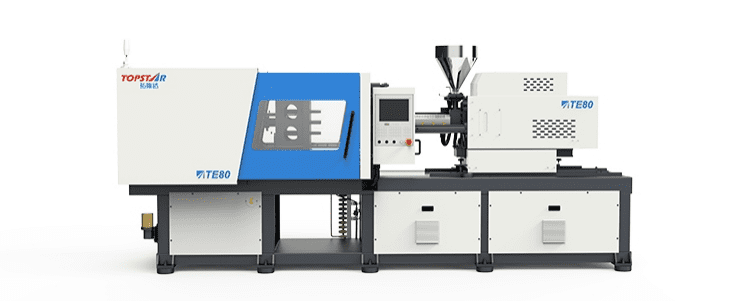
First screw pump manufactured quality of the products
World War II opened up massive demand for cheap and mass-produced products. In 1946, American inventor James Watson Hendry built the first injection molding machine in 2022, which allowed more precise control of the injection rate and quality of the products manufactured.
This machine can also mix raw materials before spraying so that colored plastic or recycled plastics mix. In 1970, Hendry developed the first air-assisted injection molding system to cool complex products rapidly.
Flexibility and rigidity of manufactured products
This improves the design flexibility and rigidity of manufactured products while saving on costs, fuel, raw materials, and waste. In 1990, aluminum molds were widely common. Nowadays, screw pumps make up the majority of plastic injection molding machines.
Injection molding machine 2022 technology produces push buttons for automotive, medical, consumer goods, toys, plumbing, packaging, and construction.
Applications of injection molding technology
Firstly, injection molding technology is widely shared in the industry, especially in the plastics industry, as the ideal method for producing large objects of the same volume. In addition, injection molding technology is also applied in the manufacturing industry of packaging, bottle caps, auto parts, components, coils, musical instruments, tables, chairs, and machine parts (including gears), …
Technological features of Injection molding
Secondly, injection molding uses ram pistons or screw pistons to inject molten material into the mold, hardening to achieve the shape of the mold cavity. This injection molding machine 2022 is commonly typical to process thermoplastics and thermosetting plastics in much larger volumes than in the past.
Thermoplastics are popular
Thermoplastics are popular because they are suitable for injection moldings, such as ease of recycling and wide application in many fields and their ease of softening and melting when exposed to heat. They are also safer than thermosets when they do not extrude in time. It can cause vulcanization and stuck control valves, leading to equipment damage.
The injection molding machine 2022 of raw materials with high pressure into the mold will form a plastic block of the desired shape. The mold can be a single-cavity or multi-cavity. The holes can be the same or different for multi-cavity molds to produce many parts in one injection cycle.
Stainless steel and aluminum molds
Mold materials are usually tool steel; stainless steel and aluminum molds are suitable for specific applications. In particular, parts with large masses or small tolerances typically do not use aluminum molds.
Thirdly, and most importantly, they have poor mechanical properties and are susceptible to corrosion, damage, and deformation during injection, precisely because Therefore, aluminum molds are very effective in manufacturing small, light parts with significantly reduced mold design and manufacturing costs and production time. Many steel molds are designed to produce millions of pieces,
Perfect temperature and humidity in injection molding machine 2022
Manufacturers spend a lot of money maintaining custom molds for a long time. Ideal temperature and moisture guarantee the lifetime of each mold. Custom molds, such as rubber injection molds stored in a controlled temperature and humidity environment to prevent warping.
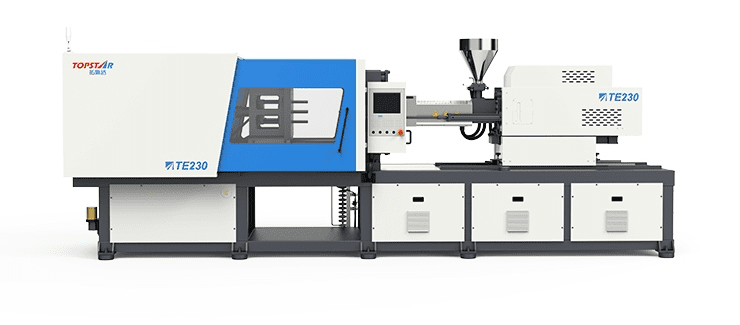
Tool steels are commonly standard.
Mild steel, aluminum, nickel, or epoxy are only suitable for prototype runs or short production processes. Modern rugged aluminum (usually alloys 7075 and 2024) with suitable mold designs easily molds the ability to cast more than 100,000 parts with proper curing.
