What are the drawbacks of traditional large-scale injection molding machines?
2024/04/08 By Topstar
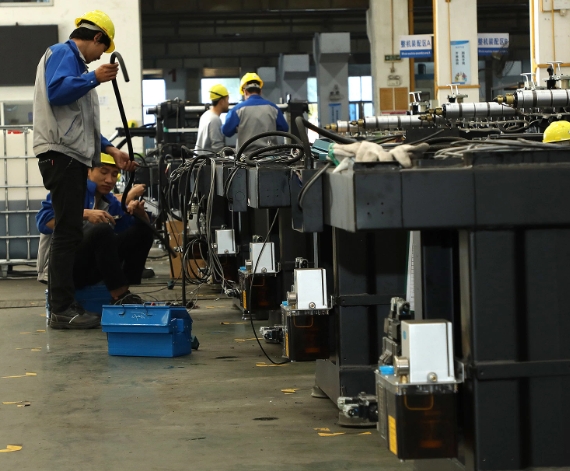
Traditional large-scale injection molding machines have always been the main plastic manufacturing and production equipment. As everyone’s needs change and the era of Industry 4.0 comes, the shortcomings of traditional large-scale injection molding machines are gradually exposed. In this guide, we will list some of their main core shortcomings and share with you what advantages Topstar’s new injection molding machine can have in breaking through traditional limitations.
High energy consumption
Traditional large-scale injection molding machines usually operate using hydraulic systems, relying on pumps, motors, and valves to control the movement of hydraulic oil. The disadvantage of this method is higher energy consumption. Hydraulic systems also require pumps to run continuously to maintain them, resulting in energy losses through friction, heat generation, and leakage. Although they can operate at high pressure and speed, they also bring increased energy consumption. High-pressure hydraulic systems require more energy to generate and maintain hydraulic pressure, and the rapid movement of machine components results in higher energy requirements for motor operation. In addition, the oversized hydraulic components they are equipped with will also increase energy consumption.
Limited flexibility and versatility
On the production side, while traditional large injection molding machines can standardize large quantities of parts, they often struggle to accommodate smaller production runs, custom designs, or changes in product specifications. Because they are equipped with fixed molds and tooling to produce specific parts, changes would be very time-consuming and labor-cost-prohibitive. Additionally, they lack the versatility to handle various materials with varying properties and specifications. This may pose limitations for manufacturers looking to use new materials or need to incorporate special additives into the injection molding process. Adjusting the machines when facing different production requirements requires additional setup time, so they lack flexibility and versatility.
Large floor area and space requirements
One of the most obvious shortcomings of traditional large-scale injection molding machines is that they require much floor space. Sufficient floor space is required to accommodate the injection molding machine, auxiliary equipment, and manipulators. This will limit layout flexibility and production capacity. When the floor space and space requirements are large, on the one hand, it will affect operational efficiency, on the other hand, the demand for large space will limit the effective use of other available floor space and limit the layout of other production facilities. And their requirements for production workshops will be higher, requiring a certain area of workshops to accommodate them.
Advantages of Topstar’s new injection molding machine
Maintaining and repairing traditional large injection molding machines can be complex and time-consuming, requiring specialized skills and expertise. As these machines age, they can experience wear and tear, leading to performance issues, downtime, and increased maintenance costs. Additionally, sourcing replacement parts for older machines can be challenging, especially if the manufacturer has ceased support or is out of business. This reliance on outdated technology can pose significant risks to the company’s operational reliability and competitiveness.
Modular design of new injection molding machine
The second major advantage of the new injection molding machine is its modular design, which allows us to adapt to various working conditions.
They comprise interchangeable modules and components that allow manufacturers to adapt according to output material type. At the same time, the modular design allows them to add auxiliary equipment easily, and the injection robot improves overall productivity and efficiency. The modular design also enables easy inspection, repair, or replacement of individual components.
Cleaner motion and smoother operation
They are smaller than traditional large injection molding machines, and Topstar’s new injection molding machines provide cleaner movement and smoother operation through the use of linear rail supports. Reducing vibration, noise, and mechanical interference during operation results in smoother movement. And for industries like medical products, which have higher quality control requirements, they can provide a cleaner production environment. They will not face problems such as oil leakage. In addition, they use special optical screws and good mixing and exhaust to ensure that transparent products do not turn yellow.