Manufacturing of the products
The two main mold-making methods are:
Standard machining method and EDM. The traditional machining method is common to the conventional mold-making way. With the development of technology, injection molding machine 2022 has become the primary means to create complex molds with higher precision and save time than traditional methods.
The electro-spinning machining method (EDM). The electro-spinning machining method (EDM) is gradually becoming widely shared, as well as for machining complex shapes or forming hard molds without heat treatment.
Moreover, EDM is a simple process in which an electrode is introduced very slowly into the mold surface. The electrode reversal of the voltage between the tool and the die causes erosion and forms the required consistency.
Casting cavities directly correlate with the casting cost
In the injection molding machine 2022, the number of casting cavities directly correlates with the casting cost. Fewer chambers and fewer tools lead to lower initial production costs.
Since the number of cavities plays an important role, so is the complexity of the molded product design. This complexity includes many factors such as surface finish, tolerances, external or internal threads, fine detailing, or several cuts. In particular, scratches or additional tool properties will increase die costs, and core and cavity surfaces will also affect production costs.
Rubber injection molding produces a highly durable product, making it the most efficient and economical molding method. The proper curing process provides precise temperature control and significantly reduces material waste.
Spray process in the injection molding machine
In the injection molding machine 2022, the plastic is fed into a hot tank through a hopper. The resin drives forward by the screw piston, enters the burning chamber, and begins to flow. The liquid resin pushes through the nozzle into the mold cavity through channels and inlets. The mold is still cold, so the resin hardens as soon as it is filled.
TRENDING POSTS
- What factors can cause delays in the injection molding process of plastic molding machine? 2022/01/31
- Exhibition Review| Topstar participates in InterPlas Thailand 2024 2022/01/31
- Star Case | Topstar helps Santong upgrade its intelligent plant 2022/01/31
- Topstar Special | National Science and Technology Workers Day 2022/01/31
HOT TOPIC
- .ervo motor-driven linear robots
- 3 axis robot
- 3 axis robots
- 3 in 1 Compact Dehumidifying Dryer
- 3-axis robot
- 3-axis robots
- 5-axis CNC machine
- accuracy
- Air Chillers
- all electric injection molding machine
- all electric injection molding machines
- All-electric injection molding machines
- and overall production quality. Therefore
- AP-RubberPlas
- automated injection molding machine
- Automation changed engineering
- automation of injection molding robots
- auxiliary machine
- Bench Injection Molding Machine
- Cabinet dryer manufacturers
- Cabinet dryers
- chiller
- CNC Drilling Machine
- CNC Drilling Machines
- cnc engraving machine manufacturer
- cnc laser cutting machine manufacturer
- CNC machine
- CNC Machine Center
- CNC Machine for Sale
- CNC Machine Manufacturing
- CNC Machine Tool
- CNC machine tool product
- CNC Machining Center
- CNC wood carving machine
- Cooling system
- Cross-Walking Single Axis Servo Cylinder Robot
- Cross-Walking Single-Axis Servo Cylinder Robot
- Cross-Walking Three-Axis/Five-Axis Servo Driven Robot
- cross-walking three-axis/five-axis servo-driven robot
- Dehumidifier Dryer
- Dehumidifying Dryer
- delta parallel robot
- Desktop Injection Molding Machine
- Desktop injection molding machines
- Desktop Molding Machine
- desktop plastic injection machine
- Desktop Plastic Injection Molding Machine
- direct clamp injection molding machine
- Direct clamp injection molding machines
- Dosing & mixing system
- Drilling Centers
- Drying and dehumidification system
- drying and dehumidifying equipment
- Drying and Dehumidifying System
- drying system
- effective and efficient. Cabinet dryers are also used in other industries where large quantities of material need to be dried
- efficient injection molding machine
- elbow hydraulic injection molding machines
- electric injection molding machine
- electric injection molding machines
- energy-efficient injection molding robot
- energy-saving injection molding machine
- etc. Among injection molding robots
- exhibition
- features of CNC machine
- Feeding And Conveying System
- Five Axis Machine Center
- Fully automatic injection molding machine
- Gathering Topstar
- giant injection molding machine
- GMU-600 5-Axis Machining Center
- Granulating & Recycling System
- Heavy duty injection molding machine
- High-precision electric molding machines
- high-precision plastic molding machines
- high-speed all electric injection molding machine
- Honeycomb rotor dehumidifier
- horizontal injection molding machine
- Horizontal Injection Molding Machines
- Horizontal Injection Moulding Machine
- Horizontal Mixer manufacturer
- How The CNC Machine Works
- hybrid injection molding machine