Breaking the limitations of traditional injection molding machines
Traditional large-scale injection molding machines have accounted for a large part of the main productivity in the manufacturing industry in the past few decades. However, due to high energy consumption, limited flexibility, and large floor space, they cannot meet the needs of modern manufacturers. Therefore, new injection molding machines have emerged to meet the needs of manufacturers under modern Industry 4.0 for high-precision, high-performance, stable, and reliable injection molding.
TRENDING POSTS
- What factors can cause delays in the injection molding process of plastic molding machine? 2024/04/08
- Exhibition Review| Topstar participates in InterPlas Thailand 2024 2024/04/08
- Star Case | Topstar helps Santong upgrade its intelligent plant 2024/04/08
- Topstar Special | National Science and Technology Workers Day 2024/04/08
HOT TOPIC
- .ervo motor-driven linear robots
- 1.0 guangdong topstar technology co. ltd
- 1.0 topstar china
- 1.0 topstar robot
- 11
- 2
- 21
- 23
- 3 axis robot
- 3 axis robots
- 3 in 1 Compact Dehumidifying Dryer
- 3-axis robot
- 3-axis robots
- 39
- 41
- 5-axis CNC machine
- 62
- accuracy
- Air Chillers
- all electric injection molding machine
- all electric injection molding machines
- All-electric injection molding machines
- and overall production quality. Therefore
- AP-RubberPlas
- automated injection molding machine
- Automation changed engineering
- automation of injection molding robots
- auxiliary machine
- Bench Injection Molding Machine
- Cabinet dryer manufacturers
- Cabinet dryers
- chiller
- CNC Drilling Machine
- CNC Drilling Machines
- cnc engraving machine manufacturer
- cnc laser cutting machine manufacturer
- CNC machine
- CNC Machine Center
- CNC Machine for Sale
- CNC Machine Manufacturing
- CNC Machine Tool
- CNC machine tool product
- CNC Machining Center
- CNC wood carving machine
- Cooling system
- Cross-Walking Single Axis Servo Cylinder Robot
- Cross-Walking Single-Axis Servo Cylinder Robot
- Cross-Walking Three-Axis/Five-Axis Servo Driven Robot
- cross-walking three-axis/five-axis servo-driven robot
- Dehumidifier Dryer
- Dehumidifying Dryer
- delta parallel robot
- Desktop Injection Molding Machine
- Desktop injection molding machines
- Desktop Molding Machine
- desktop plastic injection machine
- Desktop Plastic Injection Molding Machine
- direct clamp injection molding machine
- Direct clamp injection molding machines
- Dosing & mixing system
- Drilling Centers
- Drying and dehumidification system
- drying and dehumidifying equipment
- Drying and Dehumidifying System
- drying system
- effective and efficient. Cabinet dryers are also used in other industries where large quantities of material need to be dried
- efficient injection molding machine
- elbow hydraulic injection molding machines
- electric injection molding machine
- electric injection molding machines
- energy-efficient injection molding robot
- energy-saving injection molding machine
- etc. Among injection molding robots
- exhibition
- features of CNC machine
- Feeding And Conveying System
- Five Axis Machine Center
- Fully automatic injection molding machine
- Gathering Topstar
- giant injection molding machine
- GMU-600 5-Axis Machining Center
- Granulating & Recycling System
- Heavy duty injection molding machine
- High-precision electric molding machines
- high-precision plastic molding machines
- high-speed all electric injection molding machine
- Honeycomb rotor dehumidifier
- horizontal injection molding machine
- Horizontal Injection Molding Machines
- Horizontal Injection Moulding Machine
- Horizontal Mixer manufacturer
- How The CNC Machine Works
- hybrid injection molding machine
- hydraulic injection molding machine
- Hydraulic Injection Molding Machines
- in this article
- Industrial robot
- Industrial Robot Chinese brand
- industrial robot parts
- industrial robot supplier
- Industrial robots
- Industry Chain
- Injection Manipulator
- injection manipulator robot
- injection mold machines
- Injection molding
- Injection molding automation
- Injection Molding Automation Solution
- injection molding dryer
- Injection molding equipment
- injection molding hopper dryer
- Injection molding machine
- injection molding machine brand
- Injection Molding Machine Factory
- Injection Molding Machine Manufacture
- Injection molding machine manufacturer
- injection molding machine manufacturers
- Injection molding machine procurement
- injection molding machine robotic arm
- injection molding machine with a robot
- Injection molding machines
- injection molding material dehumidifying
- injection molding plant
- Injection Molding Robot
- injection molding robot arm
- Injection molding robot automation
- Injection molding robotic arm
- injection molding robots
- Injection moulding machine
- Injection Moulding Robots
- Injection Robot
- Injection robot arm
- Injection robot manufacturer
- Injection robot wholesale
- injection robots
- intelligent injection molding machines
- Introducing Injection Robot
- It is the best choice for drying large quantities of material at once. Cabinetmakers use these machines because they are fast
- large injection molding machine
- large injection molding machines
- Learn what industrial automation and robotics is
- linear robot
- linear robots
- low speed sound-proof granulator
- machine plastic molding
- make sure to add some! Improvements (2) Keyphrase in introduction: Your keyphrase or its synonyms appear in the first paragraph of the copy
- manipulator machine
- manufacturing
- medical grade injection molding machines
- medical injection molding machine
- medical injection molding machines
- micro injection molding machine
- middle speed granulator
- Mini CNC machine manufacturers.
- Mold Temperature Control System
- mold temperature controller
- mold temperature controllers
- molding material Dehumidifying System
- mould temperature control system
- mould temperature controller
- mould temperature controllers
- New electric injection molding machine
- nitrogen dryer manufacturer
- nitrogen dryer system manufacturer
- Oil type mold temperature controller
- Oil type mold temperature controllers
- open day
- Outbound links: No outbound links appear in this page. Add some! Images: No images appear on this page. Add some! Internal links: No internal links appear in this page
- PET Preform injection molding
- phone case maker machine
- phone case making machine
- plastic bottle making machine
- plastic bottle manufacturing
- plastic bucket making machine
- plastic bucket manufacturing
- Plastic chair making machine
- plastic forming equipment
- plastic hopper dryer
- plastic injection machine
- plastic injection machines
- plastic injection molding
- Plastic injection molding equipment
- Plastic injection molding machine
- Plastic Injection Molding Machines
- plastic injection moulding machine
- plastic injection robot
- Plastic Molding machine
- Plastic Molding Machines
- plastic molding press
- plastic moulding machine
- plastic phone case making machine
- plastic-molding machine
- powerful granulator
- Powerful Type Sound-Proof Granulator
- precision injection molding
- precision injection molding machines
- production of plastic seats
- pure water mould temperature controller
- Robot injection molding
- robot injection molding machine
- robot manufacturing companies
- Robotic arm for injection molding machine
- robotic injection molding machines
- robotics in injection molding
- SCARA robot
- SCARA robots
- Service-oriented manufacturing
- Servo Cylinder Robot
- servo driven robot
- Servo Driven Robots
- servo injection robots
- servo motor-driven linear robots
- servo-driven 3-axis robot
- Servo-Driven Robot
- Setup of injection machine
- Silicone Injection Molding Machine
- six-axis industrial robot
- Stainless Hopper Dryer
- Stainless Hopper Dryers
- star club
- swing arm robot
- take-out robots
- the choice between servo-driven robots and hydraulic robots will have a certain impact on efficiency
- the most popular injection molding machine
- the type of injection molding robot
- toggle clamp injection molding machine
- Toggle Hydraulic Injection Molding Machines
- toggle injection molding machine
- Top 10 brands of injection robots
- Topstar
- Topstar Engineering
- Topstar Industrial Robots
- Topstar injection molding intelligent
- Topstar Scara Robots
- Useful Injection molding machine
- Vertical machining centers
- volumetric type blender
- water chiller
- water chillers
- water distributor
- water type mold temperature controller
- Water Type MoldTemperature Controller
- Water-Type Mould Temperature Controllers
- We often face choices when performing injection molding. We will choose the type of injection molding machine
- wholesale of injection molding machines
- x carve CNC
- 热门查询 点击次数 展示 排名 topstar