- hydraulic injection molding machine
- Hydraulic Injection Molding Machines
- in this article
- Industrial robot
- Industrial Robot Chinese brand
- industrial robot parts
- industrial robot supplier
- Industrial robots
- Industry Chain
- Injection Manipulator
- injection manipulator robot
- injection mold machines
- Injection molding
- Injection molding automation
- Injection Molding Automation Solution
- injection molding dryer
- Injection molding equipment
- injection molding hopper dryer
- Injection molding machine
- injection molding machine brand
- Injection Molding Machine Factory
- Injection Molding Machine Manufacture
- Injection molding machine manufacturer
- injection molding machine manufacturers
- Injection molding machine procurement
- injection molding machine robotic arm
- injection molding machine with a robot
- Injection molding machines
- injection molding material dehumidifying
- injection molding plant
- Injection Molding Robot
- injection molding robot arm
- Injection molding robot automation
- Injection molding robotic arm
- injection molding robots
- Injection moulding machine
- Injection Moulding Robots
- Injection Robot
- Injection robot arm
- Injection robot manufacturer
- Injection robot wholesale
- injection robots
- intelligent injection molding machines
- Introducing Injection Robot
- It is the best choice for drying large quantities of material at once. Cabinetmakers use these machines because they are fast
- large injection molding machine
- large injection molding machines
- Learn what industrial automation and robotics is
- linear robot
- linear robots
- low speed sound-proof granulator
- machine plastic molding
- make sure to add some! Improvements (2) Keyphrase in introduction: Your keyphrase or its synonyms appear in the first paragraph of the copy
- manipulator machine
- manufacturing
- medical grade injection molding machines
- medical injection molding machine
- medical injection molding machines
- micro injection molding machine
- middle speed granulator
- Mini CNC machine manufacturers.
- Mold Temperature Control System
- mold temperature controller
- mold temperature controllers
- molding material Dehumidifying System
- mould temperature control system
- mould temperature controller
- mould temperature controllers
- New electric injection molding machine
- nitrogen dryer manufacturer
- nitrogen dryer system manufacturer
- Oil type mold temperature controller
- Oil type mold temperature controllers
- open day
- Outbound links: No outbound links appear in this page. Add some! Images: No images appear on this page. Add some! Internal links: No internal links appear in this page
- PET Preform injection molding
- phone case maker machine
- phone case making machine
- plastic bottle making machine
- plastic bottle manufacturing
- plastic bucket making machine
- plastic bucket manufacturing
- Plastic chair making machine
- plastic forming equipment
- plastic hopper dryer
- plastic injection machine
- plastic injection machines
- plastic injection molding
- Plastic injection molding equipment
- Plastic injection molding machine
- Plastic Injection Molding Machines
- plastic injection moulding machine
- plastic injection robot
- Plastic Molding machine
- Plastic Molding Machines
- plastic molding press
- plastic moulding machine
- plastic phone case making machine
- plastic-molding machine
- powerful granulator
- Powerful Type Sound-Proof Granulator
- precision injection molding
- precision injection molding machines
- production of plastic seats
- pure water mould temperature controller
- Robot injection molding
- robot injection molding machine
- robot manufacturing companies
- Robotic arm for injection molding machine
- robotic injection molding machines
- robotics in injection molding
- SCARA robot
- SCARA robots
- Service-oriented manufacturing
- Servo Cylinder Robot
- servo driven robot
- Servo Driven Robots
- servo injection robots
- servo motor-driven linear robots
- servo-driven 3-axis robot
- Servo-Driven Robot
- Setup of injection machine
- Silicone Injection Molding Machine
- six-axis industrial robot
- Stainless Hopper Dryer
- Stainless Hopper Dryers
- star club
- swing arm robot
- take-out robots
- the choice between servo-driven robots and hydraulic robots will have a certain impact on efficiency
- the most popular injection molding machine
- the type of injection molding robot
- toggle clamp injection molding machine
- Toggle Hydraulic Injection Molding Machines
- toggle injection molding machine
- Top 10 brands of injection robots
- Topstar
- Topstar Engineering
- Topstar Industrial Robots
- Topstar injection molding intelligent
- Topstar Scara Robots
- Useful Injection molding machine
- Vertical machining centers
- volumetric type blender
- water chiller
- water chillers
- water distributor
- water type mold temperature controller
- Water Type MoldTemperature Controller
- Water-Type Mould Temperature Controllers
- We often face choices when performing injection molding. We will choose the type of injection molding machine
- wholesale of injection molding machines
- x carve CNC